FPC connector is a flexible printed circuit board connector, which is usually used to connect two or more flexible printed circuit boards or to connect a flexible printed circuit board to a rigid circuit board. FPC connectors are usually composed of conductive metal foil, insulating substrate and connectors, and have extremely high flexibility to adapt to the shape of curved printed circuit boards.
What is FPC connector
FPC connector is a reliable electronic connection solution, especially suitable for applications that require high reliability and durability. Compared with traditional cable or wire connection methods, FPC connectors have smaller size and weight, which is very useful when making electronic devices with tight space. FPC connectors are often used in consumer electronics, such as smartphones, tablets, laptops, etc.
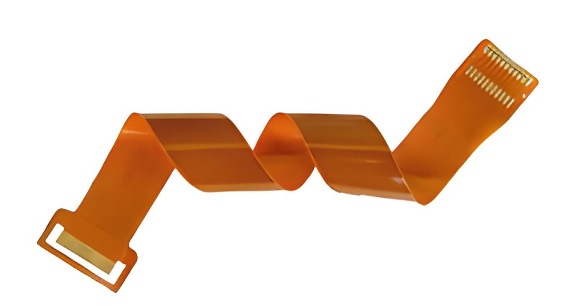
Simply put, FPC is a flexible printed circuit board, which is a printed circuit board made of insulating materials such as polyimide or polyester film and then made by special processes. The flexibility of FPC is given by its structure and materials, which makes it a connection between different components at different layers in a compact space.
In the daily work of electronic engineering technicians, FPC is a component of electronic components that are often touched. The purpose of FPC is also very simple: to build a bridge of communication between circuits that are blocked or isolated in the circuit, so that the current can flow and the circuit can achieve the expected function. It is also a bridge for signal transmission and reception.
Evolution of FPC Connectors
The Emergence of Flexible Electronics
Flexible electronics have revolutionized the design and functionality of electronic devices, enabling curved, bendable, and even stretchable form factors. FPC connectors play a pivotal role in this evolution, providing the necessary interface for connecting flexible circuits to rigid PCBs or other electronic components.
Early Developments and Challenges
The early iterations of FPC connectors were rudimentary, primarily consisting of simple flexible cables with soldered contacts. These connectors faced challenges such as limited flexibility, susceptibility to mechanical stress, and reliability issues. However, they laid the groundwork for further advancements in FPC technology.
Advancements in Materials and Manufacturing
The evolution of FPC connectors has been propelled by advancements in materials and manufacturing techniques. The introduction of flexible substrates such as polyimide and polyester has significantly enhanced the flexibility, durability, and thermal stability of FPC connectors. Furthermore, innovative manufacturing processes such as roll-to-roll printing and laser ablation have enabled the mass production of intricate FPC designs with high precision.
Miniaturization and High-Density Interconnects
One of the most notable trends in FPC connector evolution is miniaturization and the pursuit of high-density interconnect solutions. As electronic devices become smaller and more compact, there is a growing demand for FPC connectors with reduced form factors and increased contact density. Manufacturers have responded by developing ultra-miniature FPC connectors with pitch sizes as small as **<black>FPC connector</black>**0.2mm, catering to the needs of space-constrained applications such as wearable devices and IoT sensors.
Functionality of FPC Connectors
Electrical Connectivity and Signal Integrity
At its core, the primary function of an FPC connector is to establish electrical connectivity between flexible circuits and other electronic components while maintaining signal integrity. FPC connectors achieve this through the precise alignment of conductive traces on the flexible substrate with corresponding contacts on the mating connector. This ensures reliable transmission of power and data signals without signal degradation or loss.
Mechanical Flexibility and Durability
Unlike traditional rigid connectors, FPC connectors offer unparalleled mechanical flexibility, allowing them to withstand repeated bending, twisting, and flexing without compromising performance. This flexibility is essential for applications that involve movable or deformable components, such as foldable smartphones, automotive interiors, and medical devices. Additionally, FPC connectors exhibit exceptional durability, withstanding harsh environmental conditions such as temperature extremes, humidity, and vibration.
