As electronic devices continue to develop towards miniaturization, high performance and low power consumption, BGA (Ball Grid Array) circuit board technology has gradually become an important part of modern electronic products.
As an advanced integrated circuit packaging technology, BGA packaging has the advantage of providing higher integration and better heat dissipation performance, and is widely used in computers, communications, consumer electronics, automotive electronics and other fields.
This article will explore in depth the principles, design, production process and important role of BGA pcb board in practical applications.
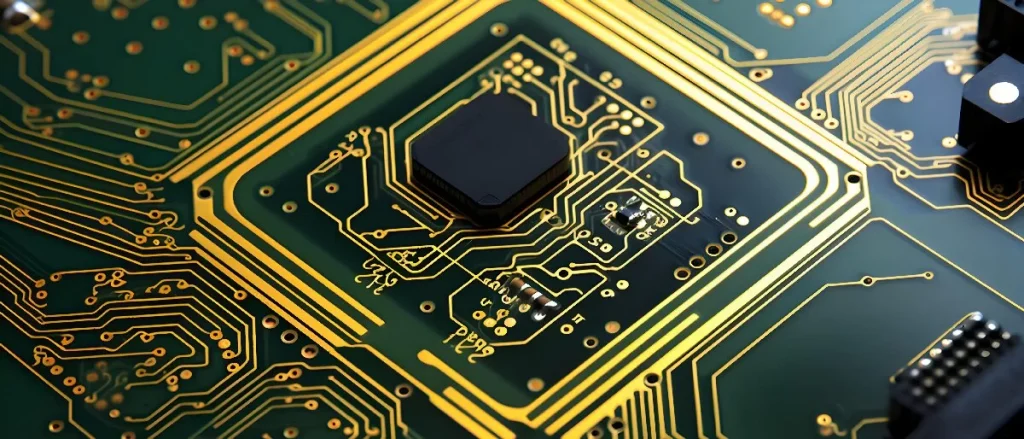
Basic principles of BGA circuit boards
BGA circuit boards are PCB (Printed Circuit Board) products packaged based on ball grid array technology. This packaging form is different from traditional pin packaging. BGA uses solder balls as connection points, which are evenly distributed at the bottom of the chip to form a matrix array. Therefore, the number of solder joints on the BGA circuit board is more, and the soldering position is more compact, which effectively improves the integration of the circuit board.
The basic principle of the BGA circuit board is to connect the integrated circuit chip with the solder points on the circuit board, and these solder points are electrically and mechanically connected through solder balls. Since the solder balls of BGA package are made of tin alloy solder, the welding performance is excellent and the welding precision is high, which makes BGA circuit boards have significant advantages in environments with high-density wiring and high-performance requirements.
Design principles of BGA pcb board
The design of BGA circuit boards should not only consider the packaging requirements of the integrated circuit itself, but also need to comprehensively design the layout, wiring and heat dissipation of the entire circuit board according to the actual application scenario. The following are several key principles for BGA circuit board design:
- Reasonable layout and wiring
The layout of BGA circuit boards needs to ensure that the signal lines are as short as possible to reduce signal propagation delays, while ensuring the quality of power lines and ground lines. BGA packaging sometimes causes long signal paths, so long signal routing should be avoided as much as possible during design, and the stability of signal transmission should be ensured by optimizing the number of PCB layers and signal layer wiring. - Thermal design considerations
BGA circuit boards face heat dissipation problems due to their compact packaging. High-power density circuit boards may cause heat accumulation, affecting the stability and life of the chip. Therefore, in the design process of BGA circuit boards, special attention should be paid to heat dissipation design. Designers can improve the heat dissipation effect by adding heat dissipation layers, optimizing the layout of heat dissipation holes, and selecting suitable thermal conductive materials. - Welding feasibility
The welding of BGA packages is a key link in the production of BGA circuit boards. Due to the large number of solder balls and their dense distribution, the welding process must be very precise. When designing, the feasibility of the welding process should be considered to ensure that the welding points can be evenly heated to avoid the phenomenon of cold welding or poor welding. Reasonable welding point spacing and solder ball diameter are crucial to ensure the quality of BGA circuit boards.
Manufacturing process of BGA circuit boards
The production process of BGA circuit boards includes multiple steps, from material selection, PCB production to chip packaging, welding and other complex processes, each of which requires precise operation and strict quality control.
