Printed Circuit Boards (PCBs) are fundamental components in modern electronic devices. They act as the backbone for electrical connections and play a crucial role in ensuring the functionality of electronic devices. Among the various surface finish options available for PCBs, Immersion Silver (ImAg) has gained significant popularity due to its unique properties and advantages. This comprehensive guide explores the intricacies of Immersion Silver PCBs, covering their benefits, manufacturing process, applications, and challenges.
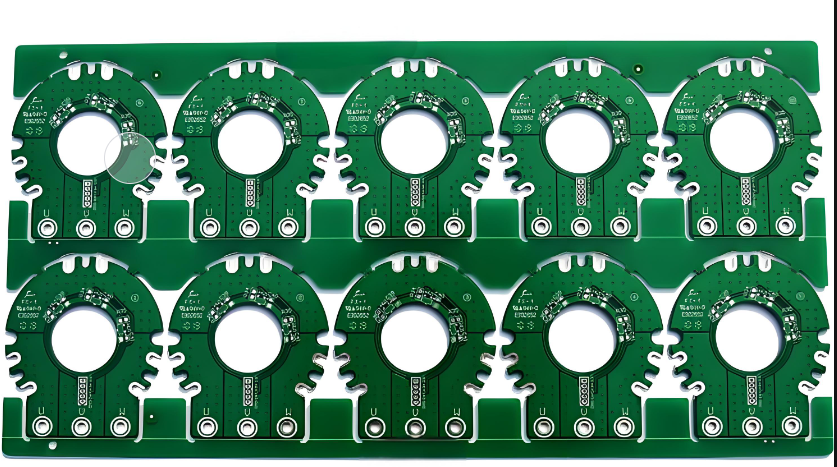
Introduction to PCB Surface Finishes
Surface finishes are applied to the copper traces on a PCB to prevent oxidation, ensure solderability, and provide a reliable connection. The choice of surface finish can significantly impact the performance, reliability, and cost of the PCB. Common surface finishes include:
- Hot Air Solder Leveling (HASL)
- Electroless Nickel Immersion Gold (ENIG)
- Immersion Tin (ImSn)
- Organic Solderability Preservatives (OSP)
- Immersion Silver (ImAg)
Each surface finish has its advantages and disadvantages, making it suitable for specific applications. Immersion Silver, in particular, has garnered attention for its excellent electrical performance and cost-effectiveness.
What is Immersion Silver (ImAg)?
Immersion Silver is a type of surface finish used in PCB manufacturing where a thin layer of silver is deposited onto the copper traces. The deposition process involves immersing the PCB in a silver solution, resulting in a uniform and highly conductive silver coating. The thickness of the silver layer typically ranges from 0.1 to 0.4 microns, ensuring a fine balance between performance and cost.
Properties of Immersion Silver
- High Conductivity: Silver is one of the most conductive metals, making ImAg an excellent choice for high-frequency applications.
- Flat Surface: ImAg provides a smooth and planar surface, which is ideal for fine-pitch components and Surface Mount Technology (SMT).
- Lead-Free: Immersion Silver is a lead-free surface finish, aligning with global environmental regulations and RoHS compliance.
- Good Solderability: The silver coating enhances solderability, ensuring reliable connections during the assembly process.
- Excellent Shelf Life: PCBs with ImAg can be stored for extended periods without significant degradation in performance.
Manufacturing Process of Immersion Silver PCBs
The manufacturing process of Immersion Silver PCBs involves several critical steps to ensure the quality and reliability of the surface finish. Here’s a detailed overview of the process:
1. Surface Preparation
Before applying the Immersion Silver finish, the PCB surface must be thoroughly cleaned to remove any contaminants, oxides, or residues. This step is crucial for ensuring proper adhesion and uniform deposition of the silver layer.
2. Micro-Etching
Micro-etching is performed to roughen the copper surface slightly, enhancing the bonding between the copper and the silver layer. This step also helps in removing any residual oxides that may have formed on the copper surface.
3. Immersion Silver Bath
The cleaned and etched PCB is then immersed in a silver bath, which contains a silver solution and various additives to control the deposition process. The silver ions in the solution are reduced and deposited onto the copper surface, forming a uniform silver layer.
4. Rinsing and Drying
After the silver deposition, the PCB is rinsed thoroughly to remove any residual chemicals from the surface. The board is then dried to prepare it for further processing or assembly.
5. Inspection and Quality Control
Quality control measures are implemented to ensure the consistency and reliability of the Immersion Silver finish. This involves visual inspection, thickness measurement, and various tests to verify solderability and electrical performance.
Advantages of Immersion Silver PCBs
Immersion Silver offers several advantages that make it a preferred choice for various applications:
1. Cost-Effective
Compared to other surface finishes like ENIG, Immersion Silver is relatively cost-effective. The lower cost of silver and the simplicity of the deposition process contribute to overall cost savings.
2. Excellent Electrical Performance
The high conductivity of silver ensures minimal signal loss, making ImAg suitable for high-frequency and high-speed applications. This is particularly important in telecommunications, data transfer, and RF (Radio Frequency) circuits.
3. Lead-Free and Environmentally Friendly
With increasing regulations on the use of hazardous substances, Immersion Silver provides an environmentally friendly and RoHS-compliant alternative. The absence of lead makes it a safer option for both manufacturers and end-users.
4. Compatibility with Fine-Pitch Components
The flat and smooth surface provided by Immersion Silver is ideal for fine-pitch components and SMT. This enhances the overall assembly process and improves the reliability of solder joints.
