Integrated Circuit (IC) welding, commonly known as IC weld, is a fundamental process in the electronics manufacturing industry. It involves the attachment of integrated circuits to a printed circuit board (PCB) through various welding techniques. This process is critical for ensuring the functionality and reliability of electronic devices. In this comprehensive article, we will explore the significance of IC welding, various techniques used, challenges encountered, and the latest advancements in this field.
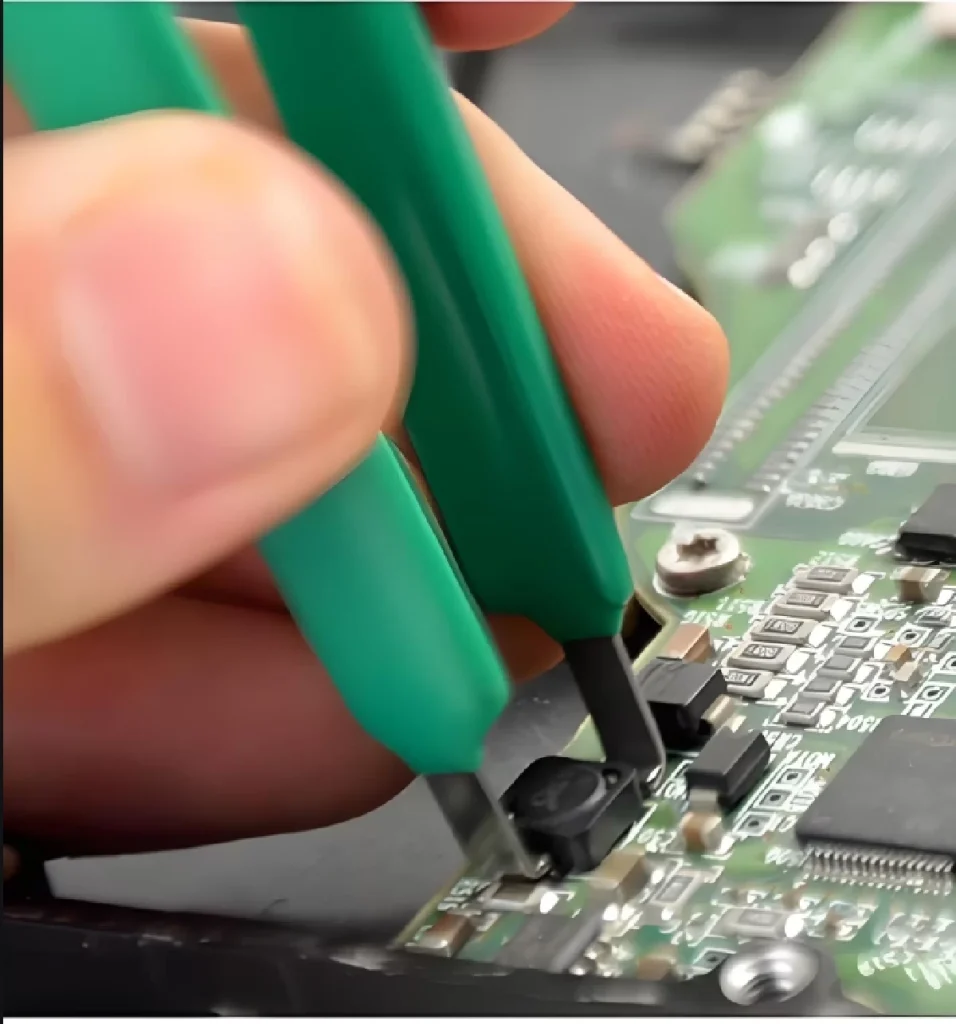
Understanding IC Weld
IC weld is a vital process that facilitates the connection of integrated circuits to PCBs. These connections are necessary for the proper operation of electronic devices. The welding process ensures that electrical signals can flow seamlessly between the IC and the PCB, which is essential for the device’s overall performance. Different techniques are used based on the specific requirements of the application, each offering distinct advantages and facing unique challenges.
The Importance of IC Weld
The IC weld process is crucial for the successful assembly of electronic devices. Integrated circuits are integral components found in nearly all electronic systems, including computers, smartphones, tablets, and industrial machinery. Properly welding these ICs to the PCB is essential for ensuring that the device operates correctly and meets its performance specifications. High-quality IC welding minimizes the risk of electrical failures and enhances the durability and reliability of electronic devices, which is crucial for consumer satisfaction and device longevity.
Key IC Welding Techniques
Several techniques are employed in IC welding, each suited to different applications and performance requirements. Understanding these techniques is essential for selecting the most appropriate method for a given application.
One of the most widely used techniques is wire bonding. Wire bonding involves using fine wires to create electrical connections between the IC and the PCB. This method can be performed using ball bonding or wedge bonding techniques. Ball bonding involves forming a small ball of gold or aluminum wire at the tip of the bonding wire, which is then heated and pressed onto the bond pad of the IC and the PCB. This technique is favored for applications requiring high reliability, such as in aerospace and automotive electronics.
Wedge bonding, in contrast, uses a wedge-shaped tool to press the wire against the bond pad, forming a wedge-shaped bond. This technique is ideal for high-speed bonding applications, such as those found in consumer electronics. Wedge bonding offers advantages in terms of speed and efficiency, making it suitable for mass production.
Another prominent IC welding technique is flip chip bonding. In this method, the IC is flipped over, and solder bumps on the IC’s surface are used to establish connections with the PCB. Flip chip bonding allows for a higher density of connections and improved performance, making it suitable for high-performance applications such as processors and memory chips. This technique is known for its excellent electrical performance and thermal conductivity.
