In the manufacturing of modern electronic equipment, printed circuit boards (PCBs) play a vital role as the basic platform for connecting and supporting various electronic components. The soldering process of circuit boards is one of the core links in PCB production, and the selection of solder mask materials directly affects the soldering quality, production efficiency and reliability of the final product.
With the continuous development of technology, more and more new solder mask materials have emerged. Among them, peelable solder mask is a widely used and highly advantageous material. It can not only effectively protect the soldering area on the surface of the circuit board, but also be easily removed after the soldering is completed, which facilitates the later processing and assembly of the circuit board.
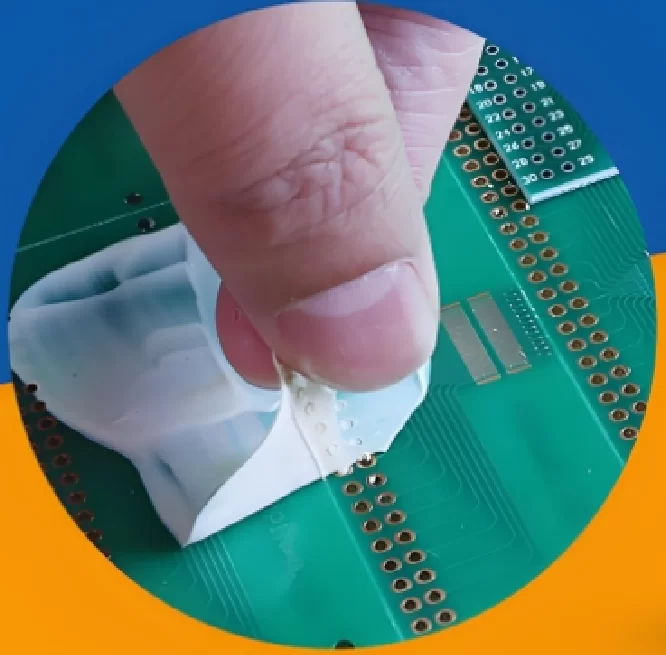
What is a peelable solder mask?
As the name suggests, a peelable solder mask is a solder mask material that can be easily peeled off after the circuit board is produced. Unlike traditional permanent solder masks, peelable solder masks do not remain on the surface of the circuit board after the entire soldering process, but can be removed by physical means (such as manual or mechanical peeling), so as not to affect the subsequent use of the circuit board.
The role of the solder mask is to prevent the solder from contaminating these areas during the soldering process by covering certain areas of the circuit board. Traditional solder masks are usually permanently applied to the surface of the circuit board, while strippable solder masks provide more flexibility because they can be easily removed after the soldering process is completed, avoiding contamination or unnecessary subsequent cleaning work.
How strippable solder masks work
The working principle of strippable solder masks is actually not complicated. It is mainly made of a special polymer material, which is coated on the surface of the circuit board and forms a protective film through thermal curing. This film plays an important role in the soldering process to prevent solder, welding gas or other contaminants from entering the area that needs to be protected.
After soldering is completed, this mask film layer does not require complex cleaning or removal like traditional solder masks, but can be easily peeled off directly by hand or tools. This feature makes strippable solder masks particularly suitable for circuit boards that need to protect areas but do not want to affect subsequent processing, especially in the production of products that require high precision and high reliability, it can effectively improve work efficiency and product quality.
Main features of strippable solder masks
Easy to peel:
The most prominent feature of strippable solder masks is their easy peelability. Compared with traditional solder masks, peelable solder masks are not only easy to apply, but can also be quickly removed by physical means after the circuit board is manufactured. This feature makes the production process more flexible, does not require additional cleaning work, and saves a lot of time and cost.
Good protection function:
The peelable solder mask can effectively protect the sensitive areas of the circuit board during the soldering process to prevent damage to it by solder, heat or welding gas. For complex circuit board designs, especially multi-layer circuit boards, this mask can prevent excessive solder from entering areas that do not need to be soldered, prevent short circuits, leaks and other problems, and thus improve the soldering quality of the circuit board.
