In the production and maintenance of modern electronic equipment, the protection of electronic components has always been an important issue. In particular, in the face of various harsh environmental conditions, how to ensure the long-term stability and reliability of the circuit has become the focus of many engineers and designers.
As an effective technical means, “conformal coating” is playing an increasingly important role in the field of electronic manufacturing.
Conformal coating is a coating material used to protect electronic circuit boards and related components, usually made of polyurethane, epoxy resin or silicone material. This coating can effectively isolate moisture, dust, chemicals and other factors in the environment that may damage the circuit, thereby improving the reliability and service life of electronic equipment.
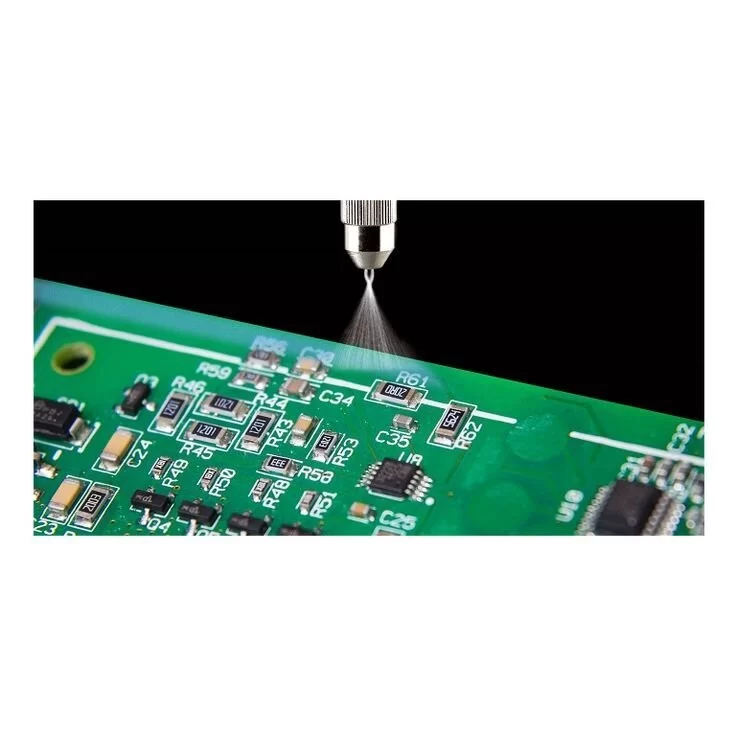
Application scenarios of conformal coating
Consumer electronics
In smartphones, tablets and wearable devices, conformal coating is widely used to protect internal circuits. These devices usually need to work in humid or dusty environments, and the coating can effectively avoid equipment failures caused by short circuits or corrosion.
Automotive electronics
With the increasing degree of automotive electronics, the reliability requirements of various sensors, control modules and infotainment systems are increasing. Conformal coating plays an important role in this field, protecting circuits from temperature changes, vibrations and chemicals, especially in engine control units and battery management systems.
Industrial control
In the field of industrial automation equipment and robots, circuit boards often need to work in harsh environmental conditions, such as high temperature, high humidity or places with corrosive gases. The use of conformal coating can significantly improve the stability and safety of the equipment.
Aerospace
Aerospace equipment needs to operate in extreme temperatures, high radiation and vacuum environments. Conformal coating can provide additional protection for these devices to ensure the normal operation of electronic systems under long-term and high-intensity conditions.
Medical equipment
Medical equipment has extremely high requirements for safety and reliability. Conformal coating can not only protect the internal circuits of the equipment, but also improve the accuracy of the equipment by reducing external interference, such as in pacemakers and MRI equipment.
Main types of conformal coating
Acrylic coating
Acrylic coating has good moisture resistance and electrical insulation, and is usually used for circuit protection with high environmental requirements. Its main advantages are simple construction and fast drying speed, but poor chemical resistance.
Polyurethane coating
Polyurethane coating has high chemical resistance and mechanical strength, and is suitable for automotive electronics and industrial equipment. However, its construction is difficult and requires special solvents for removal.
Epoxy coating
Epoxy coating has extremely high corrosion resistance and mechanical strength, and is commonly used in aerospace and military fields. However, due to its high hardness, it is not suitable for scenes that require flexibility.
