Printed Circuit Boards (PCBs) are foundational components in modern electronics, enabling the connection and functionality of various components within a device. The manufacturing and assembly processes of PCBs require precision and accuracy to ensure that the final product operates correctly. One critical accessory in this process is the pcb board clamp. This article will explore the functionality, types, and applications of PCB board clamps, providing a detailed overview of their role in the PCB industry.
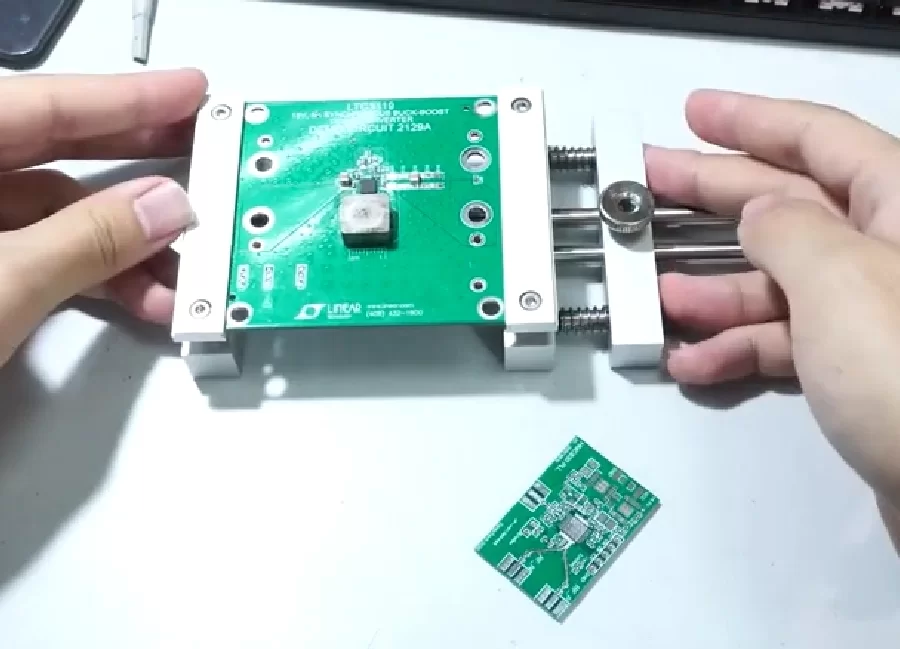
Functionality of PCB Board Clamps
The primary function of a pcb board clamp is to securely hold the PCB in place during different stages of the manufacturing and assembly processes. These stages include drilling, routing, soldering, and inspection. The clamp’s role is to ensure that the PCB remains stationary, enabling precise and consistent processing. Without a secure hold, there is a risk of misalignment, leading to defects and reduced functionality in the final product.
A PCB board clamp is designed to apply uniform pressure across the PCB’s surface, preventing any movement that could result in misaligned components or faulty connections. This is particularly important during the soldering process, where even slight shifts can cause short circuits or incomplete connections. By keeping the board firmly in place, PCB board clamps help maintain circuit integrity and ensure that all components are correctly positioned, which is essential for the device’s overall performance.
Types of PCB Board Clamps
PCB board clamps come in various types, each designed to meet specific needs in the PCB manufacturing and assembly process. Understanding these different types is crucial for selecting the right clamp for a particular application.
Mechanical Clamps
Mechanical clamps are the most common type of pcb board clamp. They use physical force, usually applied through screws, levers, or other mechanical means, to hold the PCB securely. These clamps are often adjustable, allowing them to be used with boards of different sizes and thicknesses. Mechanical clamps are known for their durability and reliability, making them a popular choice in many PCB manufacturing environments.
There are several subtypes of mechanical clamps, each offering unique benefits:
- Spring Clamps: These clamps use a spring mechanism to apply consistent pressure on the PCB. Spring clamps are easy to operate and provide a secure hold, making them suitable for various stages of PCB production. They are particularly useful in environments where the board needs to be clamped and unclamped frequently.
- Toggle Clamps: Toggle clamps feature a lever that locks into place, providing a strong hold with minimal effort. These clamps are especially useful in situations where quick and repeated clamping is necessary. Toggle clamps are often used in assembly lines, where speed and efficiency are critical.
- Screw Clamps: Screw clamps use screws to apply pressure on the PCB. While they require more time to adjust and secure, they offer precise control over the pressure applied, making them ideal for delicate or complex boards. These clamps are often used in processes that demand high precision and stability.
Vacuum Clamps
Vacuum clamps utilize suction to hold the PCB in place. They are particularly beneficial for handling delicate boards or boards with complex geometries, as they distribute pressure evenly across the entire surface. Vacuum clamps are often used in automated PCB assembly lines, where precision and repeatability are crucial. These clamps can accommodate boards with varying shapes and sizes without needing manual adjustments, making them versatile and efficient for large-scale production.
Vacuum clamps are especially useful in scenarios where traditional mechanical clamps may not provide sufficient coverage or pressure distribution. By creating a vacuum seal, these clamps ensure that the PCB is held securely without the risk of damaging sensitive components. This makes them an ideal choice for high-density PCBs and boards with intricate designs.
Magnetic Clamps
Magnetic clamps use magnets to secure the PCB. These clamps are easy to use and provide a strong hold, especially with metal-backed PCBs. However, they are not suitable for all types of boards, particularly those sensitive to magnetic interference. Magnetic clamps are often used in specialized applications where other types of clamps may not provide the necessary hold.
While magnetic clamps offer a convenient and quick solution for holding PCBs, they are generally limited to specific applications. The strength of the magnetic hold can vary depending on the board’s material and thickness, so they are typically used in situations where other clamping methods may be less effective. Magnetic clamps are also beneficial in environments where quick setup and teardown are required, as they can be easily attached and removed without tools.
