PCBA (Printed Circuit Board Assembly) test fixture plays a vital role in the electronics manufacturing industry. Its main function is to provide physical support and electrical connection for the test link of PCBA, so as to ensure the efficiency and accuracy of the test. Whether it is consumer electronics, automotive electronics, or medical equipment, this device has been widely used. In this article, we will conduct an in-depth analysis of the principles, design points, application scenarios, advantages and future trends of PCBA test fixtures.
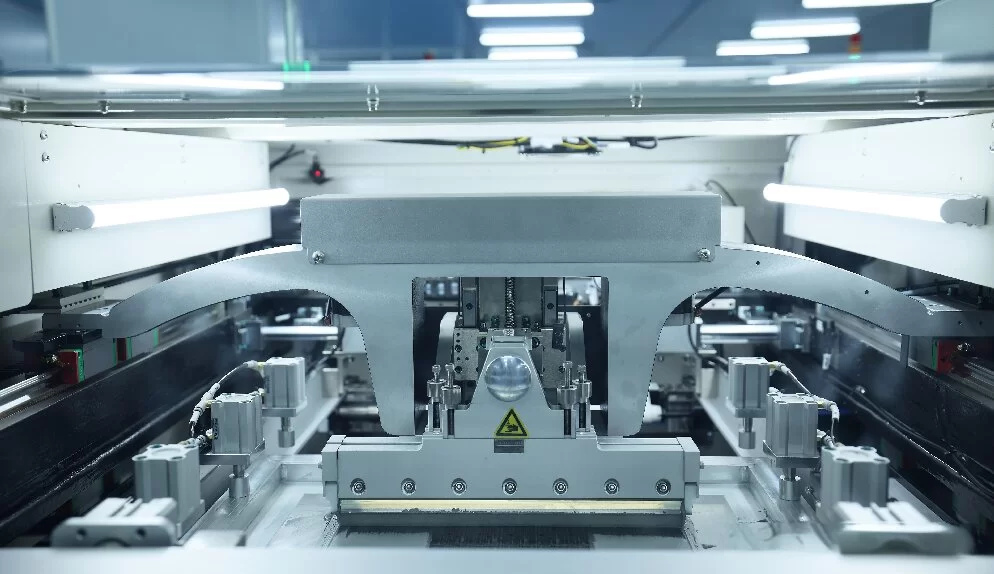
Definition and background of PCBA test fixtures
PCBA is a core component in the production of electronic products, and testing is a key link to ensure its performance and quality. PCBA test fixtures are specially designed tools for fixing PCBA during the test process and providing it with efficient docking with test equipment.
With the miniaturization and complexity of electronic products, traditional manual testing methods have been unable to meet the needs of high-precision and mass production. PCBA test fixtures came into being, which greatly improved the efficiency and consistency of testing through modular design, high-precision positioning and automation compatibility.
In modern electronic manufacturing, PCBA test fixtures are not only a basic tool for quality control, but also an important link in production automation. For example, in automated production lines, test fixtures are often combined with robotic arms and automatic test equipment to achieve fully automated operation of the test process.
Functions of PCBA test fixtures
- Stable fixation of PCBA
The test fixture ensures the stability of the PCBA during the test process through mechanical clamps, vacuum adsorption or magnetic fixation. This stability is particularly important for high-speed and high-precision testing, and can avoid test errors caused by vibration or offset. - Achieve fast connection
The test fixture is equipped with special probes, contact points or interface modules that can complete electrical connections with the PCBA in seconds. For example, some devices are designed with spring pin structures that can quickly connect to test points on the PCB, reducing the complexity of traditional manual wiring. - Support multiple test types
The test fixture can adapt to a variety of test requirements, including ICT (in-circuit test), FCT (functional test), aging test, and high-voltage test. Its flexible design enables it to cover a variety of test requirements in product development, trial production and mass production stages. - Help quickly locate faults
Through precise contact with the test points, the test fixture can quickly capture the fault points in the PCBA, such as short circuits, open circuits or abnormal electrical parameters, providing engineers with a clear reference for fault location. - Improve test consistency
In mass production, the test fixture can ensure consistent test conditions for each PCBA through standardized design, avoid differences in test results caused by manual operation, and thus improve the consistency of product quality.
