Hot bar soldering is the use of heat and pressure to press-weld a wire to a metal weld area. Hot bar soldering is an umbrella term that covers a wide range of soldering methods such as pneumatic, calcined and roll welding.
Depending on the method of heating, hot bar soldering can be divided into three main forms: table heating, head heating, and simultaneous heating of the table and head. Each of these three types of heating has its own unique advantages and disadvantages, and specific information can be found in the relevant tables. In addition, the shape of the indenter can be subdivided into wedge-shaped indenter, hollow indenter, grooved indenter and flanged indenter.
The basic principle of the hot bar soldering involves applying a solder paste to a circuit board and then melting the solder by heat to make a conductive connection between two electronic components. This technique is commonly used to solder flexible circuit boards to PCBs and is designed to make equipment lighter and smaller. In addition, the technique is effective in reducing production costs by eliminating the need for one or two flex board connectors.
In the standard hot bar soldering process, the hot press heats the hot head using the Joule heat generated by pulsed electric current through highly resistive materials such as molybdenum and titanium. The hot press head then transfers the heat to the solder paste on the PCB, causing it to melt and complete the soldering. Since the pulse current is the key to heating, precise control of it is critical. This control is achieved by means of a thermocouple circuit, which is located at the front of the heat press head and is able to monitor the temperature of the heat press head in real time and feed the information back to the power control centre to regulate the pulse current signal to ensure that the temperature of the heat press head is accurate.
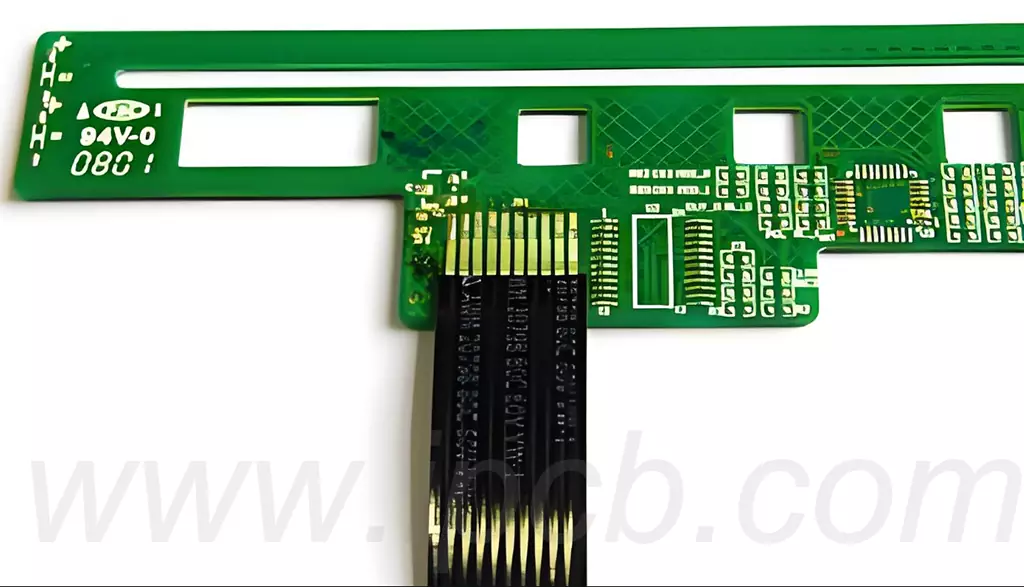
Regarding the processing of surface mount chips, the process control of hot bar soldering includes the following aspects:
- Regulation of the gap between the hot press head and the object being pressed: when the hot press head drops to contact the object being pressed, it must ensure that the two are completely parallel to ensure that the heat is evenly transferred. Usually, this requires first loosening the screws on the heat press to fix the heat press head, switching to manual mode, and then confirming the completion of the adjustment after the heat press head has completely contacted the pressed object.
- Lock the screws and lift the hot press head: After confirming that the hot press head is in good contact with the pressed object, the screws should be locked to keep the position stable, and then lift the hot press head. During the debugging process, you can use the non-tinned board as the test object.
- Ensure the fixed positioning of the pressed object: For pressed objects such as PCB circuit boards and flexible boards, it is necessary to ensure that they can be stably fixed on the fixture carrier and that the position of the hot head is fixed every time, especially in the front and rear directions. Lack of fixation can lead to empty soldering or damage to nearby components. Therefore, when designing PCBs and flexible boards, special attention should be paid to incorporating locating holes and keeping them close to the soldering area to avoid displacement during the hot press process.
- Control of hot press pressure: This is also one of the key factors to ensure the quality of soldering.
- The use of flux: Although the addition of flux can help the welding process to run smoothly, in some cases the desired welding results can be achieved without flux.
Hot bar soldering technology, with its flexibility and efficiency, occupies an important position in electronics manufacturing, ensuring the quality of soldering while promoting product lightweighting and cost savings. Through the fine control of key aspects such as heating, pressure and positioning, hot bar welding provides a reliable guarantee for the miniaturisation and precision manufacturing of electronic products.