Introduction
Carbon fiber and FR4 plates are two crucial materials extensively used in various industries such as aerospace, automotive, and electronics. Each material possesses distinct properties, making them suitable for specific applications. This article delves into the characteristics, manufacturing processes, applications, performance comparison, cost analysis, environmental impact, and future trends of carbon fiber and FR4 plates, providing a comprehensive understanding to aid in the selection of the appropriate material for specific needs.
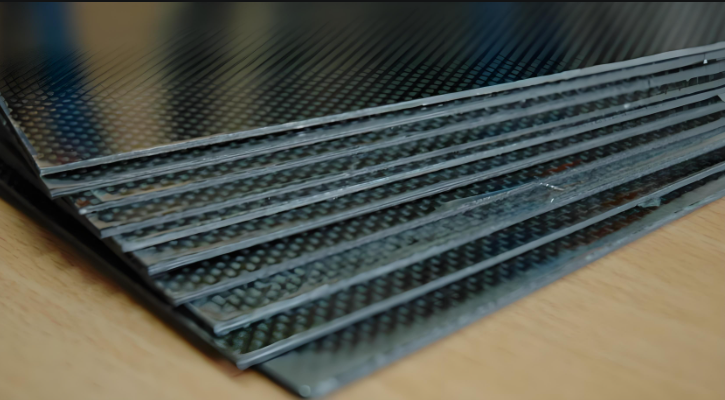
Material Characteristics
Carbon Fiber
Strength and Stiffness
Carbon fiber is renowned for its exceptional strength and stiffness. It has a tensile strength that is several times that of steel, while being significantly lighter. The high stiffness of carbon fiber makes it an ideal material for applications requiring minimal deformation under stress.
Weight
One of the most notable advantages of carbon fiber is its low weight. With a density of approximately 1.6 g/cm³, it is lighter than aluminum. This weight advantage is crucial in industries where reducing mass can lead to enhanced performance and efficiency, such as aerospace and automotive sectors.
Conductivity
Carbon fiber exhibits good electrical conductivity, which can be both an advantage and a disadvantage depending on the application. Its thermal conductivity is also beneficial in applications requiring heat dissipation.
FR4
Electrical Properties
FR4 is primarily used in electronic applications due to its excellent electrical insulating properties. It is a composite material made of woven fiberglass cloth with an epoxy resin binder that is flame resistant.
Mechanical Properties
FR4 is valued for its high mechanical strength and rigidity. It can withstand considerable stress without deforming, making it suitable for structural applications in electronic devices.
Thermal Properties
FR4 has a relatively low coefficient of thermal expansion, which allows it to maintain dimensional stability over a wide temperature range. This property is vital for ensuring the reliability of electronic circuits under varying thermal conditions.
Manufacturing Process
Carbon Fiber
Raw Materials
The primary raw material for carbon fiber is polyacrylonitrile (PAN), though pitch and rayon can also be used. The choice of precursor affects the properties of the resulting carbon fiber.
Weaving and Forming
Carbon fibers are spun into yarns and then woven into fabrics. These fabrics can be molded into various shapes and sizes to suit specific applications. The weaving process can be customized to produce different patterns, which influence the final mechanical properties.
Resin Impregnation and Curing
The woven carbon fiber fabrics are impregnated with resin, typically epoxy, and then cured at high temperatures. This process hardens the resin and bonds it with the carbon fibers, resulting in a rigid and durable composite material.
FR4
Fiberglass Fabrication
The base material for FR4 is a fiberglass fabric. The glass fibers are woven into a cloth, which provides the structural strength of the final product.
Resin Impregnation
The fiberglass cloth is impregnated with an epoxy resin, which is flame retardant. This resin provides the necessary electrical insulating properties.
Laminating and Curing
The impregnated fiberglass sheets are stacked and subjected to heat and pressure to laminate them together. This process cures the resin and solidifies the composite into a rigid plate.
Applications
Carbon Fiber
Aerospace
Carbon fiber is extensively used in the aerospace industry due to its high strength-to-weight ratio. Components such as fuselages, wings, and control surfaces in aircraft like the Boeing 787 Dreamliner are made from carbon fiber composites, reducing weight and improving fuel efficiency.
Automotive
In the automotive sector, carbon fiber is used to manufacture lightweight body panels and structural components. High-performance cars such as the BMW i8 and McLaren P1 utilize carbon fiber to enhance performance and fuel economy.
