The process of PCB (Printed Circuit Board) assembly involves numerous intricate steps, each critical to ensuring the final product’s functionality and reliability. Among these steps, the significance of BGA coplanarity stands out, particularly in modern electronic devices where miniaturization and performance are paramount. This article delves into the intricacies of BGA (Ball Grid Array) coplanarity, exploring its impact on PCB assembly, the challenges it presents, and the methods employed to ensure optimal coplanarity.
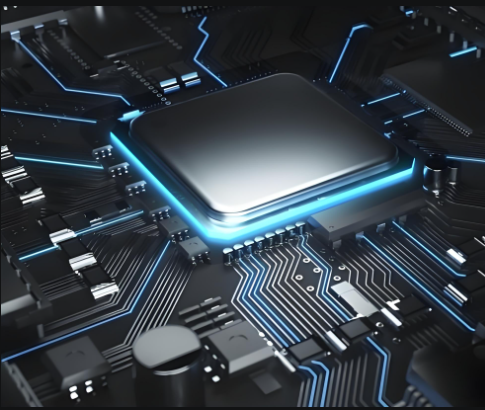
Understanding BGA and Its Importance
Ball Grid Array (BGA) is a type of surface-mount packaging used for integrated circuits. BGA packages are favored for their ability to provide a higher density of connections and improved electrical and thermal performance compared to traditional packages. The use of BGA packages has become ubiquitous in high-performance electronics, including computers, smartphones, and networking equipment.
The reliability of BGA packages in providing consistent and dependable connections is crucial. This is where the concept of BGA coplanarity comes into play. Coplanarity refers to the degree to which the tops of all the solder balls on a BGA package are aligned within a single plane. In simpler terms, it is a measure of the flatness of the solder balls.
The Impact of Coplanarity on PCB Assembly
The coplanarity of BGA packages directly affects the quality of solder joints formed during the reflow soldering process. When a BGA package is placed on a PCB, the solder balls need to make uniform contact with their corresponding pads on the PCB. If the solder balls are not coplanar, some balls may not adequately contact the pads, leading to poor solder joints or even open circuits.
Poor coplanarity can result in several issues:
- Insufficient Solder Joints: If some solder balls do not make proper contact with the PCB pads due to uneven heights, the resulting solder joints may be weak or incomplete. This can cause intermittent connections or complete failure of the joint.
- Excessive Stress: Non-coplanar solder balls can introduce mechanical stress during thermal cycling and mechanical vibrations. This stress can lead to solder joint fatigue and eventual failure.
- Rework and Repairs: Addressing issues caused by poor coplanarity often requires rework or repairs, which can be time-consuming and costly. Rework can also introduce additional risks, such as damage to the PCB or the BGA package.
In addition to these immediate impacts, poor coplanarity can lead to long-term reliability issues. Devices with compromised solder joints are more likely to fail under operational stresses, including thermal cycling, vibration, and mechanical shock. This is especially critical in industries where reliability is paramount, such as aerospace, automotive, and medical devices.
Factors Affecting BGA Coplanarity
Several factors contribute to the coplanarity of BGA packages. Understanding these factors is essential for both manufacturers and assembly houses to ensure high-quality solder joints.
- Manufacturing Tolerances: The precision with which BGA packages are manufactured plays a significant role in coplanarity. Variations in the height of solder balls during the manufacturing process can lead to deviations in coplanarity. High-quality manufacturing processes and stringent quality control measures are essential to minimize these variations.
- Material Properties: The materials used in BGA packages, including the substrate and solder balls, can influence coplanarity. Differences in the thermal expansion coefficients of these materials can cause warping or deformation during temperature changes, affecting coplanarity.
- Handling and Storage: Improper handling and storage of BGA packages can lead to physical damage, such as bending or warping, which can affect coplanarity. Proper packaging and handling procedures are critical to maintaining the integrity of BGA packages.
- PCB Design: The design of the PCB itself can impact coplanarity. Factors such as pad size, pad spacing, and solder mask design can influence how well the solder balls align with the PCB pads during assembly.
- Environmental Conditions: Humidity and temperature variations during storage and transport can affect the materials in BGA packages, potentially leading to changes in coplanarity. Control of storage conditions is crucial to maintaining package integrity.
- Assembly Processes: The processes used during PCB assembly, including solder paste application, placement, and reflow soldering, can all impact coplanarity. Variations in these processes need to be tightly controlled to ensure uniform results.
Measuring and Ensuring Coplanarity
Ensuring optimal BGA coplanarity requires precise measurement techniques and quality control processes. Several methods are commonly used to measure and ensure coplanarity:
- Automated Optical Inspection (AOI): AOI systems use high-resolution cameras and advanced image processing algorithms to inspect the coplanarity of BGA packages. These systems can quickly identify deviations in solder ball heights and provide detailed data for analysis.
- X-ray Inspection: X-ray inspection is another valuable tool for measuring coplanarity. X-ray systems can provide a three-dimensional view of the solder balls and their alignment with the PCB pads. This method is particularly useful for detecting hidden defects that may not be visible through optical inspection.
- Mechanical Measurement: Mechanical measurement techniques, such as using micrometers or height gauges, can provide accurate measurements of solder ball heights. However, these methods are typically more time-consuming and may not be suitable for high-volume production.
