PCBA contract manufacturing is a critical service in the electronics industry. It involves outsourcing the assembly of electronic components onto a printed circuit board (PCB) to specialized manufacturers. This process is essential for companies that need high-quality assemblies but may lack the necessary resources, expertise, or equipment to produce them in-house. PCBA contract manufacturing enables businesses to focus on their core competencies, such as product design and marketing, while ensuring that their products are manufactured to the highest standards.
The Role of PCBA in Electronics
PCBs are the foundation of most electronic devices, providing both the physical structure and electrical connectivity required for the device to function. The assembly of components onto the PCB, known as PCBA, involves placing and soldering components like resistors, capacitors, and integrated circuits onto the board. This process is crucial in ensuring that the final product operates correctly and reliably. PCBA contract manufacturers are vital in the electronics supply chain. They possess the expertise and equipment needed to assemble complex electronic products efficiently and accurately. By outsourcing this task to a contract manufacturer, companies can reduce costs, accelerate time-to-market, and ensure consistent product quality.
The PCBA Contract Manufacturing Process
- Design and Prototyping: The process begins with the client’s design, including a schematic, bill of materials (BOM), and PCB layout. Some contract manufacturers offer design assistance, helping clients optimize their designs for manufacturability. Once the design is finalized, a prototype is produced to test the functionality and ensure that it meets the required specifications.
- Component Procurement: After the design is confirmed, the contract manufacturer procures the components listed in the BOM. These manufacturers often have established relationships with component suppliers, enabling them to source high-quality parts at competitive prices. Effective component procurement is crucial for minimizing lead times and ensuring the availability of parts.
- PCB Fabrication: The bare PCB is fabricated according to the client’s design specifications. This step involves creating the physical board, including the copper traces, pads, and vias necessary for connecting the components. The PCB may also feature solder masks, silkscreens, and other elements that contribute to its functionality and durability.
- Assembly: The core of the process is the assembly of components onto the PCB. This can be done using Surface Mount Technology (SMT), where components are placed directly onto the board’s surface, or Through-Hole Technology (THT), where component leads are inserted into holes and soldered from the opposite side. The choice of assembly method depends on the specific requirements of the design.
- Inspection and Testing: Once the assembly is complete, the PCBA undergoes thorough inspection and testing to ensure it meets quality standards. Techniques like Automated Optical Inspection (AOI), X-ray inspection, and functional testing are used to identify defects or issues that could impact the product’s performance. These quality checks are critical to delivering a reliable final product.
- Packaging and Shipping: After passing all inspections and tests, the PCBA is carefully packaged according to the client’s specifications and then shipped. Some contract manufacturers also offer direct shipping to end customers, streamlining the supply chain.
Benefits of PCBA Contract Manufacturing
- Cost Savings: Contract manufacturers benefit from economies of scale, allowing them to purchase components and materials at lower prices. Additionally, they have the expertise to optimize the assembly process, reducing labor costs and waste.
- Access to Expertise: Contract manufacturers specialize in PCBA and possess deep knowledge of the latest technologies and industry standards. This expertise ensures that the final product is of the highest quality and meets all required specifications.
- Scalability: PCBA contract manufacturers can handle projects ranging from small prototype runs to large-scale production, offering businesses the flexibility to scale production based on demand.
- Focus on Core Competencies: By outsourcing the assembly process, companies can concentrate on their core areas, such as product development, marketing, and customer support, rather than on the complexities of manufacturing.
- Risk Mitigation: With robust quality control processes in place, contract manufacturers help reduce the risk of defects, ensuring that the final product is reliable and meets all necessary standards.
