In the design and manufacture of modern electronic devices, printed circuit boards (PCBs) are the core carriers that play a key role in connecting electronic components, transmitting signals and energy. With the iteration of technology, the form and function of circuit boards have gradually differentiated, among which the parallel development of flexible and non-flexible PCBs is particularly eye-catching.
Flex vs Non Flex PCB Evolution and Applications, The differences between these two technical paths in materials, processes and application scenarios have not only promoted the progress of the electronics industry, but also provided more possibilities for the innovation of future devices.
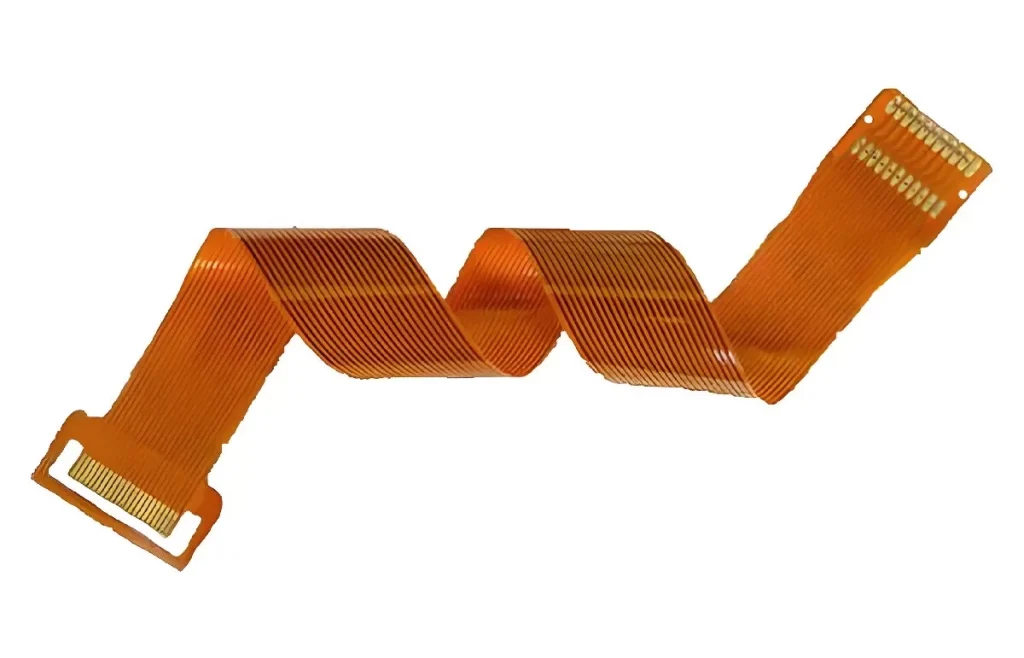
Division of technical characteristics: exploration of materials and structures
From the perspective of physical properties, non-flexible circuit boards are based on rigid substrates (such as FR-4 glass fiber) and form circuits through copper foil etching. Its advantages are high mechanical strength, controllable costs, and suitability for standardized production. For example, in scenarios such as computer motherboards and industrial control equipment that require extremely high stability, non-flexible PCBs always dominate.
They can withstand higher temperatures, pressures and physical shocks to ensure long-term stable operation. However, its limitations are also obvious: the inflexible physical form limits its application in compact spaces or wearable devices. Therefore, when facing complex environments or flexible application requirements, the technical advantages of traditional rigid PCBs are gradually challenged by flexible PCBs.
In contrast, flexible circuit boards use flexible substrates such as polyimide (PI) or polyester film (PET), and special processes are used to bend or even fold the circuit. This feature enables it to adapt to irregular spatial layouts, such as the hinge area of a smartphone’s folding screen and the microprobe of a medical endoscope. The lightweight design of flexible PCBs also significantly reduces the overall weight of the device, meeting the ultimate pursuit of portability for mobile terminals. In addition, flexible PCBs also have excellent shock and vibration resistance, which makes them increasingly used in aerospace, medical equipment and military fields.
