Flexible pcb cost plays an important role in modern electronic products. Due to their specialized materials and complex manufacturing processes, flexible circuit boards are often expensive to produce, influenced by raw materials, design complexity, and market demand.An in-depth understanding of these cost factors is essential to optimize sourcing and design strategies.
1.Raw Material Costs
The flexible PCB cost is first affected by the price of raw materials. Commonly used flexible substrates include polyimide (PI) and polyester film. Polyimide is more commonly used for its excellent thermal stability and mechanical properties,while polyester is used for cost-sensitive applications. According to market data, polyester flexible circuits use raw materials that cost about 1.5 times as much as rigid circuits,while the cost of high-performance polyimides can be four or more times higher.
The use of copper is also an important factor in material selection. The conductive layer of a flexible circuit board is usually made of copper,the thickness and quality of which directly affects the performance and cost of the circuit. High purity and thickness of copper materials usually lead to increased costs.
2.Manufacturing process costs
The process of manufacturing flexible PCBs is more complex than rigid circuit boards, involving a variety of processes and technology steps. The manufacturing process includes steps such as substrate preparation, copper lamination, patterning, cover film application, lamination, cutting and drilling. These steps require not only advanced equipment,but also stringent process controls to ensure product reliability and performance.
Common challenges in production include high precision requirements and high scrap rates. For example, complex circuit designs may require extremely small line widths and pitches, which can make the etching process more difficult and therefore more costly. In addition, the manufacture of multilayer flexible PCBs is relatively more costly as it requires more materials and process steps.
3.Design complexity
Design complexity has a significant impact on the flexible PCB cost.Complex circuit designs not only increase material and manufacturing requirements, but may also lead to higher R&D and testing costs. For example,designs that require high-density routing may require the use of more advanced PCB design software and more engineering resources, thereby increasing overall costs.
In addition, customer customization needs can also have an impact on design complexity. Demanding customers often require more stringent production standards and performance testing, which can increase a manufacturer’s workload and lead to further cost increases.
4.Customer needs and market dynamics
Customer-specific needs and market conditions are also important factors that affect the flexible PCB cost.High-end customers often require higher yields and more complex products, which can lead to manufacturers needing to invest more resources to meet these requirements. Accordingly, this can increase production costs.
Market dynamics can also affect the flexible PCB cost. For example, changes in geographic location, logistics costs and market demand can lead to price fluctuations. Labor costs and transportation costs in a particular region can also affect the final price of a flexible PCB.
5.Cost optimization strategy
In order to effectively reduce the production of flexible PCB cost,companies can adopt several optimization strategies. First, optimizing material selection by choosing cost-effective polyester substrates may reduce overall material costs. In addition, minimizing complexity at the design stage, such as reducing the number of layers and line widths, can help control production costs.
Secondly, choosing the right manufacturer is also an important factor in reducing costs.Different manufacturers differ in their technical level, production processes and equipment capabilities, and choosing a more specialized or cost effective manufacturer can significantly reduce costs. These factors should be taken into account when purchasing to ensure that the best product quality and price levels are obtained.
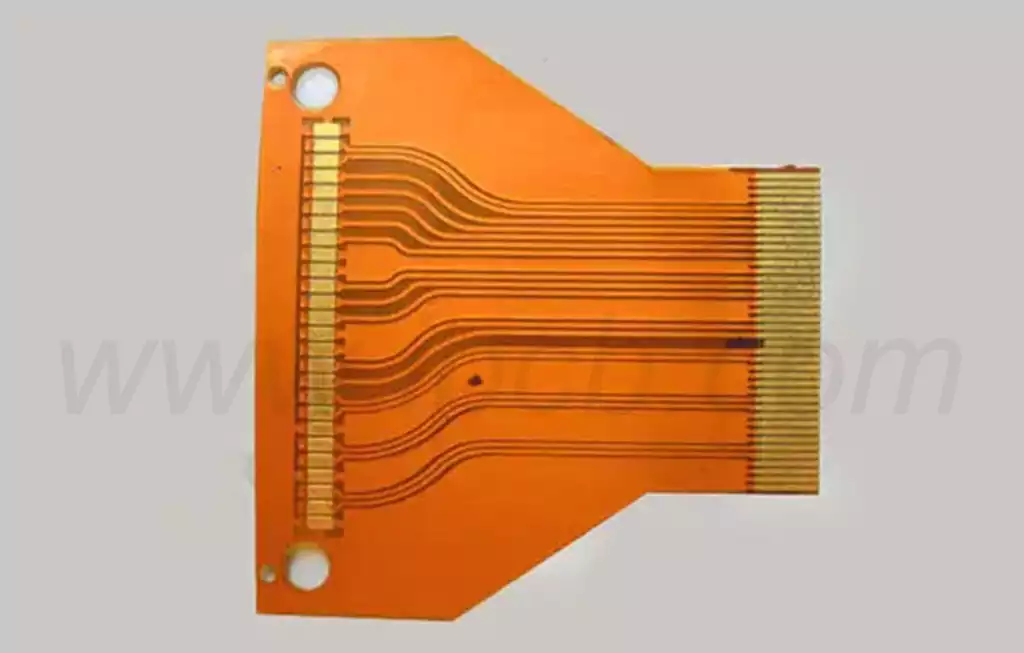
In the production of flexible PCBs, effective cost control methods:
- Optimize material selection
Material cost is an important part of flexible PCB cost structure. Choosing the right base material can significantly reduce costs. For example, choosing lower-cost polyester film instead of high-performance polyimide materials can control material costs under the premise of meeting electrical requirements. At the same time, rational selection of copper thickness and quality is also a key factor in reducing material costs. - Simplify the design process
By simplifying the circuit design process and reducing unnecessary complexity, the design and manufacturing costs of flexible PCBs can be effectively reduced. For example, reducing the number of circuit layers and avoiding the use of blind or buried holes and other complex hole types can reduce processing time and failure rate, thereby reducing overall costs. The use of simplified design software and tools in the design phase can also save time and cost. - Improve the manufacturing process
The choice of manufacturing process is equally critical to the cost control of flexible PCBs. The use of advanced manufacturing technology can improve production efficiency, reduce the scrap rate, thereby reducing the overall cost. For example, additive manufacturing processes can effectively handle complex circuit patterns, helping to improve the accuracy and efficiency of production. By continually improving manufacturing processes and techniques, companies can cut production expenses without sacrificing quality. - Implement advance planning
Establishing a clear production plan at the beginning of the design can effectively reduce the additional costs caused by modifying the design. Determining the design in advance and minimizing modifications can avoid the costs associated with multiple sampling or re-processing. Moderately increasing the production of first-time samples through reasonable purchasing strategies can also optimize costs under the condition of meeting testing requirements. - Strengthen quality management
A good quality management system is the basis for cost reduction. Strict quality control at all stages of production can reduce the increased costs due to rework. By preventing at source in the design stage, process stage and sample stage, quality problems after manufacturing can be minimized, thus reducing overall operating costs.
The structure of flexible PCB cost is influenced by a number of factors, including raw material selection, manufacturing processes, design complexity and market dynamics. In order to maintain an advantage in a competitive market, companies must adopt effective cost control strategies. By optimizing the choice of materials, simplifying the design process, improving the manufacturing process, implementing advance planning and strengthening quality management, companies can effectively reduce the production cost of flexible PCBs without reducing product quality.