Low-temperature co-fired ceramic (LTCC) technology is an eye-catching integrated component technology developed in recent years. It represents the development direction of miniaturization, high frequency and integration of electronic components. It has now become the mainstream implementation solution for passive integration.
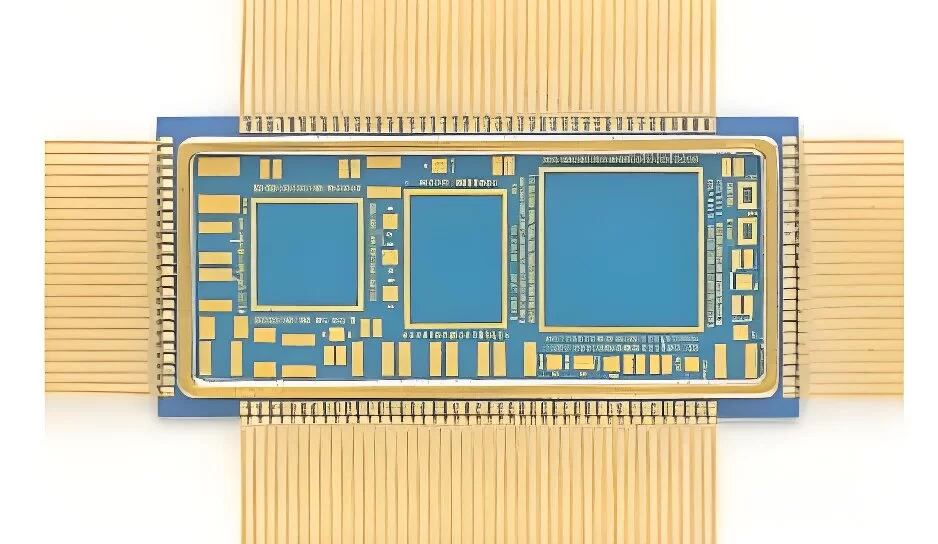
LTCC material requirements:
The material performance requirements of LTCC devices include three aspects: electrical performance, thermomechanical performance and process performance.
The dielectric constant is the most critical property of LTCC materials. Since the length of the resonator, the basic unit of a radio frequency device, is inversely proportional to the square root of the dielectric constant of the material, when the operating frequency of the device is low (such as hundreds of megahertz), if a material with a low dielectric constant is used, the device will The size will be too large to be used. Therefore, it is best to serialize the dielectric constant to suit different operating frequencies.
Dielectric loss is also an important parameter to consider when designing radio frequency devices. It is directly related to the loss of the device. In theory, I hope the smaller the better. The temperature coefficient of dielectric constant is an important parameter that determines the temperature stability of the electrical properties of radio frequency devices.
In order to ensure the reliability of LTCC devices, many thermomechanical properties must also be considered when selecting materials. The most critical of these is the thermal expansion coefficient, which should match the circuit board to which it is to be soldered as closely as possible. In addition, considering processing and subsequent applications, LTCC materials should also meet many mechanical property requirements, such as bending strength σ, hardness Hv, surface flatness, elastic modulus E, fracture toughness KIC, etc.
The process performance can generally include the following aspects: First, it can be sintered into a dense, non-porous microstructure at a temperature below 900°C. Second, the densification temperature cannot be too low to avoid preventing the discharge of organic matter in the silver paste and green tape. Third, after adding appropriate organic materials, it can be cast into a uniform, smooth, and strong green tape.
Classification of LTCC materials:
The composition of LTCC ceramics is the key factor that determines its physical and chemical properties and electrical properties. At present, there are three main categories of ceramic materials used in LTCC: glass/ceramic composite system, crystallized glass system and amorphous glass system. Among them, the first two glass/ceramic composite systems and crystallized glass systems are the focus of research in the industry.
Properties of LTCC materials:
The performance of LTCC products depends entirely on the performance of the materials used. LTCC ceramic materials mainly include LTCC substrate materials, packaging materials and microwave device materials. The dielectric constant is the most critical property of LTCC materials. The dielectric constant is required to be serialized in the range of 2 to 20,000 to be suitable for different operating frequencies.
For example, a substrate with a relative dielectric constant of 3.8 is suitable for the design of high-speed digital circuits; a substrate with a relative dielectric constant of 6 to 80 can well complete the design of high-frequency circuits; a substrate with a relative dielectric constant of up to 20,000 can be used Highly capacitive devices are integrated into multilayer structures. High frequency is a natural trend in the development of digital 3C products.
Developing LTCC materials with low dielectric constant (ε≤10) to meet the requirements of high frequency and high speed is a challenge for LTCC materials to adapt to high frequency applications. The dielectric constant of FerroA6 and DuPont’s 901 system is 5.2 to 5.9, ESL’s 4110-70C is 4.3 to 4.7, the dielectric constant of NEC’s LTCC substrate is about 3.9, and dielectric constants as low as 2.5 are under development.
The size of the resonator is inversely proportional to the square root of the dielectric constant. Therefore, when used as a dielectric material, the dielectric constant is required to be large to reduce the size of the device. Currently, dielectric materials with ultra-low loss limit or ultra-high Q value, relative dielectric constant (>100) or even >150 are hot topics of research.
For circuits that require a larger capacitance, materials with a high dielectric constant can be used, or a dielectric material layer with a larger dielectric constant can be sandwiched in the LTCC dielectric ceramic substrate material layer. The dielectric constant can be between 20 and 100. Choose between. Dielectric loss is also an important parameter to consider when designing radio frequency devices.
It is directly related to the loss of the device. In theory, it is hoped that the smaller the better. Currently, the main LTCC materials produced for radio frequency devices are DuPont (951, 943), Ferro (A6M, A6S), Heraeus (CT700, CT800 and CT2000) and Electro-science Laboratories. They can not only provide LTCC green ceramic tapes with serialized dielectric constants, but also provide wiring materials that match them.
Another hot issue in LTCC material research is the matching of co-fired materials. When co-firing different dielectric layers (capacitors, resistors, inductors, conductors, etc.), it is necessary to control the reaction and interfacial diffusion between different interfaces so that the co-firing matching of each dielectric layer is good, and the densification rate and sintering shrinkage between interface layers must be controlled. The rate and thermal expansion rate should be as consistent as possible to reduce the occurrence of defects such as spalling, warping and cracks.
Development trend:
In summary, LTCC materials have experienced a development process from simple to composite, from low dielectric constant to high dielectric constant, and the use frequency band continues to increase. Evaluated from the perspectives of technology maturity, industrialization and extensive application, LTCC technology is currently the mainstream technology for passive integration.
The above is all shared by Mia