Medical Electronics PCB circuit boards have become one of the most complex and challenging circuit boards in the industry. PCB circuit board assembly plays a fundamental role in medical equipment, involving key tasks such as signal transmission and data processing. Its technological innovation promotes the miniaturization and intelligent development of medical equipment, while ensuring equipment reliability and innovative research and development. Through strict quality control, ensure the long-term stable operation of equipment.
In medical electronics equipment, whether it is large imaging diagnostic equipment or small portable monitoring instruments, PCB circuit board assembly is indispensable. They are the foundation for implementing various functions of the device, undertaking key tasks such as signal transmission, data processing, and power management.
For example, in an electrocardiogram machine, PCB circuit board assembly is responsible for amplifying, filtering, and digitizing the electrocardiogram signals collected by sensors, and ultimately transmitting the processed data to display or storage devices.
During this process, the stability and reliability of PCB circuit board assembly are crucial for ensuring the accuracy and reliability of the electrocardiogram machine.
With the continuous upgrading and replacement of medical electronics equipment, miniaturization and portability have become important development trends. The implementation of this trend cannot be separated from the support of PCB circuit board assembly technology.
By using high-density assembly, micro components, and multi-layer board technology, PCB circuit board assembly can achieve more complex circuit functions in limited space, thereby promoting the development of medical equipment towards miniaturization.
Taking blood glucose meters as an example, with the advancement of technology, modern blood glucose meters have achieved a transformation from drip type to non-invasive type, and their volume has become increasingly compact. Behind this, the continuous innovation of PCB circuit board assembly technology is indispensable.
By optimizing the PCB circuit layout, adopting micro components, and advanced welding technology, the circuit board of the blood glucose meter can be highly integrated and miniaturized, providing patients with more convenient detection methods.
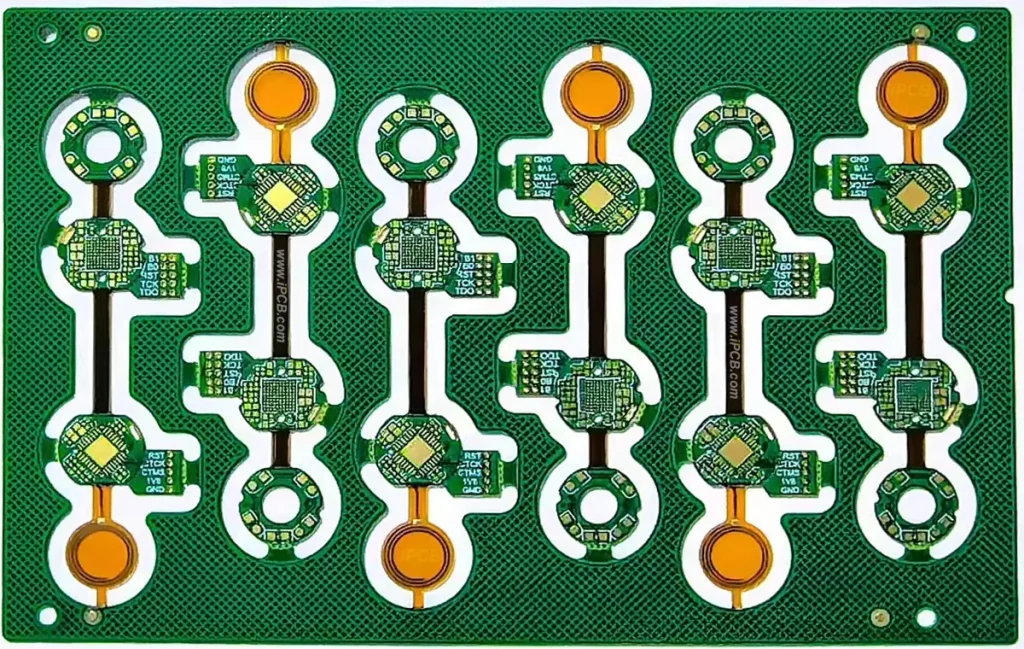
Intelligence is one of the important directions for the development of modern medical electronics equipment, and PCB circuit board assembly plays a crucial role in this process. By integrating various sensors, processors, and communication modules, PCB circuit board assembly can achieve functions such as automatic monitoring, data analysis, and remote communication of medical equipment, thereby improving the intelligence level of the equipment.
For example, in the intelligent infusion pump, the PCB circuit board assembly integrates various sensors such as flow sensors, pressure sensors, temperature sensors, etc., to monitor various parameters during the infusion process in real time, and automatically adjust the infusion speed and pressure through data analysis by the processor, ensuring the safety and effectiveness of the infusion process. Meanwhile, through the communication module, the intelligent infusion pump can also be connected to the hospital’s information system, achieving remote monitoring and management.
Medical equipment, as a special product that concerns people’s lives and health, has extremely high reliability requirements. As one of the core components of medical electronics equipment, the reliability of PCB circuit board assembly is directly related to the performance stability and service life of the entire equipment.
In order to improve the reliability of PCB circuit board assembly, medical equipment manufacturers have adopted a series of strict quality control measures in the design and production process.
For example, selecting high-quality components and printed circuit board materials, using advanced welding processes and testing equipment, and conducting strict environmental adaptability testing and aging testing.
