Materials Used in PCB 3D Printing
Conductive Inks: These are crucial for forming the electrical pathways on a PCB. Silver nanoparticle inks, copper-based inks, and conductive polymers are commonly used. Each has unique properties affecting conductivity, printability, and cost.
Dielectric Materials: These are insulating materials used for the substrate and layers separating conductive traces. Common choices include photopolymers, resins, and ceramics, selected based on their electrical insulating properties and mechanical strength.
Solder Masks and Surface Finishes: Solder masks protect the conductive traces and prevent short circuits during soldering. Surface finishes like HASL (Hot Air Solder Leveling), ENIG (Electroless Nickel Immersion Gold), and OSP (Organic Solderability Preservatives) are applied to improve solderability and protect exposed copper.
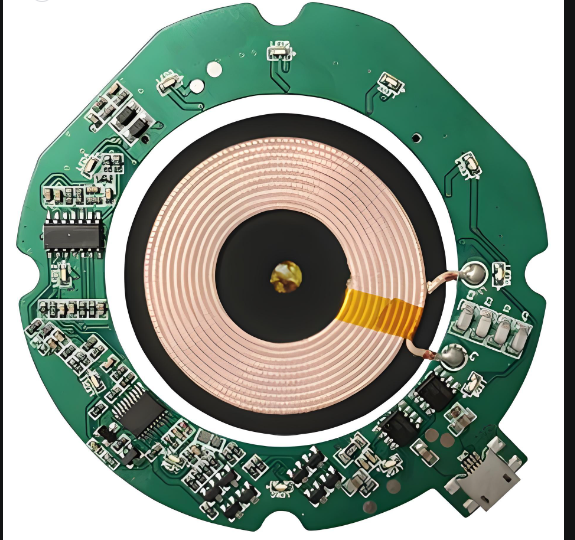
PCB 3D Printer Techniques
Inkjet Printing: This method deposits tiny droplets of conductive ink onto the substrate. It’s highly precise and suitable for fine-pitch components but requires careful control of ink viscosity and droplet size.
Aerosol Jet Printing: This technique sprays a fine mist of conductive ink, allowing for high-resolution patterns and the ability to print on 3D surfaces. It’s useful for creating complex and dense PCB designs.
Direct Laser Writing: This method uses a laser to directly write the circuit pattern onto a photosensitive substrate, which is then developed and etched. It offers high precision and is suitable for prototyping and low-volume production.
Fused Deposition Modeling (FDM): Although primarily used for structural parts, FDM can be adapted for PCB printing by using conductive filament. However, it lacks the resolution and precision of other methods.
Layer-by-Layer Construction
Substrate Layer: The process begins with printing the base layer, usually an insulating material. This forms the structural foundation of the PCB.
Conductive Traces: Conductive material is printed to form the electrical pathways. Multiple passes may be required to achieve the desired thickness and conductivity.
Vias and Through-Holes: For multi-layer PCBs, vias and through-holes are created to connect different layers. This can be done by printing conductive ink inside pre-drilled holes or by printing and curing layers sequentially.
Top Layers and Solder Mask: Once the conductive layers are printed and cured, additional insulating layers and the solder mask are applied. This protects the circuitry and prepares the board for component assembly.
Applications of PCB 3D Printing
Prototyping and Small Batch Production: The ability to quickly produce prototype PCBs allows designers to test and iterate their designs rapidly. This accelerates development cycles and reduces time-to-market.
Customized Electronics: 3D printing enables the production of highly customized PCBs, which is valuable in applications like wearable technology, medical implants, and bespoke consumer electronics.
Research and Development: Universities and research institutions use PCB 3D printers to explore new materials, circuit designs, and electronic applications. This fosters innovation and experimentation.
Educational Tools: PCB 3D printers are increasingly used in educational settings to teach students about electronics design, manufacturing processes, and hands-on prototyping.
Advanced Manufacturing: In aerospace, defense, and high-performance computing, PCB 3D printing allows for the creation of lightweight, high-density, and high-performance circuits that traditional methods struggle to produce.
Future Prospects of PCB 3D Printing
Material Innovations: Researchers are continually developing new conductive and insulating materials that improve the electrical and mechanical properties of 3D printed PCBs. These innovations will expand the range of applications and enhance performance.
Resolution and Precision Improvements: Advances in printing technology, such as finer print heads and more accurate positioning systems, will enable higher resolution and more precise PCB patterns, supporting more complex and miniaturized designs.
Hybrid Manufacturing: Combining PCB 3D printer with traditional PCB manufacturing techniques can leverage the strengths of both methods. For example, printed layers can be combined with etched copper layers to create hybrid PCBs with improved performance and reliability.
Automation and Integration: Increased automation and better integration with other manufacturing processes will streamline the production of 3D printed PCBs, making the process more efficient and cost-effective for larger-scale production.
Standardization and Quality Control: Developing industry standards for materials, processes, and quality control will ensure consistency and reliability in 3D printed PCBs. This will build confidence among manufacturers and encourage broader adoption.
Conclusion
PCB 3D printing is a transformative technology that holds significant promise for the electronics manufacturing industry. By enabling rapid prototyping, customization, and reducing waste, it offers a compelling alternative to traditional PCB manufacturing methods. Although challenges such as material properties, precision, and scalability need to be addressed, ongoing advancements and innovations are poised to overcome these hurdles.
As PCB 3D printing technology matures, it is expected to become an integral part of the electronics manufacturing landscape, driving innovation and efficiency in the development of electronic devices. For engineers, designers, and manufacturers, staying updated with these developments will be crucial in leveraging the benefits of this cutting-edge technology.
By understanding the intricacies of PCB 3D printing, we can appreciate its potential to revolutionize the way electronic circuits are designed, prototyped, and produced, heralding a new era of innovation in the electronics industry.