In the electronics manufacturing industry, fusible PCB, as a special type of printed circuit board, has gradually attracted market attention in recent years. As electronic products develop towards high integration, low power consumption, environmental protection and sustainability, fusible PCB is becoming a highlight in the industry due to its special process characteristics and application advantages.
This article will explore the definition, advantages, manufacturing process, application fields and future development trends of fusible PCB in depth, in order to provide valuable reference for relevant industry professionals.
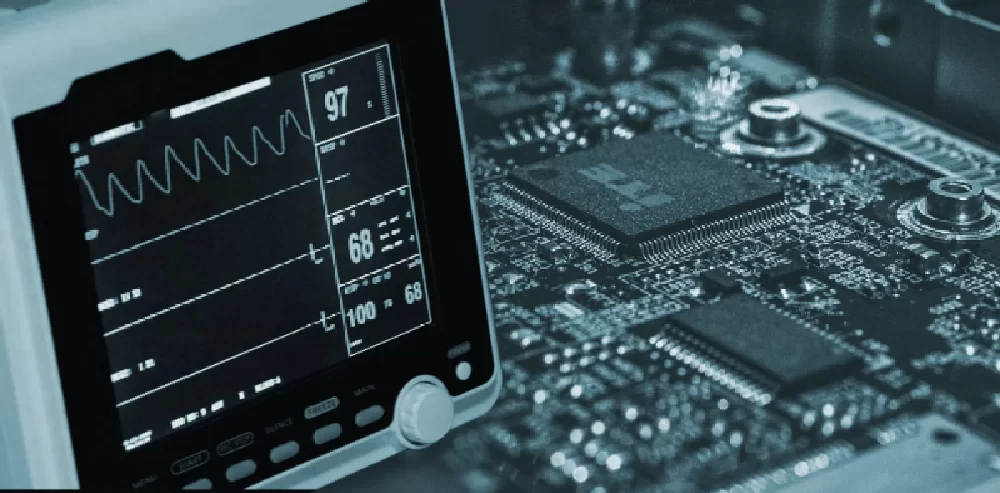
Fusible PCB is a printed circuit board with special melting point materials. Its core feature is that when a certain temperature is reached, some parts of the circuit board can melt or change shape. This feature makes fusible PCB unique in certain specific application scenarios.
Generally speaking, traditional PCBs mainly use epoxy resin glass fiber materials, while fusible PCBs may use special polymers, low melting point metal alloys or other special materials to achieve controllable melting characteristics.
In the process of electronic manufacturing and product design, the advantages of fusible PCB are mainly reflected in the following aspects.
First, it helps to improve the safety of the product. In some electronic devices that require overheating protection, fusible PCBs can automatically disconnect when the temperature is too high, thereby effectively preventing equipment damage or fire risks.
Secondly, fusible PCBs are conducive to the recyclability of electronic products. Since some fusible materials can decompose at lower temperatures, electronic products can be more easily disassembled and recycled after being discarded, which is in line with the trend of green environmental protection.
In addition, fusible PCBs can also be used in special intelligent control scenarios, such as programmable fuses, temperature sensing circuits, etc., to provide more advanced functions for electronic products.
As electronic products continue to play a role in complex environments, temperature control functions have become particularly important.
Although traditional PCBs can provide circuit connection and support functions, they often cannot effectively protect circuits and equipment when faced with excessive temperatures.At this time, the advantages of fusible PCBs are particularly significant. It can prevent more serious faults from occurring by melting or disconnecting the circuit through materials when the temperature is too high.
For example, in battery charging systems, fusible PCBs can provide thermal protection to prevent batteries from short-circuiting, expanding, or even catching fire due to excessive temperatures. As the safety requirements of consumer electronic products such as smartphones and electric vehicles continue to increase, the market demand for fusible PCBs is expected to continue to increase.
The manufacturing process of fusible PCBs is somewhat different from that of traditional PCBs.
First, in terms of material selection, it is necessary to consider how to achieve the fusible property, such as using low-melting-point alloys or reversibly degradable polymer materials. The low-melting-point metal materials used in fusible PCBs may include alloy materials such as lead, tin, and bismuth, while some special polymers may use materials with melting point variation characteristics, such as certain thermoplastic polymers.
Secondly, during the production process, the welding and assembly temperatures need to be strictly controlled to avoid the problem of premature melting of materials during the production process. To achieve this goal, each link in the process needs to be precisely controlled to ensure that the circuit board is not affected by excessive temperatures during the manufacturing process.
In addition, some fusible PCBs also need to be tested in specific environments to ensure that they can melt or fail as expected in actual use, thereby ensuring the reliability and safety of the product.
In production, fusible PCBs also require precise design of the structure and materials of the circuit board.
For example, in the wiring design of the PCB, the stability and melting temperature of the material at high temperatures need to be considered to ensure that the circuit can normally trigger the fuse function when overheating occurs.
