What is tin plating?Tin plating is the application of a layer of tin to a copper foil. In the circuit board manufacturing process, the surface of the copper foil is immersed in a solution containing tin salts,and a uniform layer of tin grows on the surface of the copper foil through an electrolytic reaction.
Tin plating and its alloys are a kind of plating with good solderability and certain corrosion resistance, and are widely used in electronic components and printed circuit boards. In addition to physical methods such as hot dipping,atomisation and tin layer preparation, methods such as electroplating,dipping and chemical plating are widely used in the industry due to their simplicity and ease of use.This technology for circuit boards can effectively protect the copper layer from oxidation and prevent the surface of copper from blackening, mutation and corrosion, thus ensuring the quality and stability of the circuit board.
Classification of tin plating
Alkaline Tin Plating
The process usually chooses sodium stannate as the core component of the plating solution,which is responsible for providing the required metal ions. In the plating solution,sodium hydroxide plays an important role.It not only combines with stannate to form stable coordination compounds,which enhances the conductivity and dispersion properties of the solution,but also its free hydroxide ions can effectively prevent the hydrolysis of stannate and avoid the formation of precipitation in the plating solution.In addition,according to specific production requirements,the plating solution may also contain other components, such as sodium acetate.
Common alkaline tin plating solution formulations and process conditions are as follows: sodium stannate at a concentration of 90,100 g/l, sodium hydroxide at a concentration of 1,020 g/l,sodium acetate at a concentration of 015 g/l, the operating temperature is controlled at 7,590 degrees Celsius, the bath voltage is set at 46 volts, and the current density is maintained at 0.53.0 amps/square decimetre.
The main features of the process include:the use of tetravalent tin salts,which have the advantages of being less susceptible to oxidation and more tolerant of impurities; simple composition of the plating solution,which has good dispersion properties;and the resulting plated layer is fine, white, and less porous. However,due to the high operating temperature of alkaline tin plating (6080 degrees Celsius),it is difficult to maintain the golden yellow colour of the anodic dissolved state,and it is easy to produce harmful divalent tin ions. At the same time, the high bath temperature leads to hydrolysis of sodium stannate and the formation of sludge precipitation. In addition, the operating temperature of the electrolyte is high,and the current efficiency is only between 60% and 90%, especially when the cathode current density is large, the current efficiency is even lower.These shortcomings have been difficult to meet the PCB production requirements for environmental protection and high efficiency, so the process is gradually replaced by acid tin plating.
Acid Tin Plating
Acid tin plating solution according to the different conductive medium, can be divided into sulfate, fluoroborate, halide and alkyl sulfonate and other types. The composition of acid tinning electrolyte is simple, easy to operate and control.By adding appropriate additives, high quality plating can be obtained at room temperature without heating. The process is characterised by high cathodic current efficiency, fast deposition rate and long working cycle of the plating solution.
