What is Modular PCB Design?
With the increasing complexity of electronic product functions, traditional single circuit board design has been unable to meet the needs of rapid iteration, flexible upgrades and efficient maintenance. In this context, the concept of “Modular PCB Design” came into being and gradually became an important trend in the electronics manufacturing industry.
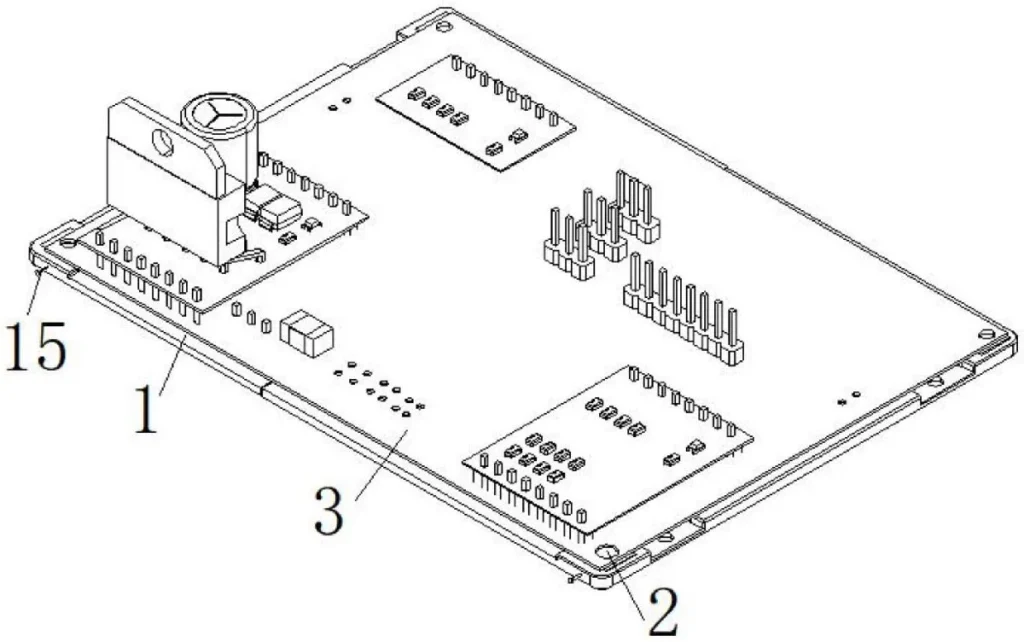
Modular PCB design, as the name suggests, is to divide the complex PCB design into several independent and functional modules. Each module can be designed, tested, and manufactured separately, and combined into a complete system like a puzzle during the final assembly. This design idea originates from the concept of system engineering and modular design, emphasizing standardized interfaces, reusability and system-level optimization.
Compared with the traditional “full-function centralized” PCB design, modular design is not just a formal split, but a systematic and forward-looking engineering strategy that takes into account the later scalability, maintainability and production efficiency from the design stage.
Real-world application
Communication equipment: such as 5G base stations, routers, control modules and RF modules are separated;
Medical equipment: such as the decoupling of signal acquisition modules and processing modules in vital signs monitoring equipment;
Industrial control systems: such as PLC I/O modules, CPU modules and other split designs;
Consumer electronics: such as detachable camera modules, smart home core control modules, etc.
It is worth mentioning that modularization is not only applicable to large and complex products, but also in some small and medium-sized projects, modularization can be used to improve project development efficiency, reduce the difficulty of later maintenance, and achieve multi-model shared design and other advantages.
In summary, Modular PCB Design is not only a product of technological development, but also a reflection of the deep integration of engineering management and product strategy. It brings not only structural optimization, but also a profound innovation in the overall development process and product life cycle cost.
Core advantages of modular PCB design
The reason why modular PCB design has gradually become mainstream in recent years is not only because it “looks neat”, but also because it brings advantages that cannot be ignored in various links such as actual product development, engineering collaboration and after-sales maintenance.
