Burn in test is the process of running a circuit board or equipment for an extended period of time under tightly controlled environmental conditions to simulate actual circuit board usage scenarios in order to check the reliability and stability of the board. The aging test time is usually more than 24 hours, and can even reach several months.
The principle of burn in board is to simulate the process of long-term use of circuit boards under certain conditions, and to promote the aging of the internal components of circuit boards through high temperature, low temperature, high humidity, low humidity, etc., in order to detect whether the circuit boards are able to work normally after long-term use. This test method can detect potential problems within the board early, preventing equipment failure or damage.
Why Burn in test?
- Discover potential defects
During the manufacturing process of circuit boards, there may be some hidden defects, such as solder joints, short component life, etc. These defects need to be used for a period of time before they become apparent. Aging test can simulate the circuit board for a long time to find these potential problems, so as to improve the reliability and stability of the circuit board. - Improve product quality and reputation
Burn in test can ensure the quality and stability of the board to a certain extent, thus improving the credibility of the product. Some important electronic equipment, such as aerospace equipment, medical equipment, nuclear power equipment, etc., the reliability and stability of the circuit board is very high, aging test can ensure the reliability and stability of the product, which is very important to ensure the safe and stable operation of the equipment. - Customer requirements
Some customers have very high requirements for the reliability and stability of circuit boards, and require burn in test, and require that the results of the test is recorded and preserved, in order to query and trace at any time.
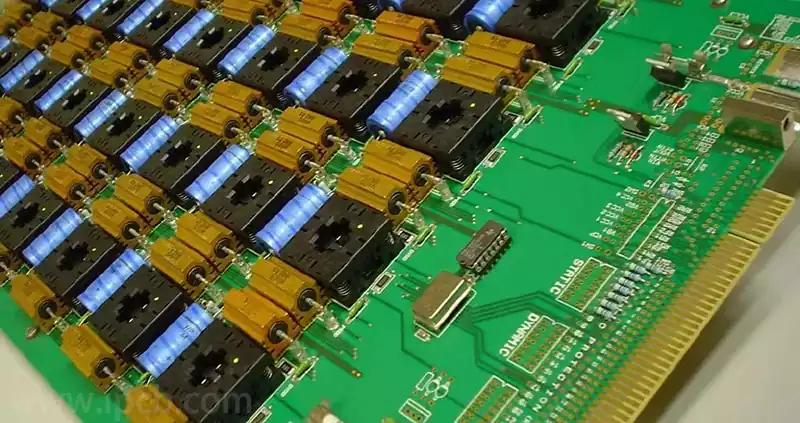
Circuit board burn in test methods
Temperature Test
Temperature testing is designed to evaluate the performance and stability of circuit boards in various temperature environments. It mainly covers low-temperature, high-temperature and cyclic temperature tests. In low-temperature testing, the board is placed in a low-temperature space, gradually cooled down and observed for changes in performance, mostly in the range of 0°C to -40°C. The temperature of the circuit board is then measured in a low-temperature environment, where the board is exposed to a low-temperature temperature. High-temperature testing places the board in a high-temperature environment, where it is gradually heated up and performance changes are detected, generally in the range of 25°C to +85°C. Cyclic temperature testing cycles the board through a set temperature range to check its stability and adaptability during temperature changes.
Humidity Test
Humidity tests are used to evaluate the board’s performance and stability under varying humidity conditions. Including low humidity, high humidity and cyclic humidity test. Low humidity test, the board will be placed in a low humidity environment, gradually increase the humidity and detect changes in performance, the test humidity range is usually 10% to 50% relative humidity. High humidity testing places the board in a high humidity environment, gradually reduces the humidity and detects changes in performance, typically in the range of 80% to 90% relative humidity. Cyclic humidity testing cycles through a set range of humidity levels to test the board’s stability and ability to adapt to changes in humidity.
Endurance Test
Durability test is used to evaluate the reliability and service life of the circuit board. It mainly includes load test, fatigue test and environmental stress test.
Load test: Apply a certain working load to the circuit board to simulate the actual working condition. After running for a period of time, the board’s performance and mechanical structure to detect any abnormalities.
Fatigue Test: Simulate the actual working condition of the board through periodic or random methods to detect its fatigue performance and stability during long-term operation.
Environmental Stress Test: Combining environmental factors such as temperature, humidity and mechanical stress, the board is subjected to a comprehensive stress test to assess its durability and reliability under comprehensive environmental conditions.
Functionality Test
Functionality test is used to verify whether the function of the circuit board meets the design requirements and expected standards. It mainly includes power supply test, function verification and interface test.
Power supply test: detects whether the power interface and power converter of the circuit board meet the design requirements and can provide stable voltage and current.
Functional verification: According to the design requirements and functional specifications of the circuit board, through experiments to verify that its functions operate normally and meet the performance indicators.
Interface test: Detect the circuit board and other equipment or systems between the interface connection is normal, whether the data transmission is stable and reliable.
Circuit board burn in test factors
- temperature: burn in test temperature will affect the test results, the higher the temperature of the shorter aging time, but if the temperature is too high will lead to damage to the circuit board. Need to set the aging temperature according to the circuit board design specifications and customer requirements. 2.
- humidity: humidity will also have an impact on the circuit board burn in test results, too high or too low humidity will affect the reliability and stability of the circuit board. Need to set the aging humidity according to the use of circuit board environment.
- aging time: the longer the aging time, the more accurate test results, but the aging time is too long will also increase production costs and testing time, need to make a reasonable balance.
- circuit board design: the design of the circuit board also has an impact on the results of the burn in test, some design flaws may lead to aging test results failures, need to be fully considered in the design phase.
- Environmental factors: the use of the circuit board environment will also affect the results of the burn in test, you need to carry out appropriate environmental simulation test.
Circuit board aging time standard due to industry norms and customer demand varies, usually in the aging time of 24 hours to 168 hours of this range. In general, the longer the aging time, the more accurate the test results will be. However, it is important to note that longer aging times can result in higher production costs and longer test cycles.
In the rapidly evolving world of electronics, circuit board burn in test is a key component in ensuring product reliability. Despite the many influencing factors, but through the reasonable set of parameters, cost and time trade-offs, we will be able to optimize the test. In the future, we look forward to the continuous innovation of aging test technology, for the electronics industry to build a solid foundation of quality.