In modern materials science, pre-impregnated glass fiber, as an important composite material, is widely applied in various fields. Whether in aerospace, the automotive industry, or electronic products, glass fiber materials play an irreplaceable role. Among them, pre-impregnated glass fiber, due to its excellent performance and flexible applications, has become a key direction in current composite materials technology.
This article will delve into the basic concepts, production processes, application fields, and future development trends of pre-impregnated glass fiber, helping readers gain a comprehensive understanding of the characteristics and potential of this material.
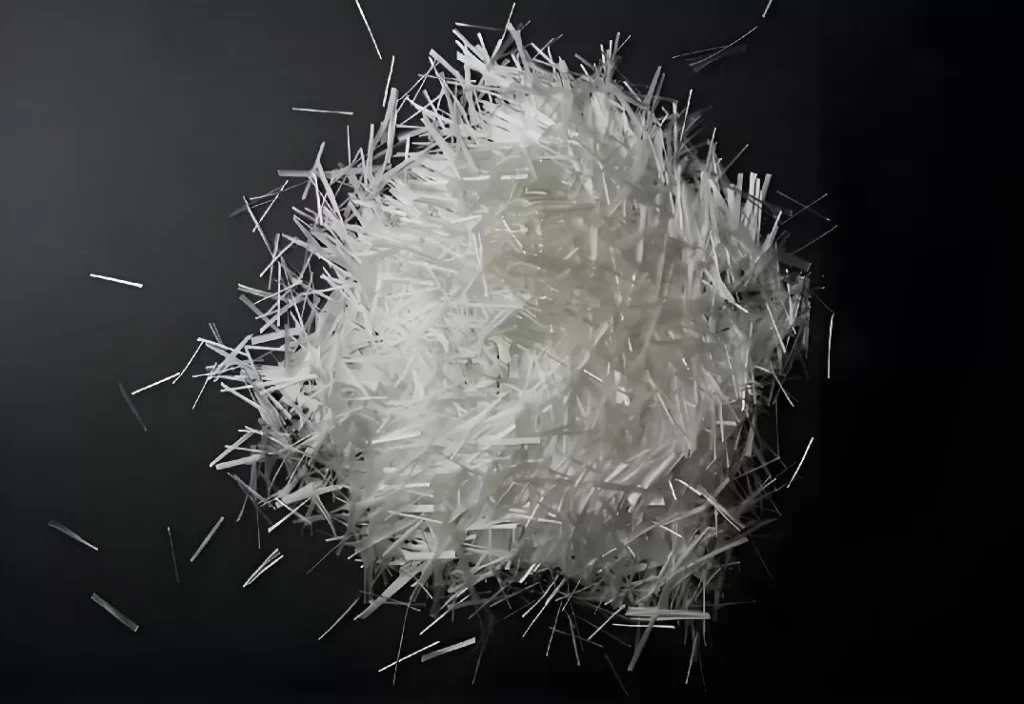
Basic Concepts of Prepreg Fiberglass
Pre-impregnated glass fiber refers to glass fibers that are pre-impregnated with resin through a specific process, so the glass fibers are already combined with a certain proportion of resin before use. This material is commonly used in the production of high-performance composite materials, particularly in applications where high strength, toughness, and high-temperature resistance are required.
The manufacturing process of pre-impregnated glass fiber mainly includes steps such as weaving the glass fiber, impregnating it with resin, curing, and molding. First, suitable glass fibers are selected, typically unwoven rovings, fabrics, or mat-like fiber materials. Next, these glass fibers are impregnated with resin, which can be selected based on the requirements, such as epoxy resin, polyester resin, etc. After resin impregnation, the glass fibers are dried and cured to form composite materials with good strength and operability.
Production Process of Pre-impregnated Glass Fiber
Selection of Glass Fiber When producing pre-impregnated glass fiber, the first step is to choose the appropriate glass fiber material. Common types of glass fiber include unwoven rovings, glass fiber fabrics, and glass fiber mats. The choice of these materials is closely related to the performance requirements of the final product.