Ergonomics and User Experience
The design of FPC connectors significantly impacts the ergonomics and user experience of electronic devices. Slim, low-profile connectors contribute to sleek and aesthetically pleasing designs, while easy-to-use locking mechanisms enhance usability and reliability. Furthermore, the flexibility of FPC connectors enables innovative form factors and ergonomic designs, improving comfort and usability for end-users.
High-Speed Data Transmission
With the proliferation of high-speed data interfaces such as USB, HDMI, and PCIe, there is a growing demand for FPC connectors capable of supporting high-speed data transmission. Advanced FPC connector designs incorporate features such as differential signaling, impedance matching, and shielding to minimize signal interference and ensure reliable data transfer at **<black>FPC connector</black>**multi-gigabit per second speeds. These connectors find applications in high-performance computing, multimedia devices, and automotive infotainment systems.
Applications of FPC Connectors
Consumer Electronics
FPC connectors are ubiquitous in consumer electronics, serving as the backbone of smartphones, tablets, laptops, and smartwatches. Their compact form factor, high reliability, and flexibility make them ideal for internal connections within these devices, facilitating interconnections between PCBs, displays, cameras, and other components.
Automotive Electronics
The automotive industry relies on FPC connectors for a wide range of applications, including vehicle infotainment systems, instrument clusters, navigation displays, and advanced driver-assistance systems (ADAS). FPC connectors withstand the rigors of the automotive environment, including temperature fluctuations, vibrations, and exposure to moisture, while providing seamless connectivity and signal integrity.
Medical Devices
In the medical field, FPC connectors play a crucial role in the design and manufacturing of diagnostic equipment, patient monitoring devices, and medical imaging systems. Their flexibility, reliability, and sterilizability make them suitable for use in disposable and reusable medical devices, ensuring accurate data transmission and patient safety.
Industrial and IoT Applications
Industrial and IoT (Internet of Things) applications leverage FPC connectors for sensor networks, industrial automation, robotics, and smart home devices. The compact size, high reliability, and customizable form factors of FPC connectors enable seamless integration into IoT devices, facilitating connectivity and data exchange in diverse environments.
Future Prospects and Emerging Trends
Flexible Hybrid Electronics (FHE)
Flexible hybrid electronics (FHE) represent the next frontier in electronic design, combining the flexibility of FPC technology with the functionality of traditional rigid components. FHE enables the integration of sensors, actuators, power sources, and computational elements onto flexible substrates, opening up new possibilities for wearable electronics, e-textiles, and conformable sensors.
5G and Beyond
The advent of 5G technology promises unprecedented levels of connectivity and bandwidth, driving the demand for FPC connectors capable of supporting **<black>FPC connector</black>**multi-gigabit per second data rates. FPC connectors will play a vital role in 5G infrastructure, enabling high-speed data transmission in base stations, antennas, and mobile devices.
Advancements in Materials Science
Continued advancements in materials science are expected to further enhance the performance and functionality of FPC connectors. Novel materials with improved electrical conductivity, thermal stability, and mechanical properties will enable the development of FPC connectors optimized for specific applications, such as flexible OLED displays, bendable sensors, and stretchable electronics.
Integration of Smart Features
FPC connectors are poised to incorporate smart features such as self-diagnosis, self-healing, and adaptive connectivity, enhancing their reliability and functionality. Smart FPC connectors will be capable of detecting and mitigating connection issues, optimizing signal quality, and adapting to changing environmental conditions, thereby extending the lifespan and performance of electronic devices.
Conclusion
In conclusion, FPC connectors have evolved from simple interconnects to sophisticated components that enable the development of flexible, compact, and high-performance electronic devices. Their unique combination of electrical connectivity, mechanical flexibility, and durability has made them indispensable in a wide range of applications, spanning consumer electronics, automotive, medical, industrial, and IoT sectors. As technology continues to advance, FPC connectors will continue to play a pivotal role in shaping the future of electronics, enabling innovative solutions that push the boundaries of what is possible.