Industrial control PCB is a multi-layer printed circuit board used in industrial control, which is one of the essential core components in industrial automation control systems. They are mainly composed of electronic components such as Large Scale Integrated Circuits (LSIs) and Surface Mount Integrated Circuits (MSIs). These components form complex electronic systems inside multi-layer PCBs, achieving various functions through precise circuit design and wiring, including but not limited to data acquisition, processing, transmission, and control.
The design and manufacturing of industrial control PCBs require a high level of technical knowledge and strict quality control to ensure their stable and reliable operation in harsh industrial environments. These PCBs need to resist environmental factors such as extreme temperature, humidity, dust, and electromagnetic interference, while also adapting to frequent mechanical vibrations and impacts.
Therefore, industrial control PCBs are not only important components of industrial control machines, but also a key factor in ensuring the efficient and stable operation of industrial automation control systems.
In the field of modern industrial automation and control, PCB printed circuit boards play a crucial role. Especially industrial control PCBs (printed circuit boards for industrial control), they are the heart of various complex industrial equipment, responsible for the transmission and processing of electronic signals, ensuring the stable operation of the system. Given its application requirements in harsh environments, there are a series of strict requirements and standard specifications for the design, manufacturing, and material selection of industrial control PCBs.
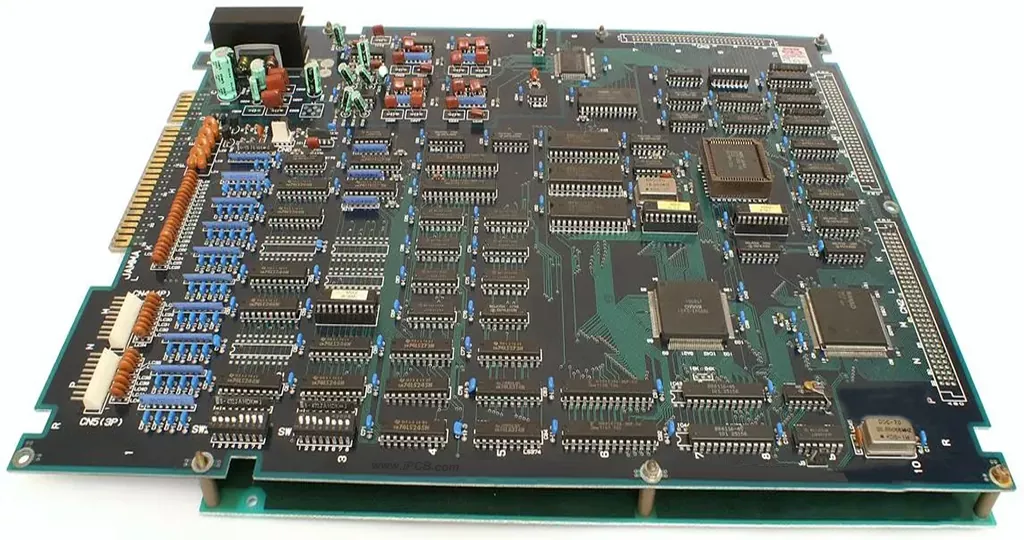
Industrial control requires environmental adaptability, and industrial control PCBs must be able to work stably in harsh environments such as extreme temperature, humidity, vibration, and dust. Therefore, the selection of PCB materials is particularly crucial.
Temperature resistance: Select substrates that can withstand a wide temperature range (usually -40 ° C to+85 ° C or even higher), such as FR-4 materials with high Tg (glass transition temperature).
Moisture resistance: Adopting moisture-proof coating and sealing technology to prevent moisture penetration and reduce the risk of circuit corrosion.
Vibration resistance: When designing, consider component reinforcement and layout, using more robust welding techniques and support structures to resist long-term vibration.
Industrial control requires high reliability requirements, and in industrial control scenarios, fault costs are high. Therefore, industrial control must have extremely high reliability for PCBs.
Redundant design: Key circuits adopt dual or multi-channel design to improve system fault tolerance.
Signal integrity: Optimize wiring, reduce signal interference, and ensure the stability of high-speed signal transmission.
Coating quality: High quality surface treatment techniques such as gold plating and chemical nickel gold are used to enhance connection reliability.
The electromagnetic compatibility (EMC) standard for industrial control circuit boards, electromagnetic interference (EMI) is common in industrial environments, and industrial control PCBs must comply with strict EMC standards, such as the IEC 61000 series.
Shielding measures: Adopting a shielding cover and grounding layer design to reduce external interference and contain internal radiation.
Filter design: Integrate a filter at the power inlet to suppress noise propagation.