The Solder Ball Grid Array (BGA) technique involves placing an array of solder balls on the underside of the IC. During the soldering process, these solder balls are melted to form connections between the IC and the PCB. BGA is renowned for its high-density connections and superior thermal performance, making it a popular choice for consumer electronics and other applications where space and performance are critical.
Thermosonic bonding combines heat and ultrasonic energy to create a bond between the IC and the PCB. This process involves applying ultrasonic vibrations and heat to the bonding wire, resulting in a strong connection. Thermosonic bonding is often used in applications that require precise control over the bonding process, such as medical devices and advanced electronics where high precision is essential.
Challenges in IC Weld
While IC welding is crucial, it presents several challenges that manufacturers must address to achieve high-quality results. These challenges include alignment precision, thermal management, and soldering defects.
Achieving precise alignment between the IC and the PCB is one of the primary challenges in IC welding. Misalignment can result in faulty connections, leading to electrical failures or reduced performance. Advanced alignment technologies and inspection systems are employed to ensure accurate placement and bonding of the IC, reducing the risk of misalignment and improving overall quality.
Effective thermal management is another critical challenge in IC welding. Excessive heat during the welding process can damage the IC or the PCB, leading to reliability issues. Proper control of temperature and cooling is essential to prevent thermal damage and ensure the longevity of the electronic device. Advanced cooling technologies and thermal interface materials are used to manage heat effectively and maintain optimal performance.
In wire bonding, the quality of the wire bonds is crucial for reliable electrical connections. Factors such as wire diameter, bond strength, and cleanliness can affect bond quality. Rigorous quality control measures and advanced bonding equipment are employed to ensure that wire bonds meet the required specifications and performance standards. This includes using high-precision bonding tools and conducting regular inspections to detect and address any issues.
Soldering defects, such as solder bridges, cold solder joints, and insufficient solder, can occur during the IC welding process. These defects can lead to poor electrical connections and device failures. Manufacturers use precise soldering techniques and advanced inspection systems to detect and correct soldering defects, ensuring that only high-quality devices are produced. Automated inspection systems and real-time monitoring help identify and address issues early in the manufacturing process.
Advancements in IC Weld Technology
The field of IC welding has seen significant advancements in recent years, driven by the need for higher performance, miniaturization, and increased reliability. These advancements include automation, new bonding materials, improved inspection techniques, and enhanced thermal management solutions.
Automation has transformed the IC welding process by improving speed, accuracy, and consistency. Automated welding systems use robotic arms and advanced control systems to perform welding operations with high precision. Automation reduces the risk of human error and enhances overall efficiency, making it possible to meet the demands of high-volume production and complex assemblies.
New bonding materials have been developed to improve the performance and reliability of IC welding. Advanced materials, such as low-thermal-expansion solder and high-strength bonding wires, offer better electrical performance and durability. These materials are designed to meet the evolving requirements of modern electronic devices, addressing challenges related to heat dissipation, mechanical stress, and long-term reliability.
Inspection techniques have also advanced significantly, providing manufacturers with better tools for detecting defects and ensuring quality. High-resolution imaging systems, such as X-ray and optical inspection, enable detailed examination of welds and connections. These advanced inspection techniques help identify issues early in the manufacturing process, reducing the likelihood of defective products and ensuring that only high-quality devices reach the market.
Enhanced thermal management solutions address the challenges of heat dissipation in IC welding. Advanced cooling technologies, such as heat spreaders, thermal interface materials, and improved heat sinks, help manage heat and prevent damage to the IC and PCB. Effective thermal management is essential for maintaining the reliability and performance of electronic devices, particularly in high-power and high-performance applications where heat can be a significant issue.
Applications of IC Weld
IC weld is used across a wide range of industries and applications. In consumer electronics, such as smartphones, tablets, and laptops, IC welding is crucial for connecting integrated circuits to the PCB. The reliability and performance of these devices depend on the quality of the IC welds, as high-density interconnects and miniaturized components require precise welding techniques to ensure proper functionality.
The automotive industry heavily relies on IC welding for assembling electronic components in vehicles. IC welding is used in critical systems such as engine control units, infotainment systems, and safety features. The reliability of these systems is essential for vehicle performance and safety, making high-quality IC welding a key factor in automotive electronics.
In medical devices, IC welding ensures the reliability and accuracy of electronic components. Medical devices often require high precision and durability, making IC welding a critical process. Applications include diagnostic equipment, monitoring devices, and implantable devices, where precise and reliable electronic connections are essential for effective operation.
Industrial equipment, including manufacturing machinery and control systems, also relies on IC welding. The performance and reliability of industrial equipment depend on the quality of electronic components and their connections to the PCB. IC welding ensures that these components operate effectively in demanding environments, contributing to the efficiency and reliability of industrial operations.
Conclusion
IC weld is a crucial process in the electronics manufacturing industry, providing essential connections between integrated circuits and printed circuit boards. The process involves various techniques, each with its own advantages and challenges. Advances in technology have significantly improved the efficiency and reliability of IC welding, addressing issues such as alignment precision, thermal management, and soldering defects. As electronic devices continue to evolve, IC welding will remain a critical component of manufacturing, ensuring the performance and durability of modern electronics.
This article has explored the fundamentals of IC weld, including its importance, techniques, challenges, and recent advancements. By understanding these aspects, manufacturers can make informed decisions about best practices for IC welding and continue to produce high-quality electronic devices that meet the demands of an ever-evolving market.