FPC, also known as FPCB or Flexible PCB, is a type of circuit board that can be bent and twisted. It is composed of a flexible insulation substrate and conductive wiring with good flexibility and elasticity, which can be bent or twisted according to the needs of the product. It is an ideal choice for miniaturization, lightweight, high-density, and complex circuit applications.
Flexible PCB also belong to the category of PCBs. For convenience, we usually refer to rigid PCBs as PCBs and flexible PCBs as FPCs. Flexible PCBs can be divided into single-sided FPC, double-sided FPC, and multi-layer FPC. The main substrate used is polyimide copper-clad sheet. This material has high heat resistance and good dimensional stability, and is pressed with a covering film that combines mechanical protection and good electrical insulation performance to form the final product. The surface and inner conductors of double-sided and multi-layer FPC boards are metallized to achieve electrical connections between the inner and outer circuits.
The functions of FPC can be divided into four types, namely Lead Line, Printed Circuit, Connector, and Integration of Function. Its applications include computers, computer peripheral auxiliary systems, consumer electronics, and automobiles.
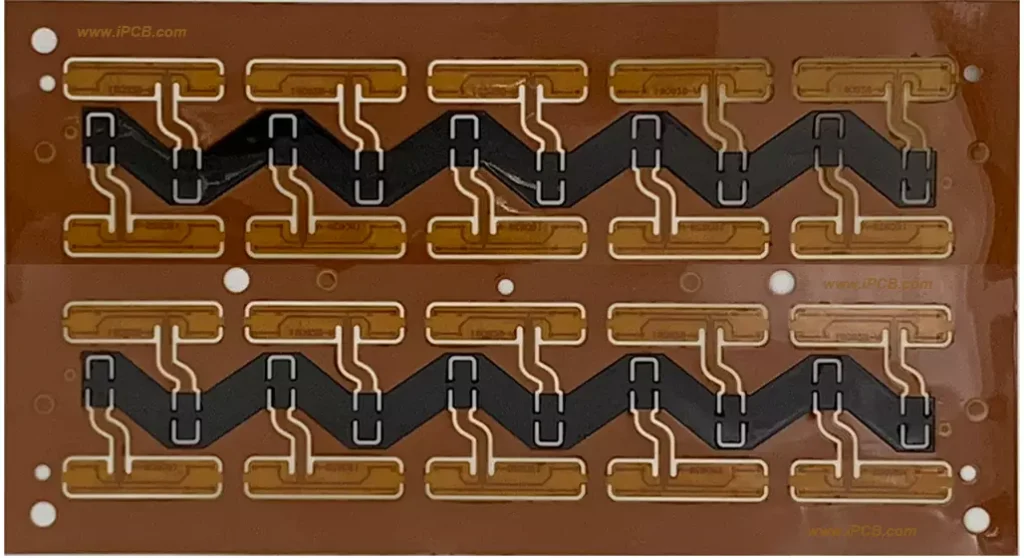
What is the difference between FPC vs PCB?
FPC board is a flexible circuit board composed of multiple layers of thin film materials that can be bent and folded, suitable for electronic products that require bending. FPC boards are commonly used in mobile devices, medical devices, automotive electronics, aerospace and other fields. FPC boards generally use metal foil as the conductive layer and are manufactured through processes such as chemical corrosion or laser cutting.
PCB is a rigid circuit board composed of one or more conductive layers and insulation layers, usually made of glass fiber reinforced materials. PCB boards are suitable for electronic products that require high stability and performance. The manufacturing process of PCB boards is relatively complex, usually requiring multiple processes such as chemical corrosion, gold plating, drilling, and copper coating.
Flexible Printed Circuit Board and rigid Printed Circuit Board are two common types of circuit boards, both of which are essential components in electronic devices. There is no absolute difference in performance between FPC and rigid PCB, only the difference in body shape and soft rigidity. Due to its thinness and softness, FPC is often used in compact and flexible connections, with the most common being the data connection between the body and screen of foldable products such as micro electronic products, flip phones, laptops, etc.
