In the rapidly evolving field of electronics, the advent of 3D printed circuit boards (PCBs) represents a significant technological advancement. Traditional PCB manufacturing, involving multiple complex and costly steps, has long dominated the industry. However, 3D printing technology is now poised to revolutionize this process, offering numerous benefits including increased design flexibility, reduced production times, and lower costs. This article explores the impact of 3D printed PCBs on the electronics industry, discussing their development, applications, and future potential.、
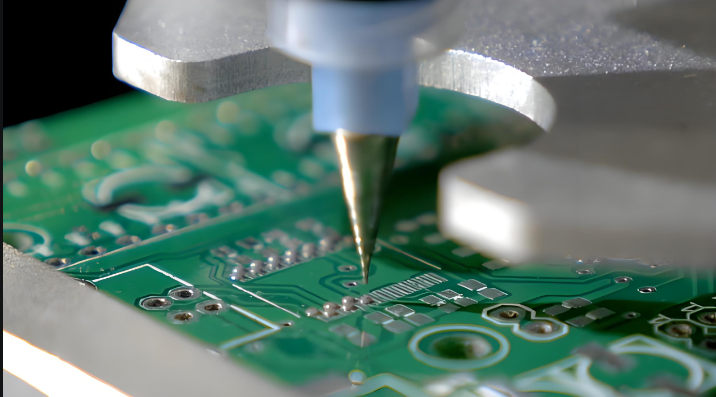
Development of 3D Printed Circuit Boards
The journey towards 3D printed PCBs began with the evolution of 3D printing technology, also known as additive manufacturing. Initially, 3D printing was primarily used for creating prototypes and simple components. However, advancements in materials and printing techniques have expanded its applications to more complex and functional items, including PCBs.
The traditional PCB manufacturing process involves several stages: designing the circuit, creating a mask, etching the copper-clad board, drilling holes, and soldering components. Each step requires precision and is susceptible to errors, leading to increased costs and longer production times. In contrast, 3D printing streamlines this process by directly building the PCB layer by layer from a digital design. This eliminates the need for masks, etching, and drilling, significantly reducing both time and cost.
Early attempts at 3D printed PCBs were limited by the materials available and the precision of the printers. However, recent innovations have addressed these limitations. Conductive inks and advanced polymers now enable the printing of intricate circuits with excellent electrical properties. High-resolution 3D printers can produce detailed and precise components, making 3D printed PCBs viable for a wide range of applications.
Applications of 3D Printed PCBs
The flexibility and efficiency of 3D printed PCBs make them suitable for various applications across different industries. One of the most significant advantages is the ability to create custom and complex designs that would be difficult or impossible with traditional methods. This has opened up new possibilities in fields such as medical devices, aerospace, automotive, and consumer electronics.
In the medical field, 3D printed circuit board enable the creation of highly customized implants and diagnostic devices. These devices often require unique shapes and specific functionalities that traditional PCBs cannot provide. For instance, wearable health monitors with flexible circuits can be printed to conform to the body, providing real-time data with greater comfort for the patient.
The aerospace industry also benefits from the weight and space savings offered by 3D printed PCBs. Complex and lightweight circuit boards can be integrated into spacecraft and satellites, improving their performance and reducing launch costs. Additionally, the ability to rapidly produce and test prototypes accelerates the development of new aerospace technologies.
In the automotive sector, the integration of 3D printed PCBs can enhance the functionality and design of electronic systems. Customizable circuit boards allow for more efficient use of space within vehicles, leading to innovations in areas such as electric vehicles, autonomous driving systems, and advanced infotainment systems.
Consumer electronics is another area where 3D printed PCBs are making an impact. The demand for smaller, more powerful, and aesthetically pleasing devices drives the need for innovative PCB designs. 3D printing allows manufacturers to create intricate and compact circuits, resulting in sleeker and more efficient products. Additionally, the rapid prototyping capabilities of 3D printing enable faster iteration and development of new consumer electronics.
Future Potential of 3D Printed PCBs
As 3D printing technology continues to advance, the potential applications and benefits of 3D printed PCBs will only expand. One of the most promising areas is the integration of embedded components within the printed circuit boards. This means that components such as resistors, capacitors, and even microchips could be printed directly into the PCB structure, further reducing assembly time and increasing reliability.
Another exciting development is the use of multifunctional materials in 3D printed PCBs. These materials can provide additional functionalities such as thermal management, electromagnetic shielding, or even energy storage. For example, a PCB could be printed with built-in heat sinks to manage temperature more effectively, or with materials that store and release energy to power the circuit.
The rise of 3D printed PCBs also aligns with the trend towards decentralized and on-demand manufacturing. Instead of relying on large-scale factories and complex supply chains, companies could produce PCBs locally and on-demand, reducing lead times and transportation costs. This could be particularly beneficial for small and medium-sized enterprises, enabling them to compete more effectively with larger companies.
Environmental sustainability is another area where 3D printed PCBs offer advantages. Traditional PCB manufacturing generates significant waste and uses hazardous chemicals. In contrast, 3D printing is an additive process that minimizes waste, and many of the materials used can be more environmentally friendly. As sustainability becomes a more pressing concern, the adoption of 3D printed PCBs could help reduce the environmental impact of electronics manufacturing.
Challenges and Considerations
Despite the many advantages of 3D printed circuit board, there are still challenges and considerations to address. One of the main challenges is the current limitation in the range of materials available for 3D printing. While conductive inks and advanced polymers have improved, they still may not match the performance of traditional materials in certain applications. Ongoing research and development are needed to expand the range of materials and enhance their properties.
Another consideration is the precision and reliability of 3D printed PCBs. High-resolution printers are essential for creating detailed and accurate circuits, but they can be expensive and require specialized knowledge to operate. Ensuring the consistency and reliability of printed PCBs is crucial for their widespread adoption, especially in critical applications such as aerospace and medical devices.
The integration of 3D printed PCBs into existing manufacturing processes also presents challenges. Companies need to invest in new equipment and training for their workforce, which can be a significant barrier, especially for small businesses. Additionally, the standardization of 3D printed PCBs and the development of industry-wide guidelines will be necessary to ensure compatibility and quality across different applications.
Conclusion
The emergence of 3D printed PCBs marks a significant milestone in the evolution of electronics manufacturing. By offering increased design flexibility, reduced production times, and lower costs, 3D printed PCBs have the potential to transform various industries, from medical devices and aerospace to automotive and consumer electronics. As the technology continues to advance, the applications and benefits of 3D printed circuit board will expand, driving innovation and efficiency in electronics design and manufacturing.
However, challenges remain, including material limitations, precision and reliability concerns, and the need for integration into existing processes. Addressing these challenges will require ongoing research, development, and collaboration across the industry. With continued progress, 3D printed PCBs are poised to play a pivotal role in the future of electronics, offering new possibilities and solutions for the ever-evolving demands of modern technology.