Hot plate for pcb soldering is an advanced soldering technique that is primarily used to securely attach electronic components to printed circuit boards (PCBs). This method utilises the heating function of the hot plate to provide uniform temperature control, thus ensuring an efficient and stable soldering process.
The hot plate for pcb soldering process achieves the processing of PCBs through a number of process steps. Firstly, this technology is applicable to all types of PCBs, including single-sided, double-sided and multilayered boards, and is able to meet the needs of different industries. In addition, it is particularly good at soldering tiny precision components, suitable for today’s miniaturised and high-density electronics. Therefore, PCB hot plate soldering in electronic equipment, communications products and medical electronics and other high-tech fields is increasingly important.
Hot plate for pcb soldering operation process
Preparation
Equipment Inspection:Before soldering, carry out a comprehensive inspection of the soldering equipment, including hotplates, soldering irons and other auxiliary tools to ensure their normal operation.
Material Preparation:Ensure that solder, flux and PCB components are complete and meet the appropriate standards.
Preheating Stage
Heating Setting:According to the PCB material and solder type, set the heating temperature of the hot plate,which is generally controlled at 90-110℃ to reduce the stress and avoid the phenomenon of pulling sharp or rounding off.
Heating Time:Keep the preheating for a certain period of time to ensure the temperature of PCB and additional components are uniform.
Soldering Stage
Apply Flux:Apply flux to the PCB surface to ensure good wetting and connection of the solder.
Heat the solder joint:Touch the soldering iron or soldering tool to the solder joint and apply heat quickly to melt the solder and form a good metal connection at the solder joint. The soldering time is usually limited to 3 seconds or less to ensure good joint characteristics.
Cooling Stage
Cooling:After the soldering is completed, the solder joint should be allowed to cool naturally to ensure that the solder is stable and solidified, if necessary, a fan can be used to accelerate the cooling process.
Cleaning: Remove residual flux and impurities from the surface of the PCB after soldering to ensure the cleanliness of the board to prevent corrosion and short circuit.
Quality Inspection
Visual Inspection: Visual inspection of the soldered PCB to ensure that the solder joints are complete and there are no missing or cold soldered joints.
Functional Test: Electrical tests are performed to ensure proper operation of the circuits and to check the electrical boot performance of the solder joints.
Principle of Hot plate for pcb soldering
Hot plate for pcb soldering realises the soldering process of surface mounted components on circuit boards by heating the solder to a molten state. The principle of operation mainly involves the key aspects of heating, pressure application and soldering.
Firstly the PCB reflow hot plate gradually raises the temperature to meet the soldering requirements by means of a precise heating system. The soldering process starts in the heated area, where the solvents and gases in the solder paste begin to evaporate, while the flux in the paste wets the pads and pins, and the paste softens and covers the pads. This process ensures adequate preparation of the PCB and components before soldering.
Next, the temperature in the soldering area rises rapidly, causing the solder paste to reach a molten state. At this point, the liquid solder wets and fuses with the PCB’s pads and component pins to form a solid solder joint. At this stage, the temperature control management of the hot plate is crucial to ensure the uniformity and stability of the temperature during the soldering process.
Finally, after the soldering is complete, the PCB enters the cooling zone to solidify the solder joints and complete the entire soldering process. This cooling process is equally important as it determines the quality and stability of the solder joints. Once the soldering is complete, the board undergoes subsequent testing and quality checks to ensure the reliability and perfection of the soldering.
Through this combined means of controlling temperature and pressure, hot plate for pcb soldering not only enhance the effectiveness of the soldering, but also reduce the incidence of defects in the soldering, allowing the modern electronics manufacturing industry to improve productivity.
Advantages of hot plate for pcb soldering
1.High efficiency
Hot plate for pcb soldering is more efficient than traditional soldering methods because it can melt and solder by heating the plate quickly. In addition, hot plate soldering can often be done with multiple joints at the same time, increasing productivity.
2.Uniformity
Hot plate for pcb soldering can make the metal plate get uniform heating, so as to achieve uniform melting of the welded joints, making the weld more solid.
3.Stable quality
As the hot plate welding requires high requirements on the surface of the workpiece, impurities can be removed before welding to make the welding quality more stable.