Design points of PCBA test fixture
- Modular design
The modular design enables the test fixture to adapt to a variety of PCBA sizes and layouts. For example, by replacing module components, manufacturers can use the same set of fixtures to test different models of products, reducing development costs. - Precision positioning technology
High-precision testing requires perfect contact between the test probe and the test point on the PCBA. Test fixtures usually use laser alignment, mechanical limit or magnetic alignment technology to ensure that the contact accuracy between the probe and the test point reaches the micron level. - High-durability materials
The fixture needs to withstand mechanical wear, frequent operation and ambient temperature changes for a long time, so it is crucial to select high-strength and high-durability materials. Aluminum alloy, carbon fiber and special plastics are common material choices. - Automation compatibility
Modern PCBA test fixtures must be compatible with automated test equipment. For example, some fixtures are designed with electric clamps and automatic docking interfaces, which can be seamlessly integrated with robotic arms or assembly lines to support unmanned operation. - Ergonomics
For fixtures that require manual operation, the design must be ergonomic, such as lightweight design and easy-to-operate fixture settings to reduce operator fatigue.
Application scenarios of PCBA test fixtures
Consumer electronics
In the production of consumer electronic products such as mobile phones, tablets, and smart watches, PCBA test fixtures are used to efficiently complete functional testing and performance verification. These products are usually produced on a large scale, and the fixtures significantly shorten the test time through automated operation.
Automotive electronics
Automotive electronics have extremely high requirements for the reliability of PCBA. For example, in ADAS (Advanced Driver Assistance Systems) and power control systems, PCBAs need to pass tests under high temperature, high humidity, and high vibration conditions. Fixtures provide reliable support for these demanding tests.
Medical Devices
PCBAs in medical devices need to meet high precision and high reliability requirements. Test fixtures help ensure device performance and patient safety through non-destructive testing methods, such as contact and non-contact probes.
Industrial Control
PCBAs for industrial control equipment often require high voltage, overload, and durability testing. Fixtures are precisely designed to meet the needs of these special test scenarios.
Communication Equipment
In communication equipment such as routers and base stations, PCBA test fixtures are used to verify signal integrity and electrical performance. These fixtures need to support high-frequency signal testing and have extremely high shielding performance.
Advantages of PCBA Test Fixtures
Improve Test Efficiency
Through fast fixing and automatic connection, test fixtures reduce the time required for traditional manual testing from minutes to seconds, significantly improving production line efficiency.
Reduce Test Costs
Modular design and automation compatibility reduce repeated investment and manual operation costs, making the test process more cost-effective.
Improve product quality
Through standardized testing processes, fixtures ensure consistency in test results for different batches of PCBAs, reducing quality issues caused by test errors.
Reduce environmental impact
Modern fixtures use environmentally friendly materials and sustainable designs, such as reducing waste generation and improving resource utilization.
Challenges of PCBA test fixtures
Miniaturization and complexity requirements: As PCBA sizes continue to shrink, test fixtures need to adapt to higher density test point layouts.
Development costs and cycles: Complex designs and high precision requirements increase development costs and manufacturing cycles.
Technical adaptability: Fixtures need to be compatible with more signal types and interface standards to adapt to functional testing of different devices.
Future development trends
Intelligence
In the future, PCBA test fixtures will be combined with AI technology to achieve adaptive testing. For example, the device can automatically adjust the probe position or optimize the test process based on test data.
High integration
Test fixtures will integrate more functions, such as signal processing modules and data analysis modules, to meet the multi-dimensional testing needs of complex products.
Miniaturization
As PCBAs continue to shrink in size, test fixtures need to have higher precision and smaller footprint to accommodate the production needs of miniaturized electronic devices.
Summary
PCBA test fixtures are key tools for modern electronic manufacturing. Their efficiency, precision, and automation not only help manufacturers improve production efficiency, but also ensure product quality. As technology continues to advance, this field will usher in more innovations, further promoting the development of smart manufacturing.