PCB protective coating is thin layers of polymers applied to the surface of printed circuit boards, typically between 25μm and 150μ thick,to protect and electrically insulate circuits and pcb components from environmental stresses. These coatings ensure PCB reliability in environments where moisture, condensation, dust, dirt, salt, chemicals, abrasion, thermal and mechanical shock, and other factors can affect circuit performance. These products were originally developed for military applications. They allow for the design of smaller electrical assemblies while increasing the mechanical support of the assembly and improving the fatigue life of solder joints.
Five key reasons to use conformal coatings on PCBs
- Provides complete protection: Conformal coatings are designed to protect circuit boards from moisture, dust, fungus, temperature extremes and other contaminants. These coatings are resistant to many types of solvents and chemical attack, and are also heat resistant. Typically, circuit boards exposed to these types of environments degrade, but conformal coatings can slow or even prevent this effect. Without the coating, leakage or corrosion may occur, damaging delicate components.
- Improved Dielectric Properties: When a conformal coating is applied to a PCB, it prevents corrosion and arching while increasing mechanical support for components and improving the fatigue life of solder joints. It also helps to compress the circuit footprint, resulting in tighter spacing between electronic components. In addition, it significantly slows down the growth of tin whiskers, reducing the risk of short circuits caused by tin whiskers between neighboring conductors.
- Convenient construction: they can be sprayed, dip-coated or brushed.With a single coat,they provide reliable protection for rigid boards and flexible film laminates as well as metal, glass or plastic substrates. They are easy to dispense and,for thicker coating requirements,certain materials can be applied multiple times.
- Time and cost savings: protective coatings allow for lighter weight, smaller assemblies because shells and casings are not required.For triple-conformal adhesive manufacturers, fewer printed circuit board repairs mean less time and labor, and more savings.
- Protecting Sensitive Information: Some conformal coatings have opaque colors that help cover markings, labels, and other identifiers on the pcb board.
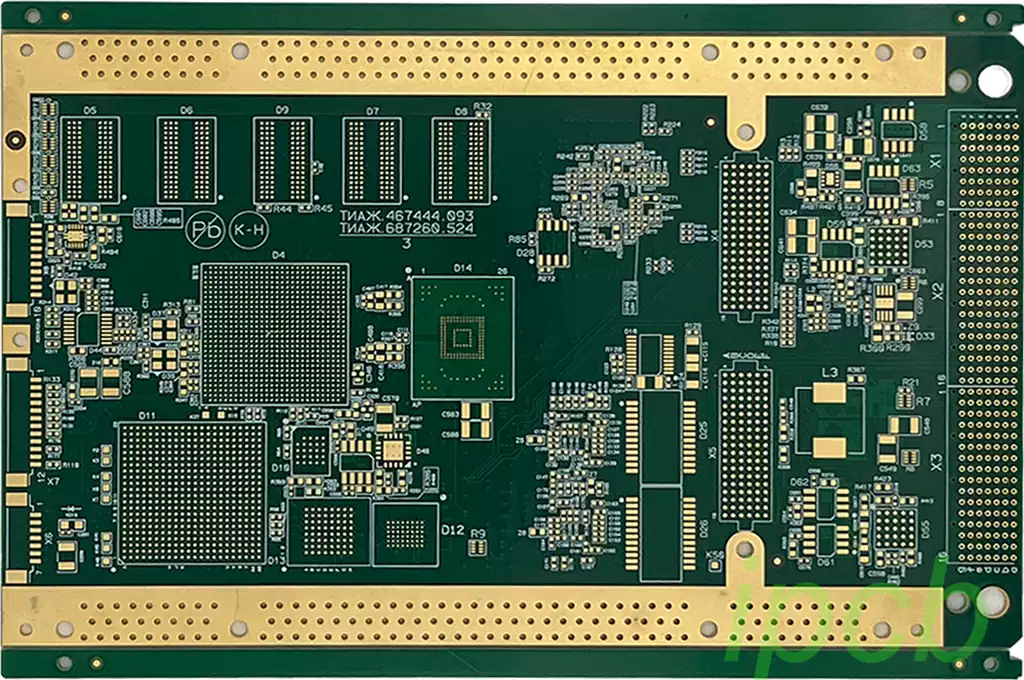
How to Choose the Right Conformal Coating
Acrylic resin (AR) conformal coatings are easy to apply and dry quickly at room temperature. Acrylics have fungus resistance as well as beneficial electrical and physical properties, are typically 0.002-0.005 inches thick, and do not withstand temperatures above 125°C, which limits their use in many high-temperature applications. Many acrylic resin variants can cure in less than 30 minutes and therefore remain a commonly used coating with advantages where shorter production times are required.
Epoxy resins (ER), usually two-component compounds, are very durable coatings with good chemical and abrasion resistance as well as moisture resistance. However, epoxy resins can shrink during polymerization and extreme temperatures can affect their stress resistance. The rugged nature of epoxies also makes them difficult to rework and repair, so they need to be applied carefully.
Silicone resin (SR) coatings are a popular choice for automotive applications because of their ability to maintain high performance in environments exceeding 200° Celsius. Silicone resins also offer good corrosion and moisture resistance. Silicone resins can be applied thicker than other coatings and therefore excel in vibration damping. Unfortunately, silicone resins are not as resistant to abrasion and solvents as other form-fitting coatings.
Polyurethane resin (UR) coatings offer reliable chemical and moisture resistance, excellent dielectric properties over long periods of time,and better isolation of signal traces,a characteristic that contributes to the miniaturization of printed circuit boards.Polyurethane resins are resistant to chemical solvents and slow the growth of tin whiskers. However, the solvent resistance of urethane resins makes the coating difficult to remove or rework.Their long-term performance is limited in high-temperature and vibration environments.
Polyparaxylene coatings (XY) are applied using a chemical vapor deposition process to form a very uniform,pinhole-free,layered film that protects printed circuit boards. XY can be applied to virtually any surface and any shape, including glass, metal,paper,resins,plastics, ceramics,ferrite and silicon.The chemical inertness of poly-paraxylene coatings enhances their utility in implantable biomedical devices. The cost of poly-paraxylene is usually somewhat higher and rework is more difficult. In addition, this coating is suitable for batch application.
In the world of electronics manufacturing, the importance of PCB protective coating cannot be overlooked. It not only provides all-around protection for printed circuit boards (PCBs) from environmental factors, but also promotes miniaturization and high efficiency of electronic devices by improving dielectric properties and optimizing circuit layout. With the continuous development of electronic technology, conformal coatings will continue to play a key role in the field of electronics manufacturing, providing a strong guarantee for the reliability, durability and miniaturization of modern electronic equipment.