Concept of Glass Epoxy PCB
Glass epoxy PCB is a common printed circuit board material, made of glass fiber cloth and epoxy resin combination. Epoxy resin as a hard and excellent electrical insulation resin material, combined with glass fiber, can significantly improve the strength, heat resistance and stability of the PCB.
In conventional PCB materials, the combination of glass fiber and epoxy resin forms a powerful composite material with high compressive strength and bending resistance. The electrical insulation of this material is excellent, so in high-speed, complex electronic systems, glass epoxy PCBs can provide greater electrical stability, avoiding circuit boards subjected to thermal expansion or current instability that can lead to performance degradation.
Compared with other types of PCBs, glass epoxy PCBs are able to maintain good performance at higher temperatures and in harsh environments, and are often used in electronic products that have high requirements for operating temperature, mechanical strength and electrical stability. Whether it is consumer electronics, communication equipment, or automotive electronics, medical equipment, glass epoxy PCBs are widely used.
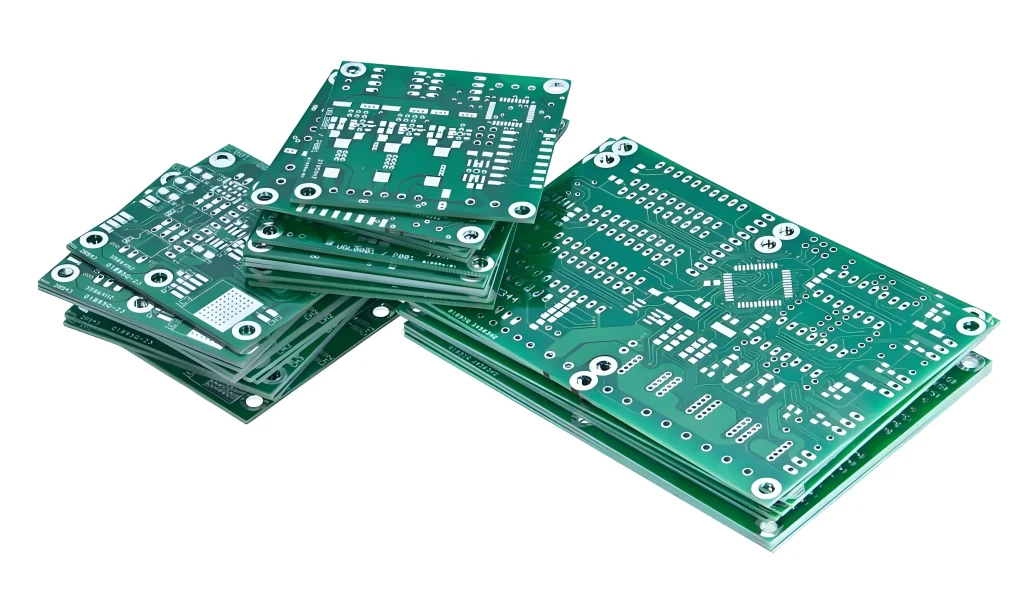
Structure of Glass Epoxy PCB
The structure of this PCB usually consists of three main component layers:
Substrate layer: glass fiber cloth impregnated with epoxy resin, cured at high temperature to form a rigid sheet with high strength and good electrical insulation.
Copper layer: The copper foil layer is directly adhered to the surface of the substrate and is the conductive layer of the PCB circuit. The circuit pattern is removed from the copper layer through an etching process, leaving a conductive path.
Surface Protection Layer: To enhance the reliability and durability of the circuit board, a protective layer (e.g., a solder mask layer) is usually applied to the surface of the copper layer to reduce oxidation and ensure solderability.
These different layers are subject to strict controls during production to ensure that the quality of the final product meets the design requirements. Especially in the production of multilayer PCBs, the precision of the layer-to-layer connections and signal transmission is critical to the performance of the board.
The glass epoxy resin PCB manufacturing process
The manufacturing process of glass epoxy PCB is relatively complex and involves multiple links. The quality of each link has an important impact on the performance of the final product, especially in high-frequency electronic devices and high-end electronic products, the precise manufacturing process is crucial.
