PCB delamination is the phenomenon of partial separation between layers of a printed circuit board (PCB) during manufacture or use. This separation is usually characterized by bubbles or blisters on the surface, which in severe cases can affect the functionality and reliability of the board. Understanding the causes and prevention of these problems is essential to safeguarding the performance of the board.
The main causes of PCB delamination
- Environmental Humidity
One of the main causes of PCB delamination is the humidity in the environment. When moisture enters between the layers of the PCB, the increase in vapor pressure may lead to layer to layer separation, thus triggering the phenomenon of delamination. In addition, in the high-temperature reflow soldering process, moisture evaporation of the formation of vapor pressure increases, if more than the bonding force of the internal material, it will lead to delamination occurs. - Improper hot pressing process
In the production process of multilayer PCB, the control of the hot pressing process is critical. Pre-pressing time is too short or too long will lead to resin loss or interlayer air residue, ultimately causing delamination. In addition, uneven thermal expansion or improper control of the pressing temperature will also affect the bonding strength between the layers, resulting in delamination. - Raw material quality problems
PCB substrate and resin material quality is also an important factor leading to delamination. Poor quality or substandard materials in the manufacturing process is prone to insufficient bonding problems, increasing the risk of delamination. In particular, some low quality glues or resins may fail to form a strong bond due to incomplete curing. - Improper surface treatment of copper foil
The surface roughness and treatment attitude of copper foil directly affects its bonding with the resin layer. If the surface roughness of copper foil is small or improperly treated, it will lead to poor bonding and possible delamination. In practice, ensuring that the surface finish of the copper foil is in place can significantly reduce the risk of delamination occurring. - Thermal shock and soldering process
Thermal shock affects the PCB during the soldering process, which can lead to inconsistent thermal expansion between different materials, and this physical stress often contributes to the occurrence of delamination. Welding temperature is too high or too many times, will have an impact on the PCB interlayer bonding, thus causing delamination phenomenon.
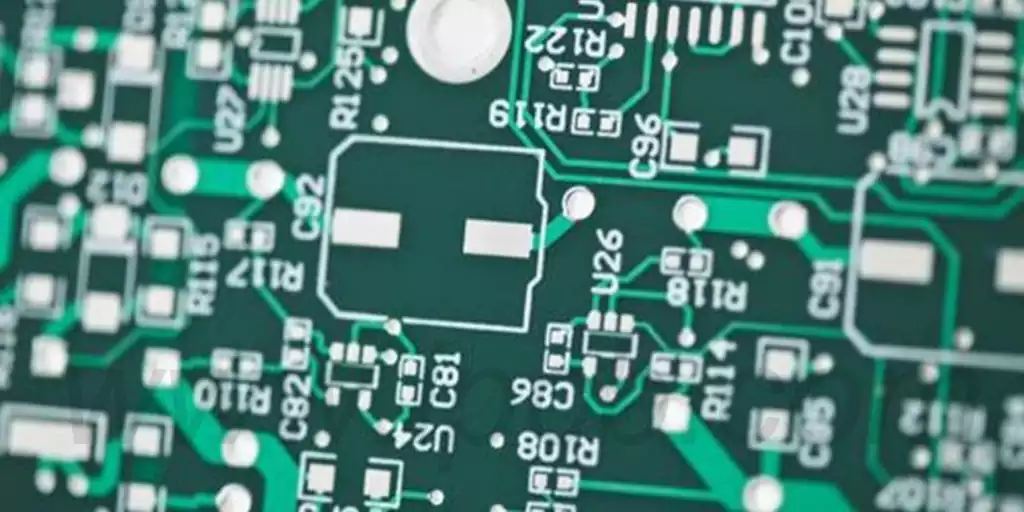
How to determine whether the PCB delamination
PCB delamination may not be immediately apparent after reflow soldering, but these signs can appear when using electronic equipment.
Unusual Heat Generation
If the layer structure of a circuit board is delaminated, it will not be able to dissipate heat efficiently, which can make the board hot. Continued exposure to heat may cause copper traces to peel away from the dielectric material, leading to short circuits and fires.
Crackling Noise
When the board is touched or moved, it may make a crackling sound, which is caused by copper traces stripping from the dielectric material and moving through the gaps.
Corrosion
Delamination can also lead to corrosion, which can occur on copper traces, boards or both, and the corrosion may show some undesirable spots on the surface.
Effects and Consequences of PCB Delamination
Electrical Properties Problems
Delamination can degrade the electrical properties of the board by stripping copper wires from the dielectric material, resulting in noise, crosstalk, impedance changes and signal reflections.
Heat Dissipation Problems
Air is not as thermally conductive as FR4 and other boards.Air gaps due to delamination can increase areas of thermal resistance,stressing moving components that generate a lot of heat.
High failure rate
In addition to electrical and thermal problems,delamination weakens the physical structure of the PCB,making it susceptible to vibration and mechanical stress.
Shortened Life Span
The combination of weakened physical structure, thermal issues and electrical problems results in reduced reliability and service life of the board.
Difficulty in Repair and Rework
Delamination makes it difficult to create reliable electrical connections, such as forming reliable solder joints when performing repairs. You may need to remove delaminated sections before tackling these rework tasks.
Higher manufacturing costs
Once an error is detected,you must rework or scrap the board,which can lead to significant losses to fix the problem.Even if the product is not detected during manufacturing, consumers can experience reliability issues,damaging the company’s reputation and increasing warranty claims.
Difficulty in Inspection and Testing
Delamination can also interfere with the PCB overhaul and testing process, and the presence of electrical problems can make it difficult to identify the root cause of the problem, leading to longer downtime.
How to prevent PCB delamination
- Control environmental humidity
Controlling the ambient humidity of the PCB board is one of the key measures to prevent delamination.High humidity can cause moisture to accumulate inside the PCB,which leads to an increase in local vapor pressure and eventually triggers delamination. Therefore, it is recommended to maintain a suitable humidity environment during the storage and production of PCBs, and it is best to store PCBs in dry conditions to avoid moisture . - Optimize the soldering process
The temperature and time of the soldering process has a great impact on the stability of the PCB.Too high a temperature or too long a soldering time may lead to material expansion and stress concentration, which can lead to delamination.Therefore,it is recommended that the reflow soldering, set the appropriate temperature profile, and minimize the soldering time to reduce the thermal impact . - Selection of high quality materials
The use of qualified PCB substrates and adhesives can significantly improve the durability of the board. the type of FR-4 material is also very critical to the performance of the PCB,the wrong choice of material may lead to increased delamination problems. Therefore, it is important to ensure that the quality of the material meets the relevant standards during the manufacturing process. - Improve the lamination process
Control of the lamination process is critical to the prevention of PCB delamination.Ensuring that the pressure and temperature during the lamination process are appropriate can improve the bonding between layers and reduce the risk of delamination.If the copper foil of a layer in a multilayer board is thicker, special attention should be paid to the quality of the lamination. - Regular Inspection and Maintenance
Regular PCB inspection, including the use of scanning acoustic microscopy and thermo-mechanical analysis, can detect potential delamination problems as early as possible. Through timely maintenance and repair, delamination can be avoided to avoid the harm to the performance of the circuit board, to ensure the stable operation of the equipment .
PCB delamination has a significant impact on the performance and reliability of the board, the cause of which involves a number of aspects. Therefore, for the environmental humidity, soldering process, material quality and lamination process and other factors to take effective preventive measures is particularly important. Through the implementation of these measures, can effectively protect the stability and reliability of PCB, for the normal operation of electronic products to provide solid support.