- Production of PCB substrates
The first step in making BGA circuit boards is to produce PCB substrates. It is very important to choose high-quality PCB materials, and high-frequency and high-speed composite materials are usually used to ensure the stability of the signal. The production of substrates includes processes such as patterning, etching, electroplating and surface treatment. The etching process determines the wiring accuracy of the circuit, while the electroplating process provides a conductive metal layer for welding. - Chip packaging
BGA packaged chips connect the chip to the substrate through a high-temperature curing process. This process usually uses aluminum wire or copper wire to connect the chip pins to the solder points on the circuit board. After completion, the chip will be wrapped with protective materials to form a stable package structure. - Soldering process
Soldering is an important part of BGA circuit board production, and the reflow soldering process is used. Reflow soldering is to heat the solder to the melting point so that the solder balls are connected to the pads on the circuit board to complete the electrical connection. Since the BGA solder balls are closely arranged on the circuit board and the welding precision is high, X-ray detection technology is usually required to check the welding quality to ensure that there is no cold soldering or short circuit at the welding point. - Testing and inspection
After the BGA circuit board is produced, it needs to undergo rigorous testing and inspection. The testing process includes electrical testing, functional testing, and X-ray inspection. Through these tests, problems on the circuit board can be effectively detected and corrected or reworked. Usually, BGA circuit boards also need to undergo stress testing and thermal cycle testing to ensure that they can operate stably under high temperature, low temperature, vibration and other environments. - Application fields of BGA circuit boards
BGA circuit boards are widely used in many industries, especially in areas that require high-density integrated circuits. The following are some of the main application areas: - Computer and communication equipment
In computer motherboards, graphics cards, and network equipment, BGA circuit boards have become the mainstream choice due to their high integration and excellent heat dissipation performance. With the continuous improvement of computer hardware performance, BGA circuit boards play an increasingly important role in the packaging of high-performance chips such as processors, memory chips, and graphics cards. - Consumer electronics
BGA circuit boards have become a common packaging method in consumer electronics products such as smartphones, tablets, TVs, and smart home devices. BGA packaging can support the integration of more functional modules, improve the performance and stability of equipment, and can effectively reduce space requirements. - Automotive electronics
With the continuous improvement of the level of automotive intelligence, BGA circuit boards are also widely used in automotive electronic systems, such as on-board computers, navigation systems, and smart meters. The application of BGA circuit boards in the field of automotive electronics can help automakers improve the functionality, stability, and safety of their products. - Industrial control and medical equipment
The application of BGA circuit boards in industrial control and medical equipment is also gradually increasing. Due to its superior electrical and mechanical properties, BGA circuit boards are widely used in PLCs (programmable logic controllers), automation equipment, and medical monitoring systems, helping equipment to provide more efficient operation and more precise control.
Future development of BGA circuit boards
With the continuous advancement of technology, the application scope of BGA circuit boards will be further expanded, and their performance will be further improved. In the future, BGA circuit boards will develop in the direction of smaller size, higher density, and higher heat dissipation performance. At the same time, with the continuous development of technologies such as 5G communications, artificial intelligence, and the Internet of Things, BGA circuit boards will usher in a wider market demand and become an important support for the next generation of electronic technology.
In short, as an important part of modern electronic products, BGA circuit boards have technical advantages that make them occupy an important position in high-performance and compact products. With the continuous advancement of technology, BGA circuit boards will play a greater role in more fields and provide strong support for the development of modern electronic products.
Challenges and solutions of BGA circuit boards
Although BGA circuit boards have many advantages, they still face some challenges in actual production and application. These challenges include manufacturing process complexity, welding quality problems, and heat dissipation design difficulties. Here are some common challenges and their corresponding solutions:
- Soldering Difficulty
Due to the tight soldering points of BGA circuit boards, traditional soldering processes often have difficulty in ensuring the reliability of each soldering point. Poor soldering quality may lead to problems such as cold soldering, short circuits, and poor soldering, which will affect the normal use of the circuit board.
Solution: In order to overcome the soldering difficulties, a high-precision reflow soldering process can be used, and the soldering quality can be detected by X-ray inspection technology. In addition, automated soldering robots and precise temperature control systems can effectively improve the reliability of soldering. For complex BGA packages, the use of laser soldering or airflow-assisted soldering technology is also an effective solution.
- Heat dissipation problem
The high-density integrated design and complex electrical functions of BGA circuit boards cause them to generate a lot of heat during operation. If the heat is not effectively dissipated, it may cause the circuit board to overheat, affect the chip performance, and even cause chip damage. Therefore, heat dissipation design has become an important issue in BGA circuit board design.
