Metal Core PCB is a special type of printed circuit board, whose substrate material is metal instead of common glass fiber reinforced plastic. Metal Core PCBs are usually made of aluminum, copper or magnesium alloy, among which aluminum and copper are the most commonly used materials.
Metal Core PCBs have been increasingly used in hybrid integrated circuits, automobiles, motorcycles, office automation, high-power electrical equipment, power supply equipment and other fields due to their excellent heat dissipation performance, machining performance, electromagnetic shielding performance, dimensional stability performance, magnetic performance and multi-functional performance, especially as the base substrate in LED packaging products.
Three common structures of Metal Core PCB:
namely Metal Core PCB, clad type, Metal Core PCB and metal core substrate, among which Metal Core PCB is the most common and most used one.
The Metal Core PCB is based on a metal plate (aluminum, copper, iron, molybdenum, etc.), and its substrate is covered with an insulating dielectric layer and a conductive layer (copper foil). The clad Metal Core PCB is a base with a layer of glaze coated on the six sides of the metal plate, which is sintered to form an integrated base, on which the conductor circuit pattern is made by wire mesh leakage, sintering and making. Metal Core PCBs are generally made of copper and aluminum as core materials, with an organic polymer insulating dielectric layer coated on the surface, or compounded on a semi-cured sheet or PET film, and covered with a conductor foil (some use the addition method to directly form a conductive pattern).
According to the composition, it can be divided into:
Metal aluminum substrate, metal iron substrate, metal copper substrate, metal molybdenum substrate, metal aluminum alloy substrate, etc.
Aluminum substrates have the advantages of high heat dissipation, high mechanical strength and good processability. However, the PCB made of it generates noise when working in the parts where switching components, power supplies and amplifier components are installed. Compared with other Metal Core PCBs, aluminum substrates have a larger relative linear expansion coefficient. In order to solve the above problems, achieve high-density wiring of PCBs and reduce and eliminate noise, aluminum substrates with two-layer structures have appeared in recent years.
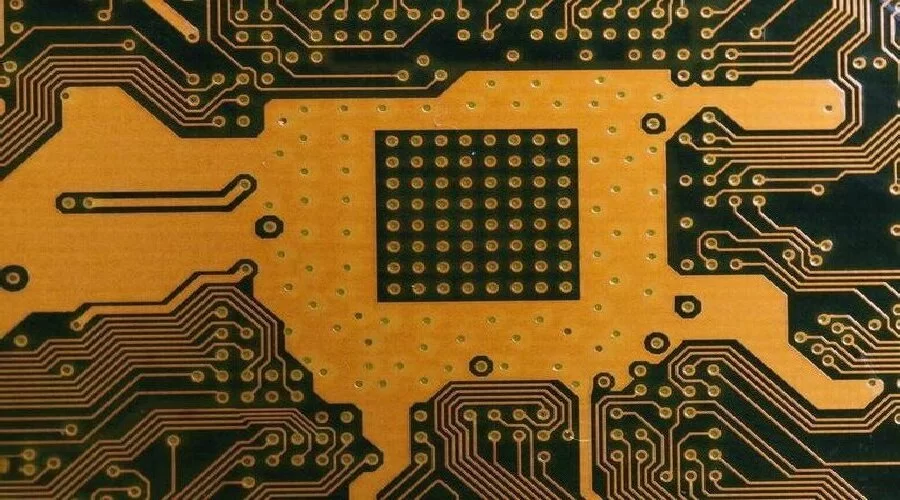
Aluminum PCB
Iron substrates have electromagnetic properties that other Metal Core PCBs do not have, and have the advantages of good dimensional stability and low price. It also has the problems of weight, corrosion resistance, and poor thermal conductivity than aluminum and copper substrates. Iron substrates are mainly divided into three categories: ① Stainless steel substrates. Its insulating layer is thick-film glass fired at high temperature. The conductor layer is made by printing the conductor material (Ad-Pd) and then firing. The mechanical strength of the board is higher than that of the ceramic substrate. However, the thermal shock and mechanical shock resistance are poor. ② Iron substrate, iron plate is used as the substrate. In order to prevent iron from rusting, there are two types of plates that are aluminum-plated and galvanized. Their insulation layer is composed of epoxy resin, epoxy glass cloth, etc. The thickness of the insulation layer is 40-150um. ③ The surface of the low-carbon steel plate as the core is a coated Metal Core PCB with no glaze.
The copper substrate has the advantages of high heat dissipation and good grounding connection as the bottom substrate. However, it has the disadvantages of heavy weight and difficulty in end surface anti-oxidation treatment.
According to the performance of the Metal Core PCB, it can be divided into:
The resin insulation layer of various Metal Core PCBs is composed of different resins. For example: there are cyclic resin, polyolefin resin, polyimide resin (PI), polyphenylene ether resin (PPE), etc. The Metal Core PCBs they constitute have considerable differences in many properties, especially in heat dissipation, insulation, heat resistance, etc.
① General-purpose metal-based copper-clad laminate
② Flame-retardant metal-based copper-clad laminate:
③ High-heat-resistant metal-based copper-clad laminate
④ High-thermal-conductivity metal-based copper-clad laminate:
⑤ Ultra-high-thermal-conductivity metal-based copper-clad laminate:
⑥ High-frequency, microwave-type metal-based copper-clad laminate:
⑦ Multi-layer metal-based copper-clad laminate, etc.
Classified by different resin insulation of Metal Core PCBs:
① General-purpose aluminum-based copper-clad laminate. Its insulation layer is composed of epoxy glass cloth adhesive sheet;
② High-heat dissipation aluminum-based copper-clad laminate. Its insulation layer is composed of high-thermal-conductivity epoxy resin or other high-thermal-conductivity resin;
③ Aluminum-based copper-clad laminate for high-frequency circuits. Its insulation layer is composed of polyolefin resin or polyimide resin-glass cloth adhesive sheet.
The biggest difference between aluminum-based copper-clad laminates and conventional FR-4 copper-clad laminates is heat dissipation. The thermal resistance of a 1.5mm thick conventional FR-4 copper clad laminate is compared with the thermal resistance of three 1.5mm thick aluminum-based copper clad laminates. The heat dissipation of the aluminum-based copper clad laminate is more than 20 times that of the ordinary FR-4 copper clad laminate.
The advantages of Metal Core PCBs include:
Excellent heat dissipation performance: Metal Core PCBs have good thermal conductivity and can effectively conduct the heat generated on the circuit board to the surrounding environment, thereby reducing the operating temperature of circuit components and improving the stability and reliability of the system.
High structural stability: Metal Core PCBs have high mechanical strength and rigidity, are not easy to deform or break, and have good tolerance in harsh environments.
Excellent electrical properties: The metal layer of the Metal Core PCB provides excellent electrical conductivity, which helps to reduce resistance and transmit signals.
Excellent high-frequency performance: The low dielectric constant and low loss tangent of the Metal Core PCB enable it to have excellent performance in high-frequency circuits and radio frequency applications.
Good high temperature resistance: Metal Core PCBs can withstand high operating temperatures and are suitable for some application scenarios in high temperature environments.
The above is my basic understanding and sharing of metals. In general, Metal Core PCBs are widely used in LED lighting, automotive electronics, communication equipment and other fields due to their excellent heat dissipation, structural stability and electrical properties.