In order to avoid mis-melting or incomplete melting under overheating conditions, engineers also need to perform thermal analysis and simulation to ensure that the circuit board performs as expected under specific working conditions.
The application areas of fusible PCBs are very wide. In the field of consumer electronics, some high-end smartphones, tablets, and wearable devices may use fusible PCBs to achieve temperature control protection to prevent battery overheating and safety accidents.
With the increasing demand for power consumption of smart devices, batteries have become a key factor limiting battery life and performance. Fusible PCBs can reduce battery overheating, increase battery life, and prevent battery safety hazards through effective thermal management.
In automotive electronics, with the development of intelligent driving and new energy technologies, on-board electronic devices require more advanced thermal management solutions, and fusible PCBs can provide protection in abnormal temperature environments to prevent key components from overheating and damage.
For example, the battery management system (BMS) and on-board charging module (OBC) in electric vehicles generate a lot of heat during operation. Fusible PCBs can effectively protect these components from failures caused by overheating, thereby ensuring the safety of the vehicle.
In the field of industrial control, some smart sensors and automation equipment may also use fusible PCBs to ensure adaptive protection under extreme conditions.
For example, for industrial equipment working in high temperature or high pressure environments, such as transformers, wind turbines, metallurgical furnaces, etc., fusible PCBs can provide the necessary temperature control function to ensure that the equipment can automatically disconnect the circuit in the event of overload or failure to prevent greater damage.
In industrial automation systems, the application of fusible PCBs can effectively improve the stability and safety of the system and reduce possible accidents in the production process.
In addition, in the field of medical equipment, some wearable medical products or implantable electronic devices may use the characteristics of fusible PCBs to enhance safety, such as automatically disconnecting the power in the event of overheating to prevent harm to the human body.
With people’s increasing attention to health and safety, fusible PCBs, as a high-safety material, may be used more in the medical field in the future.
In the future, as fusible PCB technology continues to mature, its application range may be further expanded.
For example, in the aerospace and military fields, fusible PCBs can be used in electronic equipment in extreme environments to provide additional safety. In devices such as space probes or high-altitude drones, electronic components may experience drastic temperature changes, and the self-protection characteristics of fusible PCBs can effectively reduce the risk of equipment damage.
In addition, in military equipment, some special-purpose electronic systems may need to self-destruct under certain conditions to prevent information leakage or equipment from falling into the hands of the enemy. Fusible PCBs may play a key role in such scenarios. Such applications place higher demands on materials and manufacturing processes, and will also promote the further development of fusible PCB technology.
At the same time, industry standards and regulations may also have an impact on the application of fusible PCBs. With increasingly stringent environmental regulations, the recyclability and environmental protection characteristics of electronic products have become important considerations.
If fusible PCBs can provide better solutions in environmentally friendly disassembly and material reuse, it will help companies meet green production requirements and reduce the cost of electronic waste treatment.
In addition, with the development of technology, industry associations and standard organizations may gradually establish quality inspection standards and certification systems for fusible PCBs to ensure their reliability in different application scenarios.
In the future, relevant companies need to pay close attention to changes in policies and regulations, and follow the latest industry standards in product design and manufacturing to ensure the wide application and market recognition of fusible PCB technology.
Although fusible PCBs have many advantages, they still face certain challenges in practical applications. For example, the material cost is high, especially when special polymers or low-melting-point metals are used, the manufacturing cost is higher than that of traditional PCBs. Although the high cost limits the popularity of fusible PCBs, with the advancement of technology and the increase in market demand, the cost may gradually decrease in the future.
In addition, the reliability of fusible PCBs needs to be strictly tested to ensure that they work within the appropriate temperature range without mismelting under unexpected circumstances. Therefore, it is necessary to strengthen the control of quality control during the production process to ensure the consistency and stability of the product.
The design and manufacture of fusible PCBs also face some other technical challenges. Due to their special melting characteristics, fusible PCBs may put forward higher requirements on the temperature, welding process, material adaptability, etc. during the production process. Engineers need to solve these problems through continuous technological innovation and experiments to ensure that fusible PCBs can play a role in different application scenarios.
With the advancement of technology and the growth of market demand, fusible PCBs are expected to be used in more fields. Especially in the context of increasingly stringent requirements for sustainable development and environmental protection, PCBs with strong recyclability and controllable melting will become a major trend in the electronics manufacturing industry.
With the development of intelligent manufacturing and artificial intelligence technology, fusible PCB may also be combined with new sensor technology to further expand its application in automation and intelligent electronic devices.
In general, as an emerging electronic manufacturing technology, fusible PCB has shown great potential in many fields. Although it still faces certain technical challenges and cost issues, with the advancement of materials science and the gradual acceptance of the market, fusible PCB will be expected to become a key element in the design of electronic products in the future, bringing more innovative applications to the industry.
In this process, relevant enterprises and scientific research institutions should strengthen technical research and development and cooperation, promote the continuous advancement of fusible PCB technology, and further promote its application in the electronic manufacturing industry.