As environmental concerns continue to drive change across industries, the electronics sector is also moving toward greener and more sustainable practices. One of these initiatives is the production of halogen free PCBs (Printed Circuit Boards). These boards are designed to eliminate the use of halogen-based flame retardants, which have been linked to environmental harm and health risks. This article will delve into what halogen-free PCBs are, the benefits they offer, the challenges manufacturers face, and the industries where these PCBs are commonly applied.
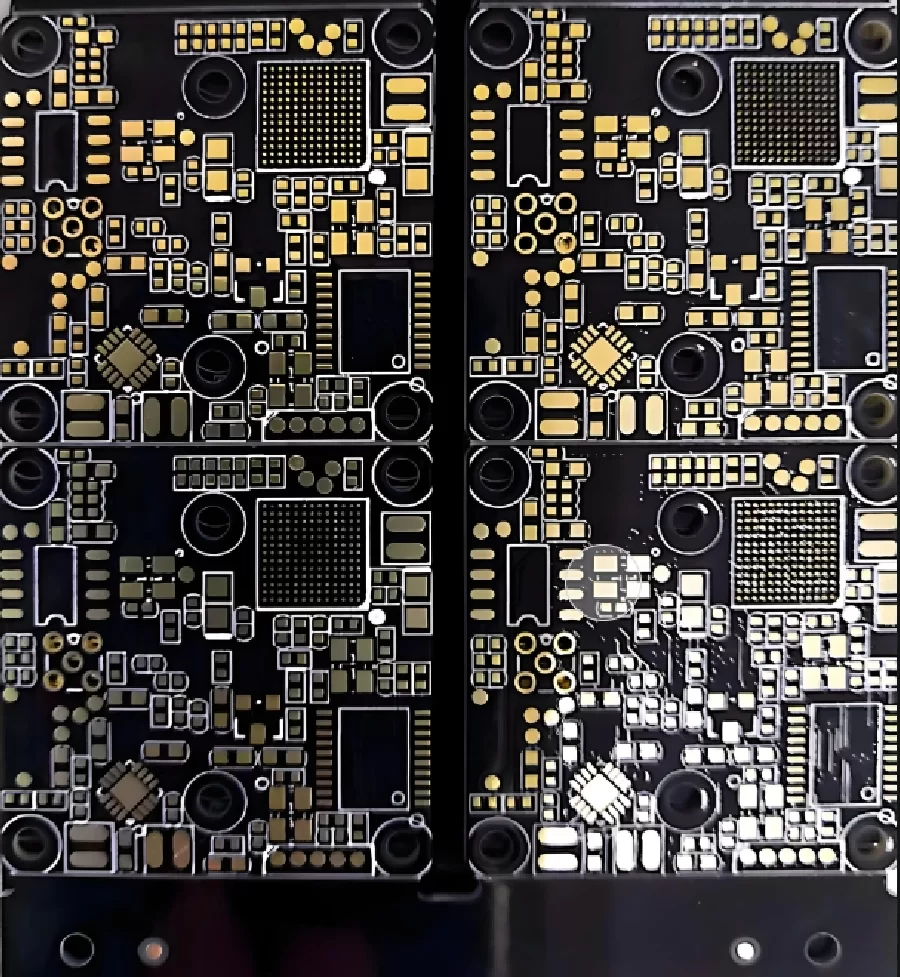
What are Halogen-Free PCBs?
Halogens such as chlorine, bromine, and fluorine are frequently used in traditional PCB flame retardants to prevent the risk of fire. While effective in suppressing fires, these chemicals release toxic compounds when incinerated, posing significant environmental and health hazards. Halogen-free PCBs avoid these substances by using alternative materials that either don’t include halogens or contain them in very low concentrations. These boards are considered halogen-free if their chlorine and bromine content is below 0.09%, and their overall halogen content remains under 0.15%, as defined by industry standards like IEC 61249-2-21.
The shift towards halogen-free PCBs is driven by both regulatory pressures and an increasing commitment by manufacturers to adopt eco-friendly practices. The goal is to minimize harmful emissions from electronic waste disposal and contribute to a more sustainable production cycle. Despite the higher costs and complex manufacturing processes associated with these boards, they are seen as a vital step toward reducing the electronics industry’s environmental footprint.
The Advantages of Halogen-Free PCBs
Environmental Benefits
One of the most prominent benefits of halogen-free PCBs is their reduced environmental impact. Traditional halogenated PCBs release dioxins and furans, which are harmful toxins that can affect both human health and the ecosystem when the boards are incinerated or disposed of improperly. In contrast, halogen-free materials are safer to handle and dispose of, reducing the environmental burden. These materials are also more compliant with strict environmental regulations like RoHS (Restriction of Hazardous Substances), which aims to limit hazardous substances in electronics production.
Halogen-free boards also contribute to the recycling process by lowering the risk of toxic emissions during the dismantling and processing of electronic waste. In an age where electronics recycling is becoming more critical, halogen-free PCBs represent a more sustainable option for manufacturers seeking to align their practices with global environmental goals.
Enhanced Thermal Performance
In addition to being environmentally friendly, halogen-free PCBs often offer better thermal stability than traditional PCBs. Most halogen-free materials come with a higher glass transition temperature (Tg), which enhances their ability to operate under high temperatures without deforming or losing structural integrity. This feature is particularly valuable in industries like automotive and aerospace, where electronics are subject to extreme temperatures and rigorous operating conditions.