Materials and processes for non-flexible PCBs
The material selection and process of non-flexible PCBs are crucial to their performance. Common substrates such as FR-4 and glass fiber materials such as CEM-1/CEM-3 perform well at high temperatures and electrical properties. FR-4 materials are mainly used in environments where power transmission is relatively stable, and have good insulation and moisture resistance. CEM materials are more common in applications with low-cost requirements, such as home appliances and low-end consumer electronics.
In the production process of non-flexible PCBs, pattern transfer is a key step. Common pattern transfer methods include photolithography and laser engraving. Through these methods, each circuit detail can be ensured to be accurate to the micron level, thereby ensuring its stability in high-frequency and high-power applications.
Flexible PCB materials and processes
Flexible PCB materials mainly include polyimide (PI), polyester (PET), polyester ether ketone (PEEK), etc. These materials have excellent temperature resistance and corrosion resistance, and can support the bending, curling and even folding of circuits, which are suitable for more complex design requirements. The core of the flexible PCB production process is how to ensure that the circuit will not crack or break while the material is bent. Laser etching and hot pressing are currently commonly used technologies. The combination of the two can achieve high-precision circuit patterns without damaging the substrate material.
Differentiation and expansion of application scenarios
The difference in the technical characteristics of the two types of circuit boards directly determines the division of their application fields. In the field of consumer electronics, non-flexible PCBs are still the mainstream choice. Taking a laptop as an example, its motherboard needs to carry heavy components such as high-performance processors and memory modules, and the support and heat dissipation performance provided by the rigid substrate are indispensable. Flexible PCBs are more often used for connecting the screen and the motherboard, the internal wiring of the camera module, and other parts that need to be bent repeatedly. This differentiated application enables non-flexible PCBs to meet the needs of high-power devices, while flexible PCBs provide solutions for space and mobility requirements.
Integration of industrial automation
The field of industrial automation presents a more complex integration trend. In the robot joint control system, non-flexible PCBs are responsible for the core control unit, while flexible PCBs are used for sensor signal transmission to adapt to the frequent movement of the robot arm. This combination not only ensures the stability of the system, but also improves the dynamic response capability. With the improvement of the level of automation, the combined application of flexible circuit boards and non-flexible circuit boards has become particularly important. They complement each other and jointly improve the intelligence of industrial systems.
Innovative applications in medical equipment
The innovation of medical equipment further highlights the irreplaceable nature of flexible technology. In implantable pacemakers, flexible circuits can fit the morphology of human tissues and reduce foreign body sensation; the probe part of disposable endoscopes uses ultra-thin flexible circuits to achieve high-definition image transmission while avoiding the rigid constraints of traditional cables. In this field, flexible circuit boards not only ensure the high performance of the equipment, but also improve the comfort and safety of patients by better fitting with the human body.
Challenges and breakthroughs in manufacturing processes
The difference in production processes is another important dimension of differentiation between the two types of circuit boards. The manufacturing of non-flexible PCBs has formed a highly standardized industrial chain. From substrate cutting, drilling, copper plating to welding, each link can be completed by automated equipment. This maturity makes its marginal cost reduction effect significant, and it is particularly suitable for large-scale mass production needs. For industrial applications that require high stability and mass production, non-flexible PCBs provide an extremely cost-effective solution.
The manufacturing of flexible circuit boards faces higher technical barriers. Because the substrate is soft and easy to deform, the etching process needs to be fixed by vacuum adsorption; the lamination process of multi-layer flexible boards requires precise control of temperature and pressure to avoid line deviation caused by thermal expansion of the material. In recent years, the popularization of laser direct imaging (LDI) technology has increased the line width accuracy of flexible circuits to within 10 microns, meeting the needs of 5G high-frequency signal transmission. This technology makes flexible PCBs occupy an increasingly important position in future communication equipment.
