Automotive pcb assembly,specifically refers to the use of automated placement technology,the various types of electronic components will be accurately placed on top of the printed circuit board (PCB),and undergo a series of processes such as soldering,testing,and ultimately produce a specific function of the electronic control components.Such components play a vital role in various electronic systems in the car, covering the engine control,body control and safety systems and many other areas.
Components of Automotive PCB Assembly
The core components of automotive pcb assembly include the printed circuit board (PCB) and its various electronic components installed on the PCB not only provides a solid support for the electronic components, but also ensures the electrical connection between them,and its quality has a direct impact on the performance and stability of the entire PCBA. The electronic components are a wide variety, including resistors,capacitors,inductors,diodes,transistors and integrated circuits, etc.,which are firmly installed in the PCB through the fine SMD process, working together to form a fully functional automotive electronic control system.
Importance of Automotive PCB Assembly
Automotive pcb assembly is a core component of the automotive electronic system, providing support for various electronic devices.Automotive pcb assembly carries key electronic components such as engine control unit (ECU),body control module (BCM),airbag control system,anti-lock braking system (ABS), etc. The normal operation of these components is directly related to the performance,safety and comfort of the car.Without PCBA,these electronic systems will not work and the function of the car will be greatly reduced.
The quality of PCBA directly affects the reliability and safety of the car. The complex working environment of automobiles,with large temperature changes and frequent vibrations,puts forward extremely high requirements for the durability and reliability of PCBA.High quality PCBA can ensure the stable operation of automotive electronic systems under various harsh conditions and avoid accidents caused by electronic failures.Therefore,automobile manufacturers are very strict on the quality control of PCBA,and adopt a variety of advanced testing technology and quality management system to ensure the reliability and safety of PCBA.
The technological innovation of Automotive pcb assembly promotes the development of automotive electronic systems.With the development of the trend of automotive intelligence and network connectivity, the complexity of automotive electronic systems continues to increase, which puts forward higher requirements for the performance and integration of PCBA.Automotive pcb assembly manufacturers continue to adopt new materials, new processes, and new designs to meet the needs of automotive electronic systems. For example, advanced technologies such as high-density interconnect (HDI) technology and buried component technology are widely used in the manufacture of automotive pcb assembly,which improve the performance and integration of PCBAs and promote the development of automotive electronic systems.
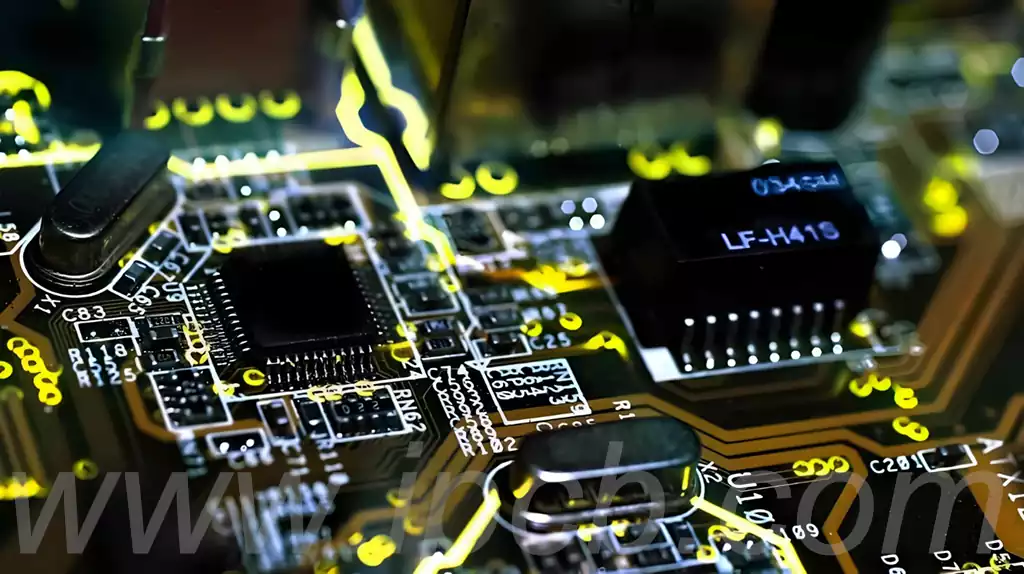
It is recommended to follow the following basic strategies in the smt processing of automotive circuit boards.
1.smt component placement direction component placement direction on the PCBA circuit board manufacturing performance. Reliability and functionality play an important role. When using wave soldering, components must be orientated parallel to the wave to prevent bridge soldering or open circuit.
2.Through-hole processing Automotive electronics have many control modules that require signal transmission.It is necessary to protect sensitive signals (such as communication modules) from electrical radiated interference through planar and controlled impedance.Each layer must use 2 to 4 vias for the connection between high current layers; in fact, using multiple vias on the PCB improves reliability,reduces resistive and inductive losses and increases thermal conductivity.
3.Thermal management components with power ratings over 10mW or over 10mA must require proper thermal management and power management components.The power and ground layers must be placed on the inner layer.If symmetrical and centred components prevent bending of the board.The first step consists of identifying the components with the most significant heat generation and measuring which heat management measures are performed.
Therefore the thickness of the alignment must be strictly controlled.Number of layers.Heat path continuity and board surface are all factors that affect the climate of the working component.Heat vias serve the same purpose as copper fields. Both tend to increase electrical conductivity.Working temperatures can be significantly reduced by using multiple soil areas and power supplies that are directly connected to the heat source through heat vias.If multiple components generate a large amount of heat,it is desirable to distribute it evenly across the board so as to avoid hot spots.On the other hand,if the heat generator is concentrated in a plurality of components,it is preferable to place it in the middle of the board so that the heat is evenly dispersed in all directions.
The importance of automotive PCB assembly as the cornerstone of automotive electronic systems cannot be overstated.From composition,function to quality control, every aspect is crucial. With the continuous development of automotive intelligence and internet connectivity,higher requirements are placed on the performance and reliability of PCBAs.Automotive PCB assembly will continue to drive the automotive industry forward and become an indispensable core driving force in the era of intelligence.