High temperature resistance:
During the soldering process, the circuit board is often exposed to high temperature environments, and the solder mask material needs to have sufficient heat resistance to effectively protect the circuit board from damage. Peelable solder masks usually have high high temperature resistance and can withstand the heat generated during the soldering process without deformation or cracking, ensuring the protective effect of the mask.
Environmental protection and low cost:
Compared with other solder masks, the materials of peelable solder masks are usually more environmentally friendly and relatively inexpensive. Due to its easy-to-peel property, the mask after removal will not cause excessive pollution to the environment, nor will it produce excess waste. In addition, due to its simple production process and convenient application, the use of peelable solder mask can effectively reduce production costs.
Wide range of applications:
Peelable solder mask has a wide range of applications in many fields. For example, in the manufacturing of electronic products in industries such as consumer electronics, automotive electronics, medical equipment, and communication equipment, peelable solder mask can play an important role. It is not only suitable for traditional PCB production, but also suitable for the manufacture of special types of circuit boards such as flexible circuit boards and HDI circuit boards.
Application scenarios of peelable solder mask
Multilayer circuit board production:
For the production of multilayer circuit boards (Multilayer PCB), the use of peelable solder mask has significant advantages. In the production process of multilayer circuit boards, different welding steps may involve different welding processes, and some areas may need to be protected during certain welding processes. The use of peelable solder mask can effectively prevent these areas from being contaminated by solder, ensure the welding quality of each layer, and also avoid the trouble caused by multiple cleaning.
High-frequency circuit board:
High-frequency circuit boards have extremely high requirements for welding quality. During the soldering process of high-frequency circuit boards, solder contamination and overheating may cause the performance of the circuit board to deteriorate or even fail to work properly. By applying peelable solder mask on these circuit boards, these problems can be avoided and the normal operation of the circuit board can be ensured.
Protection of precision components:
The use of peelable solder mask is essential in the production process of some precision components. These components require protection from the heat and solder contamination generated during the soldering process during the production process. The use of peelable solder mask can provide these components with the necessary protection to ensure their performance and quality.
Consumer electronics:
In the production process of consumer electronics, the soldering quality of the circuit board is directly related to the performance and service life of the product. As an efficient, environmentally friendly and low-cost solder mask material, peelable solder mask is widely used in the production of circuit boards for consumer electronic products such as smartphones, laptops, and televisions to ensure the smooth progress of the soldering process.
Automotive electronics:
Automotive electronic products have very high requirements for the reliability and stability of circuit boards. In automotive electronic systems, circuit boards usually need to work in harsh environments such as high temperature, humidity and vibration. The use of peelable solder mask can help improve the soldering quality of circuit boards, ensure the stable operation of automotive electronic equipment, and avoid failures during the soldering process.
Implementation steps
While the advantages of strippable solder mask in circuit board manufacturing are obvious, its application process also requires meticulous operation to ensure the maximum protection and easy stripping characteristics. When using this material, PCB manufacturers need to follow a series of steps to ensure that it can be applied efficiently and safely.
Applying the mask:
Strippable solder mask is usually supplied in liquid form, similar to paint, and is applied to the surface of the circuit board by spraying, screen printing or brushing. The coating process requires special attention to the uniformity and thickness of the coating. Too thick or uneven coating may affect the subsequent stripping effect. Therefore, when applying, operators usually use professional equipment to ensure the consistency and quality of the coating.
Curing process:
The applied strippable solder mask needs to be cured, usually by heat curing. During the heating process, the chemical components of the mask react to form a solid film layer. Controlling the curing temperature and time is crucial, because too high or too low a temperature may affect the protective effect or stripping performance of the mask. The correct curing process ensures that the mask material can provide the best protection during the soldering process and can be easily removed after the soldering is completed.
Soldering process:
The soldering process is a key step in using peelable solder masks. During soldering, the mask protects the surface of the circuit board, preventing solder from entering areas where soldering is not required, preventing unnecessary short circuits and failures. In a high temperature environment, the mask can effectively resist the heat and gas generated during the soldering process. At this time, the mask not only protects the circuit board, but also provides a proper protective barrier for soldering.