Reduce design complexity
In traditional design, a multifunctional PCB usually includes various functions such as processor, power supply, sensor interface, communication module, etc. This means that the PCB wiring density is high, the number of layers is large, and debugging is difficult. A slight logical error may cause the entire board to be scrapped. Modular design “splits” the circuit board into several functional blocks, each module focuses on a single function, allowing engineers to complete the design under simpler and clearer logic. Even if a certain module has a design defect, there is no need to overturn the entire design.
Shorten the product development cycle
In a rapidly changing market environment, “whoever launches a new product first will be competitive.” One of the greatest values of modular design is to significantly speed up the R&D iteration speed. For example, the power module or communication module used in a certain generation of products is mature and stable, and can be directly reused in the next generation of products without redesign and testing, saving a lot of time and labor costs. For cross-border or cross-departmental collaborative projects, different modules can be developed in parallel by different teams to further improve efficiency.
Improve system stability and reliability
In modular design, each module can be specially tested in an independent environment, especially high-voltage, high-frequency or interference-prone modules, which can be physically isolated from other parts, thereby reducing interference between systems and improving the stability of the whole machine. At the same time, if a module has a problem, it can also be quickly located and replaced to reduce the risk of system failure propagation.
Enhance product maintenance and scalability
From the perspective of after-sales service, modular design brings great convenience to maintenance. Compared with the traditional whole-board maintenance, which requires precise finding and welding of tiny components, modular design can usually directly replace the faulty module, greatly reducing the maintenance time. For customers, this means shorter downtime; for enterprises, this means lower after-sales costs.
In addition, as customers’ functional requirements change, modular design can also easily achieve system expansion. For example, in some industrial control systems, customers may only need 4 sensor interfaces in the early stage. When demand increases in the future, they can complete the upgrade by adding a module without replacing the entire motherboard or system.
Reduce the difficulty of production and inventory management
At the manufacturing level, modular design has another hidden advantage: standardized production and inventory control. Each module has standard specifications, and can be processed in batches and tested uniformly during production; spare parts can also be managed as modules in storage. Especially in flexible manufacturing scenarios with multiple varieties and small batches, modularization brings great flexibility and convenience in inventory management.
Typical application scenarios and industry trends of modular PCB
Modular PCB design has been widely used in many industries due to its flexibility, efficiency, and ease of maintenance, and its application scope continues to expand with the development of technology. Understanding these typical application scenarios will help grasp the actual value and future direction of this design concept.
Modular design application in the communication industry
Communication equipment, especially base stations and routers, has complex functions and fast update speed. Modular design allows RF modules, digital signal processing modules, power management modules, etc. to be independently designed and upgraded. This not only shortens the product iteration cycle, but also reduces the overall system risk caused by the upgrade of a single module. For example, different frequency band modules of 5G base stations can be flexibly replaced according to demand, greatly improving the applicability and life of the equipment.
Modular trend in medical equipment
Medical equipment has extremely high requirements for reliability and flexibility. Modular design allows key functions such as sensor modules, signal amplification modules, and processing modules to be designed and verified separately to ensure the accuracy and stability of each part. At the same time, with the development of personalized medicine and remote monitoring, modular PCB supports equipment customization and rapid upgrades to meet diverse medical needs.
Industrial Automation Field
Industrial control systems often involve complex sensor input, actuator control and communication requirements. Modular design enables I/O modules, CPU modules, and power modules to be flexibly combined to adapt to different industrial scenarios. Customers can flexibly add or replace modules according to on-site needs to customize and expand equipment. At the same time, modular design also supports the rapid replacement of faulty modules on site to reduce maintenance costs and downtime.
Consumer electronics and smart hardware
Smart homes, wearable devices and other consumer electronics fields have high requirements for lightweight, integrated and rapid iteration of products. Modular PCB design helps manufacturers quickly launch multi-functional products through standardized interfaces and module combinations to support diversified market needs. At the same time, it also facilitates product personalization and meets users’ differentiated experience.
Industry Trends and Future Outlook
With the advancement of electronic technology and the maturity of the industrial chain, the concept of modular PCB design will become more popular. Future trends include:
Intelligent design tool support: With the modular design function of EDA tools, engineers can develop and integrate modules more efficiently.
Standardized interfaces and interoperability: The industry will promote more standard interface protocols to ensure seamless collaboration between different modules.
