Thermal cutoff, also known as thermal cutoff, is a sensitive temperature-sensing circuit cutoff device. It can keenly capture the overheating phenomenon generated by electrical or electronic products during abnormal operation and decisively cut off the circuit, thus effectively preventing the occurrence of fire. This safety device is widely used in a variety of household appliances such as hairdryers, irons, rice cookers, electric stoves, transformers, motors, water dispensers, coffee makers and so on. It is worth noting that a thermal fuse operates only once at the melting temperature and cannot be restored once it has operated.
When connecting thermal cutoffs, we have a variety of options, including soldering, spot welding and twisting. Spot welding is favoured for its efficiency and precision. For spot welding, we usually use the MF inverter DC spot welder from Shenzhen Ster Technology. This equipment through the single-phase or three-phase AC rectified into pulsating DC, and then by the power switching devices composed of inverter circuit converted to medium frequency square wave, access to the transformer step-down rectified into a small pulsating DC, supply electrode welding workpiece. The inverter adopts current feedback pulse width modulation technology to ensure the output of constant current. With its excellent performance, MF inverter spot welder is especially suitable for welding thin metal parts with high thermal conductivity and fine workpieces.
Of course, when using solder for spot welding, we must take extra care to avoid damage to the thermal cutoffs due to overheating of the weld. Below is a guide to the maximum soldering time (for a single leg, leg length 10mm, at 300 degrees Celsius):
Rated action temperature TF at 102-115 degrees Celsius, soldering time is 1 second;
Welding time of 2 seconds for rated action temperature TF of 125-139°C;
When the rated operation temperature TF is 150℃, the welding time is 3 seconds.
Since the temperature sensing element inside the thermal cutoff is a piece of low-melting-point alloy wire, it is connected to both pins. Therefore, improper soldering operations (e.g., too high a soldering temperature, too long a soldering time, too short a pin, etc.) may cause heat to be transferred to the inside of the thermal cutoff through the pins, resulting in overheating and damage to the sensing element. This damage may manifest itself in the form of melting, thinning and weakening of the end by thermal shock, and reduced reliability of the connection to the pin. Once the damaged part is subjected to current passage or other factors in use, premature breakage may occur.
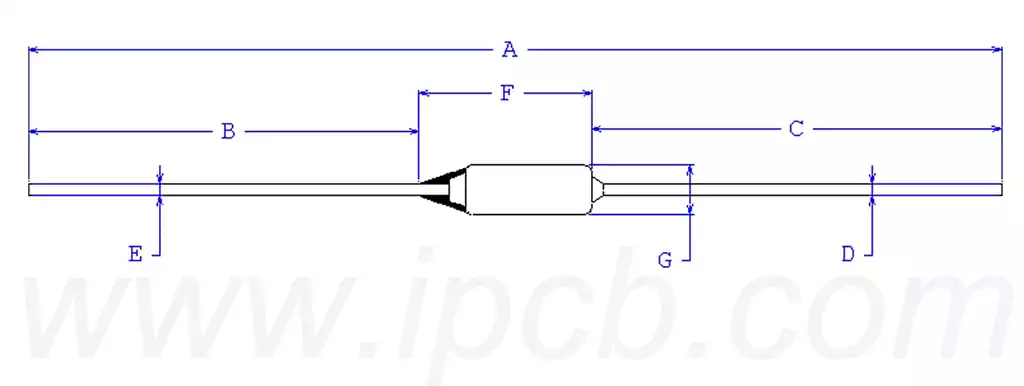
In order to avoid damage to the thermal cutoffs caused by overheating of the soldering, we can take the following measures:
Use longer pins whenever possible. Longer pins allow for longer soldering times and reduce the possibility of overheating.
In the case of shorter pins, we can use sharp-nosed pliers or other tools to clamp on the pins between the solder joints and the fuse body to dissipate heat, thus avoiding excessive heat transfer into the inside of the thermal cutoff.
At the same time, we should strictly control the soldering temperature to make sure that it is not too high and keep the soldering time as short as possible.
Through these measures, we can ensure that the thermal cutoffs will not be damaged during the soldering process, thus guaranteeing their reliability and safety in subsequent use.