Peeling off the mask:
After soldering, the most important step is to peel off the mask. The design purpose of the peelable solder mask is to ensure that it can be easily removed after soldering is completed. Usually, the operator can easily peel the mask off the surface of the circuit board using manual or mechanical methods, and the removed mask will not leave any residue or damage to the circuit board. This process is very simple, does not require complicated cleaning work, and can significantly improve production efficiency.
Quality control:
Quality control is crucial throughout the process. In particular, every link in the coating, curing and soldering process needs to be strictly monitored and inspected to ensure that the thickness, uniformity, curing effect and final peelability of the mask material meet the requirements. If there is a problem in any link, it may cause soldering quality problems or difficulty in peeling, thus affecting the production efficiency and quality of the entire circuit board. Therefore, it is crucial to implement appropriate quality control measures during the production process.
Through precise operation and management, manufacturers can give full play to the advantages of peelable solder mask, improve soldering quality, reduce unnecessary cleaning work during production, and improve overall production efficiency.
Future development trends and challenges
Although peelable solder mask has been widely used in current PCB manufacturing, with the continuous development of electronic products and circuit board design, the technology of this material may still face some new challenges and development directions in the future.
Higher performance mask materials:
With the improvement of functional requirements for circuit boards, especially in high-frequency and high-speed applications, the performance requirements for solder masks are also getting higher and higher. For example, with the popularization of 5G technology, many circuit boards will face higher temperature and frequency requirements.
In order to meet these requirements, future peelable solder mask materials may need to have stronger high temperature resistance, better mechanical strength and higher chemical stability. These improvements will ensure that the solder mask can still provide excellent protection in more complex production environments.
Environmental protection and sustainable development:
At present, environmental protection and sustainable development have become important issues worldwide. The electronics manufacturing industry, especially the PCB industry, is also facing increasing pressure in terms of material selection and environmental protection of the production process.
For strippable solder masks, more attention may be paid to the environmental friendliness of materials in the future. For example, developing non-toxic, low-volatile organic compound (VOC) mask materials to reduce waste and harmful gas emissions during the production process, thereby improving the green sustainability of the overall manufacturing process.
Automated and intelligent production:
With the rise of industrial automation and intelligent manufacturing, future PCB production may further rely on automated and intelligent equipment to reduce manual operations and improve production efficiency. Under this trend, the application of solder masks may also be more automated. For example, the mask can be applied by an automatic spraying robot, or the quality and uniformity of the solder mask can be detected by a machine vision system. The introduction of these technologies will make the application of strippable solder masks more efficient and accurate.
Multifunctionality:
Future strippable solder mask materials may not only be used for traditional solder protection, but may also have other functions, such as anti-static, anti-ultraviolet, and chemical corrosion resistance. As electronic products become more and more complex, the design and functional requirements of PCBs are becoming more and more diverse. In response to these changes, solder masks may develop in a multifunctional direction to meet the needs of different fields and applications.
Cost pressure and material optimization:
Although the advantages of peelable solder mask are obvious, its high cost is also a problem faced by some small PCB manufacturers. Therefore, more optimized materials may appear in the future to reduce costs. By improving the production process of materials and improving the efficiency of mask materials, manufacturers can reduce production costs while ensuring welding effects.
Summary
As an innovative solder mask material, Peelable solder mask plays an important role in the production of modern electronic circuit boards with its advantages of easy peeling, high temperature tolerance, good protection function, and environmental protection and low cost. From multi-layer circuit boards to high-frequency circuit boards, from consumer electronics to automotive electronics, peelable solder mask has been widely used in various fields.
With the continuous advancement of technology, the application scenarios of this material will continue to expand, bringing more innovative opportunities and solutions to the electronics manufacturing industry. For manufacturers, the use of peelable solder mask can not only improve production efficiency and product quality, but also reduce production costs, thereby enhancing the competitiveness of enterprises.
As the requirements for functions and performance of electronic products increase, peelable solder mask, as a flexible and efficient solder mask material, will continue to play a key role in the production of various high-precision circuit boards.