In the modern electronics manufacturing industry, it is crucial to ensure the quality and performance of circuit boards. With the development of science and technology, the complexity of electronic products continues to increase, and the requirements for circuit board testing are getting higher and higher. Among the many test methods, PCB functional tester plays a key role.
It can not only detect the basic functions of the circuit board, but also find potential faults and improve the reliability and stability of the product. Therefore, it is of great significance for the electronics manufacturing industry to have a deep understanding of the working principle, application field and future development trend of PCBA function tester equipment.
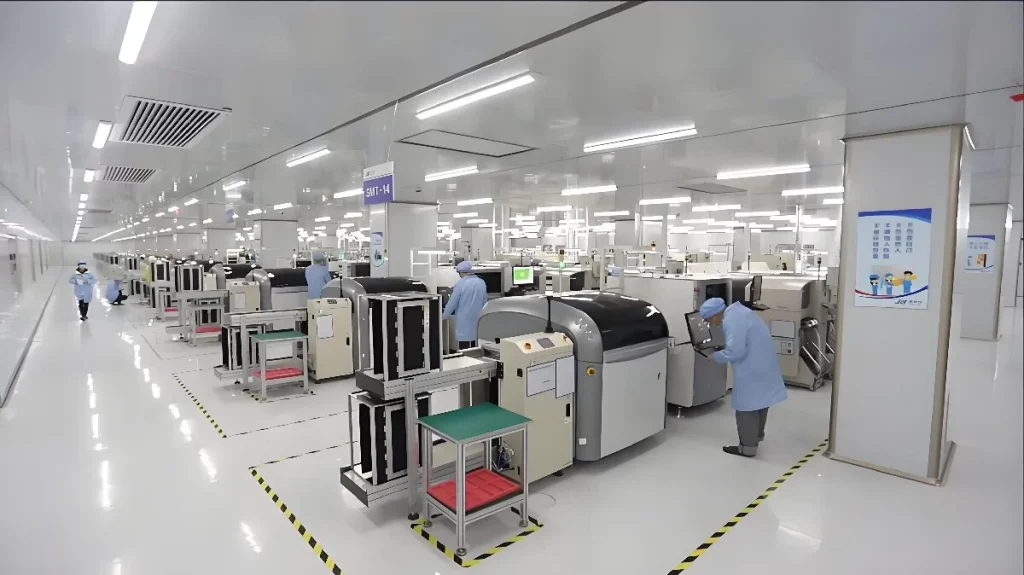
Basic concept of PCB functional tester
PCB functional tester is a device specially used to detect whether the function of printed circuit board (PCB) is normal. Its main function is to simulate the working environment of the circuit board in actual use and test its electrical performance. This equipment can check whether the circuit board can be powered on normally, whether each component can operate normally, and whether the signal transmission is stable. Compared with other test methods, such as visual inspection, flying probe test, etc., PCB functional tester is more accurate and can comprehensively evaluate the overall performance of the circuit board.
Working principle of PCB functional tester
The core principle of PCB functional tester is to detect the response of the circuit board by applying a certain electrical signal. For example, during the test, the device applies a voltage or current signal to the input of the circuit board and monitors the feedback at its output. If the output signal is consistent with the design expectation, it means that the PCB functions normally; if there is a deviation, it indicates that the circuit board may have some defects or faults. In addition, some high-end testers are also equipped with automatic fault diagnosis functions, which can quickly locate the fault point and improve maintenance efficiency.
PCB functional testers usually consist of multiple parts, including signal generation module, measurement module, data processing system, etc. The signal generation module is used to simulate the working environment of the circuit board, the measurement module is used to detect the output signal, and the data processing system analyzes the test results and provides a detailed test report. This equipment can effectively screen for problems such as short circuits, open circuits, and signal attenuation to ensure that the circuit board can operate stably in actual applications.
Main types of PCB functional testers
According to different test requirements, PCB functional testers can be divided into various types, including general-purpose, special-purpose, and customized types.
General-purpose tester: This tester is suitable for various types of PCBs and has high flexibility. They usually have multiple test modes built in to adapt to circuit boards of different specifications. This equipment is widely used in the electronics manufacturing industry, especially in the quality inspection stage of product development and early production.
Special tester: Special testers test specific types of PCBs. For example, some testers are specifically used to detect high-frequency circuit boards, while others are specifically used to detect power management modules. Due to their strong targeting, this type of equipment is widely used in specific industries, such as communication equipment, medical electronics and other fields.
Customized tester: Some companies need to perform refined tests on specific PCBs, so they will choose customized testers. The hardware and software of this tester can be adjusted according to the needs of the company to meet the testing requirements of specific products. Although the cost is high, it can provide the most accurate test results, thereby improving product quality.
Application areas of PCB functional testers
PCB functional testers play an important role in many industries, especially in electronic manufacturing, automotive electronics, medical equipment and aerospace.
Electronic manufacturing industry: The replacement speed of electronic products is extremely fast, and manufacturing companies need to ensure that each circuit board can work properly. PCB functional testers can quickly detect the functions of circuit boards, reduce the flow of defective products into the market, and improve production efficiency.
