When designing Printed Circuit Boards (PCBs), understanding electrical impedance is crucial to ensure the reliability and performance of your electronic devices. Impedance plays a key role in the transmission of signals across a PCB, affecting everything from signal integrity to power efficiency. Whether you’re developing high-speed communication devices, consumer electronics, or industrial equipment, controlling impedance is essential to achieving optimal performance.
What is Electrical Impedance?
Impedance, in the context of PCBs, refers to the resistance that a circuit offers to the flow of alternating current (AC) signals. Unlike simple resistance, electrical impedance is a complex quantity that includes both resistance and reactance, which are associated with capacitive and inductive elements on the board. The impedance of a PCB trace determines how signals are transmitted across the board and how much signal loss occurs.
In high-speed digital and RF (radio frequency) circuits, controlling impedance is critical because any mismatch can lead to signal reflections, noise, and ultimately, poor performance of the electronic device. Impedance is measured in ohms (Ω) and is typically controlled to specific values that match the components and design requirements.
Why Electrical Impedance Control is Crucial in PCB Design?
- Signal Integrity: In high-speed circuits, signals are transmitted at very high frequencies. If the electrical impedance is not correctly matched, the signals can reflect back at junctions, causing interference and data loss. This is particularly important in applications like communication devices, where clean and undistorted signal transmission is essential.
- Power Efficiency: Impedance mismatches can cause energy to be reflected back toward the source rather than being transmitted to the load. This reflection results in power losses, reducing the efficiency of the circuit. In power-sensitive applications, this can lead to overheating and even failure of the components.
- Noise Reduction: Proper impedance control helps minimize electromagnetic interference (EMI) and crosstalk between traces on the PCB. This is especially important in densely packed boards where signals can easily interfere with one another.
- Reliability: Consistent impedance across the PCB ensures that the circuit operates as intended, reducing the risk of failures in the field. This reliability is critical for products that require long-term stability, such as medical devices and automotive electronics.
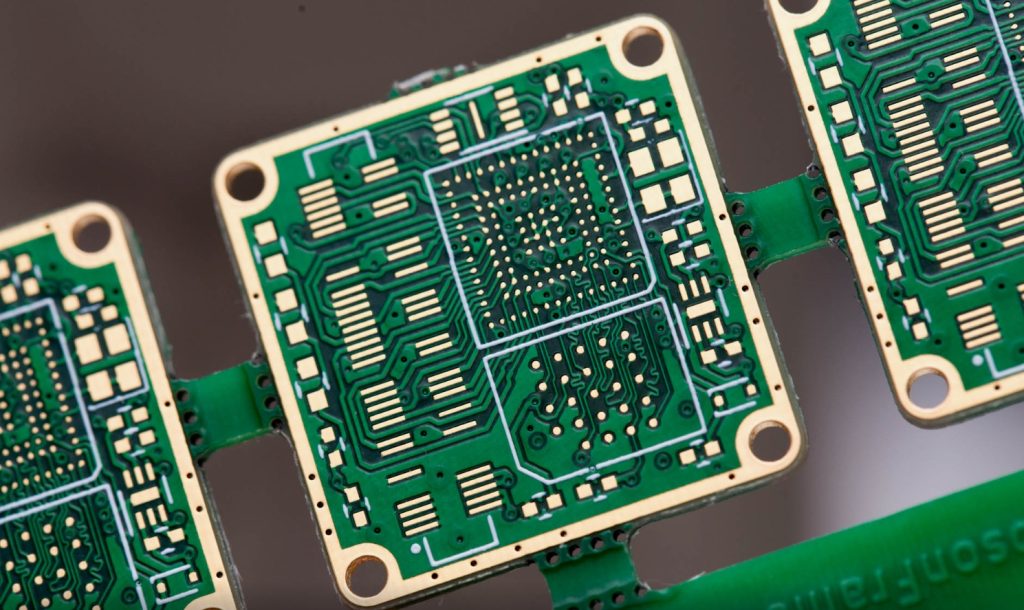
Factors Affecting Electrical Impedance in PCBs
- Trace Width and Thickness: The width and thickness of a PCB trace directly affect its impedance. Wider traces have lower electrical impedance, while narrower traces have higher impedance. The thickness of the copper layer also plays a role.
- Dielectric Material: The material used between the PCB layers, known as the dielectric, affects the capacitance of the traces, which in turn influences impedance. Different materials have different dielectric constants, which must be considered when designing for specific impedance values.