The improved thermal properties of halogen-free PCBs also make them an ideal choice for applications like telecommunications infrastructure, industrial control systems, and power management systems. In these environments, electronic components need to maintain consistent performance despite fluctuating temperature conditions, and halogen-free boards offer the durability required to ensure long-term reliability.
Reduced Toxicity in Case of Fire
A significant advantage of using halogen-free PCBs is their lower toxicity when exposed to fire. Traditional PCBs containing halogens can emit corrosive and toxic gases when burned, posing serious risks to both humans and the environment. By contrast, halogen-free materials produce less smoke and fewer harmful byproducts, making them safer in applications where fire hazards are a concern.
For industries like aerospace and defense, where safety is a top priority, halogen-free PCBs provide a way to mitigate the risks associated with toxic fumes in case of fire. This safety advantage is also appealing to manufacturers of consumer electronics, particularly in devices like smartphones and laptops, where fire risks—though minimal—are still a concern.
The Challenges of Halogen-Free PCBs
Higher Production Costs
While the benefits of halogen-free PCBs are numerous, the transition to these boards isn’t without its challenges. One of the most significant obstacles is the higher production cost. The materials used in halogen-free PCBs are generally more expensive than their halogenated counterparts. In addition, manufacturers may need to invest in new equipment or modify their production processes to accommodate the unique properties of halogen-free materials, adding to the overall cost of production.
These costs can be a deterrent for some manufacturers, particularly those in cost-sensitive markets. However, as demand for halogen-free PCBs increases and economies of scale take effect, the cost is expected to decrease. In some regions, incentives and regulations are already pushing companies to adopt halogen-free technologies despite the initial cost implications.
Manufacturing and Processing Challenges
Manufacturing halogen-free PCBs can present a variety of challenges. For one, halogen-free materials often require higher processing temperatures during production, which may necessitate changes in the PCB manufacturing process. The lamination and soldering steps, in particular, need to be carefully controlled to ensure that the materials do not degrade or delaminate under these higher temperatures.
Additionally, the properties of halogen-free materials differ from those of traditional PCBs in terms of their electrical characteristics. This can impact the performance of the PCB in specific applications, particularly those involving high-frequency signals, such as telecommunications and data processing. Manufacturers must take these differences into account during the design phase, often adjusting the layout and choosing components that can work effectively with halogen-free materials.
Trade-offs in Electrical Properties
While halogen-free PCBs excel in thermal performance and safety, they can have drawbacks in terms of their electrical characteristics. For example, halogen-free materials typically have a higher dielectric constant, which can affect the transmission of high-frequency signals. In industries like telecommunications, where signal integrity is crucial, designers must carefully balance the thermal benefits of halogen-free boards with the need for stable electrical performance.
This trade-off may require manufacturers to optimize PCB designs for specific applications, choosing materials and layouts that mitigate any potential loss in signal quality. Despite these challenges, many manufacturers have successfully integrated halogen-free PCBs into their product lines by leveraging advances in materials science and design.
Applications of Halogen-Free PCBs
Consumer Electronics
In the consumer electronics industry, there is growing awareness of environmental issues and a corresponding demand for eco-friendly products. As a result, halogen-free PCBs are becoming more common in devices like smartphones, tablets, laptops, and wearable technology. Companies like Apple and Samsung have made significant strides in reducing the environmental impact of their products by transitioning to halogen-free materials.
Halogen-free PCBs are particularly well-suited to consumer electronics because they offer a combination of environmental safety, thermal stability, and electrical performance. This makes them an ideal choice for modern devices that need to balance power, speed, and environmental responsibility.
Automotive Electronics
The automotive industry is another area where halogen-free PCBs are gaining traction. As vehicles become increasingly reliant on electronic systems for functions like engine control, infotainment, and safety features, the demand for durable, high-performance PCBs has grown. Halogen-free boards provide the thermal stability and safety required in the automotive environment, particularly in electric vehicles (EVs) and hybrid systems, which generate significant amounts of heat.
Additionally, many automakers are aligning their supply chains with sustainability goals, making halogen-free PCBs a natural choice for companies looking to reduce their environmental impact while maintaining high performance.
Telecommunications and Data Centers
In the telecommunications and data center industries, halogen-free PCBs are increasingly being used in network infrastructure and data processing systems. These environments require PCBs that can handle high-frequency signals and operate reliably under continuous use. While halogen-free materials may pose some challenges in terms of signal transmission, their superior thermal stability and reduced fire risks make them an attractive option for telecom applications.
Data centers, which generate significant amounts of heat, can particularly benefit from the improved thermal properties of halogen-free PCBs. With the growing demand for data processing and cloud services, the need for reliable, durable PCBs is higher than ever, and halogen-free options provide a safe and sustainable solution.
Aerospace and Defense
In aerospace and defense applications, where safety and reliability are paramount, halogen-free PCBs offer several key advantages. Their reduced toxicity in the event of a fire, combined with their enhanced thermal performance, makes them ideal for use in high-risk environments such as aircraft systems and military communication devices. The aerospace and defense industries are also under increasing pressure to adopt more sustainable practices, making halogen-free materials an attractive option.
Conclusion
In summary, halogen-free PCBs represent a critical step toward more sustainable and environmentally responsible electronics manufacturing. While they offer significant benefits, such as improved thermal performance and reduced toxicity, they also come with challenges related to cost and manufacturing complexity. As regulations tighten and consumer demand for eco-friendly products grows, halogen-free PCBs are expected to play an increasingly important role across various industries, from consumer electronics to automotive and aerospace. With ongoing advancements in materials science and manufacturing techniques, the future of halogen-free PCBs looks promising as the electronics industry continues to innovate and adapt to new environmental standards.