Etching is part of the PCB manufacturing process and is used to create cutter traces on printed circuit boards. This is accomplished by removing excess copper from the copper laminate, leaving only the desired circuitry on it.
There are two types of etching: dry etching and wet etching:
Wet Etching: Wet etching uses an acid solution and dissolves the unwanted copper based on a chemical reaction. The unwanted copper is dissolved when immersed in the chemical solution. The successful realization of wet etching depends on selecting the right chemical solution and etching material.
There are two types of chemicals that can be used for wet etching:
Acidic chemicals: Iron Chloride (FeCl3) / Copper Chloride (CuCl2)
Alkaline Chemicals: The chemicals used in the alkaline etching process are Copper Chloride (CuCl2 Castle, 2H2O) + Hydrochloride + Hydrogen Peroxide (H2O2) + Water (H2O).
Dry Etching: This is also known as plasma etching, where the plasma activates a chemical reaction between the base atoms and the surface atoms of the laminate, resulting in the dissolution of unwanted copper.
The point in the etching process where all the unwanted copper is dissolved is called the “break point”.
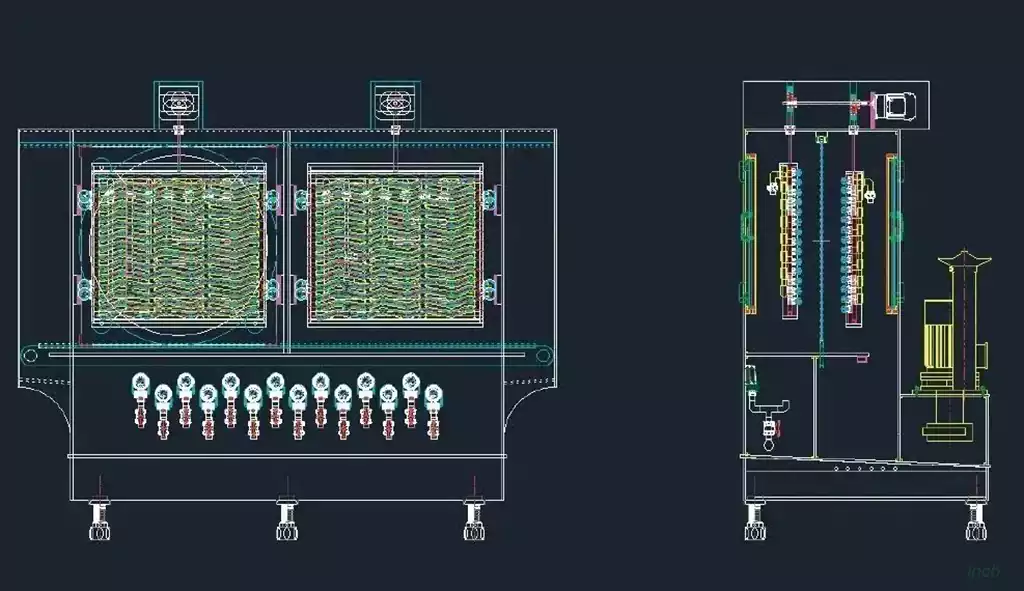
Principle of PCB Etching Process
Etching is at a certain temperature conditions (45 +5) etching solution through the spray nozzle evenly sprayed onto the surface of the copper foil, and no etching resist protection of copper redox reaction occurs, and the unwanted copper reaction off, exposing the pcb substrate and then stripped after the film treatment so that the line is formed. The main components of etching solution: copper chloride, hydrogen peroxide, hydrochloric acid, soft water (solubility has strict requirements)
PCB etching process quality requirements and control points
There can be no residual copper, especially double-sided board should be noted.
There should be no residual glue, otherwise it will cause copper exposure or poor adhesion of the plating layer.
Etching speed should be appropriate, do not allow excessive etching caused by line thinning, etching line width and the total pitch should be the focus of this site control.
The dry film on the line soldering point should not be separated or broken by washing.
After etching and stripping the film of the plate does not allow oil, impurities, copper skin warping and other poor quality.
The board should be placed to avoid jamming and prevent oxidation.
Should ensure that the etching solution distribution uniformity, to avoid the front and back or the same side of the different parts of the etching is not uniform.
PCB etching process process control parameters
Temperature of etching solution: 45+/-5℃ Solubility of hydrogen peroxide: 1.95~2.05mol/L
Temperature of film stripping solution: 55+/-5℃ Safe use temperature of etching machine≦55℃.
Drying temperature﹕75+/-5℃ Spacing between front and rear plates﹕5~10cm
Specific gravity of copper chloride solution﹕1.2~1.3g/cm3 Angle of plate release, guide plate, upper and lower nozzle switching state
Hydrochloric acid solubility: 1.9~2.05mol/L
PCB etching process quality confirmation
Line width: Etching standard line is .2mm & 0.25mm, it must be within +/-0.02mm after etching.
Surface quality: No wrinkles or scratches.
No copper residue when inspecting by light transmission.
No deformation of lines.
No oxidized water droplets
Lateral corrosion is affected by the following factors:
- Etching method: immersion and bubble etching will cause greater side corrosion, splash and spray etching side corrosion is smaller, especially spray etching the best results.
- Types of etching solution: different chemical components of different etching solution, its etching rate is different, etching coefficient is also different. For example: acidic copper chloride etching solution etching coefficient is usually
- Alkaline copper chloride etchant etching coefficient can reach 4. Recent studies have shown that the nitric acid-based etching system can be achieved almost no side corrosion, to achieve the etching of the line sidewalls close to vertical. Such etching systems are yet to be developed.
Circuit board etching is a precision art in electronic manufacturing. It provides strong support for the manufacture of electronic products with its high precision and high efficiency.