Can I cut PCB with scissors? Why do I need to cut PCBs?
Cutting PCBs is an important process for customizing and optimizing electronic projects. There are several reasons for cutting PCBs.
Personalizing Boards from Panel Arrays
When you work with PCBs, you often come across PCB panelization, where multiple smaller boards are mass-produced and connected together to form an array. These interconnected boards, commonly called boards, are organized together to simplify the production process. Still, in order to utilize each PCB, they must be removed from the panel by cutting. The cutting process plays an important role in isolating these boards and preparing them for integration into your project.
Resizing or Reshaping
Sometimes you may need to resize or reshape a PCB to make it suitable for insertion into a device. Whether you are working on a gadget or want to change the board configuration, cutting is the way to go. Resizing allows you to reduce the size of a PCB to make it fit your project requirements. Reshaping enables you to adjust the layout of a board. This adaptability plays an important role in making electronic products or reconfiguring existing boards for new uses.
Removing Damaged Sections
You may need to cut a PCB to remove damaged sections. This process is essential when parts of the board are faulty or damaged. By cutting the damaged area, you can prevent these problems from affecting the entire circuit. Removing the damaged part also allows you to salvage the rest of the PCB, ensuring that the remaining components function properly. This helps you maintain the quality and reliability of your electronic project.
Salvage functional subsections
Sometimes, you need to cut a PCB to salvage a functional subsection. If a part of the board is damaged or unnecessary for your project, cutting allows you to save and use the part that is still working properly. This can help you make full use of materials, reduce waste and ensure that the functional parts of the PCB are fully utilized. Salvaging these subsections is a cost-effective way to reuse your board for other applications or repairs.
Can I cut the PCB with scissors? The answer is not recommended, you can buy a special cutting tool to cut.
Preparation
- Material inspection: First, the PCB board material needs to be inspected to ensure that it meets the design requirements, has no defects, no bends, and has sufficient dimensional stability.
- Design confirmation: Before cutting, the design size and shape of the PCB board should be confirmed again to ensure that the cut board can meet the circuit layout and assembly requirements.
- Tool preparation: Prepare corresponding cutting tools according to the needs and scale of cutting, such as shearing machines, knives, drilling machines or laser cutting machines.
Among them, briefly introduce what a shearing machine is?
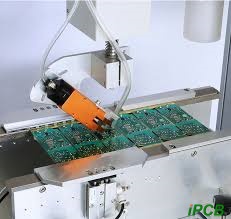
The shearing machine uses a reasonable blade gap to apply shearing force to metal plates of various thicknesses, so that the plates are broken and separated according to the required size. The shearing machine is a type of forging machine, and its main function is the metal processing industry. The products are widely used in aviation, light industry, metallurgy, chemical industry, construction, shipbuilding, automobile, electricity, electrical appliances, decoration and other industries to provide the required special machinery and complete sets of equipment. The PCB shearing machine is designed to shear the PCB board by sliding under the circular knife. This important design can ensure that the service life of the machine equipment is well extended during use. However, often in the process of using PCB shearing machines, before cutting, the engineering department of the PCB board manufacturer will produce various PCB boards based on customer requirements and reducing company costs. At this time, it is necessary to use a ruler back and forth to measure the size and then cut it. The PCB board needs to be moved back and forth, which reduces the work efficiency and may cause damage to the PCB board.
Cutting method
Mechanical cutting:
- Shearing method: Use professional shearing machines or manual shearing tools to cut the PCB board according to the predetermined size. This method is suitable for straight-line cutting and is simple to operate, but it requires high precision control.
- Punching method: Use a punch press and a mold to punch the PCB board. Punching is suitable for mass production and has high efficiency, but the corresponding mold needs to be made in advance.
Laser cutting:
- Laser cutting technology is widely used in PCB cutting due to its high precision and high efficiency. The laser cutting machine irradiates the surface of the PCB board with a high-energy laser beam, quickly melts, vaporizes or burns the material, and blows away the molten material with a high-speed airflow to achieve cutting.
- The advantages of laser cutting are smooth cutting edges, high precision, and small heat-affected zone, which is suitable for cutting of complex shapes and high-precision requirements.
Chemical corrosion cutting:
- For PCB boards of certain special materials or where special shapes need to be cut, chemical corrosion can be used. This method achieves the purpose of cutting by coating specific chemical agents on the surface of the PCB board and using chemical reactions to corrode the unnecessary parts.
- Chemical corrosion cutting requires strict control of reaction conditions and time to ensure the accuracy and consistency of cutting.
Subsequent processing
- Edge processing: The edges of the cut PCB board may need to be polished or chamfered to remove burrs and sharp edges to prevent damage during subsequent processing or assembly.
- Size inspection: After cutting, the size of the PCB board should be checked again to ensure that it meets the design requirements.