One of the characteristics of FPC is its softness: rigid PCB boards usually use FR4 fiberglass board as the substrate and cannot be bent or bent. FPC generally uses PI polyimide as the substrate, which is a flexible material that can be bent or flexed arbitrarily. Therefore, the substrate of FPC is called FCCL (Flexible Copper Clad Laminate).
Another characteristic of FPC is its thinness: the thickness of rigid PCB boards is usually 0.2mm-2mm, while the thickness of FPC is generally 0.1-0.2mm, greatly saving product space. The disadvantage that comes with it is that FPC has slightly poorer heat dissipation compared to rigid PCBs.
The materials of FPC and PCB are different: FPC boards are made of flexible film materials, while PCB boards are made of rigid glass fiber reinforced materials.
The bending ability of FPC and PCB is different: FPC boards can be bent within a certain range, while PCB boards are rigid and cannot be bent.
The manufacturing process of FPC and PCB is different: the manufacturing process of FPC board is relatively simple, usually only requiring one chemical corrosion to complete, while the manufacturing process of PCB is more complex, requiring multiple processes such as chemical corrosion, gold plating, drilling, and copper coating.
The scope of application of FPC and PCB is different: FPC boards are suitable for electronic products that require bending, while PCB boards are suitable for various electronic products that require high stability and performance.
FPC and PCB each have their own advantages and disadvantages, and suitable circuit board types should be selected according to different application scenarios. When designing circuits, it is necessary to consider factors such as circuit performance requirements, manufacturing costs, and production cycles, and after comprehensive consideration, select the most suitable type of circuit board. There are significant differences between PCB circuit boards and FPC circuit boards in terms of materials, flexibility, manufacturing processes, and application fields. When selecting the type of circuit board, the procurement of electronic equipment manufacturers should be comprehensively evaluated based on specific application requirements, design requirements, and budget factors.
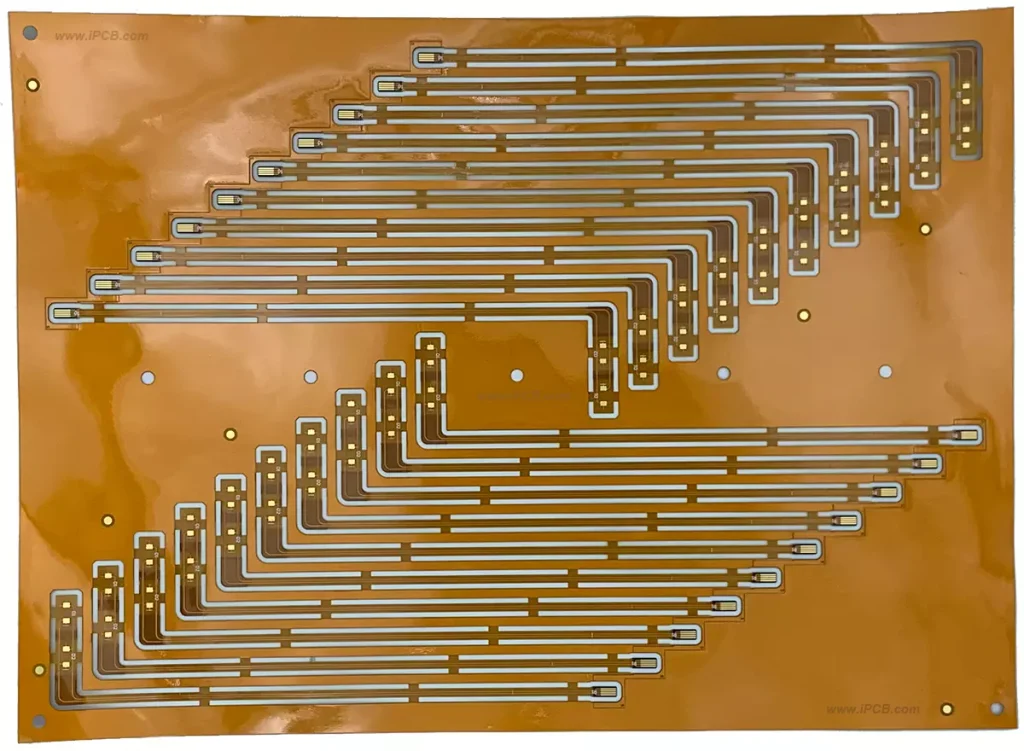
The advantages of Flexible PCB
Flexibility: The biggest advantage of FPC is its flexibility, which allows for free bending, curling, or folding in three-dimensional space, making it very suitable for application scenarios that require complex shapes or deformable products.