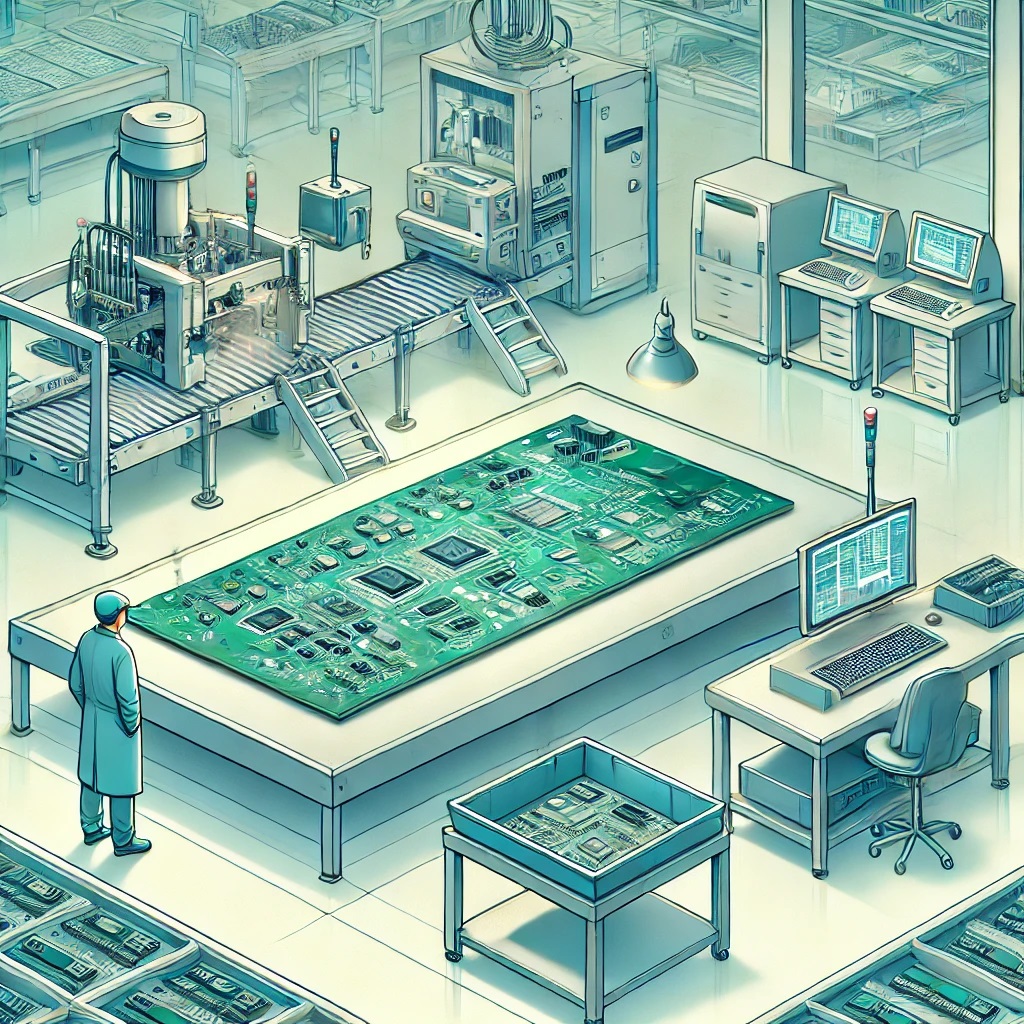
Key factors to consider when selecting a PCBA contract manufacturer:
- Experience and Reputation: Choose a manufacturer with a proven track record and a strong reputation in the industry. Look for reviews, testimonials, and case studies to gauge their reliability and performance.
- Capabilities and Services: Ensure that the manufacturer has the necessary capabilities to meet your specific needs. This includes handling the complexity of your design, the required production volume, and any special requirements like advanced testing.
- Quality Standards: Certifications like ISO 9001 or IPC-A-610 indicate a commitment to quality. These standards ensure that the manufacturer adheres to industry best practices.
- Supply Chain Management: Effective supply chain management is vital for minimizing lead times and ensuring the timely delivery of components. A manufacturer with strong supplier relationships and a well-organized supply chain is essential.
- Communication and Support: Good communication is key to a successful partnership. The manufacturer should be responsive and transparent, providing regular updates and collaborating closely with you throughout the process.
- Cost Structure: While cost should not be the sole deciding factor, it’s important to choose a manufacturer that offers competitive pricing. Be sure to understand their cost structure and any additional fees.
The Future of PCBA Contract Manufacturing
- The PCBA contract manufacturing industry is evolving rapidly, with several trends shaping its future:
- Automation and Industry 4.0: The integration of automation and Industry 4.0 technologies is transforming PCBA manufacturing. Automated assembly lines and AI-driven quality control systems are increasing efficiency and reducing costs.
- Miniaturization and High-Density Assemblies: As electronic devices become smaller, the demand for miniaturized components and high-density assemblies is growing. Contract manufacturers are adopting new techniques to meet these challenges.
- Sustainability: Environmental concerns are driving the adoption of sustainable practices, such as the use of lead-free solder and eco-friendly materials. Green manufacturing is becoming increasingly important.
- Supply Chain Resilience: Global supply chain challenges are prompting manufacturers to diversify their supply chains and invest in supply chain management technologies to ensure stability.
- Customization and Personalization: The trend towards customization is influencing PCBA manufacturing, with customers seeking tailored solutions. Manufacturers are offering more flexible services, such as rapid prototyping and small-batch production.
PCBA contract manufacturing is essential for producing high-quality electronic products efficiently and cost-effectively. By partnering with a specialized contract manufacturer, businesses can leverage expertise, advanced technology, and streamlined processes, allowing them to focus on innovation and market success. As the industry continues to evolve, staying informed about trends and selecting the right contract manufacturing partner will be key to thriving in the competitive electronics market.