Green manufacturing and sustainable development: Modular design helps reduce resource waste and electronic waste, which is in line with environmental protection trends.
Combination of flexibility and rigidity: Modular design will combine more flexible PCB technology to enhance the ability of products to adapt to complex forms.
Cloud collaboration and remote debugging: With the rise of remote office and global supply chain collaboration, modular design is more convenient for distributed team collaborative development.
Challenges and solutions for modular PCB design
Although modular PCB design brings many advantages, it also faces many challenges in actual application. Only by effectively identifying and responding to these problems can the potential of modular design be better exerted and the improvement of product quality and market competitiveness be promoted.
Challenge 1: Interface standardization problem
The interface between modules is the key to achieving flexible combination, but the industry currently lacks a unified interface standard. The interface form, signal definition, and mechanical size adopted by different manufacturers or design teams may be quite different, resulting in insufficient compatibility between modules.
Solution: Actively participate in industry standard organizations to promote the formulation of unified interface specifications. Enterprises also need to formulate strict interface specification documents to ensure that the design teams of each module collaborate to achieve interface compatibility and interchangeability. At the same time, design universal adapters or adapter boards to bridge the interface differences between different modules.
Challenge 2: Signal integrity and electromagnetic compatibility
Modular design often involves high-speed signal transmission between multiple boards, with multiple and complex interfaces, which can easily cause signal attenuation, crosstalk and electromagnetic interference problems, affecting system stability and performance.
Solution: During the PCB design stage, simulation analysis tools are used to evaluate signal integrity (SI) and electromagnetic compatibility (EMC). Optimize interface layout and routing, and reasonably design grounding layers and shielding structures. Use differential signals and shielded cables to reduce interference. For key high-speed signals, use high-speed connectors and dedicated high-speed transmission technologies.
Challenge 3: Complex mechanical structure and assembly
Multi-module combination may lead to complex mechanical size and structure, unreliable connection between modules or immature assembly process, affecting product reliability and user experience.
Solution: Modular design requires mechanical structure planning in advance to ensure standardized module size and installation method. Use high-quality connectors and lock design to ensure a stable connection between modules. Develop detailed process flow and quality inspection standards during assembly to ensure assembly accuracy and repeatability.
Challenge 4: Thermal management problem
The modules in modular PCBs have different functions and uneven power distribution, which is prone to local overheating problems, affecting device life and system stability.
Solution: Fully consider thermal management strategies during design, including reasonable layout of high-power modules and auxiliary heat dissipation measures such as heat sinks, thermal conductive materials and fans. Use thermal simulation software to predict hot spots and optimize heat dissipation paths. Use advanced heat dissipation technologies such as liquid cooling or phase change materials when necessary.
Challenge 5: Cost control
Although modular design can improve flexibility and maintenance efficiency, the design, manufacturing and testing links increase complexity and may bring higher upfront costs.
Solution: Reduce unit costs through standardized module design and large-scale production. Optimize modular structure to avoid repeated design and waste. Establish a complete design library and module reuse mechanism to improve design efficiency. Use automated testing and production equipment to improve production efficiency and product consistency.
Applicability analysis in different application fields
As a solution with flexible structure and conducive to rapid development and maintenance, modular PCB design has shown wide applicability in many industries. It is particularly prominent in industries with strong technicality, fast-changing demand and short product cycles. This section will analyze in detail its application performance in typical fields such as consumer electronics, medical equipment, industrial control, automotive electronics and communication equipment to help readers better understand its commercial value and actual implementation methods.
Consumer electronics field
Consumer electronic products are updated and iterated very quickly, and modular PCB design can effectively improve design efficiency and shorten development cycles. For example:
Smartphones, wearable devices: These products are usually composed of multiple functional modules, such as processor modules, power management modules, sensor modules, etc. Using modular design, one of the modules can be optimized separately without affecting the overall structure, so as to quickly respond to market demand.
Smart home devices: such as smart speakers, sweeping robots, etc., are also very suitable for modularization. Hardware manufacturers can quickly integrate Wi-Fi, Bluetooth, infrared and other communication modules based on the core control module to cope with the expansion of different product forms.