Lightweight: Due to its material and structural characteristics, flexible printed circuit boards are lighter than rigid PCBs, which helps to reduce the overall weight of the product.
Small footprint: It can adapt to a compact spatial layout, helping to reduce the size of the product and make it more portable.
High reliability: Flexible PCBs are more reliable because they are less prone to damage when repeatedly bent or twisted.
Efficient: Due to its excellent electrical performance and low resistance, it provides high efficiency in signal transmission.
Easy to integrate: FPC can be easily integrated with other electronic components, helping to simplify product design and manufacturing processes.
Cost effectiveness: With the continuous development of flexible printed circuit board technology and the realization of economies of scale, its costs gradually decrease, allowing more products to utilize this technology. Foot.
Disadvantages of Flexible PCB
High initial cost: Although FPC has many advantages, its initial cost is usually high, especially for high-end applications that require complex design and manufacturing.
Production difficulties: Producing FPC requires highly precise processes and equipment to ensure electrical performance and reliability.
Limited lifespan: Compared to traditional rigid PCBs, their lifespan may be shorter as they may experience fatigue and damage during prolonged use.
Maintenance difficulties: Due to the special characteristics of FPC structure and materials, FPC may be more difficult to maintain than rigid PCBs.
Size limitation: FPC size is limited by production processes and substrate materials, making it difficult to manufacture particularly large sheets.
Material limitations: Currently, FPC is mainly made of special materials such as polyimide, which are more expensive, and some materials may have an impact on the environment.
How to make a flexible PCB?
Design: Use professional software for flexible PCB design. The design process needs to consider the layout of the circuit board, the width and spacing of the wires, the number of layers, and the connection method.
Selection of substrates: Choose suitable flexible substrates, such as polyimide, polyester, etc., which have good heat resistance, insulation, and flexibility.
Production circuit: Using materials such as metal thin films or metal powders on the substrate to produce wires through processes such as printing, sputtering, and evaporation. The width and spacing of wires need to be controlled according to design requirements.
Covering the protective layer: In order to protect the wire from external environmental influences, it is necessary to cover it with a protective layer. Insulation coatings or polymer films can be used for covering.
Cutting and Prototyping: The flexible board is cut from the substrate and prototype is made for subsequent processing and assembly.
Testing and Inspection: Electrical performance testing and visual inspection of flexible circuit boards to ensure compliance with design requirements and quality control standards.
Assembly and Integration: Assemble and integrate flexible circuit boards with other electronic components to form a complete electronic product.
