In the electronics industry, pcb solder mask material is an indispensable basis for the construction of electronic devices and systems. The quality and technical characteristics of these materials have a direct impact on the performance and reliability of the final product.
Common pcb solder mask material
- Solder wire
Solder wire, as a common material for circuit board soldering, is composed mainly of tin, copper and a tin-plated layer. Depending on the tin content and form, solder wires are categorized into various types. With its excellent density, adhesion and anti-oxidation properties, as well as good toughness, solder wire is widely used in electronics, electrical appliances, communications and other fields. - Solder Paste
Solder paste, as a semi-solid soldering material, is a mixture of solder powder, flux and binder. Compared to solder wire, solder paste is more convenient to use, and can be injected automatically or manually into PCB holes and pads, which is very suitable for SMT (SMD) and THT (plug-in) technology. - Solder Pad
Solder pads, as the key circular metal interface on the circuit board, the material is mostly copper, tin or gold-plated metal. During the soldering process, the solder and the soldered devices can be firmly adhered to the pads to form a stable circuit connection. Different types of pads are optimized for different soldering techniques, such as surface mounting technology and through-hole mounting technology. - Flux
Flux plays an important role in the soldering process, it can effectively reduce the oxidation phenomenon between the solder and the soldered device, thus improving the quality and efficiency of soldering. Common fluxes include alcohol and sodium chloride. The use of flux can significantly reduce the defects and damage caused by soldering, to ensure the solidity and reliability of the soldering.
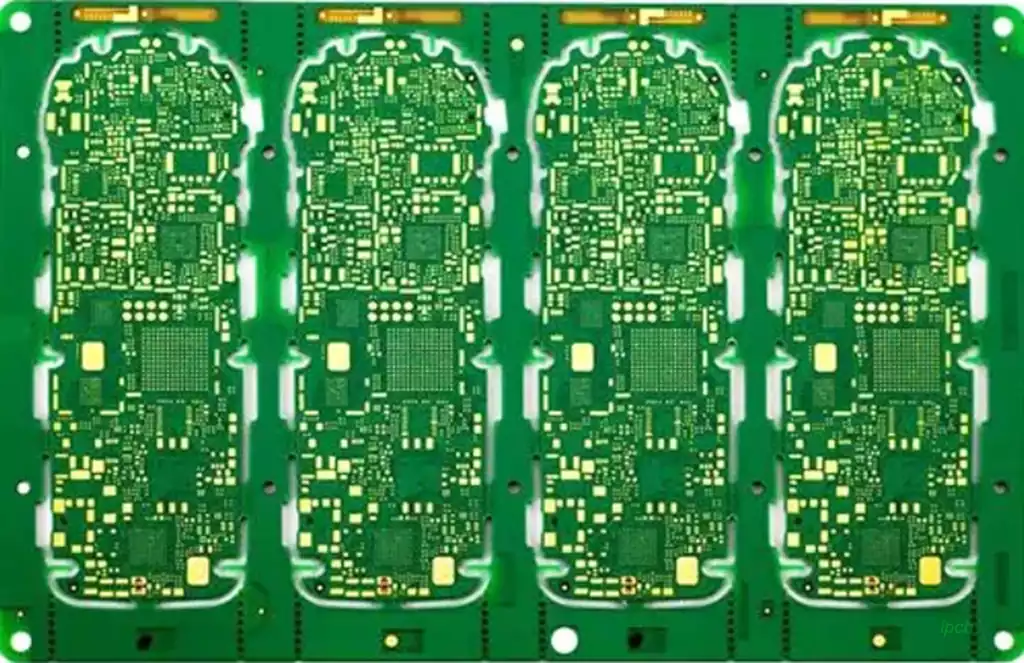
When selecting circuit board soldering materials, focus on the following factors:
- Soldering applications: Some circuit boards have very small solder joints and spacing, thus requiring the use of very fine wire. In this case, lead-free solder may be a better choice because it has a higher surface tension and therefore is easier to form smaller solder joints and connections.
- Environmental factors: Since lead is a hazardous substance, lead-free solder is considered a more environmentally friendly and safer choice.
- Cost: The cost of lead-free solder may be higher than tin-lead solder, but the gap is narrowing as tin-lead soldering becomes more tightly regulated.
- Soldering conditions: Lead-free soldering typically requires higher temperatures and longer soldering times, so these factors also need to be considered when selecting solder materials.
When choosing circuit board soldering materials, you should also pay attention to the following matters:
- if you are not sure which type of soldering material to use, contact the circuit board manufacturer for their recommended type.
- Always follow the operating instructions when soldering circuit boards. If you are unsure how to proceed, read the relevant instruction manual or seek guidance from a professional experienced person.
- Always wear gloves and a mask when working with soldering materials to avoid inhaling harmful soldering fumes and vapors.
- Always inspect the welded joints after welding to ensure their quality and connection.
In the electronics industry, the selection and application of pcb solder mask material is the key to ensuring the performance and reliability of electronic equipment and systems. When selecting soldering materials, we need to comprehensively consider a number of aspects such as soldering applications, environmental factors, cost and soldering conditions.