Buried resistors are an innovative feature of printed circuit boards (PCBs) that integrate resistive elements within the internal layers of the board itself. This advancement in PCB technology offers numerous benefits, including improved circuit performance, reduced space requirements, and enhanced reliability. This article will delve into the concept of buried resistors in PCBs, exploring their advantages, applications, and the manufacturing process involved.
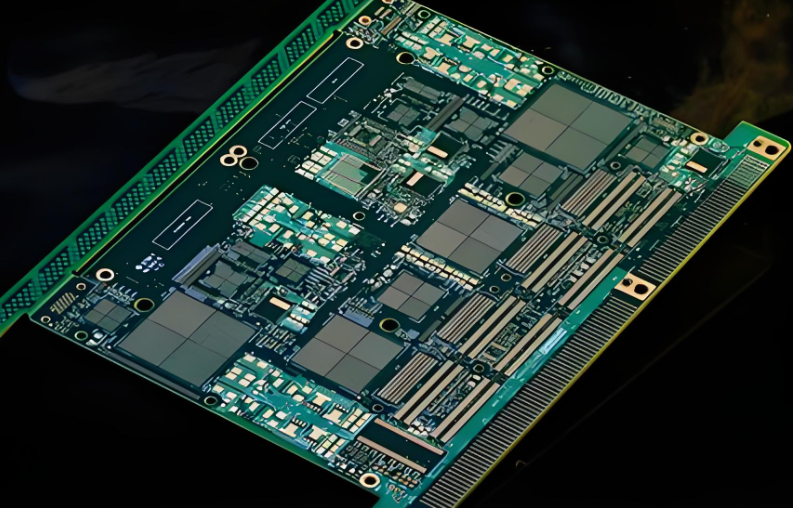
The Basics of Buried Resistors in PCBs
What Are Buried Resistors?
In traditional PCB design, resistors and other components are mounted on the surface of the board, which can consume valuable space and complicate the layout of complex circuits. Buried resistors, on the other hand, are integrated into the inner layers of the PCB. This is achieved by embedding a resistive material, such as a special ink or paste, within the layers of the PCB substrate. The resistive element is then connected to other components and traces through vias and conductive paths.
Buried resistors serve the same function as their surface-mounted counterparts by providing specific resistance values within a circuit to control the flow of current. By being integrated directly into the PCB, they allow for a more streamlined and efficient design. This is particularly advantageous in high-density circuit designs where surface space is at a premium.
How Do Buried Resistors Work?
Buried resistors function like traditional resistors, providing resistance to the flow of electric current in a circuit. They are designed to have specific resistance values and can be customized during the PCB manufacturing process to meet the exact requirements of a particular circuit. The resistive material used for buried resistors is typically a blend of conductive and insulating materials, carefully formulated to achieve the desired resistance and thermal characteristics.
The buried resistor is formed during the PCB fabrication process. A layer of resistive material is applied to a specific area of the substrate, and its resistance is precisely controlled by the thickness and width of the material, as well as its intrinsic properties. Once the resistor is formed, it is encapsulated by additional layers of the PCB, protecting it from environmental influences and mechanical stresses.
Types of Resistors in PCBs
- Surface-Mounted Resistors: Traditional resistors attached to the surface of the PCB.
- Embedded Resistors: Resistors integrated within the PCB layers but not as deeply as buried resistors.
- Buried Resistors: Resistors fully embedded within the internal layers of the PCB.
Advantages of Using Buried Resistors in PCBs
1. Space Optimization
One of the primary advantages of using buried resistors is the significant reduction in the amount of space required on the PCB surface. By embedding resistors within the layers of the board, designers can free up valuable real estate for other components, allowing for more compact and efficient designs. This is particularly beneficial for high-density circuits, where space is at a premium.
In complex electronic devices such as smartphones, tablets, and wearables, every millimeter counts. Buried resistors help achieve the necessary miniaturization without compromising functionality. This enables designers to pack more features into smaller devices, ultimately providing consumers with more powerful and versatile products.
2. Enhanced Performance
Buried resistors can lead to improved electrical performance in several ways. By eliminating the need for surface-mounted resistors, designers can reduce parasitic inductance and capacitance, leading to cleaner signal integrity and faster signal transmission. This is crucial in high-speed and high-frequency applications where signal integrity is paramount.
The absence of additional solder joints and surface connections reduces the risk of signal distortion, which can be critical in RF applications and high-speed digital circuits. The reduced parasitic effects also improve the electromagnetic compatibility (EMC) of the PCB, minimizing interference with other electronic systems.
3. Increased Reliability
Embedding resistors within the PCB can enhance the overall reliability of the circuit. Surface-mounted components are susceptible to damage from mechanical stress, temperature fluctuations, and environmental factors. Buried resistors, being shielded within the PCB layers, are less vulnerable to such external influences, leading to a longer lifespan and greater durability.
The encapsulation of resistors within the board provides additional protection against moisture, dust, and mechanical shocks. This makes buried resistors particularly suitable for harsh environments, such as automotive and aerospace applications, where electronic components are subjected to extreme conditions.