- Layer Stack-Up: The arrangement of the PCB layers (stack-up) affects the overall impedance of the traces. By carefully designing the layer stack-up, you can achieve the desired impedance while optimizing the board for other factors such as size and cost.
- Trace Spacing: The distance between adjacent traces can lead to capacitive coupling, which affects the electrical impedance. Careful control of trace spacing is essential to maintaining consistent impedance across the board.
- Environmental Factors: Temperature and humidity can affect the impedance of a PCB. Therefore, it’s important to consider the operating environment of the final product when designing the board.
How We Ensure Precise Electrical Impedance Control in Your PCB?
At our PCB manufacturing facility, we understand the importance of precise impedance control for the success of your project. Here’s how we achieve it:
- Advanced Design Tools: We use state-of-the-art software to simulate and calculate the impedance of PCB traces before production. This allows us to predict and correct potential issues in the design phase, saving you time and reducing the risk of costly revisions.
- Controlled Manufacturing Processes: Our production process includes tight control over all variables that affect impedance, including trace width, dielectric material, and layer stack-up. By maintaining these parameters within strict tolerances, we ensure that the final product meets your impedance specifications.
- Impedance Testing: We offer comprehensive impedance testing services to verify that the finished PCB meets the required impedance values. This testing includes Time Domain Reflectometry (TDR) measurements, which provide precise data on the impedance of each trace.
- Material Selection: We offer a wide range of dielectric materials with different properties to match your specific impedance requirements. Our team can help you choose the right material based on your design goals and budget.
- Expert Consultation: Our engineers are available to assist you at every stage of your project, from initial design to final production. We can provide guidance on optimizing your PCB layout for impedance control, helping you achieve the best possible performance for your product.
The Cost of Ignoring Electrical Impedance Control
Failing to properly control impedance in your PCB design can lead to a host of problems, including:
- Signal Distortion: Impedance mismatches cause signal reflections, leading to distorted waveforms that can result in data errors, especially in high-speed digital circuits.
- Increased EMI: Poor impedance control can lead to higher levels of electromagnetic interference, which can affect the performance of nearby electronics and violate regulatory standards.
- Reduced Product Lifespan: Excessive power losses due to impedance mismatches can cause components to overheat and fail prematurely, reducing the overall lifespan of the product.
- Higher Costs: Fixing impedance-related issues after production can be expensive and time-consuming. It may require redesigning the PCB, reordering materials, and conducting additional testing, all of which increase your costs and delay your time to market.
Why Choose Us for Your PCB Needs?
When it comes to PCB design and manufacturing, you need a partner who understands the intricacies of electrical impedance control and can deliver high-quality boards that meet your exact specifications. Here’s why we’re the right choice for your project:
- Experience and Expertise: With years of experience in the PCB industry, we have the knowledge and expertise to handle even the most complex electrical impedance requirements. Our team stays up-to-date with the latest technologies and industry standards to ensure your PCBs are cutting-edge.
- Customization and Flexibility: We offer fully customizable PCB solutions tailored to your specific needs. Whether you need a high-frequency PCB with controlled impedance or a multi-layer board with complex stack-up requirements, we can deliver.
- Quality Assurance: Our rigorous quality control processes ensure that every PCB we produce meets the highest standards of performance and reliability. We are committed to delivering boards that work right the first time, every time.
- Competitive Pricing: We offer competitive pricing without compromising on quality. By optimizing our processes and leveraging our industry relationships, we can provide cost-effective solutions that fit your budget.
- Fast Turnaround Times: We understand that time is of the essence in today’s fast-paced market. That’s why we offer fast turnaround times to help you get your product to market quickly.
Impedance control is a crucial aspect of PCB design, directly affecting the performance and reliability of electronic devices. Properly managed impedance ensures signal integrity, reduces noise, and enhances power efficiency, preventing issues like signal distortion and electromagnetic interference. By understanding and addressing factors like trace width, dielectric materials, and layer stack-up, designers can optimize their circuits for better performance and long-term reliability.
Incorporating electrical impedance considerations early in the design process is essential for avoiding costly revisions and ensuring the success of your electronic products. Partnering with an experienced PCB manufacturer who understands the complexities of impedance control can make all the difference, helping you achieve a high-quality, reliable product that meets your specific needs.