Unwoven rovings are typically used in applications requiring high strength and high rigidity. Glass fiber fabrics are more suitable for scenarios where flexibility and strength balance is needed, often found in the automotive and aerospace industries. Glass fiber mats, with better fillability, are used in applications requiring low weight and good heat resistance in composite materials.
Resin Impregnation After selecting the glass fiber, the next step is the resin impregnation process. The choice of resin is crucial to the performance of pre-impregnated glass fiber. Common resins include epoxy resin, polyester resin, and phenolic resin, each with distinct properties.
Epoxy resin is widely used in aerospace and electronics due to its excellent bonding strength, chemical resistance, and heat resistance. Polyester resin, being cost-effective with good mechanical properties, is commonly used in industries such as automotive and shipbuilding.
During the resin impregnation process, the glass fiber is immersed in the resin solution to ensure even distribution of the resin, ensuring that every fiber is fully impregnated. This process significantly impacts the final quality of the material and requires precise operation.
Curing and Molding The glass fiber material, once impregnated with resin, must be dried and cured to ensure the molecular structure of the resin is fully cross-linked, thereby enhancing the material’s performance. The control of temperature and time during curing is critical, as both excessive and insufficient curing can affect the mechanical properties and stability of the material.
After curing, pre-impregnated glass fiber can undergo various forms of molding treatments. Depending on the final product’s shape, further processes such as stretching, cutting, or pressing may be required to meet different application needs.
Application Fields of Pre-impregnated Glass Fiber
Aerospace Pre-impregnated glass fiber is widely used in aerospace. Because the structural requirements for aerospace vehicles are very high, particularly in terms of weight, strength, and high-temperature resistance, the use of pre-impregnated glass fiber significantly enhances material performance.
In parts of airplanes such as wings, tail fins, and fuselages, pre-impregnated glass fiber composite materials are used to replace traditional metals, reducing the weight of the aircraft while increasing strength and durability. Additionally, glass fiber composites also play an important role in the manufacturing of satellites and rockets.
Automotive Industry The demand for pre-impregnated glass fiber in the automotive industry is also increasing. With the growing environmental regulations and consumers’ focus on lightweight and fuel efficiency, car manufacturers are increasingly turning to composite materials to replace traditional metals.
The use of pre-impregnated glass fiber allows cars to reduce body weight while ensuring strength and safety, thus improving fuel efficiency. This application is particularly widespread in high-performance vehicles and racing cars.
Electronics In electronics manufacturing, pre-impregnated glass fiber is commonly used in the production of circuit boards, especially for electronic devices that require high strength and high-temperature resistance. Pre-impregnated glass fiber can significantly enhance the performance of circuit boards.
For example, in the production of computer motherboards and smartphone PCBs, pre-impregnated glass fiber is widely applied. By precisely controlling the resin-to-glass fiber ratio, the conductivity, strength, and durability of the circuit boards can be optimized to meet the high-performance requirements of electronic products.
Sports Equipment Pre-impregnated glass fiber is also widely used in the manufacturing of various sports equipment, such as golf clubs, skis, and rowing boats. These materials are often used to improve the strength and durability of equipment while reducing weight, thus enhancing the user experience for athletes.
Advantages and Future Prospects of prepreg fiberglass
- High Strength and Lightweight: Pre-impregnated glass fiber offers an excellent strength-to-weight ratio, ensuring high strength while reducing material weight.
- Good Heat Resistance: The combination of resin and glass fiber provides the material with excellent high-temperature resistance, making it suitable for use in high-temperature environments.
- Good Processability: Pre-impregnated glass fiber is easy to process and can be molded into different shapes according to needs.
- Corrosion Resistance: Compared to metal materials, pre-impregnated glass fiber has superior corrosion resistance, especially in complex environments.
Future Prospects With technological advancements and the continuous development of materials technology, the application prospects for pre-impregnated glass fiber are very broad. It will continue to play an essential role in aerospace, automotive, and electronics industries.
At the same time, with ongoing improvements in production technology, the cost of pre-impregnated glass fiber is expected to decrease further, creating more opportunities for its widespread application.
