Custom stencils refer to the customization of stencil products with different specifications, materials, and shapes according to the specific needs of customers. Customers can choose different materials, specifications, and shapes, as well as different mesh sizes and arrangements according to their needs. In addition, customized stencils can also be surface-treated and coated according to customers’ requirements to improve their durability and aesthetics.
How to make custom stencils
1. Material Selection
Types of steel: Choose the type of steel that suits the production requirements, such as low-carbon steel, high-carbon steel, stainless steel, and so on. Determine the material according to the use and environmental conditions.
Thickness: Determine the thickness of steel mesh according to production requirements. The thickness will affect the strength and durability of the mesh.
2. Open the mold
Make molds according to the design drawings to ensure the precision of the molds and surface finish to ensure the accuracy of the size and shape of the steel mesh.
3. Rolling
Put the steel plate into the rolling mill and roll it into shape under the action of the mold. The temperature and pressure control during the rolling process should be ensured to maintain the dimensional accuracy of the steel mesh.
4. Surface treatment
According to the requirements, the surface treatment of steel mesh, such as spraying, chromium plating, polishing, etc., improves corrosion resistance and aesthetics.
5. Precision Cutting
Use a CNC machine to cut the steel mesh precisely to ensure dimensional accuracy and edge smoothness. In this section, we need to pay attention to the selection of suitable cutting methods and knives to minimize the heat-affected area and maintain the performance of the steel mesh.
6. Assembly and Inspection
Assemble the cut steel mesh into a complete product and carry out a quality inspection. Ensure that all stencils meet the size, shape, and performance requirements.
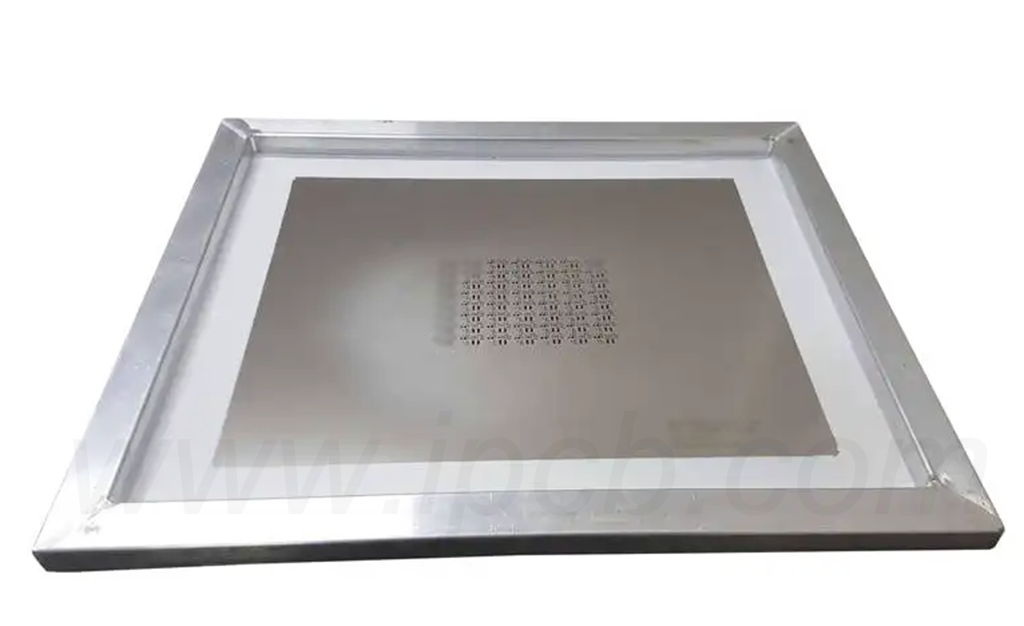
Common Custom Stencil Manufacturing Processes
The laser cutting process is one of the most common custom stencil manufacturing methods used today.This process uses a high-energy laser beam to precisely cut steel plates to create the desired mesh shape and size. This method is extremely accurate and efficient,and is capable of producing intricate patterns that are suitable for soldering high-density electronics.
The chemical etching process involves coating the steel plate with an acid-resistant adhesive and removing the adhesive layer, which causes the exposed portion of the steel plate to be attacked by acid, creating openings. This process is characterized by the ability to achieve very fine apertures and is suitable for stencil fabrication where very high soldering accuracy is required.
Electroforming is a relatively new fabrication technique that deposits metal layer by layer on a substrate by electrochemical means to form the desired mesh structure. This method is effective in increasing the strength and durability of the stencil and is suitable for process requirements for high frequency and high power electronic components.
Step stencil is mainly a process of localized thickening and thinning on a steel sheet, enabling the printing of different thicknesses of solder paste on the same stencil. The advantage of this method is that, depending on the performance of different components, different amounts of solder paste can be printed in one stencil, which enhances the flexibility and adaptability of production.
What are the factors that affect the cost of PCB layout?
1.The number of wiring layers: the more layers of the design of the wiring easier, but the price is with the number of layers straight up, the final price of the board may be doubled.
2.Vias: If not limited by device pitch or design density, use vias with a diameter of 0.25mm or greater if possible; most PCB manufacturers charge a premium for vias smaller than 0.25mm.
3.Hole-in-Plate Plugs: Do not use these except for signaling and layout and packaging constraints.
4.Back-drilled holes: Used on backplanes or single boards with high-speed signals and can add up to 10% to 20% of the cost.
5.Line widths and spacing: Usually less than 3.5 mils or less, resulting in increased costs to the manufacturer.
6.Materials: Informal materials such as high-tg, no-halogen, and high-frequency materials increase the PCB manufacturer’s lead time, which translates into increased production costs. Some high-frequency materials can be mixed with conventional materials to reduce some of the costs of production.
7.HDI and Blind Vias: This item has a significant cost increase and is best avoided if packaging permits. Tip: BGA packages with a pitch of 0.65mm and above can be fanned out through-hole, and some 0.5mm BGA packages can be fanned out through-hole depending on pad size and available pin distribution.
8.Surface work: Immersion, immersion tin, immersion silver, and metal fingers will increase the cost, of course, these items need to be specifically considered according to the type of products designed.
Custom stencils are highly personalized products that require extensive experience and expertise to produce. Choosing a high-quality customized stencil can meet the specific needs of customers and improve production efficiency and product quality.