- Cleaning: The debris and residue that may be generated during the cutting process need to be thoroughly removed through cleaning to ensure the surface cleanliness of the PCB board.
- Quality inspection: Finally, the cut PCB board is subjected to quality inspection, including electrical performance test and appearance inspection, to ensure that its quality and performance meet the use requirements.
The depaneling of PCB circuit boards refers to cutting multiple circuit boards arranged in a row from a large board into separate small boards.
The depaneling methods of PCB circuit boards mainly include the following:
- V-Groove: Cut a V-groove between the top and bottom layers of the PCB board, and then bend and break the board by applying appropriate force.
- Perforated Breakoff Tab: Drill holes at the edge of the PCB board or the designed support point, and use fragile connecting parts to connect multiple boards together. After assembly, these connecting parts can be easily broken to separate the boards.
- Routing: Cut the PCB board shape according to a predetermined path through equipment such as CNC milling machines or wire cutting machines. This method can accurately control the cutting path and is suitable for complex board shapes.
- Punching: Use a punching tool to punch the edge or specific area of the PCB board to separate the board. This method is suitable for simple-shaped boards and large-scale production.
- Laser Cutting: Use a laser to cut the PCB board. Laser cutting can achieve very fine cutting and is suitable for boards with complex shapes and high precision requirements.
Different ways to cut PCBs
When you learn how to cut PCBs, you will find that there are many different methods. Each method is suitable for different needs and materials.
Choosing the right method depends on your project requirements and the type of PCB you are working with.
Slitting
PCB cutting requires direct and simple cuts with sharp tools. You can use tools such as utility knives or metal shears, or even a cutter for greater precision. This method is ideal for simple, clean separations and minor adjustments. Cutting is best for thinner boards or less complex shapes, allowing you to quickly and efficiently get the exact size or shape you need,
Sawing
This is a method of cutting a board using a saw blade. This method is more robust than simple cutting and is ideal for thicker boards or larger materials. While sawing may leave a rougher edge than other methods, it is efficient at quickly cutting through sturdy materials. This is a good choice when you need to handle a lot of cutting tasks or deal with more sturdy PCBs.
Punching
A method of using a punching tool to create holes or specific shapes, such as a V-shape. This technique is ideal for making the exact holes needed for mounting or connection. Punching is especially useful when you need to add or modify features on a PCB rather than cutting it into separate pieces. It can help you make precise adjustments to a board without affecting the rest of the board. The most common is V-scoring.
Grinding
This is a method of removing material from a board using a rotating cutter. This technique is very precise and is ideal for creating fine and intricate shapes. Milling allows you to make intricate designs and fine adjustments, but it does require specialized equipment. It is ideal when you need to do fine work on a PCB to achieve a high degree of precision.
Grinding
Sanding or reshaping the edges of a board using a grinding wheel. This method is great for adding finishing touches and ensuring clean, smooth edges. Grinding is often done after other cutting methods to improve the appearance of the board and remove any burrs or rough spots. It helps make your PCB look more polished and professional.
Problems You May Encounter When Cutting PCBs with Scissors
You may encounter a few problems. Paying close attention to these potential issues will help you get better results and avoid common mistakes when learning how to cut PCBs.
Damaged Surface Finish
You may encounter issues with damaged surface finish. Surface finish protects circuits from damage caused by harsh environments and contributes to high solderability and shelf life. If the surface finish is damaged during the cutting process, it can affect the performance and durability of the board. To prevent this, always use sharp tools and handle the PCB carefully. Also, make sure to do a final quality control check.
Fragile PCB Fiberglass
Fiberglass reinforces the PCB and is essential to its strength. These fibers are woven together to form a strong, fabric-like material. However, during the cutting process, these fibers become brittle and may break or crack. This can affect the performance and reliability of the PCB. To minimize problems, use sharp, precise tools and handle the PCB gently. This helps maintain the integrity of the fiberglass and ensures your PCB remains strong and functional.
Thin Layer Bends
The thin layers in a PCB are fragile and can easily bend if not handled properly. This bending can cause problems with the PCB’s functionality and can affect its performance. To avoid this, use the correct cutting tools and techniques. Make sure the PCB is properly supported during the cutting process to prevent the thin layers from bending or warping. Proper handling and cutting methods will help keep the PCB in good shape and ensure it works as intended.
High Precision Required
PCBs are sensitive components that play a critical role in electronic devices. Precision is especially important for applications such as RF technology, medical devices, and wearable technology, where even small errors can affect performance.
Cutting with scissors yourself, inaccurate cutting can lead to incorrect connections or failures. To ensure your PCB works properly, use precision tools and double-check measurements, and taking extra care when cutting will help maintain the quality and reliability of your PCB.