PCB board to be retained on the part of the copper foil pre-plated layer of lead and tin resist layer, and then chemically corrode off the rest of the copper foil, known as etching. So, what are the types of PCB board etching and commonly used etching agents?
1.Types of etching graphic plating method: etching when the pcb board has two layers of copper, only one layer of copper is all etched away, the rest will form the final desired circuit.
Full-plate copper plating process: the entire board is plated with copper, the part outside the photographic film is only tin or lead-tin resist layer. Compared with the graphic plating, its biggest disadvantage is that all parts of the board have to be plated with copper twice, and they must all be etched away when etching.
There is another method, which is to use photographic film instead of metal plating as a resist layer. The method is similar to the inner layer etching process.
2.Etching agent which
Ammonia etchant is a commonly used chemical solution that does not have any chemical reaction with tin or lead-tin. In addition, there is ammonia / ammonia sulfate etching solution, after the use of which the copper can be separated by electrolysis; generally used in non-chlorine etching. Others use sulfuric acid – hydrogen peroxide as an etchant to etch the outer layer of the graphics, has not yet been adopted in large quantities.
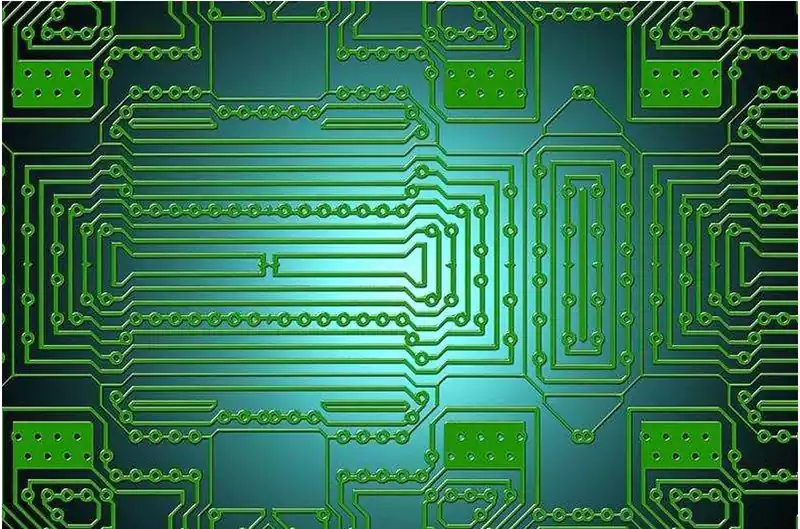
PCB board etching process should pay attention to the problem of
Reducing side etching and sudden edges
Side-etching produces raised edges.Usually the longer the printed board is in the etching solution,the more serious the side-etching will be.Side-etching will seriously affect the accuracy of printed wires,and severe side-etching will make it impossible to make fine wires.When the side etching and abrupt edge is reduced, the etch factor will rise, and a high etch factor indicates that there is the ability to maintain a fine wire, so that the etched wire can be close to the size of the original drawing.Plating etchers, whether tin-lead alloy, tin, tin-nickel alloy, or nickel, can cause a short in the wire when the raised edge is excessive.This is because the protruding edge tends to tear down and create an electrical split between two points of the wire.
Maintenance of pcb board etching equipment
The most critical factor in the maintenance of etching equipment is to ensure that the nozzles are highly clean and free of obstructions, so that the nozzles can spray smoothly.Obstructions or slag can cause pressure to be generated when spraying, impacting the plate surface. A poorly cleaned nozzle can cause uneven etching and render the entire board obsolete.
Obviously,the maintenance of the equipment is to replace broken and worn parts, and since the nozzles are also subject to wear and tear, replacement should include the nozzles.In addition,the more critical issue is to keep the etching machine free of slag,as in many cases excessive slag build-up can have an effect on the chemical balance of the etchant. Similarly,if there is a chemical imbalance in the etchant,scumming will be exacerbated. Etching solution suddenly appear a large number of slagging,is usually a signal that the balance of the solution has a problem,this time should use the stronger hydrochloric acid for proper cleaning or solution replenishment.
Factors affecting the performance of pcb board etching:
- Etchant selection and composition:
Etchant selection and composition is critical to the etching process and results. Different etchant has different erosive and selective, directly affect the etching rate and precision. Etchant chemistry, concentration and temperature need to be selected and adjusted according to the specific substrate and circuit design to achieve the desired etching results. - Substrate material and surface treatment:
The type of substrate material used has a significant impact on etching performance.Different materials (such as FR-4, high frequency substrates or metal substrates) have different properties, including dielectric constant, thermal conductivity and surface finish, which affect etch rate, uniformity and circuit quality. Proper surface finish is important to ensure optimal adhesion between the etchant and the substrate. - Etching equipment and process parameters:
The quality of pcb board etching equipment and process parameters play a key role in etching performance. Factors such as etch tank design, agitation methods, temperature control and etchant replenishment mechanisms affect etch uniformity, rate and repeatability. Accurate control and monitoring of parameters such as etchant concentration, temperature and soak time are critical to maintaining process stability and achieving desired etch results. - Circuit design considerations:
The circuit design of the PCB directly affects the etching process and results.Factors such as trace width, pitch, and circuit pattern complexity can affect the accuracy of the etch, especially when fine pitch components and high density interconnects are used. Appropriate design guidelines, such as maintaining proper gaps, avoiding over- or under-etching, and ensuring uniform etching across the PCB,are important for achieving optimal etching results. - Quality control and inspection:
Strong quality control and inspection measures are essential to monitor and ensure the consistency and reliability of the etching process.Regular sampling and analysis of etched PCBs, including dimensional accuracy, copper layer thickness and circuit integrity,helps to detect any deviations or problems.Advanced inspection methods, such as automated optical inspection (AOI) and X-ray inspection,provide additional assurance of etch quality.
PCB board etching technology involves a number of factors and requires comprehensive consideration of etchant, substrate, equipment, design and quality control to ensure high quality production. In the future, etching technology will continue to advance to meet the growing demands of electronics manufacturing.