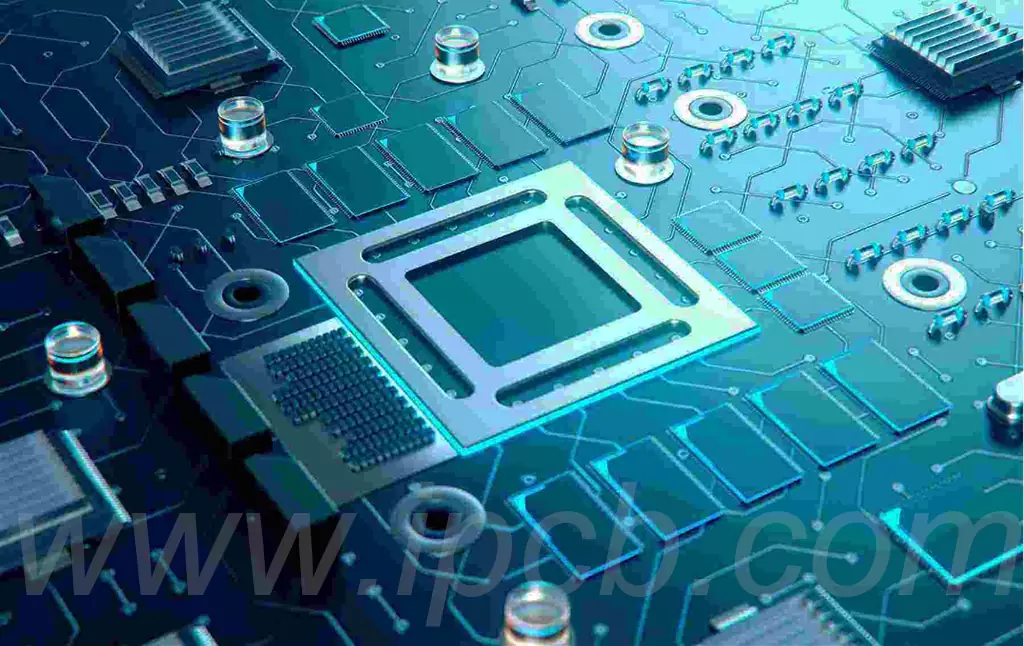
Manufacturing process for tin plating circuit boards
Surface preparation stage
In production practice,the surface of copper foils is often coated with impurities such as grease and dust,so the surface needs to be pre-treated.This step consists of placing the copper foil in a washing machine to remove contaminants,followed by a photochemical reaction machine that removes oxides from the surface of the copper foil.After the removal of the oxides,the copper foils undergo a light pickling process to further eliminate unwanted contaminants and ensure the cleanliness of the copper foil surface.
Tin plating process
After pre-treatment,the copper foil is ready for.At this stage,the copper foil is pulled into the tin-plating tank to form a tin layer on the copper foil by means of electrolysis.At the same time, ammonia and tartaric acid are added to the tin-plating tank, and the temperature,concentration and pH value of the tank are strictly controlled to ensure a uniform thickness of the tin layer.
Subsequent processing steps
After the tin layer is formed on the surface of the copper foil,subsequent processing is required to achieve a flat and smooth surface and to enhance the firmness of the tin layer.Subsequent processing usually involves heat treatment and dust removal.Heat treatment is to heat the tin layer at a high temperature to make it more stable;dust removal is to remove the oxides on the surface of the tin layer to make the surface smoother and more delicate.
Factors affecting the effect of tin plating
The role of current density in tin plating solution
The amount of current density in the tin plating solution has a direct influence on the uniformity and quality of the tin plating layer.
Importance of technical parameter setting
The setting of technical parameters, such as temperature, time, voltage, etc., plays a key role in the uniformity of the thickness of the tinned layer during the tinning process.
Selection of substrate material
Different metal substrates exhibit different properties for tin plating, such as corrosion resistance and mechanical strength.
How to select the right tin plating technology:
When selecting a tin plating process, a number of factors need to be considered, including the specific needs of the application or use, material costs, productivity, time required, and the advantages and disadvantages of the process.
Acid Poisson tin plating is known for its solution stability,high gloss,high current efficiency and ease of operation,but it has a relatively weak dispersion of the plated layer and suffers from easy hydrolysis of divalent tin.
Alkaline phosphating solutions are known for their excellent stability and uniform spreading ability,however,their high operating temperature, low current efficiency and lack of shine should not be overlooked.The methanesulfonic acid system has advantages in terms of deposition rate and wastewater treatment and is suitable for continuous plating operations.
Although fluoroborate tin plating solution is excellent in some aspects,its cost is higher than sulfuric acid tin plating solution,and there are environmental problems such as fluorine pollution, so it is rarely used in practical applications.
In the actual production process,sulfate and methyl sulfonate system of acid bright tin plating process is widely used because of its many advantages.
Tin plating technology for circuit boards is an indispensable part of the electronics industry, and its selection and application need to take into account a variety of factors. With the progress of technology, acid bright tin plating process is gradually becoming the mainstream, but no matter what kind of process, strict control parameters are the key to ensure the quality of the coating. In the future, circuit board tinning technology will continue to innovate, for the development of the electronics industry to inject new vitality.