Silicone coating
Silicone coating has excellent high temperature resistance and electrical insulation, and is suitable for use in scenes with large temperature changes, such as in automobiles and high-temperature industrial equipment.
Construction process of conformal coating
Spraying method
Spraying is one of the most common conformal coating construction methods, suitable for mass production scenes. The coating can be evenly covered on the surface of the circuit board through a spray gun or automated equipment.
Dip coating method
The dip coating method is suitable for circuit boards with complex shapes. The entire circuit board is immersed in the coating liquid and then slowly removed to form a uniform coating. This method has high construction efficiency, but it consumes more coating materials.
Brush coating method
For small batches or repair scenes, brush coating is an economical and practical choice. Through manual operation, specific areas can be flexibly coated, but the uniformity of the coating is poor.
Selective coating
Use precision spray equipment to only coat the areas that need protection, thereby saving materials and improving production efficiency. This method is suitable for products with high cost and quality requirements.
Conformal coating inspection methods
Visual inspection
Observe the coating surface through a magnifying glass or microscope to check for bubbles, pinholes or uneven coverage.
Fluorescent inspection
Use coating materials containing fluorescent agents to observe the integrity of the coating under ultraviolet light. This method can quickly find missing areas of the coating.
Thickness measurement
Measure the coating thickness through special equipment to ensure that it meets the design requirements. Common methods include ultrasonic measurement and dry film thickness measurement.
Environmental testing
Simulate actual working conditions such as humidity, temperature or chemical corrosion to verify the performance of the coating. For example, salt spray testing can evaluate the corrosion resistance of the coating.
Advantages of conformal coating
Improve circuit reliability
By isolating harmful substances in the environment, conformal coating can significantly reduce the risk of circuit shorts and component failures.
Extend equipment life
Coating reduces the possibility of circuit boards being attacked by moisture, dust and chemicals, thereby extending the service life of the equipment.
Improve environmental adaptability
In extreme temperature, vibration or corrosive environments, conformal coating can provide additional protection for equipment and ensure its stable operation.
Reduce maintenance costs
Due to the protective effect of the coating, the failure rate of the equipment is greatly reduced, and the maintenance cost is also reduced.
Limitations of conformal coating
Material cost
High-performance coating materials are expensive and may increase the production cost of the product.
Complex construction
The coating process requires professional equipment and technical support, especially for large-scale production.
Difficult maintenance
Once repairs are required, the coated circuit board may require additional processing steps, such as removing the coating.
The potential of conformal coating in the field of new energy vehicles
With the rapid popularization of new energy vehicles, core components such as battery management systems (BMS), inverters and motor control units have put forward higher requirements for reliability. These components need to work for a long time in high temperature, high humidity and strong electromagnetic interference environments, and conformal coating can provide the necessary protection.
For example, the battery system of new energy vehicles needs to cope with frequent charge and discharge cycles and drastic changes in external temperature. Silicone coatings are widely used in this field due to their excellent high temperature resistance and flexibility. In addition, polyurethane coatings can be used to protect electronic components in inverters from coolants or other chemicals due to their excellent chemical resistance.
In the field of intelligent connected vehicles, the performance of sensors and communication modules directly affects the safety and driving experience of the vehicle. The use of conformal coating can reduce the risk of equipment failure caused by environmental factors and provide reliable technical support for automakers.
Future development trends
Environmentally friendly materials
With the increasingly stringent environmental regulations, the research and development of coating materials with low volatile organic compounds (VOC) has become an important direction. Solvent-free or water-based coatings are gradually replacing traditional materials.
Intelligent construction
The introduction of automation and intelligent technology will improve the accuracy and efficiency of the coating process. For example, the robot coating system can achieve high-precision selective coating.
Functional integration
The new coating material not only has a protective effect, but also integrates functions such as thermal conductivity, shielding and self-repair, further improving the performance of electronic equipment.
Multi-field expansion
With the continuous development of electronic technology, the application scope of conformal coating will be further expanded to emerging fields such as new energy, Internet of Things and smart home.
Technological trends and innovative development
With the rapid development of electronic technology, conformal coating technology is also constantly innovating. In recent years, coating materials have gradually developed in the direction of being more environmentally friendly and having higher performance. For example, the research and development of low volatile organic compound (VOC) coatings has become a new direction for the industry. Traditional solvent-based coating materials release harmful gases during the application process, which pollutes the environment. In response to environmental protection policies, low-VOC coating materials, water-based coatings and solvent-free coatings have begun to emerge. These materials not only reduce the impact on the environment, but also provide higher safety and stability.