- Preparation of substrates
The substrate is the basis of the glass epoxy PCB, which is made by mixing glass fiber cloth and epoxy resin. The key to this process lies in the selection of glass fibers and the curing conditions of the resin. In order to ensure the mechanical strength and electrical properties of the PCB, the direction of laying the glass fibers must be precise and the ratio of the epoxy resin must be strictly controlled. The epoxy resin needs to undergo a high-temperature curing process when combined with the glass fibers to form a hard substrate. The thickness, density, hardness and surface smoothness of the substrate have a direct impact on the final performance of the entire PCB. - Copper foil deposition
The copper foil layer is the electrical foundation of the PCB, and copper is usually deposited on the surface of the substrate through an electroplating process. In this step, the thickness, uniformity and adhesion of the copper foil require special attention to ensure that the circuit conducts without any electrical contact problems. For more demanding PCBs, high purity copper may be used, or even special treatments may be applied to the copper surface to enhance the electrical properties. - Pattern Etching of Circuits
After the copper layer is deposited, the next step is to transfer the circuit pattern onto the copper foil using photolithography. The initial pattern of the circuit is formed by applying a photosensitive material, followed by UV exposure and development. Chemical etching is then used to remove unwanted copper, resulting in the final fine circuit lines. The accuracy of this step directly affects the conductivity and reliability of the circuit. - Drilling and Punching
PCBs often need to be drilled in order to mount components or make electrical connections. The accuracy of the drilled holes is very important, especially in multilayer boards, where inaccurate hole positions may prevent the circuit from being connected properly, or even lead to short circuits and functional failures. Modern drilling techniques often use a combination of laser drilling and mechanical drilling to ensure the quality and consistency of the holes. - Surface treatment and protection
Surface treatments are applied to the surface of the PCB in order to improve its solderability and durability. Common treatments include hot air leveling (HASL), electroplating, silver plating, and so on. Different treatments can be selected according to the use of demand, the purpose is to ensure that the PCB can withstand high-temperature soldering, and maintain good electrical contact performance.
The advantages of glass epoxy PCBs
Glass epoxy PCB has several unique advantages over other types of PCBs, which make it the material of choice for many high-end electronic products.
Excellent mechanical strength
Glass epoxy PCB has high tensile strength and bending resistance due to its powerful composite structure. This makes it able to withstand mechanical shock in various environments without breaking, especially when the equipment is subjected to vibration or physical shock, to maintain its performance unchanged.
Good heat resistance
Glass epoxy PCB can withstand high operating temperatures, and its heat resistance makes it possible to maintain stable electrical performance in high temperature environments. Especially in automotive electronics, aerospace and industrial automation equipment, high temperature resistance is an important consideration for its application.
Excellent electrical insulation
Glass epoxy PCB has excellent electrical insulation, can effectively prevent current leakage and electrical short circuit. For equipment requiring high electrical insulation, such as medical equipment, communication equipment, etc., glass epoxy PCB is undoubtedly the best choice.
High stability and reliability
In high-frequency, high-speed circuits, electrical stability is particularly important. Glass epoxy PCB can ensure that the electrical signals are not interfered with, so as to ensure the stable operation of electronic equipment. In the industrial field, especially in the automation equipment, the high reliability of the circuit board to ensure that the equipment runs for a long time without failure.
Corrosion resistance and long life
Glass epoxy PCB surface usually has a strong corrosion resistance, can effectively avoid the environment of moisture, chemicals on the circuit board erosion. This makes it ideal for use in wet or harsh environments.
Glass epoxy resin PCB application areas
Glass epoxy resin PCB with its excellent performance, widely used in a variety of industries and equipment, especially in the field of circuit stability and durability requirements are extremely high.
In order to adapt to this development trend, glass epoxy PCB design and manufacturing process is moving towards higher precision and smaller size direction. New miniaturization process continues to emerge, the number of layers of the circuit board continues to increase, and even developed into the field of multilayer, and even flexible circuit boards.
- Consumer electronics
Glass epoxy PCBs are widely used in consumer electronics such as smartphones, tablet PCs, and laptops. These devices usually require high miniaturization, high-density circuits and high performance, and glass epoxy PCBs can provide the required high performance and reliability. - Automotive Electronics
With the development of intelligent and automation technology, modern automotive electronics products require more and more circuit boards. Glass epoxy PCBs are widely used in automotive electronic systems because of their ability to maintain excellent performance at high temperatures, high vibration and high load conditions.