Modularity allows these electronic products to have stronger scalability and customizability, meeting the diversified personalized needs of C-end users.
Medical equipment
The medical field has extremely high requirements for the stability and traceability of PCBs, and also needs to deal with complex structures with multiple functional modules. The advantages of modular design are reflected in the following aspects:
Improve reliability: Modules are designed and verified separately, which helps to reduce the probability of overall system errors.
Easy to repair and upgrade: If some modules are damaged or outdated, just replace the corresponding modules to minimize equipment downtime.
Adapt to diverse product needs: For example, portable blood glucose meters, remote ECG monitoring equipment, etc., can adapt to the regulations of different countries or regions by replacing communication modules (such as different requirements for EU CE certification and US FDA).
In addition, modular design can also help companies quickly respond to adjustments to the approval process when medical regulations are updated, reducing redesign costs.
Industrial control and automation equipment
Industrial automation equipment usually operates under high load, high temperature, and strong interference environments, posing dual challenges to the reliability and flexibility of PCBs. Modular design has the following advantages in such scenarios:
Rapid deployment and standardized management: Typical examples include PLC (programmable logic controller) and industrial computers, which often adopt the form of backplane + module card. This makes it easier for factories to uniformly purchase, stock and maintain functional modules.
On-site pluggable maintenance: Some I/O modules and communication modules can be replaced or expanded without stopping the machine, significantly improving operation and maintenance efficiency.
Strong customization capability: Modularization allows the control system to freely combine functional modules such as sensors, relays, and displays according to the automation requirements of different production lines.
Once a common baseboard specification is established for such systems, subsequent functional iterations and product differentiation development will become efficient and low-cost.
Automotive electronic system
With the rapid development of new energy vehicles and intelligent connected vehicles, the proportion of PCB in the electronic architecture of the whole vehicle has increased significantly, and modular design has also become one of the mainstream trends.
The electrical architecture of the whole vehicle is gradually modularized: the traditional wiring harness + distributed ECU mode is gradually replaced by the “central gateway controller + functional area module”, and each module is connected through a standard high-speed protocol (such as CAN FD, Ethernet). This architecture allows PCB boards to be designed and tested separately as modules, improving design flexibility and fault tolerance.
Improve system redundancy: For example, radar modules, camera modules, power distribution modules, etc. in autonomous driving systems can be developed and upgraded separately.
Meet the differentiated needs of the pre-installed and aftermarket markets: Automakers can customize models with different configuration levels by replacing or expanding different modules, such as the hardware common base design of standard ADAS and high-end L3 autonomous driving systems.
The application of modularization in automotive electronics helps to improve the evolution of the vehicle’s electronic architecture, reduce the cost of design errors, and provide a technical foundation for future OTA (remote upgrades).
Communication equipment and network facilities
Communication industry equipment usually has extremely high data processing requirements and complex communication interfaces. Modular design is very common in products such as base stations, routers, and switches.
Separate design of high-bandwidth and high-speed interfaces: For example, the transceiver module, main control module, filter module, and power amplifier module in a 5G base station are wired separately to reduce crosstalk and improve maintenance efficiency.
Flexible support for multiple communication protocols: different communication scenarios(Fiber optic, Ethernet, wireless) Protocol adaptation can be achieved by replacing modules without changing the overall baseboard architecture.
Facilitates global deployment and certification: When deploying in different countries, operators can replace localized network protocol modules based on the same main control module to meet regulatory and technical requirements.
As communication technology develops towards higher frequencies and smaller volumes, modularization will further highlight its ability to streamline design and reduce production costs.
Summary
The core advantage of Modular PCB Design lies in its “modular thinking” that subverts the traditional board-level design logic, making the design, testing, manufacturing and maintenance processes of electronic products more efficient, flexible and sustainable.
Whether you are an engineering technician, foreign trade procurement, or an industry novice, understanding and applying the concept of modularization is an important step towards high-quality products, rapid iteration capabilities, and global market competitiveness.
In the current environment of pursuing multi-functional small volume, high frequency and high speed, rapid delivery, and sustainable development, modular PCB is not only a trend, but also an active grasp of the future.