5. Long Shelf Life
PCBs with Immersion Silver finish can be stored for extended periods without significant degradation in performance. This is particularly beneficial for industries where components may need to be stored for long durations before assembly.
Applications of Immersion Silver PCBs
Immersion Silver PCBs find applications in various industries due to their unique properties. Some of the key applications include:
Telecommunications
In the telecommunications industry, high-frequency signals and fast data transfer rates are essential. The excellent electrical performance of Immersion Silver makes it suitable for applications like mobile communication devices, base stations, and networking equipment.
Consumer Electronics
Consumer electronics, such as smartphones, tablets, and laptops, require reliable and high-performance PCBs. Immersion Silver provides the necessary solderability and conductivity for these devices, ensuring optimal performance and durability.
Automotive Electronics
The automotive industry demands robust and reliable electronic components that can withstand harsh environments. Immersion Silver PCBs are used in various automotive applications, including engine control units (ECUs), infotainment systems, and advanced driver-assistance systems (ADAS).
Medical Devices
Medical devices require precise and reliable electronic components to ensure patient safety and accurate diagnostics. Immersion Silver PCBs are used in medical equipment like diagnostic devices, monitoring systems, and imaging equipment.
Aerospace and Defense
The aerospace and defense industries require high-reliability components that can operate in extreme conditions. Immersion Silver PCBs are used in various applications, including communication systems, navigation equipment, and avionics.
Challenges and Limitations of Immersion Silver PCBs
While Immersion Silver offers numerous advantages, it also comes with certain challenges and limitations that need to be addressed:
1. Tarnishing and Corrosion
One of the primary concerns with Immersion Silver is its susceptibility to tarnishing and corrosion. Exposure to sulfur-containing environments can lead to the formation of silver sulfide, which can degrade the performance of the PCB. Proper storage and handling are essential to mitigate this issue.
2. Handling and Storage
Immersion Silver PCBs require careful handling and storage to prevent contamination and damage. Protective packaging and controlled storage environments are necessary to maintain the integrity of the silver finish.
3. Limited Thickness
The thickness of the Immersion Silver layer is relatively thin compared to other surface finishes like ENIG. This can limit its use in certain high-stress applications where a thicker finish is required for enhanced durability.
4. Compatibility with Multiple Reflow Cycles
While Immersion Silver provides good solderability, it may not be suitable for PCBs that require multiple reflow cycles during assembly. Repeated exposure to high temperatures can degrade the silver layer, affecting the overall performance.
Best Practices for Using Immersion Silver PCBs
To maximize the benefits of Immersion Silver and ensure the reliability of the finished product, it is essential to follow best practices during the manufacturing and assembly processes:
1. Proper Cleaning and Preparation
Thorough cleaning and preparation of the PCB surface are critical to ensure proper adhesion and uniform deposition of the silver layer. This includes removing any contaminants, oxides, or residues from the surface.
2. Controlled Storage Environment
PCBs with Immersion Silver finish should be stored in a controlled environment with low humidity and minimal exposure to sulfur-containing compounds. Protective packaging and proper storage conditions can prevent tarnishing and corrosion.
3. Handling Precautions
Careful handling of Immersion Silver PCBs is essential to prevent damage and contamination. Operators should use gloves and avoid direct contact with the silver surface to maintain its integrity.
4. Regular Inspection and Testing
Implementing regular inspection and testing protocols can help identify any issues with the Immersion Silver finish early in the manufacturing process. This includes visual inspection, thickness measurement, and solderability testing.
5. Proper Assembly Process
During the assembly process, it is important to use appropriate soldering techniques and temperature profiles to ensure reliable solder joints. Avoiding excessive heat and multiple reflow cycles can help preserve the integrity of the silver layer.
Future Trends and Developments in Immersion Silver Technology
As the demand for high-performance and cost-effective PCBs continues to grow, advancements in Immersion Silver technology are expected. Some of the future trends and developments in this field include:
1. Enhanced Corrosion Resistance
Research and development efforts are focused on improving the corrosion resistance of Immersion Silver finishes. New formulations and additives are being explored to reduce tarnishing and enhance the overall durability of the silver layer.
2. Improved Deposition Techniques
Advancements in deposition techniques are aimed at achieving more uniform and consistent silver coatings. This includes optimizing the chemistry of the silver bath and developing new deposition methods to enhance the quality of the finish.
3. Integration with Advanced Materials
The integration of Immersion Silver with advanced materials, such as high-frequency laminates and flexible substrates, is being explored to meet the evolving demands of modern electronic applications. This can expand the use of Immersion Silver in emerging technologies like 5G and IoT devices.
4. Eco-Friendly Alternatives
As environmental regulations become more stringent, there is a growing focus on developing eco-friendly alternatives to traditional surface finishes. Immersion Silver, with its lead
Conclusion
Immersion Silver PCBs offer a compelling combination of excellent electrical performance, cost-effectiveness, and environmental friendliness. Their unique properties make them suitable for a wide range of applications, from telecommunications and consumer electronics to automotive and medical devices. However, to fully leverage the benefits of Immersion Silver, it is essential to address the challenges related to tarnishing, handling, and storage.
By following best practices and staying abreast of advancements in Immersion Silver technology, manufacturers can ensure the reliability and performance of their PCBs. As the electronics industry continues to evolve, Immersion Silver is expected to play a significant role in meeting the demands of next-generation electronic devices.