Introduction: The intersection of craft and art
In stained glass works, each piece of glass is a narrative of light and shadow, and it is the shining metal welds that splice these fragments into a complete picture. Stained glass solder is not only an adhesive that connects each piece of glass, but also a tool for artists to express rhythm, order and details. It not only carries the stability of the structure, but also carries the life and temperature of the work.
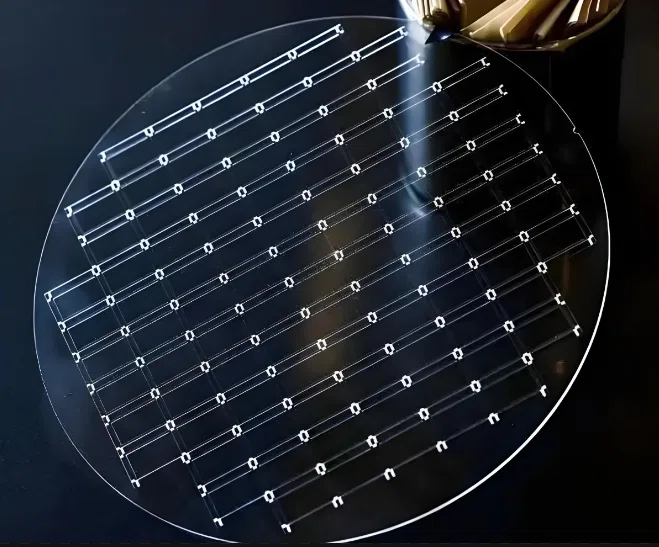
From church window grilles to modern home decorations, from ancient Western art to contemporary handmade creativity, stained glass art has lasted for a long time. One of the technical supports behind it is the continuous evolution of welding technology and the continuous innovation of materials. When many people mention welding, the first thing they think of is industrial manufacturing, PCB pads, and circuit repair, but in glass art, welding is closely linked to aesthetics.
The history of stained glass solder can be traced back to the Middle Ages, when craftsmen began to use lead strips and tin alloys to connect colorful glass into large patterns to decorate churches and courts. With the development of materials science, traditional lead-containing solders are gradually being replaced by new alloys that are more environmentally friendly and have more stable performance, but the spirit of craftsmanship has never changed – the pursuit of firm connection and delicate performance.
Modern welding is not only a “bonding” at the physical level, but also a “collage” of artistic language. Glass materials of different thicknesses, colors, and textures require different types of solders and techniques to truly present a complete picture in the designer’s mind. Mastering this craft requires both technical accumulation and artistic perception.
Therefore, this article will conduct a comprehensive discussion around stained glass solder, systematically introduce its basic principles, material properties, operating procedures, common problems and future development trends, and strive to provide a clear, practical and forward-looking popular science guide for different roles such as practitioners, enthusiasts, and purchasers
Detailed explanation of basic concepts
To understand the technical principles of stained glass solder, you first need to figure out what it is and what role it plays in the entire stained glass process chain.
Simply put, stained glass solder is a solder used to connect and fix the copper foil between colored glass sheets. It is generally composed of metal alloys, which melt at high temperatures and fill the joints to achieve structural fixation and conductive functions. Although solder is widely used in electrical engineering, it focuses more on structural stability, aesthetics and plasticity in stained glass, rather than electrical performance.
Material composition: Tin-lead alloy is the main force
Traditionally, stained glass solder is mainly tin-lead alloy, and the most commonly used ratio is 60% tin and 40% lead (60/40), or a 63/37 combination closer to the eutectic point. This ratio of solder has a moderate melting point (between 183°C and 190°C), a narrow melting range, and can solidify quickly during operation, facilitating the formation of a smooth and full weld.
Since the soldering of stained glass is usually done manually, the solder needs to have the following characteristics:
Good wettability: can quickly adhere to the copper foil and extend;
Stable fluidity: will not flow around and cause pollution during soldering;
Good surface tension: can automatically gather after melting to form a flat solder line.
In addition to 60/40 and 63/37, some artists also use 50/50 or higher tin content alloys, and choose the appropriate formula according to the different needs of the project.
