Applying a metallic/organic coating to bare pads is called surface finishing. The surface finish protects the copper pads from scratches and oxidation while promoting soldering in the reflow oven. While there are several types of surface finishes, ENIG vs ENEPIG are the two common types. Manufacturers typically use them on ceramic PCBs, flex boards, and rigid-flex PCBs to provide high reliability. ENIG and ENEPIG provide a better surface finish than OSP, HASL, immersion tin, etc.
ENIG (Electroless Nickel Immersion Gold) finishes have historically been the best fine pitch (flat) surface and lead-free option.
ENIG is a two-step process that applies a thin gold coating over a thin nickel coating. The nickel acts as a barrier to the copper and is the surface that the component is actually soldered to, while the gold protects the nickel during storage.
The inner layer of Ni is typically 3 to 6 μm thick, and the outer layer of Au is typically deposited at a thickness of 0.05 to 0.1 μm.
Ni forms a barrier layer between the solder and the copper.
The role of Au is to prevent Ni from oxidizing during storage, thus extending shelf life, but the gold deposition process also produces excellent surface flatness.
The Electroless Nickel Immersion Gold process is as follows: Cleaning -> Etching -> Catalyst -> Electroless Nickel Plating -> Immersion Gold -> Cleaning Residue
While this coating process has a long shelf life and facilitates plating through-holes, it is a complex and expensive process that cannot be reworked and is known to cause losses in signaling RF circuits.
Benefits of Electroless Nickel Immersion Gold Finishes
ENIG coatings offer many advantages, the main ones being:
● Surface flatness – particularly useful for fine pitch pcb components such as BGAs and other small shaped components.
● Suitable for crimped assemblies – provides a good connection for electrical testing.
●Suitable for lead splicing and edge card connectors.
●Cheaper compared to ENEPIG.
Disadvantages of Electroless Nickel Immersion Gold Finishes
ENIG coatings have some drawbacks:
● Black pads – result of unregulated nickel and gold plating processes.
●PCB coatings with variable thickness – due to unregulated nickel and gold plating processes.
●Low wettability- during soldering.
Electroless Nickel – Electroless Palladium Immersion Gold Plating (ENEPIG)
Chemically immersed gold plated materials have a copper-nickel-palladium-gold layer structure that allows direct lead bonding to the plating. The final layer of gold is very thin, as is the case in ENIG. The gold layer is soft, as in ENIG, so excessive mechanical damage or deep scratches may expose the palladium layer.
In contrast to ENIG, ENEPIG has an additional layer of palladium between the nickel and the gold, which further protects the nickel layer from corrosion and prevents the black matting that can occur in ENIG finishes.
Ni is deposited at a thickness of about 3 to 6 μm, palladium at about 0.1 to 0.5 μm, and gold at 0.02 to 0.1 μm.
The ENEPIG finish consists of four metal layers:
Copper
Nickel
Palladium
Gold
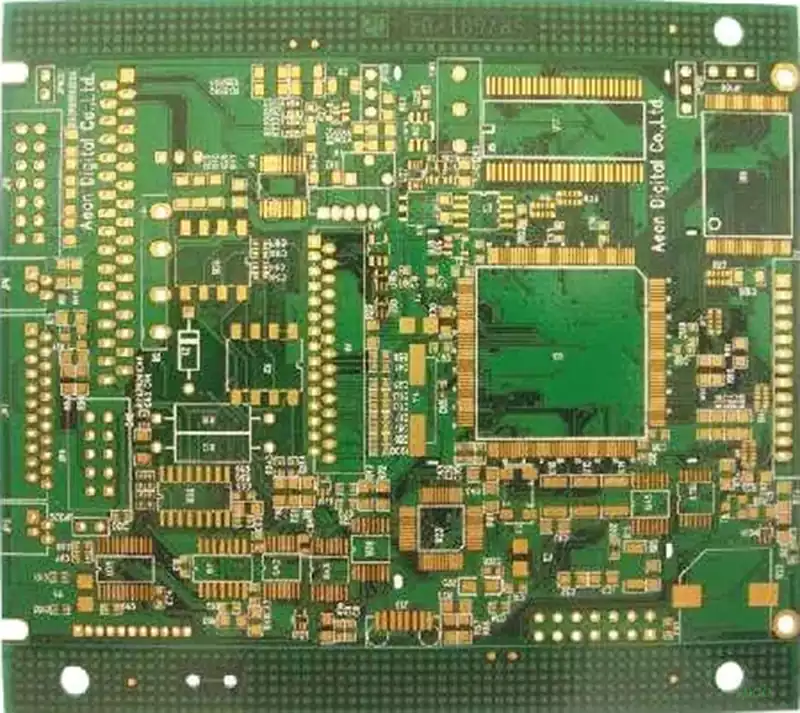
Similarities between Electroless Nickel Immersion Gold and ENEPIG finishes
Although these are two different types of finishes, they do share some common features. both ENIG and ENEPIG finishes utilize electroless nickel plating and immersion gold. Both provide a straight, flat soldering surface, making it easier to solder small components to the PCB surface. In addition, both finishes are lead-free, making them a green alternative to PCB products.
Both ENIG and ENEPIG provide excellent electrical performance and thermal dispersion. Coating the surface of PCB pads with electroless nickel immersion gold or ENEPIG requires similar procedures. For example, both processes start with copper activation followed by a chemical nickel coating. The final layer of both finishes is immersion gold.
Differences between Electroless Nickel Immersion Gold and ENEPIG finishes
The main difference between the two finishes is the presence of a palladium layer in ENEPIG. This palladium layer has high oxidation resistance and improves the electrical properties of the surface finish. However, the additional palladium layer increases the cost of the ENEPIG finish compared to ENIG.
In addition, the low reliability of the solder joints results in an inconsistent electroless Nickel Immersion Gold surface finish for gold wire bonding. In addition, additional procedures are required to stop nickel corrosion in ENIG. For these types of problems, ENIG surface treatments are best suited for low-end electronics.
The modern surface finishes of ENIG and ENEPIG are highly reliable. They are ideally suited for high-quality ceramic circuit boards. Since the PCBs do not contain any hazardous substances such as lead, they are RoHS-compliant. In addition, both finishes provide a very flat and level surface for SMT mounting. However, ENEPIG can fulfill any additional specifications for PCBs with various SMT packages. ENEPIG is often used for PCBs required by the military, aerospace and medical industries.