In addition, with the advancement of nanotechnology, nano coatings, as a new type of conformal coating material, have gradually been applied to high-end fields. Nano coatings have super high corrosion resistance, wear resistance and excellent insulation properties, and are particularly suitable for areas that require extremely high protection standards, such as aerospace, military and other fields. Some high-performance coatings also have self-repairing functions, which can automatically repair microcracks in the coating after physical damage, further improving the protection effect.
Intelligent construction is also a trend in the future. With the development of automation technology, the accuracy and efficiency of the coating process have been significantly improved. Intelligent coating equipment, especially spraying systems based on robot technology, can accurately selectively coat specific areas of circuit boards, reducing coating waste and production costs. At the same time, these intelligent devices can also monitor the coating process in real time to ensure precise control of coating uniformity and thickness.
Market Prospects and Industry Dynamics
As the global demand for electronic products continues to grow, the market prospects of Conformal Coating technology are very broad. Especially in the fields of consumer electronics, new energy vehicles, smart homes, etc., more and more devices need to operate in complex and harsh environments, which provides a lot of application opportunities for Conformal Coating technology. According to market research, the global Conformal Coating market is expected to continue to grow, especially in the Asia-Pacific region, thanks to the rapid development of the electronic manufacturing industry in countries such as China and India, the market demand will show an upward trend.
In the field of new energy vehicles, with the continuous innovation of battery technology, the demand for coating protection for components such as battery management systems (BMS) and motor control units is also increasing. New energy vehicles operate in high temperature, high humidity and strong electromagnetic interference environments. Conformal Coating can effectively improve the stability and service life of these electronic components. With the development of intelligent connected cars, the requirements for reliability and stability of on-board electronic systems are getting higher and higher, and Conformal Coating has great potential in this field.
Case Study
In the field of industrial control, the application of Conformal Coating helps improve the stability and anti-interference ability of equipment. For example, a world-renowned automation company applied polyurethane coating in its industrial robot control system. This coating successfully solved the problem of circuit short circuit when the equipment was working in high humidity and high temperature environment, greatly reduced the equipment failure rate, and reduced maintenance costs. In addition, for some sensitive high-precision equipment, epoxy resin coating was used. This solution effectively prevented the circuit board from being damaged in a highly corrosive environment.
In the field of aerospace, the application of Conformal Coating also provides protection for high-performance electronic equipment. For example, an airline applied silicone coating in its satellite electronic equipment. This coating has good resistance to temperature difference and electrical insulation, and can provide long-term and stable protection under extreme environmental conditions, ensuring that the equipment can operate without failure for a long time in space.
Comparison with other technologies
Conformal Coating is not the only electronic protection technology. There are other solutions on the market such as packaging technology and potting materials. However, compared with these technologies, Conformal Coating has the following advantages:
Lightness and flexibility: Conformal Coating can precisely coat every corner of the circuit board, with a wider protection range, and will not increase the volume of components like encapsulation or potting.
Adaptability: Conformal Coating can effectively adapt to environmental changes such as temperature and humidity, while other technologies may require additional protection measures.
Cost-effectiveness: The construction of Conformal Coating is relatively simple and can be completed by spraying, dipping, etc., which is suitable for large-scale production.
Summary and Outlook
Conformal Coating technology occupies a vital position in the electronics manufacturing industry. It can not only effectively improve the stability and reliability of equipment, but also extend the service life of equipment and reduce maintenance costs. With the continuous innovation of coating materials and the intelligent development of construction technology, the application prospects of Conformal Coating will become more and more extensive, especially in the fields of new energy vehicles, industrial automation and intelligent electronic devices.
In the future, with the strengthening of environmental protection regulations and the diversification of market demand, Conformal Coating will develop in the direction of environmental protection, intelligence and high performance. The research and development of new coating materials, the innovation of coating technology and the expansion of market applications will promote the further maturity and popularization of this technology. For manufacturers, fully understanding and applying Conformal Coating technology has become a key step to enhance product competitiveness and ensure long-term stable operation of equipment.
Through continuous optimization of technology and innovative applications, Conformal Coating will play a more important role in various fields of electronic products and become one of the indispensable core technologies in the future electronic manufacturing industry.