Lead-free solder: a balance between environmental protection and safety
With the tightening of environmental regulations, such as the EU’s RoHS standard, the use of lead as a heavy metal in solder is strictly restricted. Therefore, lead-free solder is gradually accepted in the art field. Common lead-free solders include tin-silver-copper alloy (SAC), tin-copper alloy, etc. Although the melting point is high (above 220°C), good compatibility with tool materials has been achieved by improving flux.
However, lead-free solder faces some challenges in stained glass solder applications:
Higher soldering temperature may affect glass safety;
Glossiness is not as good as lead-containing solder;
The cost is slightly higher and the operation difficulty is slightly increased.
Analysis of the difference with circuit board solder
Although stained glass solder and solder used for electronic circuits are essentially tin-based alloys, there are significant differences in the application environment, process requirements and performance requirements. First of all, from the purpose of use, electronic solder mainly focuses on the conductivity and reliability of mechanical connection, and the solder joints must withstand thermal cycles in current transmission and long-term operation; while in stained glass soldering, the main task of solder is to connect the structure and improve the aesthetics, and almost no electrical function is involved.
Secondly, the operation method is also different. Circuit board soldering is mostly completed by automated equipment, such as wave soldering, reflow soldering, etc., which requires the solder to have a precise melting point and good fluidity control to match the machine parameters. Stained glass is almost entirely soldered by hand. The artist relies on his eyesight and touch to control the release and direction of the solder, and emphasizes the ductility and surface tension of the solder, striving to form smooth, flat and decorative metal lines between the glass.
In addition, there are differences in the melting point requirements of solder. In order to protect components in electronic products, alloys with low melting points and high stability are generally selected; while the solder of stained glass can withstand relatively higher temperatures, especially when lead-free materials are used, the melting point is usually higher, which also poses more challenges to the craftsman’s operating skills.
Finally, from the perspective of flux matching, the flux in electronic welding is usually non-corrosive residual type, which is convenient for long-term electrical reliability maintenance; while the flux matched with stained glass solder focuses more on the wetting effect and deoxidation ability during welding, and a cleaner is required to remove the residue after welding to avoid corrosion and affect the appearance.
In summary, although the two use similar metal materials, stained glass solder and PCB solder reflect their own unique industry characteristics in terms of performance requirements, process flow and final effect.
Function and selection of flux
In the operation of stained glass solder, the selection of flux is also very critical. Flux can remove oxides, improve wettability, and make solder easier to adhere to the copper strip or glass border. Common types include:
Liquid rosin-based flux: easy to operate and evaporate quickly;
Paste flux: strong viscosity, suitable for fine control of soldering wires;
Neutral or environmentally friendly flux: reduce smoke and odor.
Choosing a suitable flux not only affects the quality of soldering, but also affects the safety and comfort of the working environment.
Full explanation of the soldering process
In the stained glass solder process, the formation of each soldering wire comes from a set of seemingly simple but actually very sophisticated steps. This is not only a reflection of the control of materials, but also a test of the experience and skills of the craftsman. From preparation to completion, every detail will affect the beauty and durability of the final work.
Preliminary preparation
Before the formal soldering, the artist needs to cut out colored glass pieces of suitable size and shape according to the design drawings. This process requires the use of professional glass cutters, rulers and pliers with extremely high precision. The edges of each piece of glass are polished to better adhere to the copper foil and enhance structural stability.
Then, the copper foil is applied. The copper foil used is usually a copper tape with an adhesive layer. The thickness and width are selected according to the thickness of the glass and the fineness of the work. It is the key to ensure the subsequent strong welding to wrap the copper foil evenly around the edge of each piece of glass and gently compact it. The copper foil is like a “guide rail” that provides a foundation for the solder to adhere.
Applying flux
Although the use of flux cannot be seen in the finished product, it plays a decisive role in the quality of welding. Before welding, use a brush to evenly apply liquid flux on the surface of the copper foil. This can help remove the surface oxide layer and improve the wetting ability of the solder, allowing it to adhere and extend better.
There are many types of flux, including rosin-based, halogen-free and environmentally friendly, low-corrosive, etc. In glass art, many artists prefer to use neutral flux that will not leave traces or corrosion residues after cleaning to maintain the long-term stability of the work.
Manual soldering
The soldering process is the climax of the entire process. Use a solder gun to heat the solder bar to above the melting point, and slowly apply the molten solder to the surface of the copper foil through the tip of the soldering pen. In this process, the speed, force, and routing direction all need to be highly controlled to ensure that the solder line is flat, uniform, and beautiful.