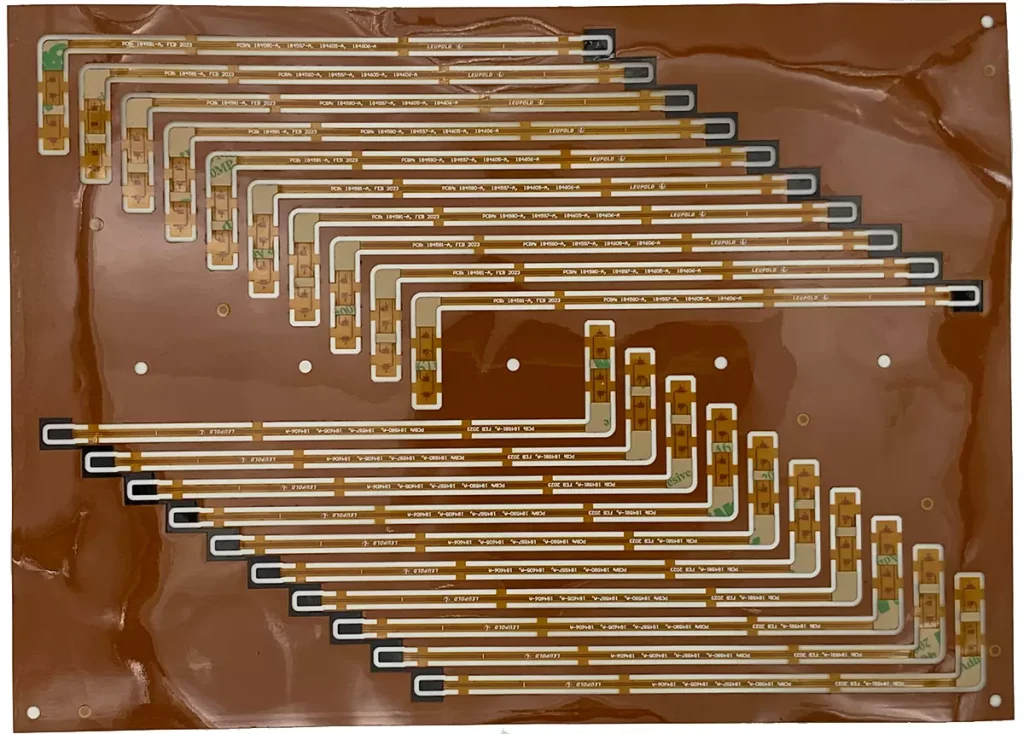
During the FPC production process, attention should also be paid to:
Keep the number of bends to a minimum: In flexible plates, the number of bends needs to be minimized to avoid applying excessive stress to the material.
Wires should be arranged in a staggered manner: By arranging wires in a staggered manner, they can better withstand bending and twisting stresses.
Wire paths should be orthogonal: In order to minimize stress during bending, wire paths should be arranged as orthogonal as possible.
When wiring, consider stress: When wiring, it is necessary to consider the stress distribution of the material during the bending process and try to match the line layout with the stress distribution of the material.
Choose appropriate materials and thicknesses: Different materials and thicknesses can affect the performance of flexible boards and need to be selected according to actual needs.
Keep clean: During the production process, the working environment needs to be kept clean to avoid pollutants affecting the performance of flexible PCBs.
Adhere to quality control standards: During the production process, you need to follow strict quality control standards to ensure that the quality of the final product meets the requirements.
In recent years, the electronic product market has grown rapidly, and the trend of miniaturization and thinness of equipment has become increasingly evident. As a result, traditional PCBs are no longer able to meet the requirements of products. Therefore, FPC manufacturers have begun to research new technologies to replace PCBs, among which FPC Board , as the most favored technology, is becoming the main connecting component of electronic devices.
FPC is widely used in various fields such as smartphones, tablets, wearable devices, and automotive electronics. Due to its excellent flexibility and bendability, it can adapt to various complex product design and assembly requirements. For example, smartphones can be used to connect various components such as displays, cameras, touch screens, etc. to achieve thin, lightweight, compact, and highly integrated designs. In automotive electronic products, FPC can be used to achieve complex wiring designs and efficient body assembly. In addition, flexible printed circuit boards have the advantages of low cost, high reliability, and environmental protection, and have been widely used and developed in the electronics industry.
Flexible PCB, as a flexible and reliable circuit board technology, plays an increasingly important role in the electronic industry. Through reasonable design, manufacturing, and application, Flex PCB can meet the needs of various products, achieving efficient and reliable circuit connections and signal transmission. With the continuous progress of technology and the increasing demand for applications, FPC will continue to leverage its advantages and make greater contributions to the development of the electronics industry.