Research on new materials
In the field of materials science, the research and development of new composite substrates has further broadened the application boundaries. For example, graphene-enhanced polyimide film improves thermal conductivity by 300% while maintaining flexibility, effectively solving the heat dissipation problem of high-density flexible circuits. This type of new composite material not only improves the performance of flexible PCBs, but also promotes the innovation of high-performance electronic products.
Evolution of reliability test standards
Reliability is always the core consideration for both rigid and flexible circuit boards. The focus of non-flexible PCB testing is on insulation performance in long-term high temperature and high humidity environments, as well as solder joint fatigue strength in vibration scenarios. The IPC-6012 standard formulated by the International Electrotechnical Commission (IEC) specifies key parameters such as substrate peel strength and hole wall copper thickness in detail. With the increasing application of electronic devices in extreme environments, the strictness of the standards is also increasing.
The test system for flexible circuit boards is more complex. In addition to conventional environmental tests, it is also necessary to simulate the bending cycles in actual use. For example, flexible PCBs for folding screen mobile phones must pass more than 200,000 dynamic bending tests, and the resistance change rate must be controlled within 5%. The newly added flexible circuit special evaluation (UL 94V-0) of the US UL certification includes flame retardancy and mechanical durability in the mandatory testing scope. These test standards ensure the reliability of flexible circuit boards under extreme use conditions, greatly promoting the development of emerging fields such as wearable devices and smart homes.
Cost-effectiveness game and balance
In the process of commercialization, the difference in cost structure of the two types of technologies significantly affects corporate decision-making. The cost of a non-flexible PCB is usually 40%-60% lower than that of a flexible version, but its system integration cost may be higher-when multiple rigid boards are required inside the device, the additional cost of connectors and cables will offset the price advantage of the substrate. For high-end devices that need to integrate multiple circuit boards, the advantages of flexible PCBs in system design are becoming more and more significant.
Although the initial investment of flexible circuit boards is high, their space utilization advantage can generate significant returns in miniaturized devices. Taking TWS headphones as an example, the use of flexible circuits can compress the internal space of the charging case by 15%, creating the possibility of increasing battery capacity. This system-level cost optimization makes flexible technology more competitive in high value-added products. As the production process continues to mature, the production cost of flexible PCBs has gradually decreased, further promoting its popularity in the field of consumer electronics.
Future trends: integration and innovation
The current technological development shows obvious integration characteristics. The popularity of rigid-flexible PCBs is a typical example: in the flight control system of drones, the rigid part carries the main control chip, and the flexible part connects the gyroscope and the motor. The overall structure reduces 60% of the connection interfaces, significantly improving reliability. Rigid-flex technology not only improves the integration of products, but also greatly reduces the space waste in traditional circuit board design.
Breakthroughs in new materials and new processes will continue to push the boundaries of technology. The laboratory results of stretchable circuit boards have achieved an elongation of 300%, which may be used in myoelectric sensors for smart clothing in the future; the research and development of biodegradable substrates is expected to solve the problem of electronic waste pollution and open up a new track for environmentally friendly circuit boards.
The combination of artificial intelligence and automated production
In the future, artificial intelligence (AI) and automation technology will become an important force to promote innovation in circuit board manufacturing. The introduction of AI technology will greatly improve the accuracy and efficiency of circuit board design and production. For example, intelligent design tools can automatically optimize circuit layout through machine learning, reducing design errors and production costs; on the production line, intelligent detection systems can monitor any deviations in the production process in real time to ensure the quality stability of the product.
Conclusion
In the wave of continuous evolution of electronic technology, the two types of circuit board technologies are not simply substitutes, but have formed a complementary and symbiotic ecosystem. From smartphones to spacecraft, from pacemakers to smart factories, the choice of technology always serves functional requirements and user experience.
Only by understanding this differentiated value logic can we find the optimal balance between design innovation and cost control and promote the development of the electronic manufacturing industry to a higher dimension. With the continuous breakthroughs in new materials and new processes, circuit board technology will play an increasingly important role in future scientific and technological innovation, open up more application scenarios, and enable more smart devices and innovative products.