Compared with automated reflow soldering or wave soldering in electronic engineering, stained glass solder emphasizes the flexibility of human control and visual judgment. For example, the artist needs to judge whether each section of copper foil is fully wetted and whether the solder forms a “bump” or a “smooth” transition in the right position.
Although the solder used in the soldering process is similar to that of circuit board soldering, the purpose is different. Circuit board soldering focuses more on conductivity and thermal stability, while stained glass solder focuses more on the continuity and decorativeness of the weld and the impact on the overall flow of the lines of the work.
Post-processing
After the soldering is completed, the work enters the post-processing stage. First, the soldering residue, especially the flux residue, must be removed, otherwise it is easy to corrode in light or moisture. Generally, a neutral detergent and a soft brush are used for cleaning, and the solder wires are dried thoroughly.
In order to enhance the visual effect of the solder wires, they are sometimes oxidized. For example, chemical oxidants are used to dye the solder wires black or bronze to make the work more retro or modern. Finally, the solder wires can be polished with anti-oxidation wax or brightener to make the metal lines more shiny under the light.
Common Problem Analysis and Skill Improvement
In the actual stained glass solder operation process, even with high-quality materials and standardized processes, various problems are often encountered. Understanding the causes of these problems and mastering the corresponding coping skills are the key to improving the quality of welding and the aesthetics of the finished product.
Uneven solder joints or rough appearance
This is one of the most common problems for novices. The reasons for uneven solder joints usually include: uneven distribution of flux, insufficient solder heating time or temperature, and uncleaned copper foil surface. When the solder cannot fully wet the copper foil, the solder joints are prone to accumulation or breakage, and appear “granular” or “intermittent”.
Solution tips:
Make sure the copper foil surface is clean and free of oxidation.
Heat the copper foil properly before soldering so that the solder can flow more smoothly.
Use high-quality, uniform solder bars to avoid solder joint defects caused by low-purity alloys.
Keep pushing the soldering iron evenly and slowly to avoid repeatedly heating the same place.
Poor solder joints or loose connections
Poor solder joints may be difficult to detect visually, but a slight force may cause the solder joint to loosen. Such problems are often related to the solder not fully soaking the copper foil, or the temperature is too low or the time is too short during the soldering process.
Solution tips:
Check whether the soldering temperature meets the standard. It is generally recommended to keep the soldering iron temperature above 300°C (depending on the type of solder).
Do not wait too long after applying flux before soldering to prevent it from failing.
Do not try to complete the solder joint quickly. Use even and slow movements to ensure that the solder fully “bites” the copper foil at the edge of the glass.
Oxidation or discoloration of solder
If exposed to air for a long time without timely cleaning, gray-black spots or uneven oxidation may appear on the surface of the solder joint. This not only affects the appearance, but also weakens the mechanical strength of the solder joint.
Solution tips:
Clean the residual flux as soon as possible after soldering.
Anti-oxidation wax, solder joint protective coating and other treatments can be used to delay the oxidation process.
Store solder and flux in a sealed and moisture-proof manner to prevent the material from oxidizing before use.
Copper foil warping or falling off
Warping caused by poor copper foil adhesion will cause the solder joint to lack support, resulting in discontinuous solder wires or loose structures. This often occurs when the glass edge is improperly handled or the adhesive pressure is insufficient.
Solution tips:
Use high-quality copper foil tape and ensure that the glass edge is polished and smooth.
Press the copper foil with your fingers or roller tool to ensure a firm fit.
Start soldering within a short time after bonding to prevent the copper foil from warping over time.
Solder accumulation or “explosion point”
The solder fails to flow evenly, or the temperature suddenly changes and causes local rapid melting, which is prone to “tin accumulation” or “tin explosion”. This will affect the flatness and appearance of the solder wire, especially in the display of works.
Solution tips:
Control the speed of the soldering iron to avoid staying at the same point for a long time.
Replace the soldering tip regularly to keep the heating efficiency stable.
Never “pile up” the solder with force, but let it spread naturally.
Residue of solder flux affects the appearance
Even if high-quality solder flux is used, if it is not thoroughly cleaned after soldering, it will leave spots and foggy deposits, affecting the transparency of the glass and the overall artistic effect.
Solution tips:
Use a neutral detergent or a special flux removal liquid.