Applications of PCB Board Clamps
PCB board clamps play a vital role in various stages of PCB manufacturing and assembly. Below are some of the key applications where these clamps are indispensable.
Drilling and Routing
During the drilling and routing stages of PCB production, the board must be held securely to ensure precise cuts and holes. A pcb board clamp provides the necessary stability to prevent any movement that could lead to inaccuracies. This is especially important when dealing with high-density boards, where even a slight misalignment can result in significant defects.
Clamps used during drilling and routing must withstand the mechanical forces involved in these processes. They need to be robust enough to hold the board in place without causing any damage to the PCB itself. Mechanical clamps, particularly screw and toggle clamps, are commonly used in these stages due to their strong hold and adjustability.
The importance of precision during drilling and routing cannot be overstated. Any deviation from the intended path can compromise the PCB’s functionality, leading to costly rework or even complete board failure. PCB board clamps ensure that the board remains fixed in the correct position, allowing the drilling and routing equipment to perform accurately and consistently.
Soldering
Soldering is a critical stage in PCB assembly, where components are attached to the board. During soldering, it is essential to ensure that the board remains perfectly still to prevent any misalignment of components. A pcb board clamp is used to hold the board securely while solder is applied to the connections.
Spring clamps are often favored in soldering applications due to their ease of use and the consistent pressure they apply. Vacuum clamps may also be used, particularly in automated soldering processes where precision is paramount. By keeping the board stable, these clamps help ensure strong, reliable connections between components and the PCB.
In addition to maintaining stability, the clamp’s material and design are crucial to avoid heat transfer during soldering. Materials that conduct heat can potentially damage the PCB or create uneven solder joints. Therefore, clamps made from heat-resistant materials are often used in soldering applications to prevent such issues.
Inspection and Testing
After assembly, PCBs undergo rigorous inspection and testing to ensure they meet quality standards. During these processes, the board must be held in place to allow for accurate testing of electrical connections and functionality. A pcb board clamp provides the necessary stability, enabling technicians and automated systems to conduct thorough inspections without the risk of damaging the board.
In inspection and testing applications, the choice of clamp depends on the specific requirements of the process. Mechanical clamps are often used for manual inspections, while vacuum clamps may be employed in automated testing setups. The clamp must provide a secure hold while allowing easy access to the board for probes and testing equipment.
The inspection and testing phase is critical for identifying defects or issues before the PCB moves to final assembly. Any movement during testing can lead to false readings or missed defects, so the clamp’s ability to hold the board firmly is essential. Moreover, in automated testing environments, the clamp must be compatible with the testing equipment to ensure seamless integration and operation.
Choosing the Right PCB Board Clamp
Selecting the right pcb board clamp for a given application requires careful consideration of several factors. These include the size and thickness of the PCB, the specific stage of production, and the level of precision required. Below are some key considerations to keep in mind when choosing a PCB board clamp.
Board Size and Thickness
The size and thickness of the PCB are crucial factors in selecting the appropriate clamp. Larger and thicker boards require clamps that can provide a strong, even hold across the entire surface. Mechanical clamps with adjustable screws or levers are often ideal for these types of boards, as they can be easily adjusted to accommodate different sizes.
For smaller or thinner boards, spring or vacuum clamps may be more suitable. These clamps provide a gentle yet secure hold, ensuring that delicate boards are not damaged during the clamping process. The ability to adjust the pressure applied by the clamp is particularly important for thin or flexible PCBs, where excessive force could cause warping or breakage.
Stage of Production
The stage of production also influences the choice of pcb board clamp. For example, during drilling and routing, a strong, stable hold is essential to prevent movement. In this case, a robust mechanical clamp, such as a toggle or screw clamp, is typically the best choice.
During soldering, a clamp that provides consistent pressure without damaging the board is necessary. Spring clamps are often preferred for this stage due to their ease of use and the even pressure they apply. For automated soldering processes, vacuum clamps may be the best option due to their ability to hold the board securely without manual intervention.
Each stage of production presents unique challenges, and the clamp must be capable of meeting these demands. Whether it’s the precision required in drilling or the stability needed during soldering, the right clamp ensures that the PCB is handled correctly and that production proceeds smoothly.
Precision Requirements
Finally, the level of precision required in the production process plays a significant role in choosing a clamp. For processes that require high precision, such as automated assembly or inspection, vacuum clamps are often the best choice. These clamps provide a secure hold without the risk of damaging the board, ensuring that all components are accurately placed and connections are thoroughly tested.
For less precision-intensive processes, such as manual assembly or basic soldering, mechanical clamps may be sufficient. These clamps offer a reliable hold and are easy to adjust, making them versatile tools in various PCB production environments.
Precision is key to ensuring the quality and functionality of the final PCB. The clamp’s ability to maintain the board’s position without causing any damage or misalignment is crucial to achieving this precision. Whether it’s holding the board steady during drilling or ensuring component alignment during soldering, the right clamp can make a significant difference in the production outcome.
Conclusion
In conclusion, the pcb board clamp is a critical tool in the PCB manufacturing and assembly process. It ensures that the board remains secure and stable during various stages, from drilling and routing to soldering and inspection. By providing a reliable hold, PCB board clamps help maintain the integrity and functionality of the final product.
Understanding the different types of PCB board clamps and their applications is essential for selecting the right clamp for a specific task. Whether it’s a mechanical, vacuum, or magnetic clamp, each type offers unique benefits that can enhance the PCB production process. By choosing the appropriate clamp, manufacturers can ensure precise, efficient, and high-quality PCB assembly.