Automotive electronics: With the advancement of automotive intelligence, on-board electronic systems are becoming more and more complex. PCB functional testers are used to detect on-board control modules, sensor circuits, etc. to ensure the stability and safety of automotive electronic systems.
Medical equipment: Medical electronic equipment has extremely high reliability requirements. For example, pacemakers and monitors need to undergo rigorous testing. PCB functional testers can ensure that the circuit boards of these devices can work stably in various environments to avoid unexpected failures.
Aerospace: Electronic equipment in spacecraft and satellites must withstand extreme environments, so the quality requirements of circuit boards are extremely strict. PCB functional testers are used to detect key circuits in aerospace electronic systems to ensure that they can still operate stably under extreme conditions.
Advantages of PCBA functional testers
Compared with traditional testing methods, PCB functional testers have the following significant advantages:
High test accuracy: It can accurately detect various electrical characteristics of circuit boards, including voltage, current, signal integrity, etc.
High detection efficiency: Automated testing equipment can quickly complete the detection of large quantities of PCBs, improve production efficiency, and reduce labor costs.
Strong adaptability: It can be adjusted for different types of PCBs and is suitable for the testing needs of various complex circuit boards.
Strong fault diagnosis ability: can accurately locate the fault point, reduce maintenance time, and improve product reliability.
Improve product quality and production efficiency
With the continuous development of PCB functional tester technology, its role in improving production efficiency and product quality has become more prominent.
In the traditional production process, detection work often relies on manual inspection or other simpler testing equipment. These methods are not only time-consuming and error-prone, but also more likely to miss potential quality problems, especially in the case of large production batches.
After using the PCB functional tester, each circuit board in the production process can be tested quickly and accurately, and faults can be discovered and eliminated in time. This not only reduces the rework cost caused by defective products, but also significantly improves production efficiency. In addition, the introduction of automated testing systems makes the operation of the production line smoother and greatly shortens the production cycle.
By reducing manual intervention, PCB functional testers provide companies with more efficient and reliable solutions, ensuring that each circuit board can meet high standards.
Improve R&D and innovation capabilities
In addition to its application in the production and manufacturing stage, PCB functional testers also play a vital role in the R&D stage. During the design and development of electronic products, the design team needs to continuously test the functions and performance of different prototype boards.
PCB functional testers provide accurate testing methods that can help engineers promptly discover potential design problems and improve them during product design. Compared with traditional manual testing methods, the use of PCB functional testers can greatly shorten testing time and improve R&D efficiency.
At the same time, with the continuous development of new technologies, modern PCB functional testers are becoming more and more intelligent, equipped with automatic fault diagnosis and analysis tools, which can help R&D teams better understand the operating mechanism and potential problems of products, thereby accelerating innovation and technology iteration.
This enables companies to launch high-quality products more quickly when facing market demand, further enhancing their market competitiveness.
Reduce production costs and improve market competitiveness
In the modern electronic manufacturing industry, reducing production costs is one of the important means for companies to maintain their competitiveness, and the application of PCB functional testers can help companies make breakthroughs in this regard. Traditional detection methods often require a lot of manual participation, which is not only costly but also inefficient.
PCB functional testers can realize automated testing, reduce dependence on manual labor, and thus reduce labor costs. At the same time, due to its efficient detection capability, it can detect defects in time in the early stage of production, avoid a large number of defective products from flowing into the next stage of production or the market, thereby reducing rework and after-sales repair costs.
In addition, accurate test data can also help companies optimize product design, reduce material waste, and improve production yield. By reducing overall production costs and improving product quality, companies can occupy a more advantageous position in the fierce market competition, thereby winning more customers’ trust and orders.
Future Development Trends of PCB Functional Testers
With the continuous advancement of electronic manufacturing technology, PCB functional testers are also constantly developing. In the future, the equipment may evolve in the following directions:
Intelligence and Automation: Future PCB functional testers will be more intelligent, able to automatically analyze test data, and predict faults based on test results. This will greatly improve detection efficiency and reduce the possibility of human error.
Higher test accuracy: As the size of electronic components continues to shrink, future testers will require higher accuracy to detect changes in tiny signals and ensure the stability of high-density circuit boards.
Remote testing and cloud computing: Future PCB functional testers may support remote testing and upload test data to the cloud for analysis. In this way, engineers can view test results anytime and anywhere, and perform fault diagnosis to improve maintenance efficiency.
Green and environmental testing: With increasingly stringent environmental regulations, future test equipment will pay more attention to energy conservation and emission reduction, reduce energy consumption, and adopt more environmentally friendly materials and processes.
Conclusion
PCBA functional tester plays an indispensable role in the electronics manufacturing industry. It can not only improve product quality, but also reduce production costs and enhance corporate competitiveness. With the continuous development of technology, this kind of test equipment will become more intelligent and precise, and play an important role in more fields. Therefore, for electronic manufacturing companies, in-depth understanding and reasonable application of PCB functional tester will help improve product quality and promote enterprises to move towards high-end manufacturing.