These measures ensure the long-term stable operation of PCB circuit board assembly in medical equipment, providing strong guarantees for the reliability of medical equipment.
With the continuous development and innovation of medical technology, new medical equipment and therapies are constantly emerging. Behind these innovations, PCB circuit board assembly plays an important driving role. By adopting advanced design concepts and technological means, PCB circuit board assembly can quickly achieve prototype verification and product iteration, providing strong support for innovative research and development of medical equipment.
For example, in the field of wearable medical devices, with the increasing demand for health monitoring and disease prevention, various new types of wearable devices such as smart bracelets and health monitoring insoles have emerged. In the development process of these devices, PCB circuit board assembly technology plays a crucial role.
By adopting flexible circuit boards and high-density assembly technology, wearable device circuit boards can achieve close fit and high integration with human skin, providing users with a more comfortable and convenient user experience.
Medical PCB circuit boards have the following aspects:
Safety and reliability: In the medical electronics industry, life support products or high-end products refer to the IPC-3 standard, while non life support products or low-end products refer to IPC-2 It is important to establish independent enterprise standards for large medical terminals and strictly control the reliability of products.
Long service life: The warranty period for general products is 1 year, while large medical equipment requires a minimum service life of 10 years. There are still differences between medical electronic PCBs and regular PCBs.
Large scale leap: from consumer medical products that meet conventional requirements, to mid to high end medical products that meet high reliability and stability requirements, and then to small portable products that meet high-density, highly integrated, intelligent, multifunctional wearable medical products.
Product conservatism: New medical technologies and products are slowly introduced into the market, and new product validation tests are repeated, which usually requires comprehensive evaluation.
Traceability: Products require strict process documentation and product traceability. Some large medical terminals require PCB processing records to be traceable for 10 years.
Fire protection requirements: The process and fire protection requirements for PCBs used in medical electronics are different. The methods of spraying tin and cleaning circuit boards are different from ordinary PCB processes. Under the premise of adopting technological measures to ensure quality and safety, it can be used for maintenance as appropriate.
Small demand: Generally, the demand for medical PCBs is small, with multiple process requirements such as back drilling, multiple pressing, mixed pressure, high precision, special impedance, thick copper, thick gold, copper embedded blocks, etc. The price focus will be very low, which is also different from ordinary circuit boards.
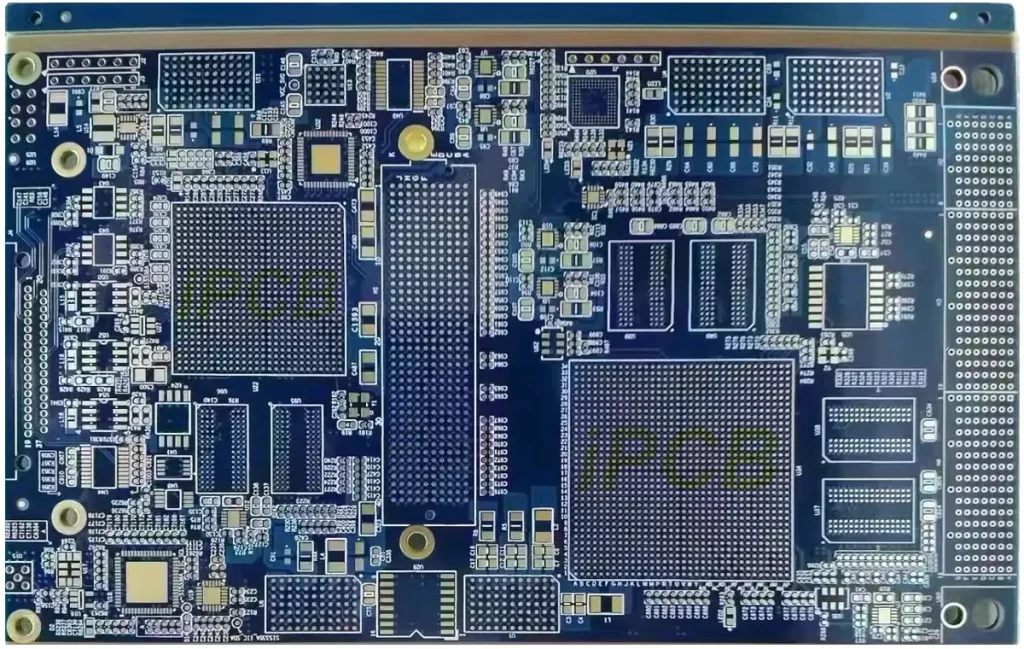
PCB boards used in medical electronics are widely used in various medical devices, including medical monitors, pacemakers, medical imaging equipment, etc. These devices have different requirements for PCB boards, but they all require high precision, stability, and reliability. The application fields of medical electronics are constantly expanding, such as emerging fields such as medical robots and wireless medical devices, and the demand for circuit boards is also increasing.
Compared with ordinary circuit boards, PCB boards used in medical electronics have unique requirements in design and manufacturing, material selection, reliability, and safety. With the continuous development and innovation of medical electronic technology, the application of medical circuit boards in medical equipment will also be further expanded, making contributions to the development of the medical industry.