4.Wide range of application
Hot plate welding can weld different materials with thickness between 0.5mm-10mm, which has a wide range of application, especially suitable for plate connection, manufacturing and other fields.
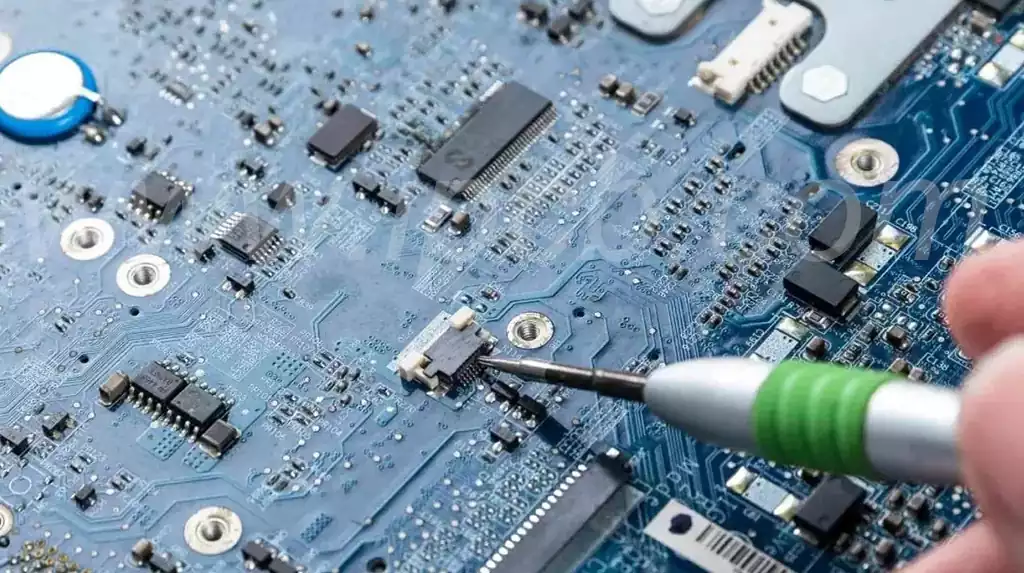
Methods to improve the quality of hot plate welding
Temperature control is critical. During the welding process, the temperature of the hot plate should be set precisely above the melting point of the solder to ensure that the solder can fully melt and uniformly wet the welding surface. Depending on the material properties, it is usually set at 300-480°C and the heating time is usually between 3-7 seconds. Reasonable temperature profile design not only helps to avoid defects such as cold soldering and false soldering, but also ensures the strength and stability of the solder joint.
In terms of pressure regulation, applying appropriate pressure can enhance the wettability of the solder and the connection strength of the solder joint. By adjusting the hydraulic equipment and soldering time, the pressure during the soldering process is kept within the optimal range. It is usually recommended to set the pressure at 1-100 kg/cm² to avoid floating or missing solder joints.
Solder paste selection is also an important factor in solder quality. Different types of solder paste have different viscosity and melting properties, so it is crucial to choose the right paste for the specific soldering task. A good solder paste maintains good flow and wettability during the soldering process, ensuring an intact and reliable solder joint.
During the preheating process before soldering, it should be ensured that the PCB and its components are preheated evenly to reduce thermal stress and deformation. Reasonable preheating can avoid defects in solder joints due to sudden temperature changes. In addition, in the cooling step after the completion of welding, attention should be paid to the cooling speed, fast and uniform cooling can avoid the internal stress and deformation of the solder joints, and improve the quality of the solder joints.
The quality inspection of the welded joints after welding is also very important. Through visual inspection, X-ray inspection and online electrical testing and other methods, can be timely found and solve the welding process may appear defects, and then optimise the welding process, improve the overall production efficiency.
With the rapid development of the modern electronics manufacturing industry, hot plate for pcb soldering, as an advanced welding technology, is becoming the preferred method of connecting electronic components to printed circuit boards with its advantages of high efficiency, uniformity and stable quality. Through precise temperature control and pressure regulation, combined with high-quality solder paste and scientific preheating and cooling steps, PCB hot plate welding not only enhance the quality of soldering, but also significantly improve production efficiency.