Plating is an extremely critical step in the FPC manufacturing process. Plating not only strengthens the circuit’s conductivity, but also improves its corrosion resistance and appearance.
FPC (Flexible Printed Circuit) is plated on the following levels:
Optimisation of conductive properties
Metallic gold has excellent conductive properties. When an FPC is coated with metallic gold, the conductivity of the circuit is significantly enhanced. This plays a decisive role in ensuring the stable operation of electronic devices and maintaining the reliability of signal transmission.
Enhanced corrosion resistance
Metallic gold plating can form a protective barrier on the surface of the FPC to protect it from corrosion. Especially in humid, high temperature or corrosive substances in the environment, the gold plating layer can effectively extend the service life of the FPC, to ensure the long-term stability of its performance.
Enhance the aesthetic appearance
Gold plating process can give the FPC surface metal unique luster and texture, thus enhancing the overall aesthetics of the product. For those who pay attention to the appearance of the texture of the electronic products, this is particularly important to help enhance the competitiveness of the product market.
Improved soldering
Gold plating can optimise the soldering performance between the FPC and other electronic components. It can make the soldering process smoother and the quality of soldering more reliable, reduce the occurrence of bad soldering phenomenon, and improve the overall quality of the product.
Enhanced wear-resistant properties
The metal gold plating layer has a certain degree of hardness, which can improve the wear resistance of FPC to a certain extent. In the process of use, it can reduce the wear and tear caused by friction, protect the integrity of the FPC surface, and extend its service life.
Enhance Reliability and Stability
The gold plating layer also enhances the reliability and stability of the FPC and reduces the risk of circuit failures due to changes in environmental factors (e.g. humidity, temperature, etc.). It can provide a more stable operating environment for electronic equipment, ensuring the long-term stable operation of the equipment.
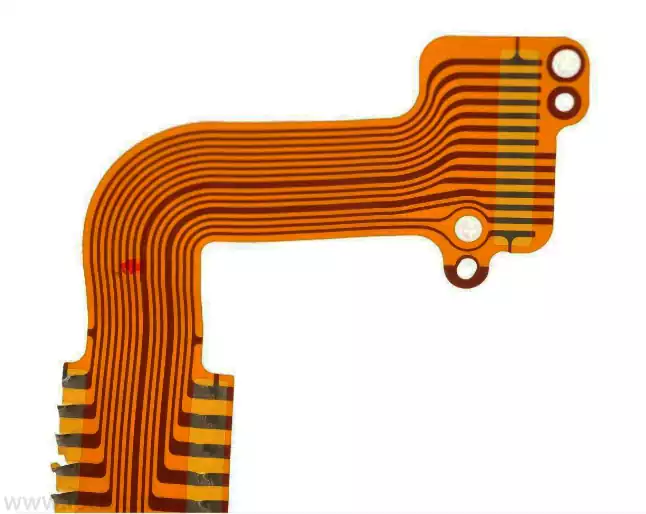
Within the scope of plating process, the whole plating and selective plating are two representative means, each of which has unique advantages and is suitable for different use scenarios.
FPC Plating
Literally, the entire surface of the FPC is plated in an all-round way. The advantage of this method is that it can guarantee the uniformity and consistency of the surface of the circuit board, thus improving the overall performance of the circuit. The whole plating is generally used to improve the conductivity and corrosion resistance of the situation.
Process steps: the whole plating process is relatively simple, roughly covering the pre-treatment, plating and post-treatment of the three links. Pre-treatment is mainly for the FPC surface cleaning and activation treatment, so that the plating solution can better adhere to it. In the plating process, the entire FPC is immersed in the plating solution, with the help of electric current, to generate a uniform layer of metal plating on the surface of the FPC. Post-processing is mainly to clean and dry the plated layer to enhance the stability and durability of the plated layer.
Application areas: Plating is suitable for applications with stringent requirements for FPC surface performance, such as high-precision instruments, aerospace equipment, and so on. These equipments have very high standards for the conductivity, corrosion resistance and stability of the circuit boards, and plating can provide a full range of protection to ensure the stable operation of the equipment.
FPC partial plating
Partial plating differs from whole plating in that it is only implemented on a specific part of the FPC. This method is more flexible, and the plating area can be selected according to the actual demand, thus realising material and cost savings.
Process steps: The process steps for partial plating are relatively more complicated. The first step is to perform a precise masking operation on the FPC to ensure that areas that do not need to be plated are not affected. Subsequently, plating is performed on selected areas, and finally the mask is removed and subsequent processing is performed. The core point of partial plating is the precise masking and positioning of the plating area, which requires a high level of skill and finesse on the part of the operator.
Applicable situations: Localised plating is suitable for scenarios where there are special performance requirements for specific areas of the FPC. For example, in some electronic devices, perhaps only in the key circuit nodes to enhance the conductivity, this time can be used in localised plating, not only to achieve the performance requirements, but also to reduce costs. In addition, partial plating is also commonly used to create FPC products with unique patterns or logos to enhance the aesthetics and recognition of the product.
FPC whole plating and selective plating each show their strengths, in different application scenarios play a key role. With the development of science and technology, the two will continue to optimise and upgrade, continue to inject new vitality into the field of FPC manufacturing, and promote the industry to new heights.