The solder ball reflow process is a commonly used surface mount technology. It can realize the soldering function by heating and melting the solder ball and connecting it to the solder joints on the substrate, and can be widely used in electronic products to improve the reliability of the connection, save space, and facilitate the handling.
Principle
Solder ball reflow soldering is one of the most commonly used surface mount technology, the principle is mainly through the heating of the solder ball melting, and then connected with the solder joints on the substrate. Specifically, it can be divided into the following steps.
- Bottom preheating: Before heating the tin ball, by heating the bottom preheating to increase the temperature to ensure that the tin ball to reach the melting point.
- Heating the tin ball: After preheating the bottom, heat the tin ball to reach the melting temperature.
- Reflow area: After the solder ball melts, it needs to be put into contact with the solder joint of the substrate, and the common method is to pull the solder ball to the solder joint through the surface tension of the liquid.
- Cooling: After the soldering is completed, it needs to be cooled to make the connection stronger and avoid floating or falling.
APPLICATIONS
Solder ball reflow soldering can be widely used in electronic products in the surface mount technology, such as computer motherboards, TV motherboards, cell phone chips, automotive control systems and so on. Its advantages are mainly in the following areas.
- Improve the reliability of the connection: large welding area, vertical solder joints, not easy to loosen.
- Saving space: the size of the solder ball can be controlled, the soldering point can be set in a very close position.
- Convenient handling: stable solder joints, not easy to have problems, and can be fully automated using the machine for soldering.
In the SMT production process, often encountered after reflow soldering out of the board has a tin bead, tin bead generation, so that the quality of the product is not guaranteed, so that the appearance does not look smooth. Causes of reflow solder beads:
Incorrect temperature profile
In order to make the PCB surface in 60 ~ 90s to 150 ℃, and insulation about 90s, which can not only reduce the PCB and components of the thermal shock, but also to ensure that the solvent of the solder paste can be partially evaporated not to be in the re-flow soldering, due to the rapid increase in temperature appears too much solvent and caused by splashing, so that the paste rushed out of the pad and the formation of tin beads.
Quality of solder paste
Solder paste in the metal content is usually (90 ± 0.5)%, the metal content is too low will lead to too much flux components, so too much flux will not be easy to evaporate due to the preheating stage caused by flying beads.
Increased water vapor/oxygen content in solder paste. Since solder mask paste is usually refrigerated, when it is taken out of the refrigerator, the recovery time is not ensured, thus leading to the entry of water vapor. In addition, the cap of the solder paste bottle should be tightly closed after each use, and if it is not tightly closed in time, it will also lead to the entry of water vapor.
Printing and Patch
Solder paste in the printing process, due to the template and pad alignment offset, if the offset is too large will lead to solder paste dip to the pad outside, easy to appear after heating beads of tin.
Therefore, the template should be carefully adjusted clamping, there should be no loose phenomenon, in addition to the printing environment is not good will also lead to the generation of tin beads, the ideal ambient temperature (25 ± 3) ℃, relative humidity of 50% ~ 65%.
The thickness of the template and the opening size
Stencil thickness and opening size is too large will lead to an increase in the amount of solder paste, but also cause the solder paste flow to the pad outside, especially with the chemical corrosion method of manufacturing the template.
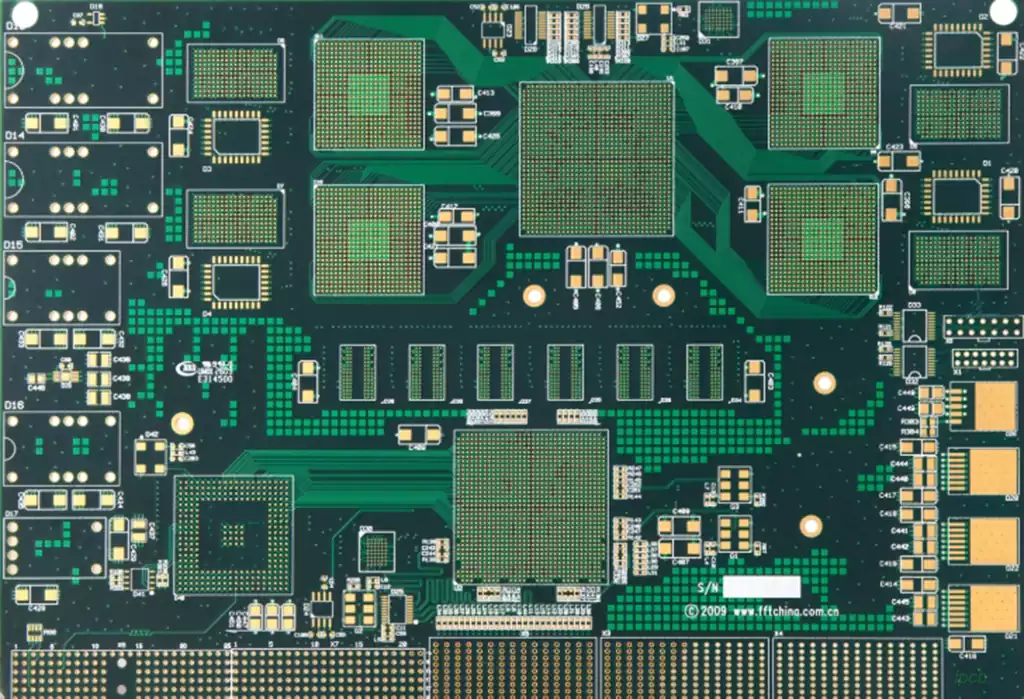
Reflow solder beads solution
- Control soldering temperature: in the soldering process, the need to control the soldering temperature, to avoid the temperature exceeds the set value, but also pay attention to reduce the residual solder particles, in order to reduce the probability of solder beads.
- Control the welding time: in the welding process, need to control the welding time, to avoid welding time is too long, simplify the welding process to reduce the probability of solder beads.
- Select the appropriate solder: in the selection of solder, need to pay attention to the uniformity of the coating, to avoid excessive use, strict compliance with the use of specifications, as well as regular cleaning of the welded area to avoid contamination.
- Pay attention to circuit board pretreatment: before welding, the need for circuit board pretreatment, including oil removal, de-oxidation treatment, etc., which can effectively avoid the formation of solder beads on the circuit board residual impurities.
- Increase the cleaning process: after the completion of welding, the need to increase the cleaning process, cleaning the residual solder and solder particles, to avoid their repeated use, causing damage to the circuit board.
The solder ball reflow process as a highly efficient surface mount technology, which plays a vital role in the manufacture of electronic products. However, the problem of tin beads generated during the reflow soldering process cannot be ignored. Through in-depth understanding and control of the temperature profile, solder paste quality, printing and placement process and other key factors, we can effectively reduce the generation of tin beads, improve the quality of soldering and product reliability.