Challenges and development trends of glass epoxy PCBs
Although glass epoxy resin PCB has many advantages, but also faces some challenges in its development process. With the continuous miniaturization and high performance of electronic products, the requirements for PCB materials are getting higher and higher. In order to meet future needs, glass epoxy PCBs require continuous innovation in design, manufacturing and materials.
1.Miniaturization and high-density circuit design
With the advancement of technology, electronic products are becoming more and more miniaturized and integrated, which requires PCB design to be able to carry more, smaller and denser components. This puts forward higher requirements for glass epoxy resin PCB: not only need to ensure electrical performance, but also must have a higher density and finer line pattern.
2.High-frequency and high-speed signal transmission capability
With the development of 5G, Internet of Things, automotive electronics and other fields, the signal transmission capability of PCBs has put forward higher requirements. Especially for the design of high-speed and high-frequency circuits, the quality of the signal and the stability of the transmission have become key factors.
The high-frequency performance of glass epoxy PCBs still has certain bottlenecks compared to other materials. In order to enhance its performance, the formulation of the material needs to be continuously optimized, especially the dielectric constant and loss factor (Df) of the material need to be precisely controlled. By introducing new resin materials and glass fiber types, signal loss can be reduced to ensure stable transmission of high-speed signals.
The future of glass epoxy resin PCB technology
With the continuous progress of technology, glass epoxy PCB materials and processes will continue to higher performance, lower cost and more environmentally friendly direction. The following are several major trends in the future development of glass epoxy PCB:
- Stronger thermal management capabilities
As electronic devices become more and more powerful, especially the popularity of high-performance computing, artificial intelligence and 5G communication devices, the power consumption of electronic devices increases, and heat dissipation becomes an important issue. Glass epoxy PCBs need to have better thermal conductivity to ensure that they can dissipate heat efficiently and maintain system stability under high-power operating conditions.
To meet this challenge, researchers are continuously developing new thermal management techniques. For example, the use of new thermally conductive resins or metallic substrate materials can reduce thermal stress and electrical performance degradation in the event of heat buildup. The introduction of these technologies will greatly enhance the potential of glass epoxy PCBs in high-power electronic devices.
- Higher reliability
Reliability has always been an important direction in the development of PCB technology. The reliability of glass epoxy PCB is closely related to its electrical properties and mechanical strength. In order to ensure the stability of the PCB in harsh environments, it is necessary to continuously optimize its resistance to vibration, moisture, oxidation and other properties.
New epoxy resin material formulations are constantly being researched to enhance the reliability of glass epoxy resin PCBs in environments such as high humidity, high temperature and high radiation. Meanwhile, based on advanced testing technology, real-time monitoring of PCBs can be realized to improve their reliability and lifetime.
- Integration of multiple technologies
In the future, glass epoxy resin PCB may no longer be just a single material, but will be combined with other technologies to form a composite PCB. for example, the combination of flexible circuit boards (FPC) and rigid circuit boards (RPCB), so that the PCB can be used in different forms. In addition, glass epoxy PCBs may also be combined with other functional materials (e.g., sensors, wireless charging technology, etc.) to form more intelligent and multifunctional electronic systems. - Highly automated production processes
With the intelligent development of the manufacturing industry, the future production of glass epoxy resin PCB will rely more and more on highly automated production lines. Automation technology not only improves production efficiency, but also reduces errors caused by human factors, ensuring the accuracy and consistency of the PCB.
Through intelligent production management, future PCB factories may be able to achieve fully automated production, further reducing production costs and improving overall product quality and production flexibility.
Summary
Glass epoxy PCB has become one of the indispensable core materials in the modern electronics industry by virtue of its excellent electrical properties, mechanical strength, high temperature resistance and reliability. With the continuous development of science and technology, glass epoxy PCB will continue to meet various challenges and play an important role in many emerging fields. In the future, with the continuous innovation of materials, the improvement of manufacturing process and the advancement of environmental regulations, glass epoxy PCB will play a greater potential in the miniaturization of electronic products, high-speed, intelligent and so on.