With the rapid development of automotive electronics technology, automotive PCB assembly as a key electronic manufacturing link, its reliability is directly related to the safety and performance stability of the vehicle system. Enhancing the reliability of automotive PCB assembly not only reduces the failure rate and rework cost, but also effectively improves the overall quality of the vehicle and user experience.
Basic Requirements for Automotive PCBs
Quality Assurance Requirements
Automotive PCB manufacturers should comply with ISO9001. PCB manufacturers are fully compliant with the ISO9001:2008 quality management system and are committed to adhering to the strictest standards in manufacturing and assembly.
Automotive products have their own peculiarities. in 1994, Ford, General Motors and Chrysler together established the quality control system QS9000 in the automotive industry. in the early 21st century, along with the ISO9001 standard compliant, a new quality control system in the automotive industry was published, that is ISO/IATF16949.
Performance Attributes of Automotive PCBs
Multiple Automotive PCBs
Automobiles combine mechanical and electronic equipment. Modern automotive technology is a blend of traditional and advanced science and technology, such as manual interior components and advanced GPS. in modern automobiles, there are electronic devices with different functions in different locations and different types of PCBs derived from different functions.
Based on the substrate material, automotive PCBs can be classified into two main categories: inorganic ceramic-based PCBs and organic resin-based PCBs.Ceramic-based PCBs have high-temperature resistance and excellent dimensional stability, allowing them to be directly applied to high-temperature motor systems. However, it is characterised by poor ceramic manufacturability and high cost. Currently, with the development of resin substrate materials in terms of heat resistance resin-based PCBs have been widely used in automobiles with substrate materials that have different properties applied to different locations.
Generally, flexible PCBs and rigid PCBs are used in the usual instruments to indicate vehicle speed and mileage as well as air conditioning equipment. Dual or multi-layer PCBs and Flex PCBs are used for audio and video entertainment devices in cars. For communication and wireless positioning devices and safety control devices, multilayer PCBs, HDI printed circuit boards and Flex PCBs are applied.For automotive motor control systems and powertrain control systems, special boards should be used.
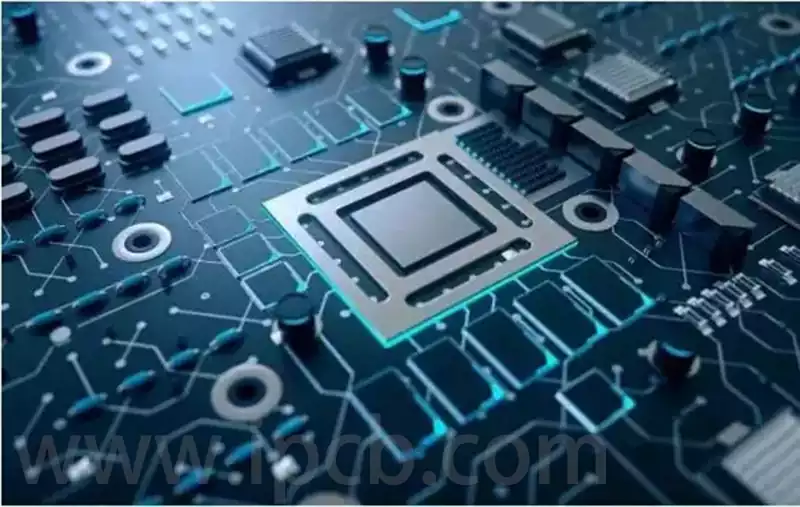
Experiences and points to improve the reliability of automotive PCB assembly:
It is very critical to pay attention to reliability at the design stage. Reasonable arrangement of component layout and line wiring is the basis for ensuring stable operation of PCBA. For example, key signal lines should be kept as short as possible to reduce the interference between high-frequency signals. For power components, it is necessary to select a package with good heat dissipation performance, and at the same time, reasonably design the heat dissipation channel to ensure that the heat can be effectively released. At the same time, the design also needs to fully consider the impact of environmental factors on the product, including temperature changes, humidity fluctuations and mechanical vibration, etc., and for these factors to carry out the necessary reliability simulation and testing, to ensure that the product in the actual use of the environment performance.
High reliability and long service life: Since the average service life of automobiles is 10 to 12 years, automotive PCBs must have a long service life to match, and be able to withstand harsh climatic and environmental conditions.
High mechanical strength and stability: Automotive PCBs need to withstand long-term vibration and shock without damage. Tests that simulate the actual operating environment of the vehicle, such as hot and cold cycle tests, vibration tests and drop tests, are used to ensure their mechanical properties.
Incoming material quality control is a critical step in ensuring the reliability of PCBAs. To manufacture reliable PCBAs, it is necessary to use high-quality electronic components and PCB substrates. Therefore, it is very important to select high-quality suppliers and conduct strict incoming inspection of their materials. Through a variety of inspection means, such as electrical performance testing, appearance inspection and X-ray inspection of components, unqualified products can be effectively screened out, preventing the flow of defective materials into the production process, thus enhancing the overall quality and stability of the final PCBA.
Fine management of the manufacturing process is also an important means to enhance the reliability of PCBA. The production process of automotive PCB assembly involves a number of links, including opening, drilling, copper sinking, solder resist, text printing, shape processing, plug-in, patch, welding, cleaning, testing and so on. Each link requires strict control of process parameters and strict quality testing. For example, the welding process is a key link in PCBA manufacturing, and its quality directly affects the reliability of PCBA. Therefore, it is necessary to select appropriate welding equipment and technology, and strictly control the welding temperature, time and other parameters to ensure the quality of welding.
Environmental stress screening (ESS) is also an effective method to enhance the reliability of PCBA. By applying certain environmental stresses, such as temperature cycling, vibration, humidity, etc., to PCBAs, potential defects can be stimulated and eliminated before delivery.
Lead-free compliance and environmental requirements: Compliance with RoHS (Restriction of the Use of Certain Hazardous Substances in Electrical and Electronic Equipment Directive) and other environmental regulations ensures that PCB materials and manufacturing processes are lead-free and hazardous substances are controlled.
Continuous quality improvement and reliability growth is a long-term strategy to enhance PCBA reliability. By analysing and summarising the quality problems that occur during the production process and continuously optimising the process and design, the reliability of PCBA can be continuously improved. For example, by collecting and analysing customer feedback, we can understand the problems that occur during the actual use of PCBA and target improvements.
The reliability of automotive PCB assembly is critical to vehicle performance and safety. In the future, with the continuous progress of automotive electronics technology, the continuous deepening of reliability improvement experience and standards will provide solid technical support and guarantee for the high-quality development of the automotive industry.