- Coplanarity Testing during Manufacturing: Implementing coplanarity testing as part of the manufacturing process is crucial. Manufacturers can use automated testing equipment to measure coplanarity at various stages of production, ensuring that deviations are detected and corrected early.
In addition to these measurement techniques, real-time monitoring during the reflow process can help identify and address issues as they arise. Advanced reflow ovens equipped with monitoring systems can adjust parameters on the fly to ensure uniform heating and cooling, further improving coplanarity outcomes.
Mitigating Coplanarity Issues
To mitigate coplanarity issues, manufacturers and assembly houses can implement several best practices:
- Strict Quality Control: Implementing stringent quality control measures throughout the manufacturing process can help minimize variations in coplanarity. Regular inspections and testing should be conducted to ensure compliance with specifications.
- Optimized PCB Design: Designing PCBs with proper pad sizes, spacing, and solder mask openings can improve the alignment of solder balls with PCB pads. Collaboration between PCB designers and assembly engineers is essential to achieve optimal coplanarity.
- Controlled Reflow Soldering Process: The reflow soldering process should be carefully controlled to minimize thermal stresses and ensure uniform soldering. Proper temperature profiles and reflow oven settings are critical to achieving consistent coplanarity.
- Use of Advanced Materials: Selecting materials with compatible thermal expansion properties can reduce the risk of warping and deformation. High-quality substrates and solder balls can contribute to better coplanarity.
- Training and Education: Ensuring that all personnel involved in the manufacturing and assembly processes are well-trained and aware of the importance of coplanarity can help maintain high standards. Continuous education on best practices and new technologies is essential.
Case Studies and Real-World Applications
Examining real-world applications and case studies can provide valuable insights into the importance of coplanarity and the measures taken to ensure it.
- Consumer Electronics: In consumer electronics, such as smartphones and tablets, BGA packages are used extensively. Ensuring coplanarity is critical to maintaining the reliability of these devices, especially given their frequent use and exposure to varying environmental conditions. Manufacturers invest heavily in quality control and inspection techniques to ensure optimal coplanarity.
- Automotive Electronics: Automotive electronics require high levels of reliability and durability. BGA packages in automotive applications must withstand extreme temperatures, vibrations, and mechanical stresses. Ensuring coplanarity is essential to prevent solder joint failures and ensure the long-term performance of these critical systems.
- Medical Devices: Medical devices, such as diagnostic equipment and implantable devices, rely on BGA packages for their compact size and high performance. Coplanarity is crucial to ensure the accuracy and reliability of these devices, which directly impact patient safety and health.
- Aerospace Applications: In aerospace applications, the reliability of electronic components is of utmost importance. BGA packages used in satellites, aircraft, and other aerospace systems must endure extreme conditions, including temperature fluctuations and mechanical shocks. Ensuring coplanarity in these components is vital to prevent failures that could lead to catastrophic consequences.
Future Trends and Technological Advancements
The field of BGA coplanarity is continuously evolving, driven by advancements in technology and increasing demands for higher performance and reliability. Several trends and innovations are shaping the future of coplanarity in PCB assembly:
- Advanced Inspection Technologies: Innovations in inspection technologies, such as machine learning and artificial intelligence, are enhancing the accuracy and speed of coplanarity measurements. These technologies can analyze large volumes of data and identify patterns that may indicate potential issues, allowing for proactive quality control.
- Miniaturization and High-Density Packaging: As electronic devices continue to shrink in size, the demand for high-density packaging solutions, including BGAs, is increasing. Ensuring coplanarity in these miniaturized packages presents new challenges that require innovative manufacturing and inspection techniques.
- Flexible and Rigid-Flex PCBs: The use of flexible and rigid-flex PCBs is becoming more prevalent in various industries. Ensuring coplanarity in these complex and often non-planar structures requires advanced materials and precise manufacturing processes.
- Sustainable Manufacturing Practices: The electronics industry is increasingly focusing on sustainability and environmentally friendly manufacturing practices. Ensuring coplanarity while minimizing waste and energy consumption is a growing area of research and development.
- Material Science Innovations: Advances in material science are leading to the development of new materials with improved thermal and mechanical properties. These materials can help reduce coplanarity issues by providing more stable and uniform solder balls.
Conclusion
In the ever-evolving landscape of electronic manufacturing, the importance of BGA coplanarity cannot be overstated. Ensuring that BGA packages have optimal coplanarity is crucial to achieving reliable and high-performance solder joints in PCB assembly. By understanding the factors that affect coplanarity, implementing rigorous quality control measures, and embracing technological advancements, manufacturers can overcome the challenges associated with coplanarity and deliver products that meet the highest standards of reliability and performance.
As the industry continues to advance, the pursuit of perfect coplanarity will remain a key focus, driving innovation and excellence in electronic manufacturing. Through collaboration, continuous improvement, and a commitment to quality, the goal of achieving flawless coplanarity in BGA packages is not only attainable but essential for the future of electronic devices. Ensuring that the next generation of technology performs reliably under various conditions will depend heavily on our ability to control and improve BGA coplanarity, making it a cornerstone of modern PCB assembly practices.