PCB, the Chinese name for the printed circuit board, also known as printed circuit boards, is an important electronic component, is the support body of electronic components, is the carrier of the electrical connection of electronic components. Because it is made using electronic printing technology, it is called printed circuit board.
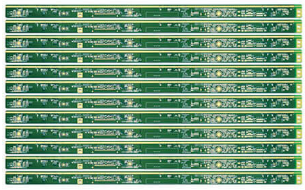
Source PCBs, the interconnection of electronic components was accomplished by the direct connection of wires. Today, wires are only used in laboratories for experimental applications and exist; printed circuit boards have definitely taken absolute control in the electronics industry.
PCB production process
1.Contact the manufacturer
First of all, you need to contact the manufacturer, and then register the customer number, there will be someone for you to quote, order, and follow up the production progress.
2.Open material
Purpose: According to the requirements of the engineering data MI, in line with the requirements of the large sheet, cut into small pieces of production boards. Meet the customer’s requirements of small pieces of sheet material.
Process: large sheet material → according to the requirements of MI cut board → curium board → beer rounded edges → out of the plate
3.Drilling
Purpose: According to engineering data, in the opening to meet the requirements of the size of the sheet, the corresponding position of the hole drilling the required diameter.
Process: stacked board pins → on the board → drilling → under the board → inspection and repair
4.Copper sinking
Purpose: copper sinking is the use of chemical methods in the insulation hole wall deposited on a thin layer of copper.
Process: rough grinding → hanging board → copper sinking automatic line → under the board → dip % dilute H2SO4 → thickened copper
5.Graphic transfer
Purpose: graphics transfer is the production of film on the image transferred to the board
Process: (blue oil process): grinding board → printing the first side → drying → printing the second side → drying → burst → developing → check; (dry film process): hemp board → pressure film → static → alignment → exposure → static → developing → check
6.Graphic plating
Purpose: graphic plating is in the line graphic exposed copper skin or hole wall plating a layer of copper layer to achieve the required thickness and the required thickness of gold and nickel or tin layer.
Process: on the board → degreasing → wash the second → micro-etching → wash → pickling → copper plating → wash → acid dip → tin plating → wash → off the board
7.Desmear
Purpose: to use NaOH solution to remove the anti-plating cover film layer so that the non-line copper layer exposed.
Process: water film: inserted frame → dip alkali → rinse → scrub → over the machine; dry film: put the board → over the machine
8.Etching
Purpose: etching is the use of chemical reaction method will be non-line parts of the copper layer corrosion.
9.Green oil
Purpose: green oil is the green oil film graphics transferred to the board, play a role in protecting the line and prevent the role of welding parts on the line tin
Process: grinding board → printing sensitized green oil → curium board → exposure → punch shadow; grinding board → printing the first side → baking board → printing the second side → baking board
10.Character
Purpose: characters are provided to facilitate the identification of a mark
Process: green oil after the final curium → cooling and resting → adjust the network → print characters → post-curium
11.Plated fingers
Purpose: in the plug finger plated with a layer of nickel and gold layer of the required thickness, so that it has more hardness of wear resistance
Process: on the board → degreasing → wash twice → micro-etching → wash twice → pickling → copper plating → wash → nickel plating → wash → gold plating
12.Tin-plated plate (a parallel process)
Purpose: tin spray is not covered with solder resist on the exposed copper surface sprayed with a layer of lead and tin to protect the copper surface from corrosion and oxidation, in order to ensure that a good welding performance.
Process: micro-etching → air-drying → preheating → rosin coating → solder coating → hot air leveling → air-cooled → washing air-drying
13.Molding
Purpose: through the mold stamping or CNC gong machine gong out the shape of the customer’s needs molding methods organic gong, beer plate, hand gong, hand-cutting
Explanation: The accuracy of data gong machine board and beer board is higher, followed by hand gong, and the lowest hand-cut board can only do some simple shapes.
14.Test
Purpose: through the electronic 100% test, detection of visual not easy to find to the open circuit, short circuit and other impact on the functionality of the defects.
Process: mold → release → test → qualified → FQC visual inspection → unqualified → repair → back to the test → OK → REJ → scrapped!
15.Final Inspection
Purpose: through 100% visual inspection of the board appearance defects, and minor defects to repair, to avoid problems and defects board out.
Specific workflow: incoming material → view information → visual inspection → qualified → FQA spot check → qualified → packaging → unqualified → processing → check OK!
The above is my sharing today about source pcb, thank you.