Solder paste is the core material in SMT mounting, it is a kind of material used to connect the electrode of parts and the pad of circuit board, mainly used for the welding of PCB surface resistance, capacitance, IC and other electronic components in SMT industry.
It is made of solder powder, flux and other surfactants, thixotropic agent to be mixed to form a paste mixture, it is accompanied by smt patch process and the emergence of a new type of welding materials, is to ensure the reliability of the reflow soldering process is an important factor. Flux contains different components, such as rosin, active agents, thickening agents. These substances in a long period of time under the static, because of their own gravity will lead to sinking the phenomenon of precipitation stratification, will seriously affect the role of it, so before use should be stirred, will be re-mixed into these substances to be used together. As the storage needs to be kept frozen, it will make the movement and uniformity of the solder paste affected. Therefore, it should be stirred sufficiently before printing so that the flux and tin powder are mixed evenly in order to achieve good use. The general mixing time is 1 to 4 minutes, which varies depending on the mixing method.
The classification of solder paste can be categorized in a number of ways.
- Classified according to the melting point of alloy solder, it is divided into high-temperature (above 217℃), medium-temperature (173~200℃) and low-temperature (138~173℃). The most commonly used solder paste melting point of 178 ~ 183 ℃, according to the different temperatures required for welding, choose a different melting point of it.
- According to the activity classification of the flux, it can be divided into R grade (inactive), RMA grade (medium activity), RA grade (fully active) and SRA grade (super active). Generally R grade is used for the soldering of aerospace and avionics products, RMA grade is used for military and other high reliability circuit assemblies, and RA grade and SRA grade are used for products of consumer electronics.
- Classified according to the viscosity of it. Solder paste viscosity varies greatly, usually 100 ~ 600Pa – s, up to 1000Pa – s or more, the use of paste can be based on the application of different means of technology to choose.
- According to the cleaning method classification, can be divided into organic solvent cleaning class, water cleaning class, half-water cleaning class and no cleaning class several kinds. Organic solvent cleaning class such as traditional rosin solder paste, water cleaning class is more active, half-water cleaning class and cleaning class is the direction of the development of electronic product technology.
- According to whether it contains lead to points, can be divided into leaded and lead-free solder paste, leaded and lead-free difference at a glance, in fact, the main is the difference between the amount of lead in the solder paste. In today’s environmental requirements of the majority of electronic products SMT chip processing are using lead-free process, but there are some products still need to use the leaded process, the main reason is that the leaded process is better soldering results, and the cost is also cheaper.
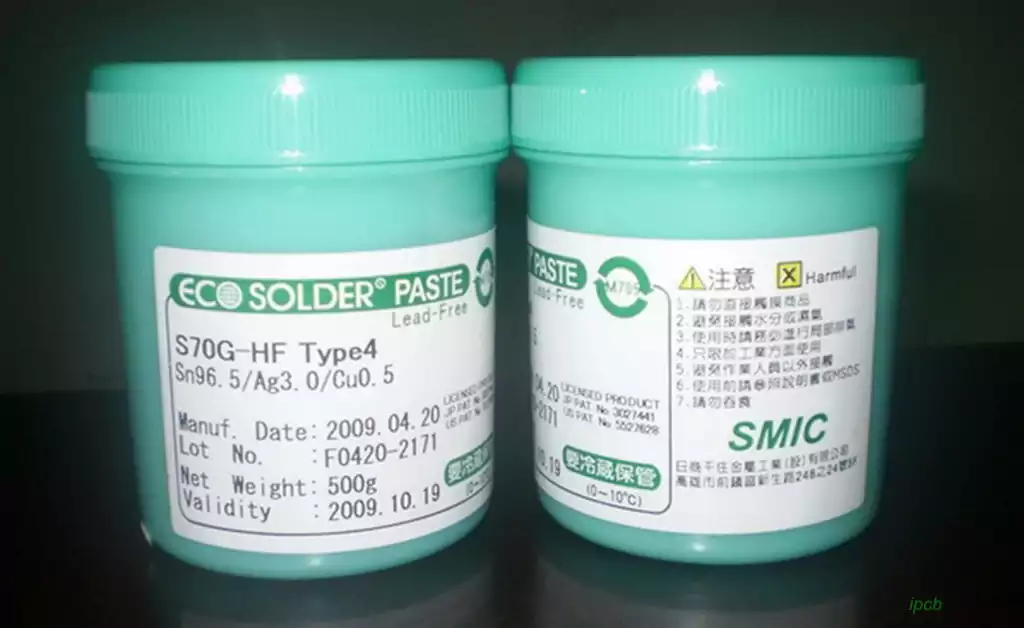
Some of the roles of the main synthetic components in the solder paste flux:
- Thixotropic agent (Thixotropic): This component is mainly to regulate the viscosity of it and printing performance, to prevent the printing of drag, sticking and other phenomena;
- Activator (Activation): This component mainly plays a role in removing the PCB board copper film pad surface layer and parts of the oxidized material of the role of soldering parts, at the same time has the effect of reducing the surface tension of tin, lead;
- Solvent (Solvent): This component is the solvent of the solder component, in the mixing process of it plays a role in regulating the uniformity of it has a certain impact on the life of it;
- Resin (Resins): This component mainly plays a role in increasing the adhesion of it, but also has the role of protection and prevention of post-solder PCB oxidation again; the component of the parts fixed to play a very important role.
As the core soldering material in the SMT placement process, the quality and performance of it has an important impact on the manufacturing quality of electronic products. Through the in-depth understanding of its composition, classification and the role of each synthetic component in the flux, we can better grasp the characteristics of the solder paste and the application method, so as to improve the reliability and efficiency of the SMT placement process.