Rigid-flex PCB designs combine rigid and flexible board technologies. In most rigid-flex boards, flexible circuit substrate layers are attached to one or more rigid boards internally, externally, or both, depending on the design specifications of the application. Typically, rigid-flex printed circuit boards are produced with a flexible polyimide material on a copper-clad substrate that is attached to a rigid board. The layers of the flexible portion of the rigid PCB typically have filled vias to ensure interconnectivity between them.
What are the advantages of PCB rigid-flexible boards over traditional rigid boards?
PCB rigid-flex boards offer high reliability and stability. Due to the presence of flexible circuit boards, PCB rigid-flex boards are better able to absorb external shocks and vibrations, reducing the risk of board damage and breakage. At the same time, the use of rigid boards also ensures the stability and reliability of the circuit board, so that it can work properly in a variety of harsh environments.
Secondly, rigid-flex boards offer a higher degree of design freedom.Traditional rigid board wiring is limited to the plane layout,while the rigid-flexible combined board through the flexible circuit board bending and folding,can be arranged in three-dimensional space more components and lines,improve the circuit board wiring density and functional integration, for the innovative design of the product to provide a greater space.
Rigid-flex pcb also offers lower costs and fast production cycles.Compared to the traditional way of designing and manufacturing rigid and flexible circuit boards separately, the integrated design and manufacturing process of PCB rigid-flex boards can dramatically shorten the production cycle and reduce the labor and material costs in the manufacturing process, thus lowering the overall cost.
Why choose PCB rigid-flex boards?
Rigid-flex boards are able to fulfill a wider range of applications.Whether it’s in consumer electronics, medical devices, aerospace equipment or smart wearable devices, it offers better performance and reliability to meet the specific needs of different products for circuit boards.
Secondly, rigid flex pcb has higher adaptability and scalability. Due to the existence of flexible circuit boards, the combination of rigid-flexible boards can be better adapted to the shape, size and functional requirements of the product, and can be easily expanded and upgraded for the subsequent development and improvement of the product to provide greater space.
With its advantages of high reliability, design freedom, low cost and fast production cycle, PCB rigid-flexible combination board has become an important choice in the field of electronic product design and manufacturing. Whether you are pursuing innovative design, improving product performance or reducing manufacturing costs, choosing PCB rigid-flex boards is a wise decision. I believe that with the continuous progress of technology, PCB rigid-flexible combination board will play an important role in more areas, bringing more convenience and possibilities for our lives.
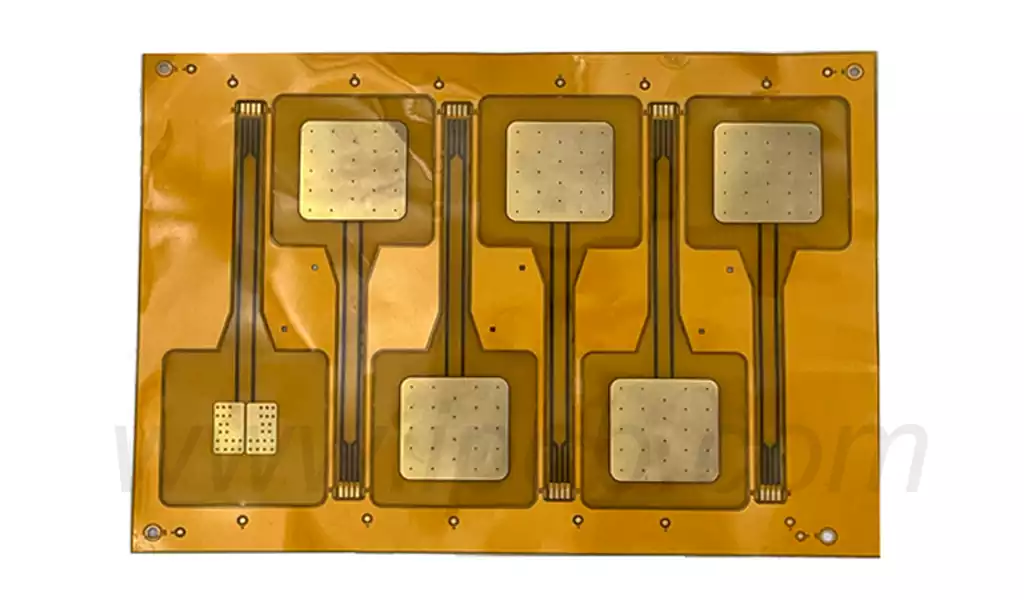
Manufacturing process of rigid flex circuit boards
Material preparation
The main materials for rigid flex printed circuit boards include mineral wool,calcium silicate board, wood fiber board, steel plate and so on.Before production, you need to carefully select and purchase the right materials to ensure that their quality meets the requirements.ProcessingProcessing is the key step in making the soft and hard combination board.First,calcium silicate board and wood fiber board are tightly bonded to form a strong base layer.Next, mineral wool is made into the desired shape and size and then assembled with the base layer to form the complete panel.Finally,steel plates are secured throughout the bonded panels to enhance the stability and strength of the structure.
Assembly
The fabrication process of rigid-flex panels requires assembly to ensure that the various parts are tightly and seamlessly connected.During the assembly process,careful measurements are taken and a plan is developed to ensure that each panel is assembled correctly.GluingIn the production of rigid-flex panels, adhesives are used to bond the materials together.During the bonding process,the amount and uniformity of the bonding is strictly controlled to ensure the quality and stability of the entire panel.
Deep Processing
After the soft and hard bonded panels are made,they can be deeply processed.According to different applications and needs, it can be cut into the required size and shape, and processed with planing, punching and other processing procedures to meet the various needs of customers.
Application of Rigid-Flex Plate
Some of the features and functional advantages of rigid-flex panels, such as reduced interface connections, minimized package weight and size, and resistance to extreme conditions,have made them widely sought after for applications in commercial, industrial, and household sectors. In addition to small consumer products such as telephones and multimedia players,they are used in the following industries:
Medical:Used in devices such as pacemakers,cochlear implants,handheld monitors,imaging equipment,drug delivery systems, wireless controllers, and more.
Aerospace: This application produces equipment such as radar equipment, GPS, radio communication systems, control tower systems, sensors, noise and vibration test systems, motion sensors, and environmental and climate test chambers.
Telecommunications: This field has base stations, handheld devices,communication satellites,wireless communication systems,signal processing systems, transmission media,routers and servers, and online signal extension systems.
Consumer Appliances: This is a common application for rigid-flex panels, commonly found in ovens, TV remote controls, washing systems, lighting systems, solar energy systems, UV water purifiers, electronic irons, and more.
Automotive: The industry is no exception,applying rigid-flex to electronic control modules, transmission controls, LCDs,comfort control units, and products such as air conditioning, music, traction control,entertainment and navigation systems.
Military: Rigid-flex PCB has important applications in the production of weapon guidance systems,communication systems,GPS,aircraft missile launch detectors, and surveillance or tracking systems.
Manufacturing: In this field, rigid-flexible combination boards are used in test equipment,electrical switches,industrial automation systems,control panels, industrial air conditioning and closed-circuit television monitoring systems.
Rigid-flexible pcb combination board with its unique advantages, in the electronics industry plays an increasingly important role. It not only improves the performance and reliability of products, but also meets the diverse needs of design. With the continuous progress of technology, this kind of circuit board will show its charm in more fields and inject new vitality into the development of the electronics industry.