4. Thermal Management
Buried resistors can help with thermal management by dissipating heat more evenly across the board. This can reduce hotspots and improve the overall thermal performance of the PCB, which is particularly important in applications with high power or heat generation.
The integration of resistors into the PCB layers allows for better heat dissipation through the substrate, reducing the thermal stress on individual components. This contributes to improved reliability and performance, especially in power electronics and high-performance computing applications.
5. Cost Efficiency
While the initial setup and manufacturing of PCBs with buried resistors may be more complex, the potential cost savings in terms of reduced component count, smaller board size, and increased reliability can offset the initial investment. Over time, the use of buried resistors can lead to cost efficiencies in both manufacturing and maintenance.
By reducing the number of components and solder joints on the board, manufacturers can achieve lower assembly costs and reduced inspection and testing time. Additionally, the enhanced reliability and durability of buried resistors contribute to lower failure rates and maintenance costs in the long run.
Applications of Buried Resistors in PCBs
1. Consumer Electronics
In the world of consumer electronics, where devices are continually shrinking in size while increasing in functionality, buried resistors offer an ideal solution. Smartphones, tablets, wearables, and other compact devices can benefit from the space savings and enhanced performance provided by buried resistors.
The integration of buried resistors allows manufacturers to design smaller, more powerful devices with extended battery life. This is crucial in the highly competitive consumer electronics market, where consumers demand more features in ever-smaller form factors.
2. Telecommunications
Telecommunication devices and infrastructure, such as routers, switches, and base stations, require high-performance PCBs to handle large volumes of data at high speeds. Buried resistors can improve signal integrity and reduce electromagnetic interference, making them an excellent choice for these applications.
In telecommunications, maintaining signal integrity is essential for reliable data transmission. Buried resistors help minimize signal loss and distortion, ensuring that telecommunication systems operate efficiently and effectively even under heavy loads.
3. Automotive Electronics
Modern vehicles are equipped with numerous electronic systems, including advanced driver-assistance systems (ADAS), infotainment systems, and engine control units. Buried resistors contribute to the compact and reliable design of automotive PCBs, ensuring that these systems perform reliably under various conditions.
The harsh operating environment of vehicles requires robust and reliable electronic components. Buried resistors, with their enhanced durability and thermal performance, are well-suited for automotive applications, where safety and reliability are paramount.
4. Medical Devices
Medical devices demand precision and reliability. Buried resistors can enhance the performance of medical PCBs by minimizing parasitic effects and improving thermal management. This is critical for devices such as diagnostic equipment, patient monitoring systems, and implantable devices.
In medical applications, the integration of buried resistors can improve the performance and reliability of critical devices, contributing to better patient outcomes and more accurate diagnoses. The reduced footprint of buried resistors also allows for more compact and portable medical devices.
5. Aerospace and Defense
In aerospace and defense applications, where reliability and performance are critical, buried resistors offer significant advantages. PCBs in these sectors often need to withstand extreme conditions, and the embedded design of buried resistors contributes to the durability and resilience of the circuit.
The aerospace and defense industries demand high reliability and performance from electronic systems. Buried resistors provide the necessary robustness and reliability, ensuring that critical systems function effectively even in challenging environments.
Manufacturing Process for PCBs with Buried Resistors
1. Design and Simulation
The process of integrating buried resistors into a PCB begins with careful design and simulation. Engineers use specialized software to model the circuit and determine the optimal placement and values of the buried resistors. This step is crucial to ensure that the final product meets the desired performance specifications.
The design phase involves creating a detailed layout of the PCB, including the placement of buried resistors and the routing of conductive traces. Simulation tools help verify the electrical and thermal performance of the design, allowing engineers to make necessary adjustments before fabrication.
2. Material Selection
The choice of materials for buried resistors is critical to achieving the desired resistance and thermal characteristics. Common materials include resistive inks and pastes that can be precisely formulated and applied to achieve specific resistance values. The material must also be compatible with the substrate and other layers of the PCB.
Selecting the right resistive material involves balancing factors such as resistance tolerance, thermal stability, and compatibility with the PCB manufacturing process. Advances in material science continue to expand the range of options available for buried resistor applications.
3. Layer Stackup
Designing the layer stackup for a PCB with buried resistors requires careful consideration of the placement of the resistive elements within the board. Engineers must balance factors such as signal integrity, thermal management, and mechanical stability when determining the optimal layer configuration.
The layer stackup defines the arrangement of conductive and insulating layers within the PCB. Proper layer configuration is essential to achieve the desired electrical and thermal performance while minimizing crosstalk and signal degradation.
4. Deposition of Resistive Material
Once the design and materials are finalized, the resistive material is deposited onto the specified layers of the PCB substrate. This can be done using screen printing, inkjet printing, or other deposition methods, depending on the material and design requirements. The deposition process must be carefully controlled to ensure uniformity and accuracy.
The deposition process involves applying a precise layer of resistive material to the designated areas of the substrate. This step requires careful control of the deposition parameters to achieve the desired resistance values and uniformity across the board.