Technical Challenges and Innovation Directions for prepreg fiberglass
Although pre-impregnated glass fiber is widely used in various industries and offers numerous advantages, it faces some technical challenges in the production process. Many technological innovations are ongoing to enhance its performance, reduce production costs, and expand new application fields. Below, we will explore these technical challenges and future innovation directions.
Material and Performance Optimization With the continuous upgrading of industrial demands, the performance requirements for pre-impregnated glass fiber are becoming increasingly higher. For example, in aerospace, the requirements for composite materials’ strength, toughness, and heat resistance are extremely strict. To meet these requirements, researchers are constantly optimizing the ratio of glass fiber to resin, process parameters, and material selection.
Simultaneously, functionalizing pre-impregnated glass fiber has become an important direction for future development. In the electronics field, demands such as conductivity, radiation resistance, and thermal management are gradually emerging, and more functional pre-impregnated glass fiber materials may be developed for future use.
Cost Control and Production Efficiency Improvement Although pre-impregnated glass fiber has obvious performance advantages, its production cost is relatively high, especially in high-end fields such as aerospace and automotive. The production process and raw material selection require advanced technical expertise, which results in high product costs. Therefore, reducing the production cost of pre-impregnated glass fiber and improving production efficiency are key focuses of current research.
To reduce costs, researchers are attempting to improve resin impregnation processes, develop new low-cost resins, and optimize composite material molding processes to achieve cost-effective production of pre-impregnated glass fiber. Additionally, emerging automation technologies, such as robotics and intelligent control systems, are providing new opportunities to improve production efficiency and reduce costs.
Sustainability and Environmental Issues With increasing global attention to environmental and sustainability issues, the recyclability and environmental impact of pre-impregnated glass fiber have become key areas of research. Traditional glass fiber and resin materials are difficult to recycle, creating challenges in waste disposal.
To address this, researchers are exploring more eco-friendly resin materials, such as bio-based resins and recyclable resin systems. At the same time, recycling technologies for pre-impregnated glass fiber are gradually developing, and more efficient and environmentally friendly recycling processes may be achieved in the future.
Green Manufacturing Technologies Green manufacturing technologies for pre-impregnated glass fiber are another hot topic in the industry’s development. With increasing concerns about the environmental impact of the manufacturing process, more companies are focusing on reducing energy consumption and waste emissions during production. The development of new green manufacturing technologies, such as low-energy curing techniques, eco-friendly resins, and waste recycling, will lay the foundation for sustainable production and application.
Future Application Prospects of Pre-impregnated Glass Fiber
Electronics and Information Technology With the rapid development of emerging technologies such as 5G communication, the Internet of Things, and artificial intelligence, the demand for electronic devices with high performance is increasing. This includes requirements for lightweight, strength, and temperature resistance, which are core advantages of pre-impregnated glass fiber. The future applications of pre-impregnated glass fiber in electronics and information technology will continue to grow.
Advanced Manufacturing and Smart Materials The continuous advancement of advanced manufacturing technologies and smart materials is also providing new opportunities for pre-impregnated glass fiber. In areas such as 3D printing and additive manufacturing, pre-impregnated glass fiber can be used to create high-performance custom components, achieving more precise and personalized applications.
Transportation and Robotics With the development of the transportation industry and intelligent robotics, the need for high-performance materials with light weight, high strength, and high durability is also growing. Pre-impregnated glass fiber will play a key role in the development of the next generation of transportation and robotic systems, helping them achieve greater performance and efficiency.
Conclusion
Pre-impregnated glass fiber is a promising material in various high-tech fields. As an indispensable material in modern manufacturing, it possesses outstanding performance advantages such as high strength, heat resistance, corrosion resistance, and low weight. However, due to challenges in cost, production efficiency, and environmental concerns, its wide application still faces some hurdles.
With the continuous advancement of material technology, the cost of pre-impregnated glass fiber will continue to decrease, and its applications will expand. The future direction of innovation will focus on optimizing material performance, improving production efficiency, developing more sustainable manufacturing technologies, and meeting the growing demand for high-performance materials in emerging industries.
In conclusion, pre-impregnated glass fiber will continue to play a critical role in the development of composite materials and will provide more solutions for various industries as technology and innovation continue to advance.