Try to clean as soon as possible after soldering to avoid solidification of residues.
After cleaning, wipe with a dry cloth or polish with a soft brush to restore the brightness of the glass.
Modern application expansion and style evolution
Stained glass solder, a traditional soldering process, was originally used to make artworks such as church window grilles, religious decorations, and handmade lamps. With the continuous evolution of material technology and modern design concepts, its application scenarios have long surpassed the scope of classical art and are developing in a broader direction such as commercial space, home decoration, and even architectural structure.
Bold attempts in architectural art
In modern architectural design, stained glass is no longer limited to small-scale decorative decoration, but gradually moves towards large-scale, structural integration. With its exquisite welding frame and flexible pattern layout, the stained glass solder process is often used in indoor partitions, curtain walls, sun rooms and other fields.
For example, in high-end hotels or villas, the semi-transparent partition wall created by this process is not only beautiful, but also can introduce natural light and enhance the texture of the space. At the same time, since the welding frame line itself has a certain mechanical strength, with the structural support of the metal frame, the artistic expression of high-rise glass curtain walls can also be achieved.
Personalized interpretation in home customization
With the improvement of consumers’ aesthetic awareness, stained glass solder has been widely introduced into the home improvement market and has become a new favorite for customized furniture and home accessories. Whether it is a retro-style Tiffany lamp, a European panel door, or a modern geometric color-matching window piece, it can be finely realized with the help of welding technology.
The solder frame not only stabilizes the structure, but also can be polished, electroplated, and given a variety of visual effects such as bronze, bright silver, and matte black, making the entire work more decorative while maintaining functionality.
In addition, some home furnishing brands
Modular stained glass components have been launched. Customers only need to choose the pattern style and color scheme, and professional workshops can complete the welding and assembly to meet the needs of small batches and high customization.
Extension of art education and cultural and creative industries
Stained glass solder has gradually become an important part of art education. Many art colleges and art schools have included it in craft courses, allowing students to participate in real manual welding to improve their understanding of the relationship between metal, glass and color.
At the same time, some cultural and creative brands and independent designers have also incorporated this technology into peripheral products, such as key chains, pendants, night lights, puzzle frames, etc. These products are not only strong in craftsmanship and unique, but also have good commercial conversion potential.
Especially during the festive season, some art fairs often see “festival-limited” stained glass pendants, Christmas pendants, etc., which are varied in form and flexible in shape, and are very popular with consumers.
Cross-border development integrating new technologies
In addition to the continuous inheritance and evolution of traditional welding technology, modern stained glass solder has also begun to cross-integrate with other technologies, deriving more innovative forms. For example, some studios try to embed LED light strips into welding structures to create “dynamic colored glass” that can be lit; or combine smart dimming glass with painted patterns to achieve the organic unity of technology and art.
In addition, with the development of 3D printing technology, some metal welding molds and complex support structures can also be prefabricated by printing, greatly improving welding efficiency and stability. In the future, there may even be AI automatic welding patterns to assist designers in efficiently completing batch customization tasks.
Trends in sustainable and environmentally friendly design
In the contemporary market environment that emphasizes environmental awareness, the material selection of stained glass solder is gradually shifting towards green. Many high-end workshops have abandoned traditional lead-based solders and switched to low-toxic or lead-free alloys to ensure the health and safety of operators and end users.
The use of recycled copper foil and environmentally friendly flux is also gradually becoming popular, and some glass brands promote the use of recycled glass as raw materials to build a more sustainable process. These efforts not only reflect the response of modern technology to social responsibility, but also enhance the brand image and trust of stained glass in the global market.
Summary
The stained glass solder process is not only a technical means to connect glass and metal, but also an artistic expression that combines traditional craftsmanship with modern design concepts. Whether in church window grilles, home lighting, or modern architectural partition design, this process shows a stunning unique charm.
With the continuous advancement of environmentally friendly materials, modern manufacturing equipment and creative design, stained glass solder is gradually breaking away from the label of “classical” and becoming a new bridge connecting art, practicality and business. For practitioners who love arts and crafts or are engaged in home decoration, construction, cultural creation, education and other related industries, mastering this technology can not only increase the added value of products, but also have the opportunity to develop their own unique style.
In the future, this traditional welding art that originated a hundred years ago will continue to shine with new brilliance in the ever-changing applications.