Sporting Goods
Carbon fiber is popular in the sporting goods industry for equipment like bicycle frames, tennis rackets, and golf clubs. Its lightweight and strong properties improve the performance and durability of these products.
FR4
Printed Circuit Boards (PCBs)
FR4 is the material of choice for manufacturing PCBs due to its excellent electrical insulation and mechanical strength. It is used in virtually all electronic devices, from smartphones to industrial machinery.
Consumer Electronics
FR4 is widely used in consumer electronics, including computers, televisions, and home appliances. It provides a stable and reliable platform for mounting electronic components.
Industrial Control Equipment
In industrial automation and control systems, FR4 boards are used for their reliability and durability. They ensure that electronic circuits perform consistently under harsh environmental conditions.
Performance Comparison
Strength and Stiffness
Carbon fiber outperforms FR4 in terms of strength and stiffness. Its superior tensile strength and rigidity make it suitable for high-stress applications where minimal deformation is critical. In contrast, while FR4 is mechanically strong, it cannot match the tensile strength of carbon fiber.
Weight
Carbon fiber’s low density gives it a significant advantage over FR4 in applications where weight reduction is crucial. This property makes carbon fiber the preferred choice for aerospace and automotive industries, where minimizing weight can lead to enhanced performance and efficiency.
Thermal Performance
Carbon fiber has better thermal conductivity and stability compared to FR4. It can dissipate heat more effectively and maintain its properties at higher temperatures. FR4, while having a low coefficient of thermal expansion, does not conduct heat as efficiently, making it less suitable for applications requiring high thermal performance.
Electrical Performance
FR4 excels in electrical insulation, making it ideal for electronic applications. Its non-conductive nature ensures the safe operation of electronic circuits. On the other hand, carbon fiber’s conductivity can lead to electromagnetic interference (EMI) issues, which must be managed carefully in electronic applications.
Cost and Economic Considerations
Carbon Fiber Cost Analysis
The production of carbon fiber is an expensive process, involving high costs for raw materials and complex manufacturing techniques. This results in a high price for carbon fiber products, limiting their use to high-end applications where performance benefits justify the cost.
FR4 Cost Analysis
FR4 is relatively inexpensive to produce, making it suitable for mass production. Its cost-effectiveness and suitability for a wide range of electronic applications contribute to its widespread use in the electronics industry.
Value for Money Comparison
While carbon fiber offers superior performance characteristics, its high cost restricts its use to applications where these benefits are essential. FR4, on the other hand, provides a good balance of performance and cost, making it the preferred material for many electronic applications where cost-effectiveness is a priority.
Environmental Impact and Sustainability
Carbon Fiber
The production of carbon fiber has a considerable environmental impact due to the energy-intensive processes involved. However, efforts are being made to develop more sustainable manufacturing methods and improve recycling technologies. The potential for recycling carbon fiber is growing, though it remains a challenge compared to more traditional materials.
FR4
The manufacturing of FR4 involves the use of chemicals and processes that can be harmful to the environment. Additionally, the disposal of electronic waste containing FR4 poses significant environmental challenges. Recycling FR4 board is complex, requiring advanced techniques to separate the fiberglass and resin components.
Future Trends
Carbon Fiber
As technology advances, the cost of carbon fiber production is expected to decrease, making it more accessible for a broader range of applications. Innovations in manufacturing techniques and material science are likely to enhance the properties of carbon fiber, further expanding its use in various industries.
FR4
The development of new resin formulations and advanced manufacturing processes is expected to improve the performance of FR4 materials. There is also ongoing research into more environmentally friendly alternatives to traditional FR4, which could lead to more sustainable electronic products in the future.
Conclusion
Carbon fiber and FR4 plates each have their unique advantages and applications. Carbon fiber, with its exceptional strength, stiffness, and lightweight properties, is ideal for high-performance applications in aerospace, automotive, and sporting goods. However, its high cost limits its use to these specialized fields. FR4, on the other hand, offers excellent electrical insulation, mechanical strength, and cost-effectiveness, making it the material of choice for electronic applications.
When selecting between carbon fiber and FR4, it is essential to consider the specific requirements of the application, including performance, cost, and environmental impact. Both materials play crucial roles in modern technology and industry, and ongoing advancements will continue to enhance their capabilities and applications.
In conclusion, understanding the distinct characteristics and applications of carbon fiber vs FR4 plates allows for informed decision-making in material selection, ensuring optimal performance and efficiency in various industrial and technological applications.