5. Lamination and Curing
After the resistive material is applied, the PCB layers are laminated together under heat and pressure. This step is crucial for embedding the resistive elements within the board and ensuring a solid bond between the layers. The laminated board is then cured to set the resistive material and finalize the PCB structure.
Lamination involves bonding multiple layers of the PCB together, encapsulating the buried resistors within the board. The curing process ensures that the resistive material maintains its properties and adheres securely to the substrate.
6. Drilling and Plating
Vias and holes are drilled in the PCB to connect the buried resistors to other components and layers. These vias are then plated with copper to ensure electrical conductivity. This step requires precision to avoid damaging the resistive elements and maintain the integrity of the circuit.
The drilling and plating process creates the necessary electrical connections between the buried resistors and other components on the PCB. Precision is critical to ensure that the vias are accurately positioned and properly plated for reliable conductivity.
7. Testing and Inspection
The final step in the manufacturing process is thorough testing and inspection. PCBs with buried resistors undergo electrical testing to verify the resistance values and ensure that the circuit functions as intended. Visual inspections and X-ray analysis may also be performed to detect any defects or inconsistencies.
Testing ensures that the manufactured PCB meets the required specifications and performs reliably in its intended application. Inspection methods, such as automated optical inspection (AOI) and X-ray analysis, help identify defects and ensure the quality of the finished product.
Challenges and Considerations
1. Design Complexity
Designing PCBs with buried resistors adds an additional layer of complexity to the design process. Engineers must carefully consider the placement and value of the resistive elements, as well as their impact on the overall circuit performance.
The integration of buried resistors requires a thorough understanding of the circuit’s electrical and thermal requirements. Engineers must balance trade-offs between performance, cost, and manufacturability to achieve the desired design.
2. Manufacturing Precision
The manufacturing process for PCBs with buried resistors requires high precision and control. Any variations in the deposition or lamination processes can affect the resistance values and compromise the performance of the circuit.
Achieving consistent and accurate resistance values requires precise control of the manufacturing process. Manufacturers must implement rigorous quality control measures to ensure that the finished PCBs meet the specified performance criteria.
3. Cost Implications
While buried resistors offer several advantages, they can also increase the initial cost of PCB manufacturing. The added complexity and precision required for these designs may result in higher production costs, which must be weighed against the potential benefits.
The cost implications of using buried resistors depend on factors such as the complexity of the design, the volume of production, and the specific requirements of the application. Manufacturers must carefully evaluate the cost-benefit trade-offs when considering the use of buried resistors.
4. Thermal Management
Although buried resistors can help with thermal management, they also require careful consideration of heat dissipation within the PCB. Engineers must design the board to effectively distribute and dissipate heat to avoid hotspots and ensure reliable operation.
Effective thermal management is essential to prevent overheating and ensure the long-term reliability of the PCB. Engineers must consider factors such as thermal conductivity, heat sink design, and airflow when designing PCBs with buried resistors.
Future Trends in PCB Technology
The use of buried resistors in PCB technology is expected to continue growing as electronic devices become smaller, faster, and more complex. Here are some future trends to watch for:
1. Advanced Materials
The development of new resistive materials with improved properties, such as higher thermal conductivity and better compatibility with various substrates, will enhance the performance and reliability of buried resistors in PCBs.
Advances in material science are driving the development of new resistive materials with enhanced performance characteristics. These materials offer improved resistance stability, thermal conductivity, and environmental compatibility, enabling more efficient and reliable PCB designs.
2. Increased Integration
As PCB technology advances, the integration of other passive and active components within the board layers is likely to increase. This trend towards greater integration will enable even more compact and efficient designs.
The trend towards increased integration is driven by the need for smaller, more powerful electronic devices. By integrating additional components within the PCB, designers can achieve more compact and efficient designs, reducing the overall size and complexity of electronic systems.
3. Smart and Flexible PCBs
The demand for smart and flexible PCBs is on the rise, driven by the growth of wearable electronics, IoT devices, and advanced robotics. Buried resistors will play a key role in enabling the flexible and adaptive circuits needed for these applications.
Flexible PCBs offer the ability to bend and conform to different shapes, making them ideal for applications where space and form factor are critical. The integration of buried resistors in flexible PCBs enables more versatile and adaptable designs, supporting the development of innovative new products.
4. Eco-Friendly Manufacturing
Sustainability is becoming a significant focus in PCB manufacturing. The development of eco-friendly materials and processes will reduce the environmental impact of producing PCBs with buried resistors.
The push for sustainability in electronics manufacturing is driving the development of eco-friendly materials and processes. Manufacturers are exploring new ways to reduce waste, minimize energy consumption, and use environmentally friendly materials in PCB production.
Conclusion
Buried resistors in PCBs represent a significant advancement in electronic design and manufacturing. By embedding resistive elements within the PCB layers, designers can achieve space optimization, enhanced performance, and increased reliability. These benefits make buried resistors an attractive option for a wide range of applications, from consumer electronics to aerospace and defense. As technology continues to evolve, the role of buried resistors in enabling smaller, faster, and more efficient electronic devices will only grow, paving the way for new innovations and opportunities in the world of electronics.