Signal line protection: Differential pairing or shielding of sensitive signal lines to reduce interference effects.
The safety regulations for industrial control circuits follow the safety standards of the International Electrotechnical Commission (IEC), UL and other organizations to ensure electrical safety
Insulation distance: Ensure sufficient insulation distance between high voltage, low voltage, and signal lines.
Fire rating: Use flame-retardant materials to meet the requirements of V-0 or higher fire rating.
Production and testing standards for industrial control circuit boards
From design to production, every step must comply with industry standards, such as the quality requirements of IPC-A-600/610 for PCBs.
Precision manufacturing: Using high-precision production equipment to ensure circuit accuracy and tolerance control.
Strict testing: Conduct comprehensive testing including flying needle testing, AOI (Automatic Optical Inspection), X-ray testing, etc., to ensure that the PCB is defect free.
The design and manufacturing of industrial control PCB is a highly specialized field that not only meets basic electronic functional requirements, but also maintains efficient, stable, and safe working conditions in complex and ever-changing industrial environments. By following the above requirements and standard specifications, it can be ensured that industrial control equipment can still operate reliably under long-term and high load operating conditions, providing a solid foundation for the development of industrial automation. With the continuous advancement of technology, industrial control PCBs will become more intelligent and integrated in the future, continuously promoting the development of Industry 4.0 era.
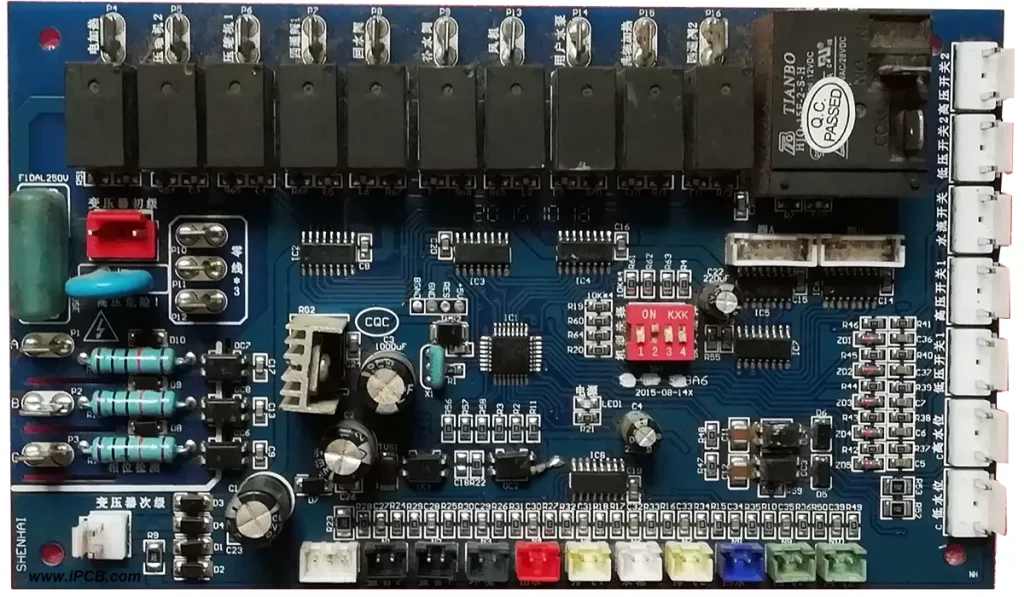
Application of Industrial Control Circuit Board
Industrial control PCBs have a wide range of applications in various fields of industrial automation control. For example, in the automotive manufacturing process, industrial control PCBs can be used to achieve automated production line control, improve production efficiency and quality. In the field of petrochemicals, industrial control PCBs can be used to monitor and control the operation of systems, ensuring the safety and stability of the production process. In the field of power, industrial control PCBs can be used to monitor the operation status of the power grid and achieve power automation control. In the textile industry, industrial control PCBs can be used to achieve automated textile machinery control, improve the quality and output of textiles. In the logistics field, industrial control PCBs can be used to achieve automated warehouse management, improve warehouse operation efficiency and accuracy.
The application of industrial control PCBs can improve production efficiency and quality, ensuring the safety and stability of the production process.
Industrial control PCB is one of the core components in industrial automation control, which plays an important role and has a wide range of applications. In order to meet the needs of industrial automation control, industrial control PCBs need to have advantages such as high integration, high reliability, customization, and high cost-effectiveness. When manufacturing industrial control PCBs, it is necessary to meet requirements such as high precision, high reliability, high temperature resistance, shock resistance, and electromagnetic compatibility.