Flex PCB coverlay is an insulating protective layer covering the surface of the flexible printed circuit board, playing a role in protecting the surface conductors and increasing the strength of the substrate. The protective material of the outer layer of graphics, there are generally two types to choose from.
The first type is dry film type (cover film), the selection of polyimide materials, without adhesive directly with the etching of the circuit board to be protected after lamination press. This cover film requires pre-forming before pressing, revealing the need to weld the part, so it can not meet the requirements of the assembly of the finer.
The second category is photorealistic type. Photorealistic type of species is covered in the dry film using a film machine paste pressure, through the photorealistic way to reveal the welding part, to solve the problem of high-density assembly; the second is a liquid screen-printing type of covering materials, commonly used thermosetting polyimide materials, as well as photorealistic type of flexible circuit boards, such as special solder resist inks. These materials can better meet the requirements of fine-pitch, high-density assembly of flexible boards.
Structure of FPC
Substrate layer: The substrate layer of FPC is made of flexible insulating materials, commonly used polyester film (such as polyester sheet PET) and polyimide film (PI film). These materials are highly flexible and have high tensile strength. The base layer provides strength and flexibility, allowing the FPC to be bent, folded or adapted to complex shapes. The protective layer provides protection and isolation.
Metal Layer: The conductive metal layer on the flexible circuit board is generally copper foil, usually between 0.009mm and 0.072mm thick. Copper foil is attached to the substrate layer, through a special chemical etching and etching process, it will be etched into the design of the required wires, electrodes and other shapes. The wire lines in the metal layer connect the electronic components and play a role in transmitting signals and currents.
Protective layer: In order to protect the wire layer, FPC is usually coated with a protective layer, commonly used protective layer materials such as polyester resin, polyurethane and so on. The protective layer not only protects the wire layer from damage, but also prevents oxidation, corrosion and other environmental factors.
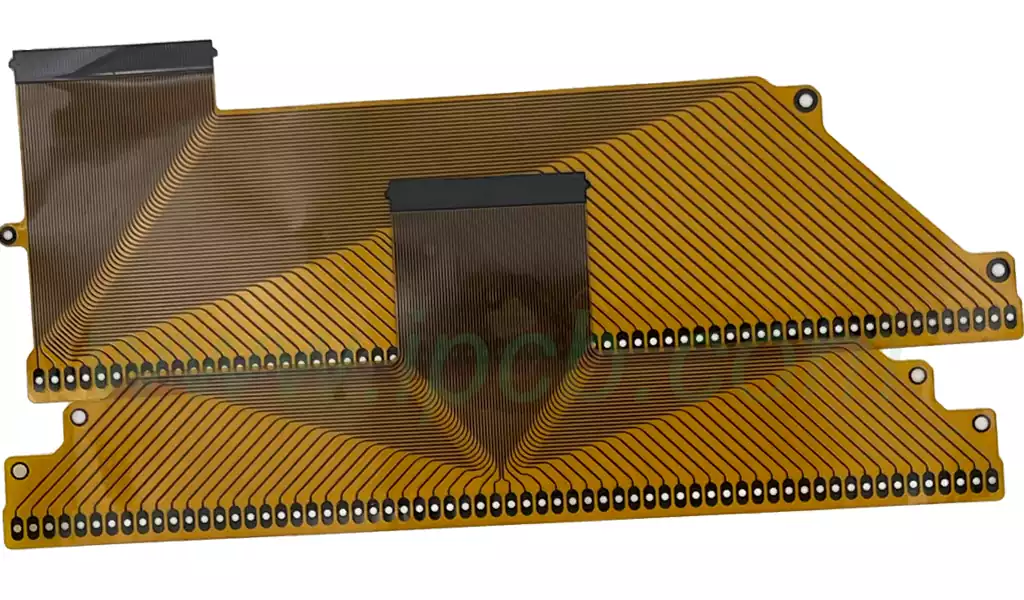
Processing options for the Flex PCB coverlay
In the current printed circuit industry, both mechanical and laser processing use common manufacturing processes. Both processing methods use their own unique combination of equipment and each has its own advantages and disadvantages.Which processing method is used to obtain the overlay depends on the flexible circuit application environment, throughput, lead time, and cost.
Machining
Machining is, of course, by far the most efficient method of producing overlays. The main advantage of machining is that manufacturers can use a combination of their existing equipment for PCB drilling and fabrication. It allows for fast drilling, multiple workstations (4-6) can drill holes at the same time, there is no need to learn anything new, and the equipment is readily available to each PCB manufacturer. The quality of the holes depends on the drilling tool and machining has minimal limitations on the size of the holes.
Laser Processing
Investment in laser drilling is required; however, this equipment is primarily used for laser drilling of bare circuit board.Many PCB manufacturers do not have off-the-shelf laser equipment, and the cost of drilling is much higher than drilling with mechanical equipment. Drilling with a laser is faster than mechanical drilling, but only one hole can be drilled at a time. Holes drilled with a laser are very accurate and there is no minimum hole size limit.
Flex pcb coverlay or bendable soldermasks
Bendable soldermask is usually the cheapest when it comes to cost. Some one- or two-layer bendable circuits are not subject to multiple bending cycles or maximum bending radii, and such circuits can be coated with an epoxy-based soldermask, which is designed to be a non-cracking, bendable soldermask. However, this is not recommended when the soldermask is designed to require dynamic bending or a maximum bend radius. Another option is laminated flexible cover layers, which are composed of the same core material as the bendable circuit and are well suited for dynamic bendable circuit applications.
The coverlay flex pcb material is a polyimide sheet with an acrylic adhesive on one side. It is typically created by pre-processing holes in the polyimide sheet where openings are needed in the final surface layer. This overlay sheet is usually processed using a lamination method that employs specialized pads to ensure uniformity around the copper components on the flexible layer. For rigid-flex circuits, the overlay layer is usually cut to be embedded in the rigid circuit and is no more than 50 mils thick. This is done so that all plated holes in the rigid-flex circuit are free of any acrylic adhesive, as it can affect the integrity of the plated layer on the hole walls.
In FPC manufacturing, the selection of the Flex PCB coverlay and processing technology are key, and together they determine the performance and reliability of the FPC. As technology continues to advance, we look forward to more innovative solutions in the future, bringing more possibilities to the FPC industry.