Solution: In order to solve the heat dissipation problem, designers usually adopt a multi-layer PCB design to increase the thermal conductivity by adding a heat dissipation layer. In addition, the use of auxiliary heat dissipation measures such as thermal conductive materials, thermal conductive silicone and metal heat sinks is also an effective way to solve the heat dissipation problem of BGA circuit boards. In high-performance BGA circuit boards, liquid cooling or air cooling systems may also need to be added to ensure the best heat dissipation effect.
- Electromagnetic interference problem
As the package size of BGA circuit boards becomes smaller, the current and signal line density on the circuit board increase, which may lead to electromagnetic interference (EMI) problems. Electromagnetic interference not only affects the normal operation of the equipment, but also may affect the performance of other surrounding electronic equipment, and even violate relevant regulatory standards.
Solution: In order to reduce electromagnetic interference, designers can reduce the crossing and interference of signal lines through reasonable layout and wiring. For example, use ground plane design to separate signal lines from power lines, and use shielding layers to isolate electromagnetic interference signals. At the same time, the use of filters, noise suppression components and appropriate grounding design can effectively reduce electromagnetic interference.
- Cost control
Although BGA circuit boards have high performance and stability, their production process is complex and the material cost is high, especially in high-frequency and high-speed applications, the required materials and processes are more sophisticated. Therefore, the production cost of BGA circuit boards is often more expensive, which may become one of the factors restricting its popularity.
Solution: In order to reduce costs, companies can optimize production processes and adopt more efficient production equipment and materials. For example, the use of high-density interconnect (HDI) technology and miniaturized components can reduce the area and material consumption of PCBs, thereby reducing manufacturing costs. In addition, the introduction of mass production and automated production lines can also help reduce production costs.
Market Prospects of BGA Circuit Boards
With the continuous development of science and technology, the application areas of BGA circuit boards are also expanding. Especially in some emerging industries, BGA circuit boards will play an increasingly important role.
- 5G Communication
The promotion of 5G technology has put forward higher requirements for electronic equipment, especially in signal processing, data transmission rate and device size. BGA circuit boards have become an ideal choice for 5G communication equipment with their high density, high-speed performance and good heat dissipation characteristics. With the construction of 5G base stations, terminal equipment and network infrastructure, the demand for BGA circuit boards is expected to grow significantly. - Artificial Intelligence
The development of artificial intelligence technology, especially in the fields of deep learning and computer vision, has put forward higher requirements for the processing power of electronic equipment. BGA circuit boards can provide more powerful computing power in artificial intelligence devices, and have advantages in high-speed processing, storage and heat dissipation. In the future, BGA circuit boards will play a key role in artificial intelligence chips and smart hardware. - Autonomous driving
As an important development direction in the future transportation field, autonomous driving technology also puts forward higher requirements for automotive electronic systems. The application of BGA circuit boards in autonomous driving systems can provide efficient signal processing and computing capabilities, while having good anti-interference and heat dissipation performance. With the maturity of autonomous driving technology, BGA circuit boards will play an increasingly important role in autonomous driving vehicles. - Internet of Things
The popularity of Internet of Things technology has promoted the emergence of a large number of smart devices, which usually require high-density integrated circuits and small size to adapt to different application scenarios. BGA circuit boards can meet this demand and are widely used in smart homes, industrial Internet of Things, smart medical and other fields. As the number of Internet of Things devices continues to increase, the market demand for BGA circuit boards will continue to grow.
Conclusion
As an advanced packaging technology, BGA circuit boards have an irreplaceable and important position in modern electronic products. Its high-density integration, high performance and miniaturization have made it widely used in many industries such as computers, communications, consumer electronics, and automotive electronics.
With the continuous advancement of technology, the manufacturing process and performance of BGA circuit boards will be further improved, providing strong support for the innovation of various electronic devices.
However, the production and application of BGA circuit boards still face some challenges, especially in welding, heat dissipation, electromagnetic interference, etc. In order to overcome these challenges, the industry needs to continuously innovate technology and optimize design and manufacturing processes.
In the future, with the rapid development of emerging technologies such as 5G, artificial intelligence, autonomous driving and the Internet of Things, BGA circuit boards will play a greater role in more fields and become an important force in promoting scientific and technological progress.
In general, BGA circuit boards are not only a key component of modern electronic technology, but also represent the trend of future electronic equipment development. With the industry’s continuous pursuit of high performance, low power consumption and miniaturized design, BGA circuit boards will continue to play an important role in the global electronics industry and promote the birth and development of various new electronic products.